Introduction
3D printing, also known as additive manufacturing, has revolutionized manufacturing and design. It provides unprecedented capabilities to quickly create complex geometries with little waste. However, many 3D printed parts suffer from poor mechanical properties due to porosity and other defects inherent in the printing process.
Hot isostatic pressing (HIP) is a manufacturing process that subjects 3D printed parts to both high temperature and isostatic pressure to improve their density, performance, and reliability. The combination of heat and pressure enables the closure of internal voids and fuses together internal defects and particles within metals and ceramics.
HIP applied after 3D printing thus enhances the properties of printed parts, enabling new applications and improved performance. The synergistic combination of 3D printing and HIP pushes the boundaries of design complexity and high performance.
What is hot isostatic pressing?
Hot isostatic pressing is an advanced manufacturing process used to reduce porosity and increase density in metals, ceramics, polymers, and composite materials. In the HIP process, the component is subjected to both elevated temperature and isostatic pressure in a high pressure containment vessel.
Isostatic means uniform pressure is applied from all directions simultaneously. This is achieved by surrounding the component with an inert gas, liquid, or glass beads which transmit pressure evenly to the surface of the part.
The simultaneous application of heat and pressure enables the material’s internal pores and voids to close up, densifying the part. Densification depends on the material’s viscoplastic properties at the selected temperature and how easily the pores can deform and eliminate gaps between particles.
The typical HIP process involves:
- Placing parts in a pressure containment vessel
- Evacuating air and backfilling with an inert gas such as argon
- Heating up to process temperature, often between 1900-2200°F (1040-1200°C)
- Applying isostatic pressure up to 30,000 PSI (200 MPa)
- Cooling under pressure before release and removal
The HIP process diffuses material to close internal pores, minimizes or eliminates internal voids, and metallurgically bonds internal defects. This improves the quality, performance and reliability of manufactured parts across industries like aerospace, defense, automotive and energy.
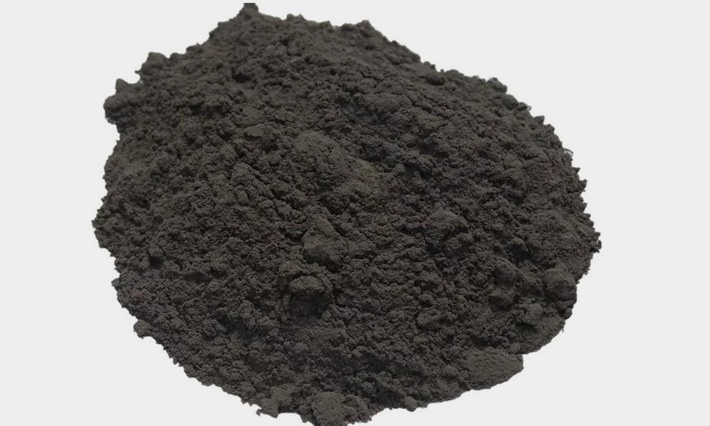
How does hot isostatic pressing enhance 3D printed parts?
Most metal 3D printing techniques like selective laser melting (SLM) and electron beam melting (EBM) produce parts with some level of porosity. This is due to the nature of building up parts layer-by-layer from metal powder.
Defects like micro-cracks and micropores up to 100 μm are formed between powder particles and adjacent solidified layers. Parts can have up to 5% porosity depending on the material and printing parameters used.
This intrinsic porosity causes several problems:
- Mechanical properties like fatigue strength and fracture toughness are severely reduced
- Leak paths are created causing parts to fail leak tests
- Functional performance is impaired especially for fluid flow and pressurized systems
- Corrosion resistance and chemical compatibility suffers due to penetration along pores
- Dimensional accuracy is compromised as pores can continue growing during subsequent heat treatment
- Surface finish quality degrades as pores near the surface act as stress concentrators
Hot isostatic pressing eliminates these pores to significantly enhance the material and performance properties of 3D printed metals. HIP achieves:
- Increased density – closing internal voids and gaps metallurgically bonds the material to reach 100% density
- Improved mechanical properties – eliminates stress concentrators caused by defects to improve strength, ductility and fracture resistance
- Leak-tight structures – closes microscopic paths for fluids to leak through the material
- Better surface finish – crushes pores near the surface thereby improving surface smoothness
- Dimensional stability – prevents continued growth of pores during future thermal processes
- Higher reliability – removes defects to improve quality and consistency of printed parts
Thus HIP overcomes key limitations of metal 3D printing to enable high performance end-use parts production.
