Introduction
3D printing, also known as additive manufacturing, has revolutionized production across industries. The technology builds objects layer by layer using materials like plastics, metals, ceramics, and even living cells. 3D printing offers advantages like mass customization, rapid prototyping, and distributed manufacturing. One of the most promising materials for 3D printing is metal, allowing the production of end-use parts with high strength and durability.
molybdenum disilicide powder is an advanced ceramic material that is gaining popularity as a metal powder for 3D printing. MoSi2 offers exceptional properties that make it well-suited for 3D printed parts across aerospace, automotive, medical, and industrial applications.
What is molybdenum disilicide powder?
Molybdenum disilicide (MoSi2) is an intermetallic ceramic compound composed of molybdenum and silicon atoms in a 1:2 ratio. It has a tetragonal crystal structure and is classified as a refractory ceramic due to its high melting point of 2,030°C.
Some key properties of molybdenum disilicide include:
- High melting point – Enables use in high temperature applications up to 1,700°C in oxidizing environments
- Low density – Approximately 6.24 g/cm3, providing weight savings
- Excellent oxidation resistance – Forms a protective SiO2 layer at high temperatures
- Thermal conductivity – Up to 125 W/mK, for good heat dissipation
- Thermal shock resistance – Resists cracking from thermal stresses
- High strength – Flexural strength around 700 MPa at room temperature
These attributes make MoSi2 suitable for demanding applications in extreme environments. The material has been used for decades in high-temperature heating elements and thermal management applications. More recently, it has emerged as an exceptional powder bed material for 3D printing high-performance metal parts.
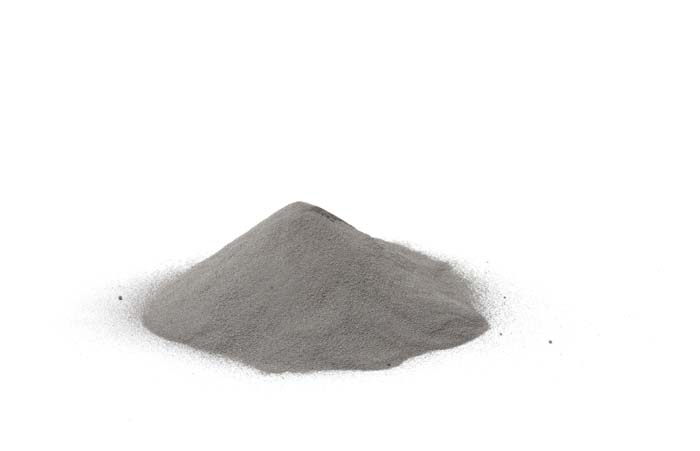
Why Use MoSi2 Powder for 3D Printing?
Molybdenum disilicide possesses a unique combination of properties that make it a prime candidate for 3D printing high-strength, thermally stable metal components.
High Melting Point
The very high melting point of MoSi2 allows 3D printed parts to maintain their strength and shape at elevated temperatures exceeding 1500°C. This enables use of the material in extremely hot environments.
Oxidation Resistance
MoSi2 forms a protective silica (SiO2) layer when exposed to oxygen at high temperatures. This oxide scale protects the material from further oxidation and corrosion. The oxidation resistance allows 3D printed MoSi2 components to operate in air or oxidizing atmospheres at high temperatures.
Thermal Properties
The low coefficient of thermal expansion minimizes thermal stresses, while the high thermal conductivity enables effective dissipation of heat from 3D printed metal parts. This results in excellent thermal shock resistance for cyclic heating applications.
High Strength
MoSi2 maintains good strength and creep resistance at high temperatures. Its room temperature flexural strength exceeds 700 MPa, making it stronger than many steel alloys. This allows lightweight, high-strength parts to be 3D printed.
Low Density
With a density around 6.2 g/cm3, MoSi2 is significantly lighter than traditional high-temperature alloys based on tungsten or molybdenum. The lower density enables lighter weight components to be fabricated.
Processability
MoSi2 powder can be processed using standard powder bed fusion techniques for metals, allowing complex geometries to be easily fabricated. Parts can be post-processed via hot isostatic pressing (HIP) to further enhance densification and properties.
