Electric beam manufacturing refers to a variety of manufacturing processes that utilize concentrated energy sources such as lasers, electron beams, or plasma arcs to selectively melt, fuse, or vaporize materials. By precisely controlling the energy source, these processes allow for extremely accurate and repeatable manufacturing with minimal thermal distortion. Electric beam manufacturing enables the production of complex geometries and micro-scale features not achievable by traditional subtractive manufacturing techniques.
How Do Electric Beam Manufacturing Processes Work?
Electric beam manufacturing relies on the principles of energy density and heat transfer. By focusing energy into an extremely narrow beam, very high energy density can be achieved. When this concentrated energy interacts with the material, only a small volume is melted or vaporized. Heat dissipates quickly from this small interaction volume into the surrounding material which remains cooler. This allows extremely accurate and localized melting, fusing, or vaporization of the material.
There are several common types of electric beam manufacturing:
Laser Beam Manufacturing
- Uses a highly focused laser beam as the energy source
- Laser beams can be focused down to 0.01 mm or below
- Allows very high precision and minimizing of thermal distortion
- Used for welding, cutting, cladding, additive manufacturing, etc.
Electron Beam Manufacturing
- Uses a focused beam of electrons as the energy source
- Electron beams can be focused down to 0.1 mm
- Allows working in a vacuum environment
- Used for welding, additive manufacturing, etc.
Plasma Arc Manufacturing
- Uses a plasma jet as the energy source
- Plasma arcs offer high energy density
- Allows keyhole welding of metals
- Used for high penetration welding and cutting
In all cases, the workpiece and/or the beam source are moved via CNC control to trace out the desired geometry. Computer controls and automation allow the process to be highly repeatable and consistent.
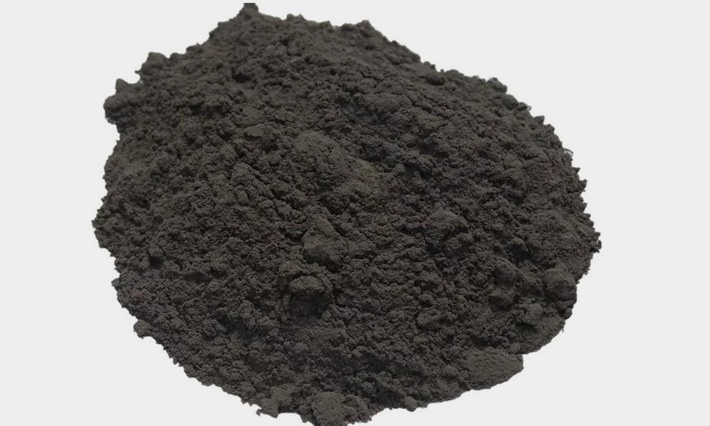
What Are the Benefits of Electric Beam Manufacturing?
Compared to conventional manufacturing methods, electric beam manufacturing offers several advantages:
- Extreme precision – Due to the highly focused energy beams, feature sizes and tolerances down to 0.01 mm are possible. This enables microscale components and electronics.
- Minimal thermal distortion – Only a small volume of material is melted at a time. This allows rapid cooling and minimizes detrimental thermal effects. Parts show less warping and distortion.
- No tooling required – The energy beam essentially acts as a tool, removing the need for physical tooling. This enables rapid prototyping and design iteration.
- Highly repeatable – The CNC-controlled beams allow extremely consistent and repetitive processing suitable for mass production.
- No forces or stresses – Since there is no physical contact, delicate structures can be made without damage. Internal features and geometries are also possible.
- Excellent metallurgical properties – Rapid cooling rates can create fine-grained structures and unique material properties.
- Wide material compatibility – Metals, polymers, composites, and ceramics can be successfully processed with proper parameter selection.
These advantages enable electric beam manufacturing to be used for a wide array of applications not easily produced by other means. The processes continue to improve in accuracy, repeatability, and cost-effectiveness.
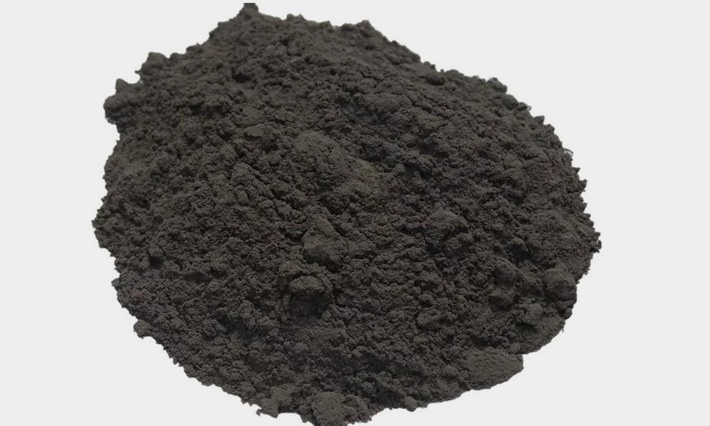
What Materials Can Be Processed?
