1. Introduction
Additive manufacturing, also known as 3D printing, has emerged as a transformative technology across various industries. One of the most promising areas of additive manufacturing is the production of metal components, including aluminium. This article provides a comprehensive overview of aluminium additive manufacturing, highlighting its benefits, applications, challenges, recent developments, and future outlook.
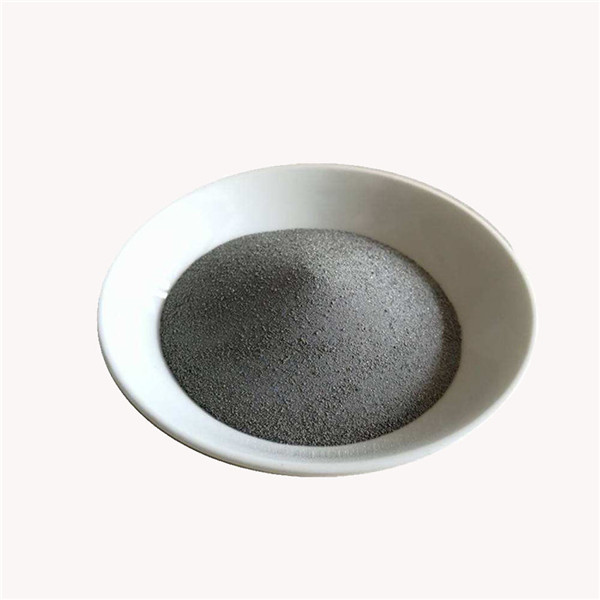
2. Benefits of Aluminium Additive Manufacturing
Aluminium additive manufacturing offers numerous advantages over traditional manufacturing methods.
Lightweight and High Strength
One of the key benefits of aluminium additive manufacturing is its ability to produce lightweight and high-strength components. The unique layer-by-layer fabrication process enables the creation of complex geometries and internal structures that enhance strength while reducing weight. This makes aluminium additive manufacturing particularly valuable in industries where weight reduction is critical, such as aerospace and automotive.
Design Flexibility and Customization
Another advantage of aluminium additive manufacturing is its unparalleled design flexibility. Traditional manufacturing often imposes limitations on complex designs, but with additive manufacturing, intricate shapes and internal features can be easily achieved. This enables engineers and designers to optimize part performance and functionality. Furthermore, additive manufacturing allows for customization on a mass scale, empowering companies to cater to individual customer preferences and needs.
Cost-Effectiveness
While the initial setup costs for aluminium additive manufacturing can be higher compared to traditional methods, it offers long-term cost savings. Additive manufacturing eliminates the need for costly tooling and reduces material waste since parts are built layer by layer, using only the required amount of material. This makes it cost-effective, especially for low-volume production or complex parts that would be expensive to produce using conventional methods.
Reduced Waste and Sustainability
Aluminium additive manufacturing promotes sustainability by significantly reducing waste. Traditional manufacturing processes often generate substantial amounts of scrap material, whereas additive manufacturing minimizes waste by using only the necessary material for each component. Additionally, the ability to recycle and reuse metal powders further enhances the sustainability of aluminium additive manufacturing.
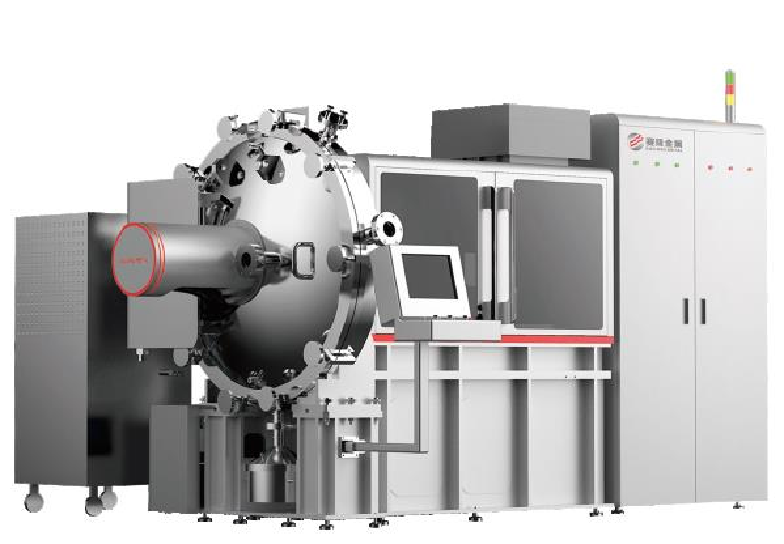
3. Applications of Aluminium Additive Manufacturing
The versatility of aluminium additive manufacturing opens up a wide range of applications across various industries.
Aerospace Industry
The aerospace industry benefits greatly from aluminium additive manufacturing due to the need for lightweight, high-strength components. Additive manufacturing enables the production of complex aerospace parts, such as engine components, turbine blades, and structural elements, with reduced weight and improved performance.
Automotive Industry
In the automotive sector, aluminium additive manufacturing is utilized for prototyping, tooling, and the production of lightweight components. By using additive manufacturing, automakers can reduce vehicle weight, leading to improved fuel efficiency and reduced emissions.