The combination of these attributes makes MoSi2 an exceptional material for 3D printing high-performance components for use in extreme environments and advanced applications.
How is MoSi2 Powder Produced?
Molybdenum disilicide powder for 3D printing is commercially produced via several methods, most commonly involving high temperature reactions between molybdenum and silicon.
Some key production routes include:
Reaction of Mo and Si Elements
MoSi2 powder can be synthesized by reacting molybdenum powder directly with silicon powder at temperatures exceeding 1,400°C in either vacuum or inert gas atmospheres. The powders are milled together and undergo the following reaction:
Mo (s) + 2Si (s) → MoSi2 (s)
Reduction of MoO3
MoSi2 powder can be produced by reducing molybdenum trioxide (MoO3) powder with silicon, carbon, or hydrogen gas. This involves heating a mixture of MoO3 and Si powder to over 1,000°C to initiate the reductions:
MoO3 (s) + Si (s) → MoSi2 (s) + SiO2 (g)
MoO3 (s) + 3C (s) → MoSi2 (s) + 3CO (g)
MoO3 (s) + 3H2 (g) → MoSi2 (s) + 3H2O (g)
Siliconization of Mo
MoSi2 is formed by heating molybdenum metal powder with silicon vapor or silicon-containing gases like silane (SiH4). The gaseous silicon diffuses into the Mo powder particles to produce MoSi2 at the particle surfaces.
Mo (s) + 2SiH4 (g) → MoSi2 (s) + 4H2 (g)
The resulting MoSi2 powder is further milled and sieved to achieve the desired particle size distributions for 3D printing applications.
MoSi2 Powder Properties for 3D Printing
Molybdenum disilicide powders destined for 3D printing must meet exacting specifications for properties like particle size, shape, and purity to enable high density printing.
Particle Size
Typical size distributions are 10-45 μm or 15-53 μm. Fine powders promote powder spreading and density, while large particles improve powder flowability. Particle size affects the minimum feature resolution.
Particle Morphology
Spherical, rounded powder particles allow smooth powder spreading and packing during printing. Irregularly-shaped particles hinder powder flow and can negatively impact density.
Purity
High chemical purity (>99.5% MoSi2) is required to avoid issues with contamination affecting densification and properties. Critical impurities to control are oxygen, carbon, and metallic elements.
Flowability
The powder must have flow properties matched to the printer powder handling system. Flow rates, shear forces, and spreadability are important parameters.
Tap Density
Higher tap densities allow more powder to be packed into a given volume, increasing print resolution and reducing porosity. Tap densities of 4-5 g/cm3 are typical.
Maintaining strict control over these powder characteristics ensures reliable, high-quality printing using MoSi2 feedstock. Print parameters and post-processing are also critical to achieve fully dense parts.
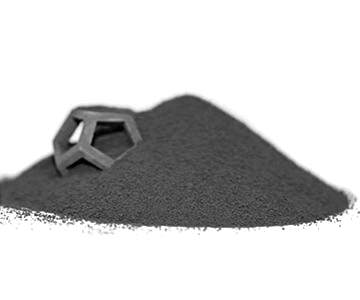
Key Applications of 3D Printed MoSi2 Components
The exceptional high-temperature properties of molybdenum disilicide enable many new applications of 3D printed metal parts using MoSi2 powder feedstocks.
Aerospace
- Engine components – Turbine blades, nozzles, combustion chambers
- Hypersonic vehicles – Leading edges, propulsion systems
- Spacecraft – Thrusters, engines, mirrors
Energy
- Nuclear reactors – Fuel cladding, heat exchangers
- Fossil fuel systems – Wellbore components, valves, tooling
- Solar concentrators – Reflectors, heat exchangers
Automotive
- Racing components – Pistons, turbochargers, exhaust
- Sensors – High temperature pressure, gas sensors
- Heating elements – Igniters, glow plugs
Industrial
- Glass molds – Precision cast parts resistant to molten glass
- Extrusion dies – For ceramics, metals, polymers
- Heating elements – High temperature furnace components
Medical
- Orthopedic implants – Joint replacements resistant to wear
- Dental implants – Tooth replacements and bridges
The high melting point, strength, and oxidation resistance of MoSi2 enables components to survive and function in challenging environments exceeding 1,500°C. 3D printing facilitates fabrication of complex, high-performance parts tailored to these demanding applications.
