1. Introduction
Additive manufacturing, also known as 3D printing, has revolutionized various industries by enabling the production of complex and customized parts. One crucial component of additive manufacturing is metal powder, which serves as the raw material for creating solid metal objects through layer-by-layer deposition. The price of metal powders used in additive manufacturing can significantly impact the overall production cost and profitability. In this article, we will explore the factors influencing additive manufacturing metal powder prices and discuss strategies for managing these costs effectively.
2. Understanding Additive Manufacturing
2.1 What is Additive Manufacturing?
Additive manufacturing refers to the process of creating three-dimensional objects by adding layers of material on top of each other. Unlike traditional subtractive manufacturing methods that involve cutting or drilling material away, additive manufacturing builds objects from the ground up. This technology offers unparalleled design freedom, allowing complex geometries and intricate structures to be produced with ease.
2.2 Types of Additive Manufacturing Processes
There are several additive manufacturing processes, including:
- Powder Bed Fusion: In this process, a thin layer of metal powder is selectively melted and fused together using a laser or electron beam. This layer-by-layer approach builds the object from the bottom up.
- Directed Energy Deposition: In this process, a high-energy source, such as a laser or electron beam, is used to melt and fuse metal powder as it is continuously fed onto a substrate. This technique is often used for repairing or adding material to existing parts.
- Binder Jetting: In this process, a liquid binder is selectively deposited onto a layer of metal powder, bonding the particles together. This process is repeated layer by layer until the object is fully formed.
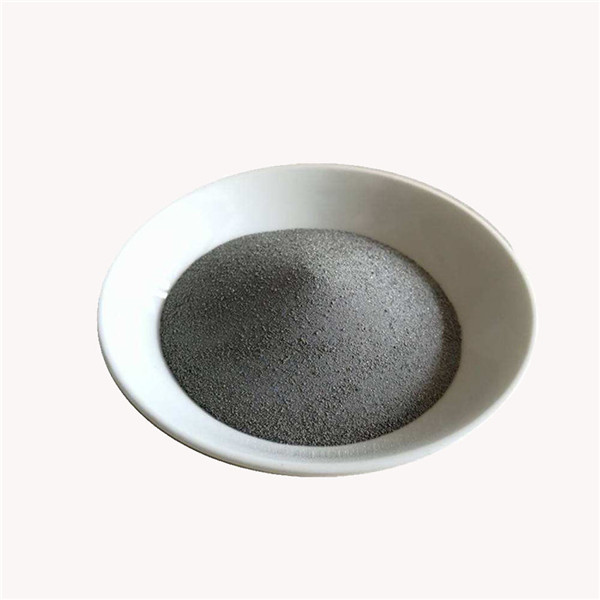
3. Metal Powder in Additive Manufacturing
3.1 Importance of Metal Powder in Additive Manufacturing
Metal powder is a critical component in additive manufacturing as it acts as the building material for creating solid metal objects. The properties of the metal powder, such as composition, particle size, and shape, directly influence the final characteristics of the printed part. Therefore, selecting the right metal powder is essential for achieving the desired mechanical, chemical, and physical properties of the printed object.
3.2 Factors Affecting Metal Powder Prices
Several factors contribute to the pricing of metal powders used in additive manufacturing. These include:
- Material Composition and Purity: The type of metal and its purity significantly impact the price of the powder. Precious metals like gold and platinum tend to be more expensive compared to common metals like aluminum or stainless steel. Higher purity levels also increase the cost.
- Powder Particle Size and Shape: Finer powders with smaller particle sizes and spherical shapes are often more expensive due to the increased surface area and improved flowability. Certain applications may require specific particle sizes, leading to variations in additive manufacturing metal powder price.
- Powder Production Methods: Different manufacturing processes used to produce metal powders can affect additive manufacturing metal powder price. Methods such as gas atomization, water atomization, and plasma atomization have varying costs associated with them.
- Powder Supplier and Quality Assurance: The reputation and quality standards of the powder supplier play a role in pricing. Trusted suppliers that ensure consistent quality, reliability, and certification may charge higher additive manufacturing metal powder price.