Medical Industry
In the medical field, aluminium additive manufacturing finds applications in the production of orthopedic implants, prosthetics, and surgical instruments. The ability to customize and tailor implants to fit individual patients’ needs is a significant advantage of additive manufacturing, leading to better patient outcomes and reduced surgery time.
Consumer Goods Industry
The consumer goods industry leverages aluminium additive manufacturing for the production of intricate and personalized products. From jewelry and accessories to household items and electronic devices, additive manufacturing allows for creative designs and customization, providing consumers with unique and tailored products.
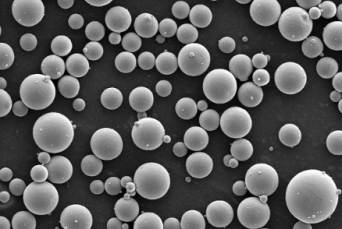
4. Challenges and Limitations of Aluminium Additive Manufacturing
While aluminium additive manufacturing offers numerous benefits, there are also challenges and limitations to consider.
Material Properties and Quality Control
Achieving consistent material properties and ensuring quality control throughout the additive manufacturing process can be challenging. Variations in powder quality, porosity, and microstructural defects may affect the mechanical properties of printed aluminium parts. Robust quality control measures and advancements in material characterization are essential to address these concerns.
Post-Processing Requirements
Post-processing of aluminium additive manufactured parts is often necessary to achieve the desired surface finish, dimensional accuracy, and mechanical properties. Additional steps such as heat treatment, machining, and surface finishing may be required, adding to the overall production time and cost.
Cost Considerations
While aluminium additive manufacturing can be cost-effective for certain applications, it may still be more expensive than traditional manufacturing methods for high-volume production. The cost of equipment, materials, and post-processing should be carefully evaluated to determine the economic feasibility of adopting additive manufacturing.
Scaling up Production
Scaling up the production of aluminium additive manufactured parts can be a challenge. The layer-by-layer nature of the process may limit the production rate, making it difficult to meet high-demand requirements. Developing efficient and scalable additive manufacturing systems is crucial to address this limitation.
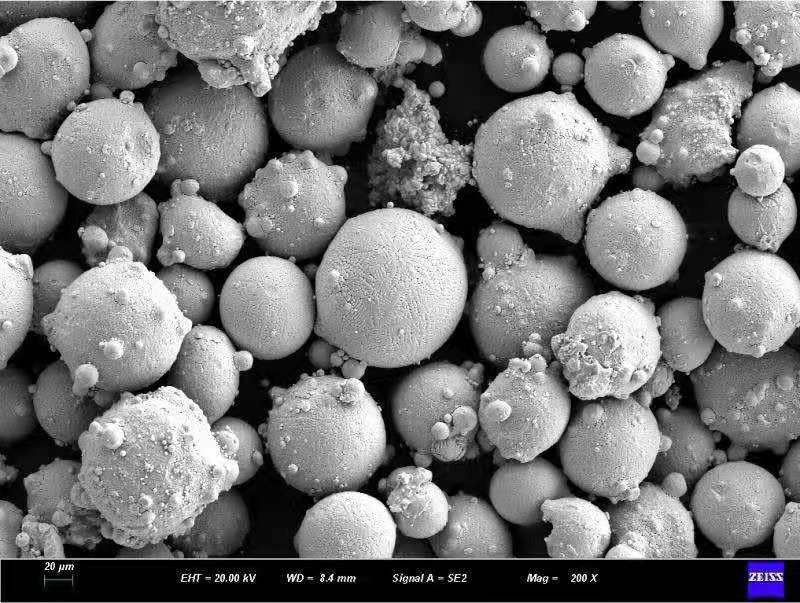
5. Recent Developments and Innovations in Aluminium Additive Manufacturing
The field of aluminium additive manufacturing is rapidly evolving, with several recent developments and innovations driving its progress.
Improved Metal Powder Quality
Advancements in powder metallurgy and the development of high-quality aluminium powders have contributed to enhanced material properties and process reliability. The availability of high-performance powders facilitates the production of aluminium components with improved mechanical properties and surface finish.
Advanced Process Monitoring and Control
The integration of advanced monitoring and control systems in aluminium additive manufacturing enables real-time monitoring of process parameters and ensures consistent part quality. Sensors and data analytics help identify deviations, optimize process parameters, and minimize defects, enhancing the reliability and repeatability of additive manufacturing.
Integration of Artificial Intelligence and Machine Learning
Artificial intelligence (AI) and machine learning (ML) algorithms are being applied to aluminium additive manufacturing to optimize process parameters, predict part quality, and improve overall efficiency. AI-driven algorithms can analyze vast amounts of data and optimize printing strategies, leading to improved part performance and reduced production time.
Hybrid Manufacturing Approaches
Hybrid manufacturing, combining additive manufacturing with traditional machining or other processes, is gaining traction in the aluminium additive manufacturing field. This approach allows for the production of complex parts with superior surface finish and dimensional accuracy, leveraging the strengths of both additive and subtractive manufacturing methods.
