Introduction
Metal powders are finely divided metal particles that are used in a variety of manufacturing processes. Metal powders can be made from various metals like iron, aluminum, copper, nickel, and more. They have widespread applications across many industries including automotive, aerospace, electronics, chemical, pharmaceutical, and others. This comprehensive guide will walk you through the different methods used for producing metal powders along with their principles and applications.
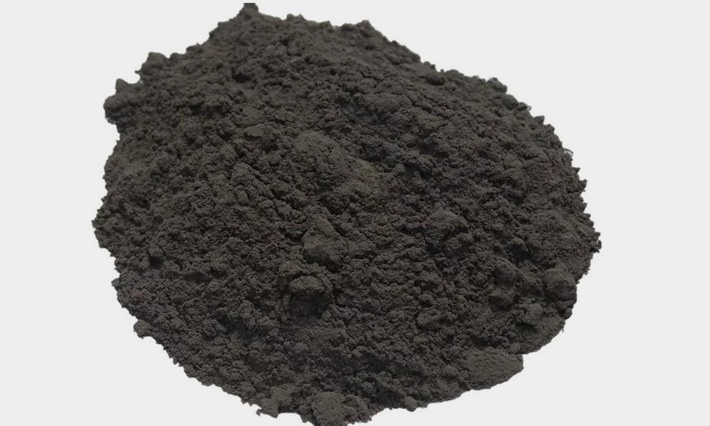
Methods for Producing Metal Powders
There are several techniques used for producing metal powders which can be classified into mechanical, physical, and chemical methods. Each method has its own principles, equipment requirements, and results in powders with different characteristics. The common methods used for metal powder production include:
Mechanical Methods
Milling
Milling involves the mechanical breaking down of metal into a powder form. The starting material is usually in the form of coarse particles or scraps which are milled using ball mills, hammer mills, or jet mills. In ball milling, the particles are broken down by grinding balls tumbling inside the mill. Hammer mills use hammers or blades to crush the metal. Jet mills micronize particles by colliding them at high velocities. Milling produces powders with irregular shapes and wide particle size distribution. It is simple and cost-effective but doesn’t allow precise control over powder characteristics.
Atomization
Atomization is a metal powder production method that involves forcing molten metal through a small opening in a nozzle or orifice. The metal emerges as a spray of fine droplets which solidify into powder particles. Based on the method of disintegration, atomization can be further classified into gas, water, plasma, centrifugal, and ultrasonic atomization. Gas and water atomization are the most common types. This method produces spherical powders with precise particle sizes. However, it requires specialized equipment and high energy input.
Electrodeposition
Also known as electroplating, electrodeposition produces metal powder by electrolytically depositing metal ions onto a cathode from an electrolytic solution. The deposited layer is removed and ground into a powder. This method allows control over particle size and shape. But the powders have low apparent density and production rates are slow. It is used for producing powders from metals like copper, iron, cobalt, etc.
Physical Methods
Evaporation
Evaporation techniques like vacuum evaporation produce metal vapors that are then condensed into fine metal powders. The metal is heated until it evaporates in a vacuum chamber and then condenses on cold surfaces to form a powder. This method can produce spherical powders with controlled particle size distribution. However, it requires specialized equipment and is unsuitable for metals with high melting points.
Sputtering
Sputtering uses plasma energy to eject atoms from a solid metal target. The ejected atoms are deposited as a thin film and scraped off to form powders. It allows control over particle size, morphology, and composition. But the production rate is very slow and unsuitable for large-scale manufacturing. This method is primarily used for producing ultrafine and nanopowders.
Chemical Methods
Reduction
Reduction involves converting metal salts or oxides to powdered metal using reducing agents like hydrogen, carbon, carbon monoxide, etc. For example, iron oxide can be reduced by hydrogen to produce iron powder. This versatile method can produce powders from various metals. The powders have high purity but irregular shapes and wide particle size distribution.
Electrolysis
Electrolysis uses electrolytic cells to produce metal powders from solutions containing their ions. The powder is deposited at the cathode while the anode dissolves to replenish metal ions in the solution. This method allows control over particle characteristics and is used for producing aluminum, chromium, titanium, magnesium powders. However, it is an expensive process with slow production rates.
Self-propagating high-temperature synthesis (SHS)
SHS involves an exothermic reaction between metal oxides and reducing agents to produce metal powders. The heat generated by the reaction sustains and propagates the chemical conversion process. Iron oxide and aluminum are commonly used raw materials in SHS reactions. It is a simple, cost-effective method but requires specialized reaction equipment and process control.
