1. Introduction
In recent years, the field of additive manufacturing has witnessed significant advancements, especially in the realm of 3D printing with metal powders. Metal 3D printing offers a groundbreaking way to fabricate complex and intricate components with high precision and excellent mechanical properties. This article delves into the world of metal powders for 3D printing, exploring their benefits, types, processes, characteristics, and applications.
2. Understanding Metal Powders for 3D Printing
Metal powders are the building blocks of metal 3D printing. They are finely ground particles of various metals that are used as the raw material for additive manufacturing processes. These powders possess specific properties that allow them to be selectively melted and fused together to create three-dimensional objects layer by layer.
3. Benefits of Metal Powders in 3D Printing
The use of metal powders for 3d printing offers numerous advantages over traditional manufacturing methods. One key benefit is the ability to produce complex geometries that would be otherwise challenging or impossible to manufacture using conventional techniques. metal powders for 3d printing also enables rapid prototyping, reducing lead times and costs associated with tooling.
Furthermore, this technology allows for lightweight designs, as internal lattice structures and hollow parts can be easily integrated into the printed components. The ability to customize and optimize designs based on specific applications is another notable advantage. By leveraging metal powders, engineers can create parts with tailored mechanical properties, such as enhanced strength, durability, and heat resistance.
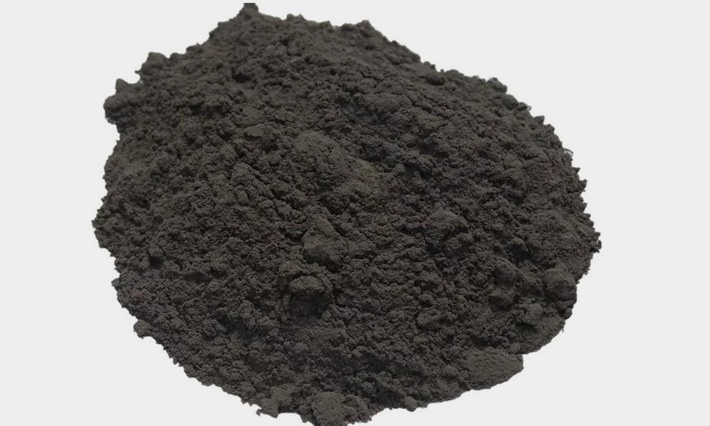
4. Types of Metal Powders Used in 3D Printing
metal powders for 3d printing encompasses a wide range of materials, each with its own unique characteristics and applications. Some commonly used metal powders include:
4.1 Stainless Steel Powders
Stainless steel powders are popular for their corrosion resistance, making them suitable for applications in the automotive, aerospace, and medical industries. They offer good strength and high-temperature resistance.
4.2 Titanium Powders
Titanium powders are renowned for their excellent strength-to-weight ratio and biocompatibility. They find extensive use in the aerospace, medical, and automotive sectors, where lightweight and high-strength components are essential.
4.3 Aluminum Powders
Aluminum powders are valued for their low density, good thermal conductivity, and high strength. They are widely employed in the aerospace, automotive, and consumer electronics industries, enabling the production of lightweight parts.
4.4 Nickel Powders
Nickel powders possess excellent corrosion resistance and high-temperature properties. They are utilized in applications such as chemical processing, electronics, and power generation.
4.5 Copper Powders
Copper powders offer high electrical and thermal conductivity, making them suitable for applications in electronics, telecommunications, and heat exchangers.
4.6 Other Metal Powders
In addition to the above, there are various other metal powders for 3d printing, including cobalt, bronze, and precious metals like gold and silver. These materials find their applications in diverse industries, such as jewelry, dental, and artistic creations.
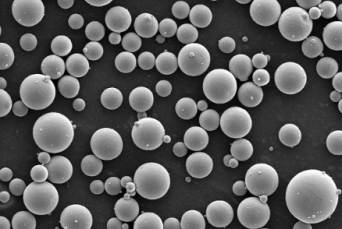
5. Powder Bed Fusion (PBF) Process
The powder bed fusion (PBF) process is one of the primary techniques employed in metal 3D printing. It involves selectively melting and fusing metal powders layer by layer to create complex parts. There are two main variations of the PBF process:
5.1 Selective Laser Melting (SLM)
Selective Laser Melting (SLM) utilizes a high-power laser beam to selectively melt and fuse metal powders for 3d printing. The laser scans the powder bed according to the desired cross-section of the part, solidifying the material layer by layer.