The 3D Printing Process for MoSi2
Molybdenum disilicide components are fabricated using standard powder bed fusion techniques adapted for high temperature materials. This involves selectively melting layers of MoSi2 powder using a focused heat source in an inert atmosphere.
Powder Bed Fusion
Powder bed fusion (PBF) uses either a laser or electron beam to selectively melt and fuse material spread in a thin layer over a build plate. The process takes place inside a sealed chamber filled with an inert gas like argon or nitrogen.
Common PBF techniques used with MoSi2 include:
- Selective laser melting (SLM) – Uses a high power laser as heat source
- Electron beam melting (EBM) – Uses a focused beam of electrons for melting
Printing Process
The general 3D printing process for MoSi2 involves:
- MoSi2 powder is spread in a thin layer over the build platform using a recoater blade or powder spreading system
- The laser or ebeam selectively scans and melts regions of the powder bed corresponding to the part cross-section
- The build platform lowers, another layer of powder is spread over the top, and the process repeats
- After all layers are complete, the 3D printed part is removed from the powder bed
- Unfused powder is recovered and sieved for reuse in subsequent prints
Inert Atmosphere
Printing is performed under vacuum or in inert atmospheres with oxygen content below 50 ppm to prevent oxidation of the MoSi2 powder. Common atmospheres are argon, nitrogen, or mixtures like Ar-5%H2.
Post-Processing
As-printed MoSi2 parts often undergo post-processing like hot isostatic pressing (HIP) to increase density and improve material properties after printing. This densifies any residual porosity.
Key Print Parameters for MoSi2
Printing high-quality, fully dense MoSi2 components requires optimization of print parameters tailored to the material’s unique properties and powder characteristics.
Laser Power
- Typical range of 50-500 W
- Higher power densities promote melting and densification
- Excessive power can cause evaporation or ablation
Scan Speed
- Speeds of 100-1000 mm/s
- Slower scans increase energy input and densification
- Fast scans can generate porosity defects
Hatch Spacing
- Spacing of ~50-200 μm between scan lines
- Wider spacing causes porosity between melt pools
- Narrower spacing increases density
Layer Thickness
- Layer thickness of 20-100 μm
- Thinner layers improve resolution and accuracy
- Thicker layers build parts faster
Inert Gas Flow
- Low flow rates <10 L/min during printing
- Removes process byproducts like silica
- Higher flow can disturb unmelted powder
Preheating Temperature
- Substrate preheat of 300-1000°C
- Improves powder sintering and thermal conductivity
- Reduces residual stresses and cracking
Optimization of these parameters is needed to achieve fully dense, void-free MoSi2 printed parts with good structural integrity and properties.
Post-Processing Methods for MoSi2 Parts
As-printed molybdenum disilicide components often undergo additional post-processing to improve their material properties and performance.
Hot Isostatic Pressing (HIP)
HIP simultaneously applies heat and high isostatic pressure to close internal voids and increase density. Typical HIP conditions are 1,200°C at 100-200 MPa for 2-4 hours in an inert atmosphere. This can improve density to over 99%.
Heat Treatment
Heat treatment at 1,400-1,600°C in inert gas or vacuum further densifies parts by promoting sintering and grain growth. This also relieves residual stresses from printing.
Surface Machining
Machining operations like milling or grinding can be applied to improve surface finish and dimensional accuracy of printed parts. This also removes any surface defects.
Coatings
Applying ceramic coatings by chemical or physical vapor deposition provides environmental protection. Aluminide and silicide coatings improve oxidation and corrosion resistance.
Infiltration
For highly porous prints, infiltrating filler metals like copper or nickel increases densification and strength. This converts the component to a MoSi2-metal composite.
The combination of printing process refinement and appropriate post-processing enables MoSi2 parts with optimal microstructure and the designed material properties.