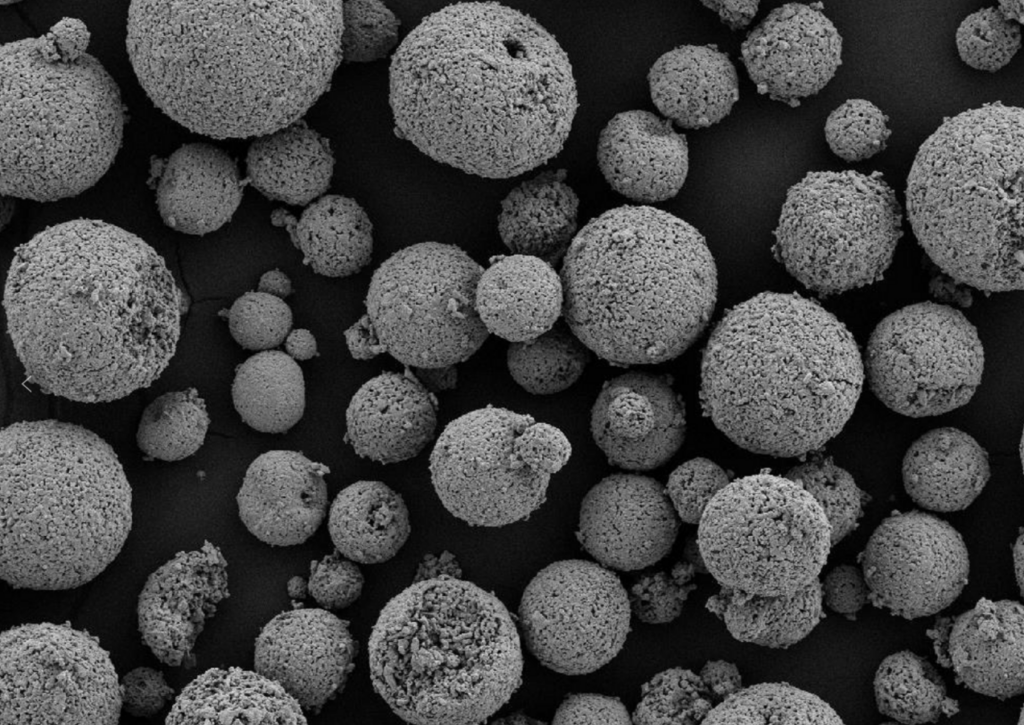
4. Pricing Factors for Metal Powders in Additive Manufacturing
4.1 Material Composition and Purity
The composition and purity of the metal powder are crucial factors influencing its price. Rare or exotic metals, such as titanium or cobalt-chromium alloys, tend to be more expensive due to their limited availability and higher production costs. Additionally, higher purity levels often require more extensive refining processes, contributing to increased additive manufacturing metal powder price.
4.2 Powder Particle Size and Shape
Particle size and shape significantly impact the flowability and packing density of metal powders. Finer powders with smaller particle sizes are more desirable for achieving higher resolution and smoother surface finishes. However, the production of fine powders requires specialized equipment and processes, which can increase costs.
4.3 Powder Production Methods
Different manufacturing techniques, such as gas atomization, water atomization, or plasma atomization, are used to produce metal powders. Each method has its advantages and associated costs. For example, gas atomization is a widely used method that produces spherical powders, but it may be more expensive than other techniques.
4.4 Powder Supplier and Quality Assurance
The choice of powder supplier is crucial to ensure consistent quality and reliability. Reputable suppliers invest in quality assurance measures, including certifications, rigorous testing, and traceability of their materials. While these suppliers may charge higher additive manufacturing metal powder price, they offer peace of mind and minimize the risk of using subpar powders.
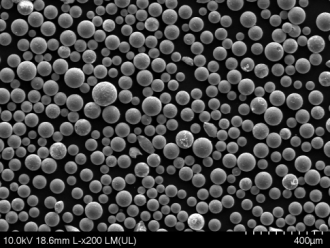
5. Current Trends in Additive Manufacturing Metal Powder Prices
The additive manufacturing metal powder price used in additive manufacturing are subject to various market trends and influences. Understanding these trends is vital for businesses to stay competitive and make informed decisions. The following factors impact the current metal powder prices:
- Market Demand and Supply: Fluctuations in market demand for additive manufacturing applications influence additive manufacturing metal powder price. Increased demand for specific metals or alloys can lead to price spikes, while oversupply may result in lower additive manufacturing metal powder price.