Many different materials are compatible with electric beam manufacturing:
Metals – All common metals can be processed including steel, aluminum, titanium, nickel alloys, and more. Different alloys and tempers may require adjusted parameters. Fiber lasers offer advantages with highly reflective materials like copper or gold.
Polymers – High-powered lasers can selectively melt a wide range of thermoplastic polymers for welding or additive manufacturing. Some polymers such as PTFE require specialized beam sources.
Composites – Fiber-reinforced polymers can be processed to a limited extent if parameters are controlled to avoid thermal damage to fibers.
Ceramics – Ceramic materials require very specialized high-powered lasers for processing due to their refractory nature and poor thermal conductivity.
Silicon – Lasers can trim, drill, and cut silicon wafers for microelectronics applications. Plasma dicing is also being adopted.
Diamond – Due to its hardness and chemical resistance, diamond can only be machined practically using lasers.
Proper beam parameter selection and control is crucial to achieve sound processing and prevent uncontrolled thermal damage when working with different materials. Process development is an important first step.
What Are the Common Electric Beam Processes?
There are several well-established manufacturing processes that leverage electric beam energy sources:
Laser Cutting
- Laser cutting uses a focused high power laser to melt/vaporize material and induce cutting
- Can cut complex 2D profiles from sheet metal, plate, and pipe with minimal distortion
- Process is very accurate and repeatable for automation
Laser Welding
- Focused laser energy allows precision welding of miniaturized components or thin materials
- Low heat input minimizes distortion which is crucial for delicate parts
- Can weld dissimilar and reactive materials given proper joint design
Laser Drilling/Ablation
- Lasers can drill holes through metals, polymers, and composites with no tool wear
- Percussion and trepanning techniques can create holes with fine diameters and finish
- Multi-pulse processing enables very high aspect ratio holes
Laser Marking
- Laser marking is a non-contact way to mark parts for identification, branding, or traceability
- Creates permanent surface marks without material removal or distortion
- Can mark metals, plastics, ceramics, paper, leather, and many other materials
Laser Cladding
- Laser cladding deposits a coating material onto a part using a focused laser beam
- Achieves metallurgical bonding as the cladding powder melts into the substrate
- Allows wear-resistant or corrosion-resistant coatings to be built up
Laser Shock Peening
- Laser shock peening uses high-power pulses to create shockwaves that impart compressive stresses
- Compressive stresses inhibit fatigue crack initiation and improve part life
- Deeper compressive stresses are created versus conventional shot peening
Laser Additive Manufacturing
- Also known as laser powder bed fusion, direct metal laser sintering, or selective laser melting
- Layer-by-layer 3D printing process using metallic powder and laser melting
- Allows complex geometries and customized parts directly from 3D CAD data
Electron Beam Welding
- Uses a focused electron beam to provide high welding penetration in a vacuum
- Ideal for joining reactive metals like titanium that are prone to atmospheric contamination
- Can weld very thick sections due to full penetration capability
Electron Beam Additive Manufacturing
- Also known as electron beam powder bed fusion or electron beam melting
- Builds up 3D metal parts from metallic powder using an electron beam heat source
- Environmentally controlled process avoids issues with material oxidation
Plasma Arc Welding
- Plasma arc welding uses a constricted plasma jet to concentrate heat energy
- Can fully penetrate thick sections in a single pass unlike traditional welding
- Produces weld seams with minimal distortion and excellent metallurgical properties
Plasma Arc Cutting
- Uses a high temperature plasma jet to melt/oxidize material to induce cutting
- Has high cut speed capability for thick plate and can produce good edge quality
- Plasma stream concentrates heat in tight area for precision cutting
There are many other niche processes such as laser peening, laser glazing, laser annealing, plasma keyhole drilling, etc. that take advantage of beam energy in specialized ways. The list continues to grow with advances in beam generation technology and control capabilities.