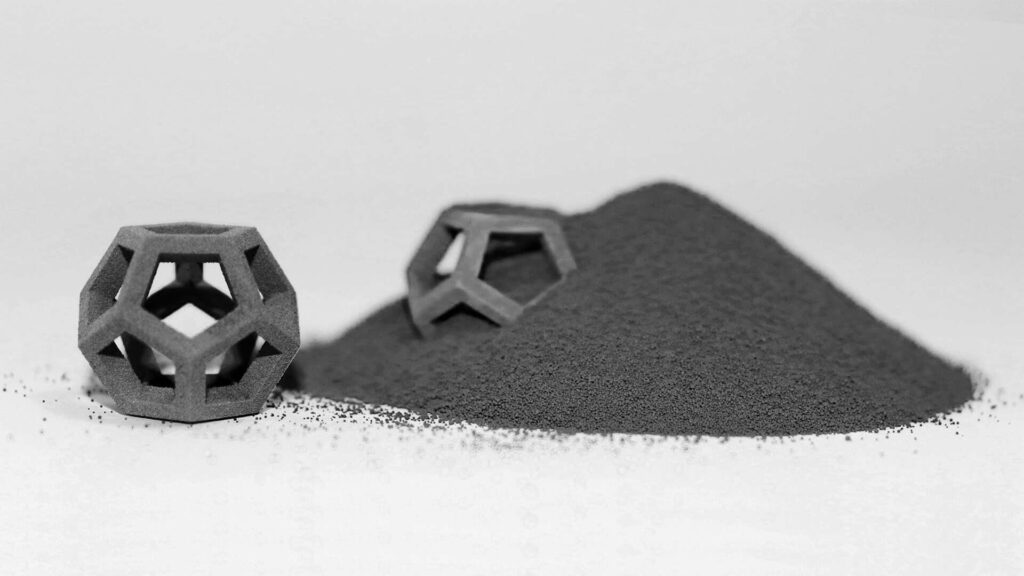
Microstructure of Printed MoSi2
The microstructure of as-printed MoSi2 differs notably from conventional MoSi2 ceramics produced via powder processing and sintering. This has important implications for the material’s properties.
Grain Structure
- Primarily elongated columnar grains aligned in the build direction
- Epitaxial growth across melt pools produces crystalline continuity
- Equiaxed fine grains in some regions
- Overall grain size typically 10-100 μm
Defects
- Porosity from lack of fusion defects
- Cracks between layers from residual stresses
- Occasional unmelted particles along grain boundaries
Phases
- Predominantly tetragonal β-MoSi2 phase
- Small fractions of hexagonal α-MoSi2 in some cases
- Traces of molybdenum and silicide sub-phases
Composition
- Close to nominal MoSi2 stoichiometry
- Some Si loss via evaporation causes slight Mo-rich composition
- Oxygen pickup to levels of 0.5-1 wt%
The unique as-printed microstructure results from the rapid melting and solidification during the layerwise printing process. Maximizing density and optimizing grain structure are active research areas.
Mechanical Properties of Printed MoSi2
Molybdenum disilicide printed by powder bed fusion exhibits good mechanical properties thanks to its strong atomic bonding, refractory nature, and microstructural design.
Strength
- High flexural strength up to ~850 MPa
- Compressive strength over 1,500 MPa
- Tensile strength ranges from 200-450 MPa
Hardness
- Vickers hardness of 5-9 GPa depending on density
- Approaches sintered MoSi2 hardness
Fracture Toughness
- Reported values of 4-7 MPafm^1/2
- Lower than sintered MoSi2 due to microcracking
High Temperature Strength
- Strengths exceeding 500 MPa at 1,000°C
- Gradual decrease above 1,200°C
- Better than sintered MoSi2
Thermal Shock Resistance
- Thermal shock parameter of 250-400 W/m
- Resists cracking during thermal cycling
With further refinement of printing and post-processing, the properties of 3D printed MoSi2 parts continue to improve toward their theoretical limits.
Advantages and Potential Issues of MoSi2 Powder Printing
Molybdenum disilicide clearly possesses outstanding properties that make it highly attractive for printing high-performance metal components. However, there are some disadvantages and technical challenges that must be addressed.