- Technological Advancements: As additive manufacturing technology evolves, new materials and improved production methods emerge. These advancements can impact additive manufacturing metal powder price, especially if they offer superior properties or cost-effective alternatives to existing powders.
- Industry Competition: The competitive landscape of additive manufacturing drives pricing strategies among powder suppliers. Intense competition may lead to price reductions or special offers to attract customers.
- Raw Material Costs: The cost of raw materials used to produce metal powders is a significant factor in pricing. Fluctuations in the prices of metals and other input materials, such as gas or electricity, can directly impact the overall cost of metal powders.
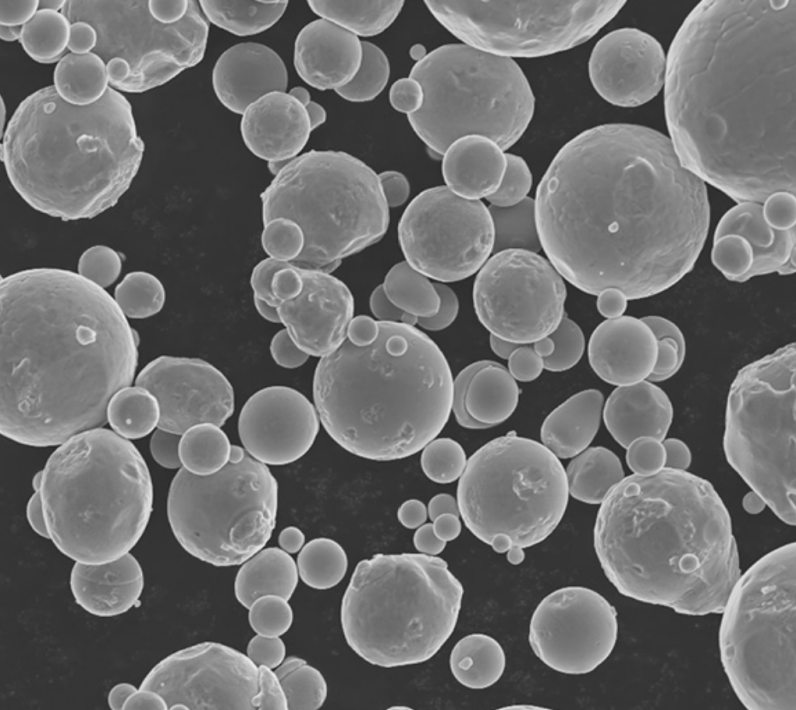
6. Strategies for Managing Metal Powder Costs
To manage metal powder costs effectively in additive manufacturing, businesses can consider the following strategies:
- Supplier Evaluation and Negotiation: Thoroughly evaluate potential powder suppliers based on their quality standards, certifications, and track records. Negotiate pricing agreements that balance cost and quality, considering long-term partnerships.
- Material Optimization and Waste Reduction: Optimize part designs and printing parameters to minimize material waste. Implementing nesting strategies, improving support structures, and reducing unnecessary build volumes can result in significant cost savings.
- Recycling and Reusing Metal Powders: Implement recycling programs to recover and reuse excess or used metal powders. Recycling reduces material costs and minimizes environmental impact. Establishing proper powder handling and recycling processes can help maximize resource utilization and minimize waste.
- Process Optimization: Continuously analyze and optimize the additive manufacturing process to enhance powder efficiency. Fine-tuning parameters such as layer thickness, laser power, and scanning speed can improve part quality while reducing the amount of powder consumed.
- Bulk Purchasing and Inventory Management: Consider purchasing metal powders in bulk to take advantage of volume discounts. Efficient inventory management practices, including just-in-time ordering and minimizing stockpiling, can help reduce holding costs and prevent material obsolescence.
- Collaboration and Knowledge Sharing: Engage with industry peers, research institutions, and additive manufacturing communities to share best practices and insights on cost-saving measures. Collaborative efforts can lead to innovative solutions and cost optimization strategies.