5.2 Electron Beam Melting (EBM)
Electron Beam Melting (EBM) uses an electron beam instead of a laser to melt and fuse the metal powders for 3d printing. EBM operates in a vacuum environment and can achieve higher build speeds compared to SLM.
6. Direct Energy Deposition (DED) Process
Apart from PBF, another metal 3D printing technique is Direct Energy Deposition (DED). This process involves melting metal powders for 3d printing using a focused energy source, such as a laser or electron beam, while simultaneously depositing the molten material onto a substrate. DED allows for the production of large-scale components and repair of existing parts.
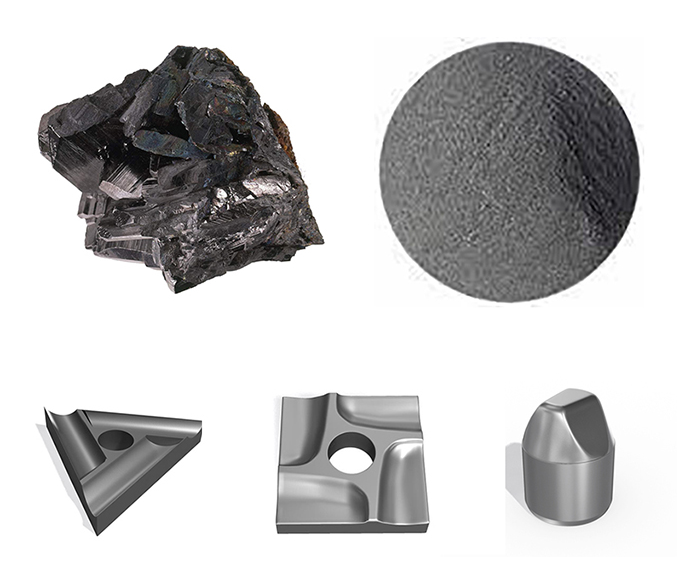
7. Metal Powder Characteristics for 3D Printing
To ensure successful and high-quality metal 3D printing, several powder characteristics need to be considered:
7.1 Particle Size and Distribution
The particle size and distribution of metal powders for 3d printing significantly impact the print quality and final part properties. A narrow particle size distribution promotes uniform melting and reduces the risk of defects.
7.2 Powder Morphology
The shape and surface characteristics of metal powders for 3d printing influence their flowability and packing density. Spherical powders are generally preferred due to their improved flowability and packing efficiency.
7.3 Powder Flowability
Powder flowability is crucial for achieving consistent powder spreading and uniform layer thickness during the printing process. Proper flowability ensures optimal powder bed density and minimizes the risk of powder agglomeration.
7.4 Powder Density
The density of metal powders for 3d printing affects the mechanical properties of printed parts. Higher powder density generally results in improved strength and lower porosity in the final components.
7.5 Powder Composition and Purity
The composition and purity of metal powders for 3d printing directly impact the material properties of the printed parts. It is essential to use high-quality powders with the desired alloy composition and minimal impurities.