HIP process for 3D printed parts
The typical HIP process for additively manufactured parts involves:
HIP Can and Sealing
The 3D printed parts are placed inside a HIP can – usually made of glass, steel or aluminum – along with ceramic or glass bead filler. The HIP can supports the part against pressure and transmits pressure evenly against all surfaces.
The can is then hermetically sealed by welding or crimping the lid. This retains the inert gas later used to apply pressure. The can also prevents contamination during the HIP process.
Degassing
The HIP can assembly is placed in the high pressure containment vessel. This vessel is sealed and pumped down to create a vacuum. Vacuum removes air and moisture that can cause oxidation during HIP.
The vessel is then backfilled with an inert gas like argon to surround the parts. The inert atmosphere prevents chemical reactions during heating.
Heating and Pressurization
The vessel is heated up at a controlled rate up to 1900-2200°F (1040-1200°C) – the typical HIP temperature for metals. Heating activates diffusion and creep mechanisms in the material that help close pores.
Once at temperature, high pressure up to 15,000-30,000 PSI (100-200 MPa) is applied isostatically using the inert gas. This pressure collapses internal voids and pushes the material to fill gaps.
Cooling and Release
After a predetermined time at temperature and pressure (typically 3-6 hours), the vessel is cooled at a controlled rate. Pressure is maintained during cooling to enable full densification.
Once cooled, the pressure is released gradually. The HIP can is removed and opened to recover the treated parts. Additional machining can recover the original dimensions.
Benefits of HIP for 3D printed parts
Key benefits of using HIP to post-process 3D printed metals:
Increased Density
HIP achieves 100% density in printed metals by collapsing voids and diffusion bonding layers. This improves integrity for load-bearing structures and leak-tight systems.
Higher Strength
Eliminating defects like micro-cracks and pores removes stress concentrations. This increases strength and ductility close to conventionally processed materials.
Better Surface Finish
Micro-voids near the surface are crushed to create a smoother surface with improved finish and appearance. This also enhances fatigue resistance.
Dimensional Stability
Pores are collapsed rather than allowed to grow during subsequent heat treatment. This improves dimensional accuracy and geometric tolerances.
Larger Parts
HIP enables 3D printing and consolidation of larger parts not possible with other techniques. Parts up to 50 inches diameter can be produced.
Design Freedom
HIP maintains the design freedom of 3D printing for complex geometry parts. It broadens the application of printed metals to critical structural and fluid handling uses.
Shorter Lead Times
Combining 3D printing and HIP shortens manufacturing timelines compared to traditional multi-step processing. It enables rapid production of complex, high performance parts.
Industries using HIP for 3D printed parts
HIP is leveraged across major industries to enhance 3D printed metal parts for robust end-use applications:
Aerospace
HIP improves density, strength and surface finish of printed aerospace components like turbine blades, rocket engines nozzles, and satellite brackets. This enables lightweight, complex geometries for extreme mechanical loads and temperature resistance.
Medical
Medical implants like hip joints and bone scaffolds are HIPed after 3D printing to completely eliminate internal voids. This improves biocompatibility and fatigue resistance when implanted within the body.
Automotive
HIP is applied to 3D printed automotive parts like turbochargers and fluid handling cylinders. This provides 100% leak-tight structures to withstand cyclic pressures and loading.
Defense
The defense sector uses HIP to produce printed parts like missile casings and conformal cooling channels for molds. HIP enables complex geometries capable of ballistic impact resistance.
Energy
For nuclear, oil drilling, and other energy applications, HIP ensures complete densification of printed components for fracture resistance under extreme pressures and temperatures.
As 3D printing expands across industries, HIP will grow in tandem to deliver enhanced performance, reliability and consistency.