Advantages
- High strength maintained to over 1500°C
- Excellent oxidation resistance in air
- Lower density than tungsten or molybdenum alloys
- Complex geometries can be printed
- Properties exceeded sintered MoSi2
Potential Issues
- Brittleness and susceptibility to cracking
- Amount of porosity in as-printed parts
- Powder handling difficulties from irregular particles
- Relatively high material costs
- Lack of alloy development compared to superalloys
Continued research to optimize printing parameters, develop new alloy compositions, and improve post-processing will help overcome current limitations with MoSi2 additive manufacturing.
Cost Analysis of MoSi2 Powder
Molybdenum disilicide powder for 3D printing has costs significantly above conventional metal powders like stainless steel. However, the price differential is justified for extremely demanding, high-temperature applications.
Raw Material Costs
- Molybdenum metal prices range from $25-40/lb
- Silicon metal prices range from $1-2/lb
- Powder production yields are 70-90%
MoSi2 Powder Cost
- Typical MoSi2 powder costs are $75-150/lb
- Approximately 3-5 times more than 316L stainless steel powder
Component Cost Savings
- Reduced waste from optimized geometries
- Lower buy-to-fly ratios compared to machining
- Reduction in lead times and inventory
Unique Capabilities
- Access to new geometries and performance
- Components operate in extreme temperatures
- Enables new product innovation
Despite its higher initial cost, MoSi2 powder offers long-term value for manufacturing specialized high-temperature components with enhanced performance.
Health and Safety Considerations for MoSi2
As an advanced ceramic material, molybdenum disilicide powder requires proper handling precautions similar to other fine metal powders used in 3D printing.
Powder Hazards
- Small particle size presents an inhalation hazard
- Potential sensitization from repeated exposure
- Always handle powder in well-ventilated areas
Printing Emissions
- Melting can generate irritating fumes and particles
- Use exhaust ventilation on printers
Worker Protection
- Wear protective equipment – respirators, gloves, eye protection
- Minimize skin contact with powder
- Adhere to recommended exposure limits
Environmental Release
- Prevent powder spills and containment losses
- Follow disposal regulations
Research Progress on MoSi2 Printing
Active research is advancing MoSi2 additive manufacturing technology on multiple fronts from novel powder production methods to inline monitoring processes.
Novel Powder Synthesis
- Ultrasonic-assisted synthesis allows control of MoSi2 powder morphology and size distribution
- Combustion synthesis from molybdenum and silicon nanopowder precursors yields ultrafine <50 nm powders
- Plasma spheroidization of irregular powders improves powder flowability for printing
- Selective laser melting can directly synthesize MoSi2 powder from molybdenum and silicon
Defect Control
- Inline monitoring using high-speed imaging detects defects as they form
- Modeling of thermal stresses and distortion minimizes cracking
- Grain structure manipulation using seeded nuclei controls anisotropy
- Optimized scan strategies precisely control melt pool dimensions
In Situ Alloying
- Reactive printing from molybdenum powder infiltration with silicon melts
- Additional alloying elements like tungsten or rhenium introduced to powder bed
- Graded compositions and functionally graded parts printed by controlling melt pools
Surface Modification
- Laser cladding of metallic coatings like nickel aluminide for oxidation protection
- Powder bed infiltration with copper improves thermal and electrical conductivity
- Nanoparticle seeding of powder layers modifies grain growth and properties
Applications Under Development
Cutting-edge applications of 3D printed molybdenum disilicide are being developed in highly demanding fields including hypersonics, nuclear energy, and metal 3D printing.
Hypersonics
- Lightweight combustion chambers and nozzles for scramjet engines
- Sharp leading edges for reentry vehicles and hypersonic aircraft
- Hot structures for propulsion systems and thermal protection
Nuclear Energy
- Fuel cladding with enhanced accident tolerance
- Complex geometries for gas-cooled reactor components
- Radioactive waste storage and management systems
Additive Manufacturing
- Lattice structures with negative coefficient of thermal expansion
- High temperature susceptors for microwave sintering
- Precision nozzle arrays for powder bed fusion printing heads
The unique properties of 3D printed MoSi2 expand the frontiers of high-temperature material technology and enable next-generation component designs.