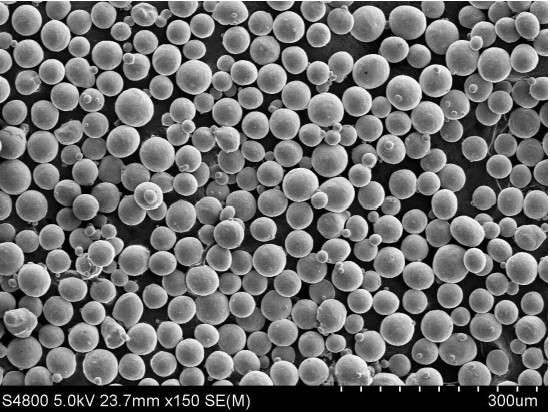
6. Future Outlook of Aluminium Additive Manufacturing
The future of aluminium additive manufacturing looks promising, with several exciting possibilities on the horizon.
Expansion of Applications
As the technology continues to advance and overcome existing limitations, the range of applications for aluminium additive manufacturing is expected to expand further. Industries such as defense, energy, and electronics are likely to embrace additive manufacturing for the production of aluminium components, driving innovation and opening new opportunities.
Enhanced Material Properties
Ongoing research and development efforts aim to improve the material properties of aluminium additive manufactured parts. This includes enhancing mechanical strength, fatigue resistance, and corrosion resistance.
Increased Adoption in Various Industries
With the continuous advancements in aluminium additive manufacturing and the growing awareness of its benefits, more industries are expected to adopt this technology. Sectors such as marine, renewable energy, and telecommunications can leverage the advantages of lightweight and durable aluminium components, leading to increased adoption and integration of additive manufacturing.
Collaborations and Research Initiatives
Collaborations between academia, industry, and research institutions play a vital role in advancing aluminium additive manufacturing. Joint research initiatives and knowledge sharing help accelerate the development of new materials, process optimization techniques, and innovative applications. These collaborative efforts contribute to the overall growth and maturation of the technology.
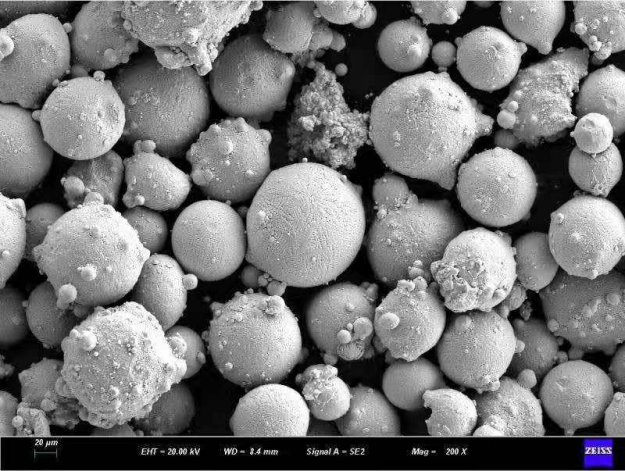
7. Conclusion
Aluminium additive manufacturing is revolutionizing metal fabrication, offering a wide range of benefits and applications. Its lightweight and high-strength properties, design flexibility, cost-effectiveness, and sustainability make it a compelling choice for industries seeking innovation and efficiency. While challenges such as material properties, post-processing, cost considerations, and scalability exist, ongoing research and technological advancements are addressing these limitations. With recent developments in metal powder quality, process monitoring, AI integration, and hybrid manufacturing, the future of aluminium additive manufacturing holds great promise. As industries continue to explore and embrace this technology, we can expect to witness further expansion of applications, improved material properties, and increased collaboration, leading to a bright future for aluminium additive manufacturing.
FAQs
1. Is aluminium additive manufacturing suitable for large-scale production? Aluminium additive manufacturing is best suited for low-volume production or complex parts where traditional methods may be costlier or less efficient. However, advancements in technology are gradually enabling scalability, and it may become viable for larger-scale production in the future.
2. How does aluminium additive manufacturing contribute to sustainability? Aluminium additive manufacturing reduces material waste by using only the necessary amount of aluminium powder. It also enables the recycling and reuse of excess powder, minimizing environmental impact and promoting sustainability compared to traditional manufacturing processes.
3. Can aluminium additive manufactured parts achieve the same strength as conventionally manufactured parts? With proper process optimization, aluminium additive manufactured parts can achieve comparable strength to conventionally manufactured parts. However, it requires careful consideration of process parameters, material properties, and post-processing techniques to ensure optimal mechanical properties.
4. Are there any specific design limitations in aluminium additive manufacturing? Aluminium additive manufacturing offers great design freedom, but certain factors such as overhangs, support structures, and surface finishes should be taken into account during the design phase. Design guidelines and software tools are available to help optimize designs for additive manufacturing.
5. How does aluminium additive manufacturing benefit the aerospace industry? Aluminium additive manufacturing enables the production of lightweight and complex aerospace components, leading to reduced fuel consumption, improved performance, and lower emissions. It also allows for rapid prototyping and customization, enhancing design flexibility and innovation in the aerospace sector.