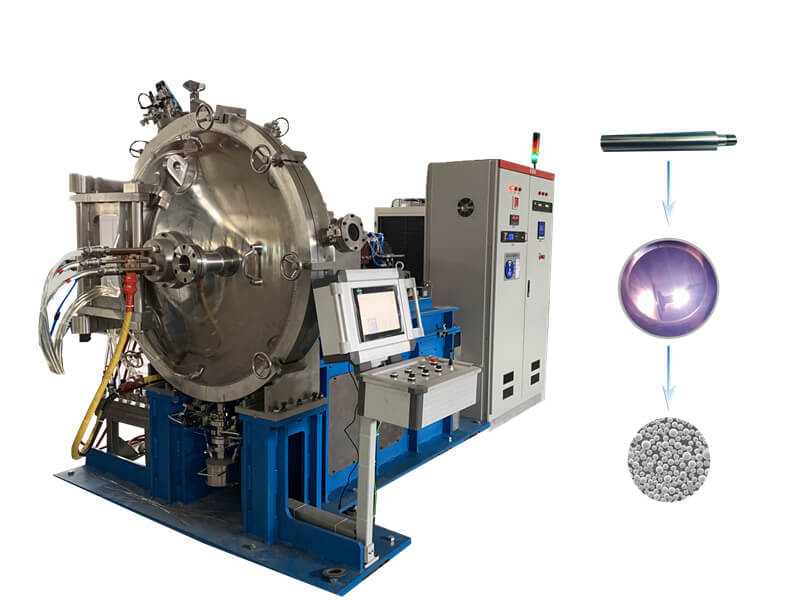
8. Preparing Metal Powders for 3D Printing
Proper handling and preparation of metal powders for 3d printing are critical to ensure successful printing and maintain powder integrity:
8.1 Powder Handling and Storage
Metal powders must be stored and handled in controlled environments to prevent contamination and oxidation. The use of appropriate storage containers and humidity-controlled rooms helps maintain the quality of the powders.
8.2 Powder Reusability
In many cases, metal powders for 3d printing can be reused to minimize material waste and costs. However, the powders must undergo careful analysis and testing to ensure they meet the required quality standards. Various techniques, such as sieving and sieving analysis, are employed to assess the powder’s condition and suitability for reuse.
9. Considerations for Successful Metal 3D Printing
To achieve successful metal 3D printing, several considerations should be taken into account throughout the process:
9.1 Design Considerations
Designing parts for metal powders for 3d printing requires understanding the capabilities and limitations of the technology. It is essential to optimize designs for additive manufacturing, considering factors like support structures, overhangs, and thermal stress. Designing with specific applications in mind enables the creation of innovative and functional components.
9.2 Post-Processing and Finishing
Metal 3D printed parts often require post-processing and finishing to achieve the desired surface finish and dimensional accuracy. Techniques like machining, polishing, and heat treatment may be employed to remove support structures, improve surface quality, and enhance mechanical properties.
9.3 Quality Control and Testing
Maintaining quality control throughout the metal 3D printing process is crucial. In-process monitoring, inspection, and testing ensure that parts meet specified tolerances, structural integrity, and material properties. Non-destructive testing methods like X-ray and CT scanning help identify defects or inconsistencies in the printed components.
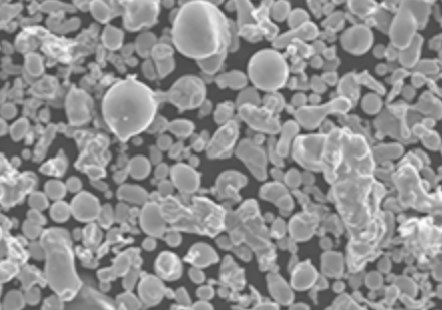
10. Applications of Metal 3D Printing
Metal 3D printing finds applications across a wide range of industries:
10.1 Aerospace and Defense
Metal 3D printing revolutionizes aerospace and defense manufacturing by enabling the production of lightweight, complex, and high-performance components. It allows for the creation of optimized geometries, reducing weight while maintaining structural integrity and meeting stringent industry standards.
10.2 Automotive
In the automotive sector, metal 3D printing offers opportunities for lightweighting, part consolidation, and rapid prototyping. It enables the production of customized components, including engine parts, brackets, and suspension components, resulting in improved performance and fuel efficiency.
10.3 Healthcare
Metal 3D printing has made significant contributions to the healthcare industry. It allows for the production of patient-specific implants, prosthetics, and surgical instruments with optimized designs and biocompatible materials. This technology facilitates faster and more accurate medical interventions, improving patient outcomes.
10.4 Industrial Manufacturing
Metal 3D printing is increasingly adopted in industrial manufacturing for the production of complex tooling, molds, and jigs. It enables faster turnaround times, reduces material waste, and provides greater design freedom for customized manufacturing solutions.