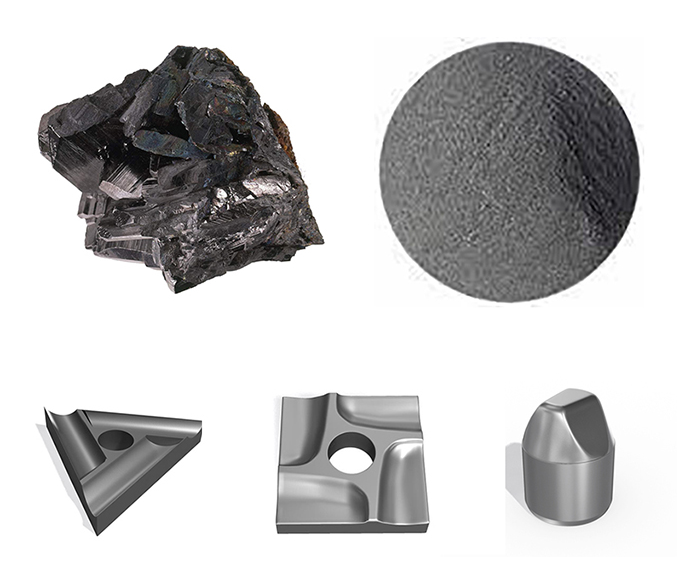
Materials for HIP of 3D printed parts
HIP has been demonstrated for a wide range of metals and alloys used in commercial 3D printing:
- Titanium and titanium alloys like Ti-6Al-4V are highly popular for aerospace applications. HIP achieves 100% density and improves fatigue performance.
- Aluminum alloys like AlSi10Mg can be printed and HIPed for a lighter alternative to titanium with similarly enhanced properties.
- Nickel-based superalloys such as Inconel 718 and 625 are widely used in jet engines and gas turbines. HIP removes defects while retaining strength at high temperatures.
- Stainless steels including 316L and 17-4PH are commonly used to print strong, corrosion resistant parts across industries. HIP eliminates porosity for improved structural integrity.
- Tool steels like H13 and D2 provide excellent hardness after HIP to print durable tooling like molds with conformal cooling channels.
- Refractory metals including tungsten, tantalum, and molybdenum are inherently porous from AM but can be fully densified by HIP.
- Cobalt-chrome alloys provide excellent wear resistance for orthopedic implants when HIPed after 3D printing.
Both standard and custom alloys are continually being qualified for additive manufacturing combined with HIP to expand capabilities.
HIP process parameters
The main HIP process parameters that can be optimized to suit different 3D printed parts are:
- Temperature – Typical range of 1850-2200°F. Higher temperatures increase diffusion rates to close pores faster. But excessive temperatures can cause microstructural changes.
- Pressure – Standard pressures of 15,000-30,000 PSI used. Higher pressures collapse pores at lower temperatures. But too high pressures can damage surface finish.
- Time – Standard hold times of 3-6 hours at peak temperature and pressure. Longer times enable more densification but increase costs.
- Heating/cooling rates – Faster heating increases productivity but risks distortions. Slower heating ~50-100°F/min and cooling avoid thermal strains.
- Dwell time – Holding at peak temperature allows sufficient diffusion bonding. Shorter times risk incomplete densification.
HIP process parameters are optimized to suit the specific 3D printing alloy composition, part geometry, powder size and required material properties.
Challenges of using HIP with 3D printed parts
While HIP provides significant benefits, some limitations and challenges exist:
- Modified dimensions – HIP can cause 2-5% shrinkage. Parts may require re-machining after HIP to recover dimensions.
- Surface finish – HIP can reduce surface roughness from AM but may not achieve the smoothest surface finishes. Additional polishing may be needed.
- Geometric limitations – HIP cans restrict maximum part size. Very complex geometries can be difficult to fill uniformly with HIP beads.
- Cost – HIP adds significant cost over conventional heat treatment. Economic benefits rely on improved performance justifying the investment.
- Process development – Optimal HIP protocols must be developed for each specific alloy composition, powder size and AM process used to ensure full densification without defects.
Further research and process refinements are focused on adapting HIP for greater geometric freedom, surface quality, turnaround times and cost-effectiveness.
The future of HIP and 3D printing
HIP has proven to be an enabling technology to qualify 3D printed metals for high value, critical applications across aerospace, medical, automotive, and defense sectors.
As 3D printing expands from prototyping to full-scale production, HIP will be crucial for industries reliant on parts with high structural integrity and performance. Increased adoption of both technologies is expected with improvements in automation, turnaround times and costs.
New developments in HIP to support AM include:
- Quicker cycling times – Novel heating methods and faster cooling aim to reduce typical HIP cycles from over 6 hours to under 3 hours. This improves throughput.
- Larger build volumes – Containment vessels are increasing to accommodate larger printed parts up to 50 inches diameter. This expands capabilities.
- Hybrid HIP – Special HIP cycles with controlled cooling rates or in-situ heat treatments are being developed to further optimize properties.