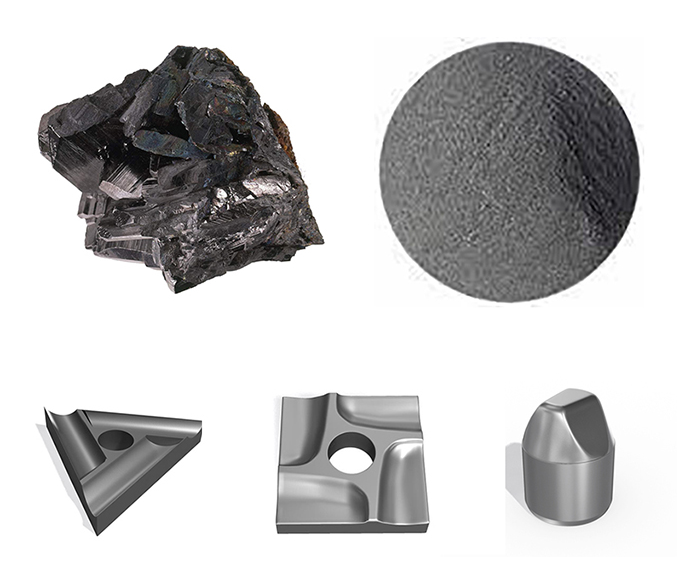
Commonly Used Metals for Making Powders
Some of the commonly used base metals for making powders include:
- Iron: Iron powders are one of the most widely used ferrous powders. They are produced from reduced iron ore and find applications in powder metallurgy, manufacturing of auto parts, magnets, cutting tools, and magnetic inks.
- Aluminum: Aluminum powders have high thermal/electrical conductivity and are used in thermite reactions, additive manufacturing, automotive parts, paints, pyrotechnics, etc. They are produced by atomization of molten aluminum.
- Copper: Copper powders have excellent thermal and electrical conductivity. They are manufactured by electrolysis, atomization, or reduction methods and used for making electronic components, winding wires, friction materials, welding rods, etc.
- Nickel: Nickel powders have corrosion resistance, toughness, and ferromagnetic properties. They are produced by carbonyl decomposition, electrolysis, or reduction and used for making alloy steels, batteries, catalysts, conductive paints, etc.
- Tin: Tin powders find use as plating materials, in solders, bearings, and chemical manufacturing. They are produced by atomization or electrodeposition from tin solutions.
- Tungsten: Tungsten powders have high density, strength, and melting point. They are manufactured by hydrogen reduction and used for making tungsten wires, heating elements, and wear-resistant coatings.
- Silver: Silver powders have high electrical and thermal conductivity. They are produced by electrolysis and used in solders, brazing alloys, conductive coatings, and photovoltaic contacts.
- Gold: Gold powders are chemically stable and electrically conductive. They are produced using electrolytic or evaporation methods and used for electronics manufacturing and decorative coatings.
Applications of Metal Powders
Metal powders have a diverse range of applications across many industries:
- Manufacturing: Powder metallurgy uses metal powders to manufacture finished or semi-finished components. The powders are compacted and then sintered to produce precise parts with complex shapes. Common products include gears, bushings, bearings, magnets, cutting tools, auto parts, etc.
- Additive manufacturing: Selective laser sintering, direct metal laser sintering, and binder jetting use metal powders to 3D print metal components layer by layer. Aerospace, medical, and automotive industries use these technologies.
- Electronics: Copper and silver powders are used to manufacture printed circuits, multilayer ceramic capacitors, and conductive adhesives. Ferrite powders produce inductors and transformers cores.
- Chemical industry: Metal powders act as catalysts and reagents for manufacturing chemicals, pharmaceuticals, petroleum products, pigments, and battery materials.
- Coatings: Aluminum flakes produce metallic coatings in paints. Copper and zinc powders make anti-corrosive coatings. Metal powders also produce conductive coatings and electromagnetic shielding.
- Welding: Aluminum and magnesium powders are used to provide exothermic reactions in thermite welding. Iron, copper, and nickel powders produce welding filler materials.
- Pyrotechnics: Aluminum, magnesium, and iron powders are key components of fireworks, sparklers, flares, and thermites due to their exothermic oxidation reactions.
- Others: Metal powders find other niche applications in making diamond tools, friction materials, brazing alloys, conductive plastic, magnetic inks, etc.