Future Outlook
Molybdenum disilicide possesses exceptional characteristics that make it poised to become a highly valued powder material for printing specialised metal components.
- Adoption will accelerate for hypersonics, space, and nuclear applications
- Alloy development will strengthen mechanical properties and fracture toughness
- Costs will decline as powder manufacturing scales up
- Increased competition will improve quality and expand material offerings
- Design tools will optimize geometries for thermal and structural performance
- Hybrid printing with graded compositions will produce enhanced functionality
- Standards will be developed to qualify aerospace and nuclear parts
- High-volume production will be enabled by multiple large-format printers
By leveraging the benefits of both MoSi2 and 3D printing, manufacturers can push the performance limits and design envelopes for the most challenging operating environments.
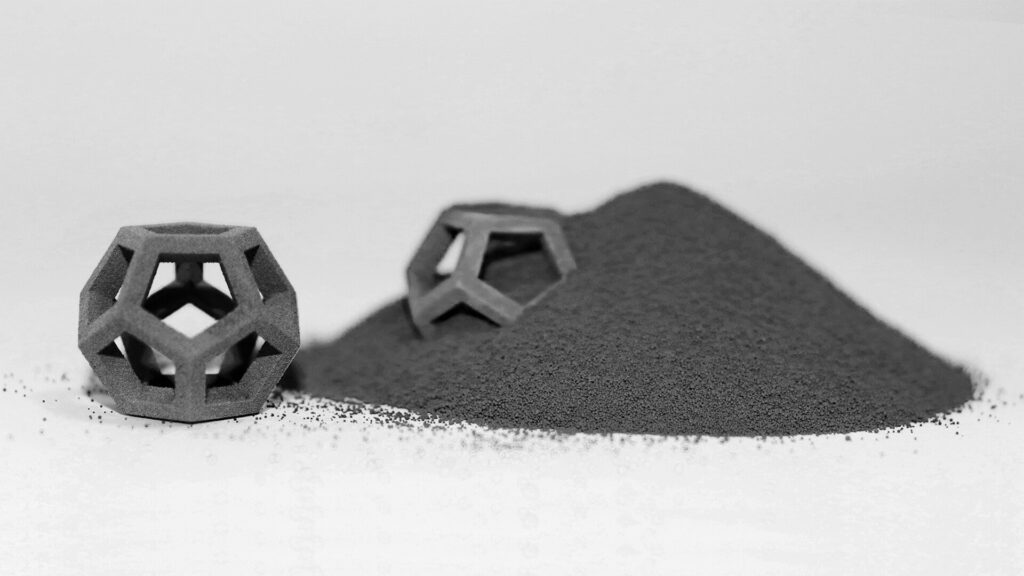
Conclusion
Molybdenum disilicide possesses a unique combination of properties including high strength, creep resistance, oxidation resistance, and thermal conductivity up to extremely high temperatures exceeding 1500°C. These attributes, combined with new capabilities enabled by 3D printing complex geometries from MoSi2 powder, are opening up exciting new applications across aerospace, energy, automotive, medical, and industrial fields.
However, technical challenges remain in producing high purity, spherically-shaped powders optimized for additive manufacturing. Refining print parameters to achieve high density parts and developing post-processing to enhance properties and performance will be ongoing pursuits. Alloying and nano-engineering will provide further improvements.
But the future outlook for MoSi2 additive manufacturing is very bright. By leveraging the synergies between this exceptional material and the geometric freedom of 3D printing, manufacturers will continue pushing the performance boundaries ever higher. This will result in lighter, stronger, and more capable components able to operate in the most extreme environments.
FAQ
What is molybdenum disilicide (MoSi2)?
Molybdenum disilicide (MoSi2) is an advanced ceramic material composed of molybdenum and silicon. It has a tetragonal crystal structure and a very high melting point of 2030°C. Key properties include high strength, oxidation resistance, thermal conductivity, and thermal shock resistance.