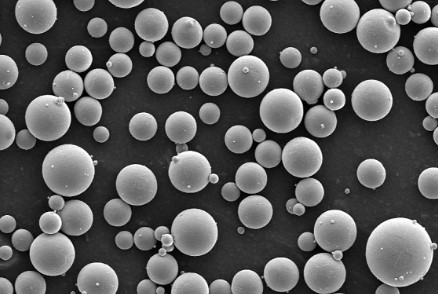
7. Future Outlook for Additive Manufacturing Metal Powder Prices
The future of additive manufacturing metal powder price in additive manufacturing will be shaped by various factors. As the technology becomes more widespread and demand increases, it is expected that economies of scale will drive down additive manufacturing metal powder pricefor certain metals. However, the introduction of new alloys, improved production methods, and evolving market dynamics may introduce pricing variations.
Advancements in powder manufacturing technologies, such as novel atomization methods or powder recycling techniques, could help reduce production costs and ultimately additive manufacturing metal powder prices. Additionally, ongoing research and development efforts focused on material optimization and alloy innovations may lead to cost-effective alternatives with enhanced properties.
It is crucial for businesses to closely monitor market trends, technological advancements, and supply chain dynamics to adapt to changing additive manufacturing metal powder price effectively. By staying informed and implementing cost management strategies, companies can navigate the evolving landscape of additive manufacturing and maintain competitiveness.
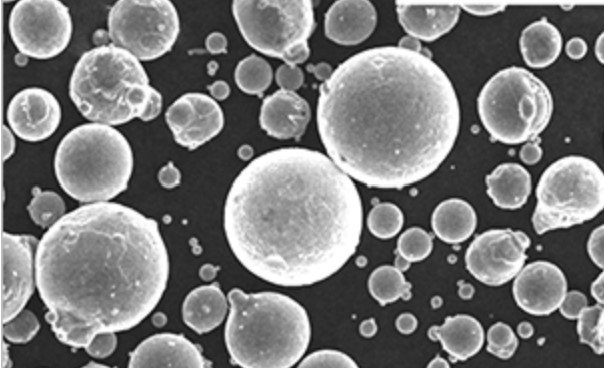
8. Conclusion
additive manufacturing metal powder price play a significant role in the overall cost of additive manufacturing. Understanding the factors influencing these prices, such as material composition, particle size, production methods, and supplier quality, is essential for businesses aiming to optimize their additive manufacturing processes.
By adopting strategies such as supplier evaluation, material optimization, recycling, process optimization, bulk purchasing, and collaboration, companies can effectively manage metal powder costs. Continuously monitoring market trends and technological advancements will also enable businesses to stay ahead in a rapidly evolving industry.
As additive manufacturing continues to revolutionize various sectors, including aerospace, automotive, healthcare, and more, managing metal powder costs will remain a critical aspect of achieving economic viability and driving innovation.
FAQs
1. Are metal powders the only materials used in additive manufacturing?
No, while metal powders are widely used in additive manufacturing, other materials such as polymers, ceramics, and composites can also be utilized depending on the desired application and requirements.
2. How can I ensure the quality of metal powders used in additive manufacturing?
Choosing reputable suppliers who adhere to strict quality standards, certifications, and traceability measures is essential. It is recommended to request material certifications, perform in-house testing, and collaborate with trusted partners to verify powder quality.
3. Can metal powders be recycled in additive manufacturing?
Yes, metal powders can be recycled and reused in additive manufacturing processes. Implementing proper powder handling, storage, and recycling systems can help minimize waste and reduce material costs.
4. Are metal powders used in additive manufacturing expensive?
The cost of metal powders varies depending on factors such as material composition, purity, particle size, and production methods. While certain metals or alloys may be relatively expensive, advancements in technology and increased market competition are gradually driving prices down.
5. How can additive manufacturing benefit from cost optimization?
Cost optimization in additive manufacturing can lead to enhanced profitability, increased competitiveness, and improved resource utilization. By implementing strategies such as material optimization, recycling, and process optimization, businesses can achieve cost savings and improve overall efficiency.