- Quality assurance – Inline monitoring and inspection tools for HIP will help characterize densification and validate part quality.
- Modeling tools – Simulation software is enabling better predictions of distortion and property improvements from HIP.
The synergistic advancement of 3D printing and HIP will open new avenues for designing and efficiently manufacturing complex, high performance components across critical industries.
Key Takeaways on HIP and 3D Printing
- Hot isostatic pressing (HIP) applies high temperature and uniform pressure to collapse internal voids in 3D printed metals, improving density, performance and reliability.
- HIP eliminates porosity defects such as micro-cracks inherent in powder bed fusion 3D printing processes.
- Key benefits of HIP for 3D printing include increased density, higher strength, better surface finish, dimensional stability and improved designs.
- HIP enables lighter weight designs, complex geometries, and innovative conformal features for aerospace, medical, automotive and defense applications.
- With improvements in automation, speed and cost, HIP will be increasingly adopted to enhance quality and capabilities of metal 3D printing across production environments.
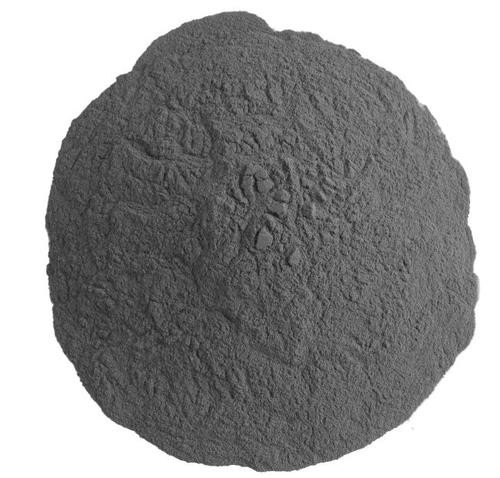
FAQ
What is hot isostatic pressing used for in 3D printing?
Hot isostatic pressing (HIP) is used as a post-processing method for 3D printed metal parts. HIP helps to eliminate porosity defects by applying high temperature and isostatic pressure to collapse voids and densify parts. This improves the density, performance, and reliability of additively manufactured components.
How does HIP enhance the properties of 3D printed metals?
HIP enhances properties of 3D printed metals in several ways:
- Increases density to near 100% by diffusion bonding layers and closing internal gaps
- Eliminates micro-cracks and pores to significantly improve fatigue life and strength
- Provides superior surface finish by crushing near-surface defects
- Offers better dimensional stability by preventing further void growth during heat treatment
- Enables larger and more complex geometries to be printed and consolidated
What types of materials can be HIPed after 3D printing?
Most alloys printed by powder bed fusion methods can be HIPed, including:
- Titanium alloys like Ti-6Al-4V
- Nickel superalloys such as Inconel 718 & 625
- Stainless steels including 316L and 17-4PH
- Aluminum alloys such as AlSi10Mg
- Tool steels like H13 and D2
- Cobalt chrome alloys for medical uses
- Refractory metals such as tungsten and tantalum
Both standard and custom alloys are continually being qualified for additive manufacturing and HIP.
What industries use HIP on 3D printed parts?
Major industries using HIP to post-process 3D printed parts include:
- Aerospace – Turbine blades, rocket nozzles
- Medical – Orthopedic implants like hip joints
- Automotive – Fluid handling parts, turbochargers
- Defense – Missile casings, armor
- Energy – Components for nuclear, oil and gas industries
As 3D printing expands across sectors, HIP adoption will grow to enable high-performance end-use parts production.
How does the HIP process work for 3D printed parts?
Key steps in the typical HIP process for 3D printed parts include:
- Parts are enclosed in a HIP can along with filler media
- Can is sealed and placed in the HIP vessel
- Vessel is evacuated, backfilled with inert gas, then heated up to 1900-2200°F
- Isostatic pressure up to 30,000 PSI is applied
- Dwell time at peak temperature and pressure densifies parts
- Vessel is cooled under pressure before releasing
HIP parameters are tailored for the specific part alloy, geometry and properties required.
What are some challenges associated with using HIP for 3D printed parts?
Some key challenges include:
- Dimensional changes up to 5% shrinkage requiring re-machining
- Limits on maximum part size based on HIP vessel capacity
- Non-uniform densification for complex geometries
- Long process cycles of 6+ hours
- Costs higher than conventional heat treatment
- Developing optimized protocols for different alloy systems