Why is MoSi2 good for 3D printing?
MoSi2 has properties ideal for 3D printing high-temperature components, including a high melting point, excellent oxidation resistance, good strength at high temperatures, low density, and thermal properties that minimize thermal stresses. This enables printed parts to perform in extreme environments.
How is MoSi2 powder made?
MoSi2 powder is commercially produced by reacting molybdenum and silicon at high temperatures exceeding 1400°C. Other methods include reducing MoO3 with silicon or producing MoSi2 coatings on molybdenum particles via vapor phase reactions. The powder is milled and classified to achieve particle sizes suitable for 3D printing.
What 3D printing process is used with MoSi2?
MoSi2 is almost exclusively printed using powder bed fusion techniques like selective laser melting (SLM) and electron beam melting (EBM). These methods involve selectively melting layers of powder using a focused heat source in an inert atmosphere.
Does MoSi2 require post-processing after 3D printing?
Yes, as-printed MoSi2 parts often undergo post-processing like hot isostatic pressing (HIP) or heat treatment to increase density, relieve stresses, and improve material properties. Additional surface finishing or coatings can also be applied.
What are the main applications for 3D printed MoSi2?
Key applications taking advantage of MoSi2’s high temperature capabilities include aerospace components like hypersonic propulsion and reentry vehicle structures, nuclearreactor parts, automotive sensors and turbochargers, metal 3D printing components, and industrial tooling.
What are the main challenges with printing MoSi2?
Critical challenges include producing high purity powder optimized for additive manufacturing, minimizing porosity and cracking in printed parts, improving fracture toughness, and reducing costs. Alloy development is also relatively immature compared to traditional high temp alloys.
Is MoSi2 safe to print with?
Like any fine metal powder, certain precautions are necessary when handling MoSi2 powder to minimize dust generation. Printing should be done with adequate ventilation and inert atmospheres. Printer operators should wear personal protective equipment and follow good work practices.
know more 3D printing processes
Frequently Asked Questions (FAQ)
1) What powder specifications are critical for Molybdenum Disilicide Powder in PBF?
- Tight PSD (commonly 10–45 μm), high sphericity for flow, low oxygen/carbon (target O < 0.3–0.8 wt% depending on process), and >99.5% purity. Verify via ISO/ASTM 52907, ICP‑OES/MS, LECO (O/N/H/C).
2) Can MoSi2 be processed on standard laser PBF systems?
- Yes, but success hinges on elevated preheat (often 300–800°C), low oxygen (<50 ppm), tailored scan strategies to mitigate cracking, and powder handling practices similar to reactive alloys.
3) How does Molybdenum Disilicide Powder compare to Ni superalloys for high temperature?
- MoSi2 offers higher oxidation resistance at 1200–1500°C and lower density, but lower fracture toughness at room temperature. It excels for hot structures and heating elements; superalloys lead in damage tolerance.
4) What post‑processing most improves printed MoSi2?
- HIP (e.g., 1200–1400°C, 100–200 MPa) to close porosity, stress‑relief/heat treatment for microcrack healing, and surface finishing (grinding/electropolish). Select coatings (aluminide/silicide) further enhance oxidation resistance.
5) Is powder reuse feasible with MoSi2?
- Limited but possible. Use inert closed‑loop handling, sieving, and blend rules; monitor oxygen rise and PSD shift. Many workflows cap at 3–6 cycles before blending with virgin powder to control Si loss/oxide buildup.
2025 Industry Trends: Molybdenum Disilicide Powder
- Wider availability: More suppliers offer gas‑atomized and plasma‑spheroidized MoSi2 with improved sphericity and lower oxide films.
- Preheat‑centric strategies: Elevated bed/platform preheat and beam shaping reduce microcracking and improve density for thin‑wall features.
- Digital material passports: Lot‑level tracking of PSD, O/N/H/C, reuse count, and tap density becoming standard for aerospace/energy qualification.
- Sustainability: Argon recovery on atomizers and powder circularity programs cut gas use 20–35% and reduce scrap.
- Application pull: Hypersonic leading edges, hot structures, and high‑temp sensors drive demand for MoSi2 and MoSi2‑based composites.