Properties of Metal Powders
The properties of metal powders are influenced by the production method as well as the composition, particle size, shape, porosity, and microstructure. Important powder properties include:
- Particle size: Measured in micrometers (microns), size influences density, reactivity, and sintering behavior. Ultrafine powders have sizes below 10 microns.
- Particle shape: Shape affects powder flow and packing density. Granular, spherical, flake, and dendritic shapes are common.
- Particle size distribution: A narrow distribution allows uniform packing and processing whereas a wide distribution may segregate during handling.
- Apparent density: Ratio of mass to powder volume. Affects compressibility and final part density. Values range from 25%-80% theoretical density.
- Tap density: Maximum density achieved after mechanical tapping. Indicates powder packing efficiency.
- Flow rate: Important for handling and processing. Influenced by factors like particle size, shape, surface oxide, and moisture.
- Compressibility: Ability of powder to deform under pressure into a compact. Depends on ductility, work hardening, and adsorbed gases.
- Sintering activity: Ability of powder particles to bond together during heating. Influenced by composition, particle size, oxide content, and defects.
- Purity: Presence of oxygen, nitrogen, and carbon can adversely affect powder properties. High purity is required for critical applications.
Safety Measures for Handling Metal Powders
Handling metal powders comes with potential health and safety hazards. Some key measures include:
- Use protective equipment – gloves, eye protection, face masks, and full-body suits while handling powders to prevent inhalation and skin contact.
- Avoid ignition sources – powders may combust when exposed to heat, sparks, or flames. Follow proper grounding procedures.
- Prevent dust explosions – powders form explosive dust-air mixtures. Use dust extraction systems and avoid powder accumulations.
- Store inertly – powders are often stored in sealed containers under inert gases like argon or nitrogen to prevent oxidation.
- Ensure proper ventilation – use fume hoods or local exhaust ventilation to prevent exposure to metal fumes and powder dust.
- Avoid spills – clean spills immediately using vacuum systems, not brushes which disperse dust.
- Follow safe disposal – dispose according to local environmental regulations and not via drains or landfills.
- Provide training – train workers on powder hazards, proper handling procedures, and emergency measures.
- Conduct monitoring – monitor dust levels and worker exposure to ensure they are within permissible exposure limits.
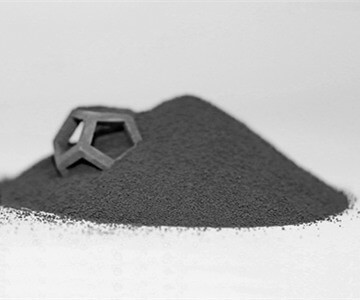
FAQs
What are the main methods for producing metal powders?
The main methods are:
- Mechanical milling
- Atomization
- Chemical reduction
- Electrolysis
- Evaporation techniques
What are metal powders used for?
Metal powders are used to manufacture finished parts through powder metallurgy, produce additively manufactured components, make electronic devices, apply conductive/resistant coatings, manufacture chemicals and catalysts, and create pyrotechnics.
How are metal powder particle sizes measured?
Particle sizes are measured in micrometers (microns) using microscopy, laser diffraction, sedimentation, sieving, and dynamic light scattering techniques. Ultrafine powders have sizes below 10 microns.
What precautions should be taken when handling metal powders?
Precautions include using protective gear, avoiding ignition sources, preventing dust explosions, inert storage, proper ventilation, safe disposal, worker training, and exposure monitoring.
What properties of metal powders affect their performance?
Important properties are particle size, shape, size distribution, density, flow rate, compressibility, sintering ability, purity, and composition. These influence processing, handling, and final product quality.
How are metal powders safely stored?
Metal powders are often stored in sealed containers under inert gases like argon or nitrogen to prevent oxidation reactions. This maintains powder purity and prevents changes in powder characteristics.
What is powder metallurgy?
Powder metallurgy is a manufacturing process that uses metal powders to produce finished or semi-finished components. It involves compacting the powders followed by sintering to produce precise metal parts with complex shapes.
Which metals are commonly used to produce powders?
Iron, aluminum, copper, nickel, tin, tungsten, silver, and gold are commonly used. The metal is chosen based on required material properties and application.
What is atomization process for metal powder production?
In atomization, molten metal is forced through a nozzle, breaking up into fine droplets that solidify into powder particles. It allows control over particle size and shape and is used to produce spherical powders.
What are the hazards associated with metal powders?
Metal powders can combust when exposed to heat or sparks. They form explosive dust-air mixtures. Metal fumes and fine powders are also toxic upon inhalation. Proper protective gear and handling procedures are required.