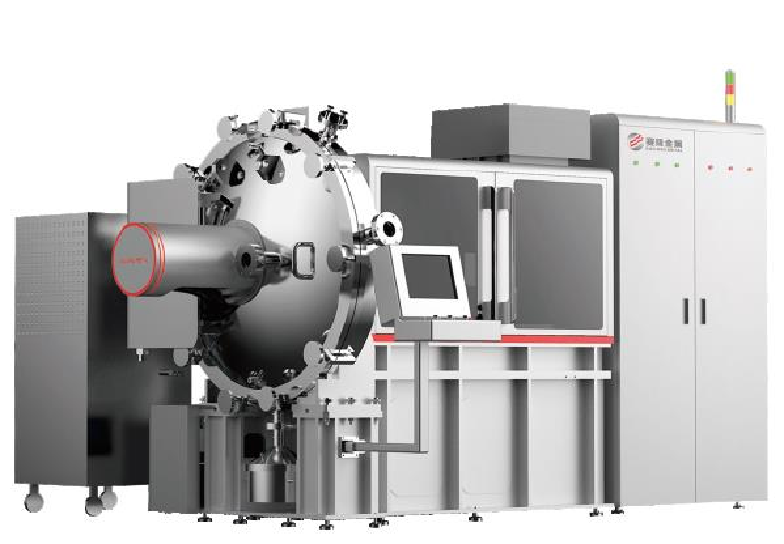
11. Future Trends in Metal 3D Printing
Metal 3D printing continues to evolve rapidly, and several exciting trends are shaping its future:
- Advancements in material development: Research efforts focus on developing new metal alloys with enhanced properties, expanding the range of materials available for 3D printing.
- Improved printing processes: Ongoing research aims to increase printing speeds, improve accuracy, and reduce costs to make metal 3D printing more accessible to a broader range of industries.
- Multi-material printing: The ability to print parts with multiple materials or varying compositions opens up new possibilities for creating functional and composite structures.
- Integration of other manufacturing processes: Hybrid approaches that combine metal 3D printing with other manufacturing techniques, such as CNC machining or post-process surface treatments, offer opportunities for improved efficiency and cost-effectiveness.
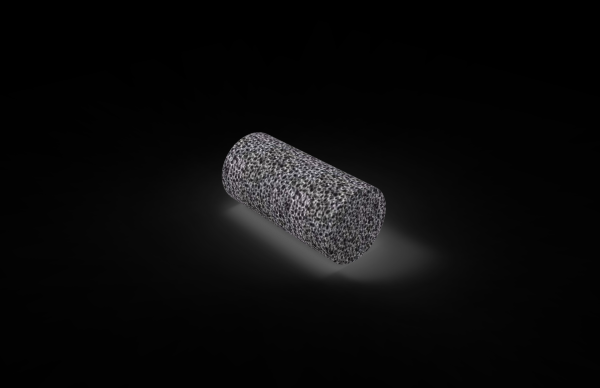
12. Conclusion
Metal powders for 3D printing have revolutionized the manufacturing industry, enabling the production of complex and customized components with superior mechanical properties. This article explored the benefits of metal powders, various types used in 3D printing, the powder bed fusion and direct energy deposition processes, powder characteristics, and considerations for successful printing. It also highlighted the applications of metal 3D printing across industries and discussed future trends in the field. With ongoing advancements, metal 3D printing is poised to reshape the manufacturing landscape and unlock new possibilities in design and production.
FAQs
Q1: Can any metal be used in 3D printing? Yes, a wide range of metals can be used in 3D printing, including stainless steel, titanium, aluminum, nickel, copper, and more.
Q2: What are the advantages of metal 3D printing over traditional manufacturing methods? Metal 3D printing offers benefits such as the ability to create complex geometries, rapid prototyping, lightweight designs, and customized mechanical properties.
Q3: Are metal 3D printed parts as strong as traditionally manufactured parts? Yes, properly designed and manufactured metal 3D printed parts can exhibit comparable strength and mechanical properties to traditionally manufactured parts.
Q4: Can metal powders be reused in 3D printing? In many cases, metal powders can be reused, but careful analysis and testing are required to ensure their suitability for reuse.
Q5: What are some emerging applications of metal 3D printing? Emerging applications include aerospace and defense manufacturing, automotive components, healthcare implants, and industrial manufacturing for tooling and jigs.