2025 KPI Snapshot for MoSi2 in Powder Bed Fusion (indicative ranges)
Metric | 2023 Typical | 2025 Typical | Notes/Sources |
---|---|---|---|
Achievable relative density (as‑built) | 96–98% | 97–99% | HIP commonly ≥99.5% |
As‑built Ra (μm) | 18–30 | 15–25 | Post‑finish reduces further |
Preheat setpoint (°C) | 300–700 | 400–900 | Reduces cracking/warp |
Oxygen (wt%) after 3 reuse cycles | +0.2–0.4 | +0.1–0.3 | Better inert handling |
Build scrap rate (complex lattices) | 10–18% | 6–12% | Scan/path optimization |
References: ISO/ASTM 52907; ASTM E1019 (O/N/H); supplier technical notes; GE Additive/Arcam and LPBF OEM application briefs; NIST AM‑Bench insights
Latest Research Cases
Case Study 1: Preheat‑Driven Crack Mitigation in LPBF MoSi2 Thin Walls (2025)
Background: An aerospace R&D team experienced edge cracking in 0.5–1.0 mm walls for a hypersonic hot‑structure demonstrator.
Solution: Increased platform preheat from 450°C to 700°C, narrowed hatch spacing, applied rotated stripe strategy, and implemented inert O2 < 30 ppm; followed by HIP at 1300°C/150 MPa.
Results: Edge crack incidence −60%; density +1.2% absolute; room‑temperature flexural strength +15%; dimensional bow reduced from 350 μm to 140 μm over 80 mm span.
Case Study 2: Plasma‑Spheroidized MoSi2 Powder for Improved Flowability (2024)
Background: A powder producer sought to reduce recoater streaking and lot‑to‑lot variability.
Solution: Applied plasma spheroidization to water‑reduced MoSi2, targeting sphericity >0.93; introduced inline optical morphology and automated Hall flow QC.
Results: Hall flow improved by 1.6 s/50 g; apparent density +0.25 g/cm³; LPBF layer defects −35%; customer yield +9% across three geometries.
Expert Opinions
- Prof. Christopher Schuh, Head of Materials Science and Engineering, Northwestern University
Key viewpoint: “For intermetallic ceramics like MoSi2, controlling defect populations—porosity and microcracks—via preheat and post‑densification is the linchpin for reproducible performance.” - Dr. John Slotwinski, Materials Research Engineer, NIST
Key viewpoint: “Digital powder passports capturing PSD, O/N/H/C, and reuse history are essential to qualifying Molybdenum Disilicide Powder across sites and machines.” https://www.nist.gov/ - Dr. Anushree Chatterjee, Director, ASTM International AM Center of Excellence
Key viewpoint: “Expect rapid maturation of test methods and specifications for MoSi2 AM, mirroring what we’ve seen in titanium and nickel systems.” https://amcoe.astm.org/
Practical Tools/Resources
- ISO/ASTM 52907: Powder feedstock characterization for AM
https://www.iso.org/standard/78974.html - ASTM E1019 (O/N/H analysis) and related chemical analysis standards
https://www.astm.org/ - NIST AM‑Bench: Datasets and validation resources for AM processes
https://www.nist.gov/ambench - GE Additive and LPBF OEM application notes on high‑temperature ceramics/intermetallics
https://www.ge.com/additive/ - Materials Project: Crystal and thermodynamic data for MoSi2
https://materialsproject.org/ - OSHA/NIOSH resources on respirable dust and metal powder handling best practices
https://www.osha.gov/ and https://www.cdc.gov/niosh/
Last updated: 2025-08-27
Changelog: Added five MoSi2‑focused FAQs, 2025 KPI/trend table, two recent case studies on preheat and powder spheroidization, expert viewpoints, and vetted standards/resources to support qualification of Molybdenum Disilicide Powder in AM.
Next review date & triggers: 2026-03-31 or earlier if OEMs publish MoSi2 parameter sets, new ASTM/ISO methods for intermetallic powders are released, or major datasets on MoSi2 reuse/oxidation control become available.