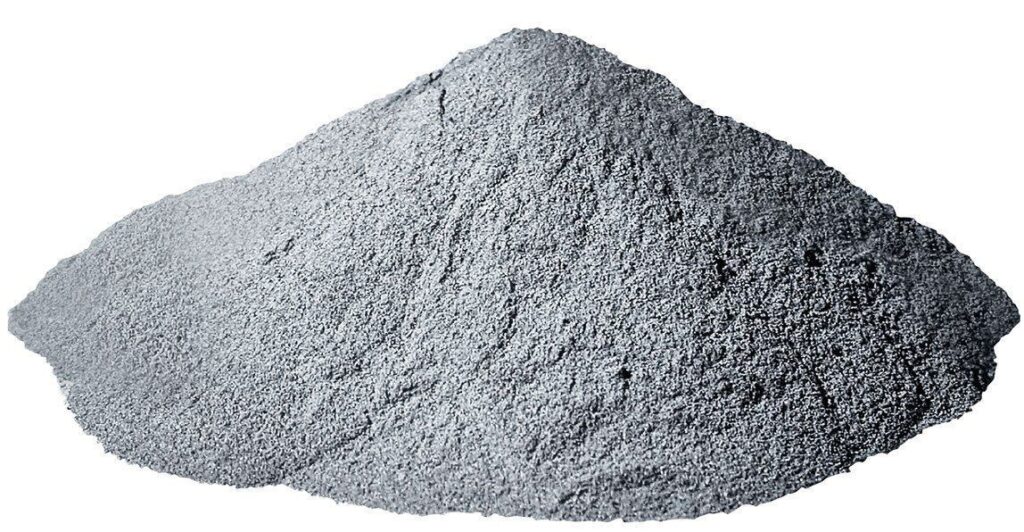
How Does Quality Assurance Work With These Processes?
Consistent quality control and assurance practices are important for any manufacturing process. Some key quality aspects for electric beam processes include:
- Process Monitoring – Many machines have sensors to monitor beam power, position, focus, gas flows, vacuum levels, etc. during processing. Data is logged and analyzed.
- In-Process Inspection – Machine vision systems can optically inspect parts in-process looking for defects and improper processing. This enables quick corrective action.
- Post-Process Inspection – Parts are inspected after production using optical metrology, X-ray radiography, ultrasonic testing, mechanical testing, metallography, etc.
- Parameter Optimization – Design of experiments helps determine ideal parameters to meet requirements. Parameters are validated over multiple builds.
- Maintenance & Calibration – Beam generators and positioning systems require regular maintenance and recalibration to ensure stable operation.
- Operator Training – Comprehensive training for machine operators and process engineers ensures proper operation.
- Traceability – Part identification and production data helps trace final parts back to all process parameters and raw material lots.
- Standards Compliance – Stringent quality management principles per ISO and industry standards are implemented.
- Process Control – Statistical process control using control charts tracks process stability and detects deviations from nominal conditions.
With proper quality infrastructure, electric beam processes offer very consistent and repeatable processing. Tight tolerances, material properties, and performance are readily achievable.
What Safety Precautions Are Required?
Electric beam manufacturing does require some unique safety measures:
- Laser Safety – Precautions must be taken to avoid direct eye exposure or skin burns. Protective eyewear, barriers, skins, alarms, and interlocks are required.
- Electron Beam Hazards – Faradic x-rays are generated requiring shielding. Stray electron beams also require containment.
- Fume Extraction – Many beam processes generate weld fumes, particulates, or hazardous gases requiring localized fume extraction.
- Electrical Hazards – Beam generators involve high voltages warranting proper insulation, separation, and access interlocks.
- Fire Hazards – Flammable vapors, oils, and dusts create a fire risk with beam energy. Proper housekeeping is critical.
- Noise Exposure – Some beam processes like plasma arc cutting produce loud noise necessitating hearing protection.
- Ergonomic Risks – Improper lifting, bending, and repetitive motions can lead to strains or other injuries.
With proper engineering controls, administrative policies, Personal Protective Equipment (PPE), and training, these hazards can be effectively managed for a safe workplace. Careful design of facilities and equipment is also needed to isolate beam hazards.
How Are Parts Designed and Simulated For Beam Processes?
Several software tools aid in the design and simulation of parts for electric beam manufacturing:
- CAD Software – CAD programs allow detailed 3D modeling of component geometries optimized for additive manufacturing. Design constraints can be incorporated.
- Topology Optimization – Algorithms can optimize the layout of material to improve performance under loading. This enables significant lightweighting.
- Simulation Software – Finite element analysis and computational fluid dynamics simulate stresses, temperatures, distortion effects, thermal-structural interactions, residual stresses, etc. This enables design validation.
- Process Modeling – Specialized software can simulate the energy beam interaction with powder beds to model melt pools, temperature gradients, vaporization, etc. This ensures process feasibility.
- Build Planning – Build processors slice CAD models and generate optimal toolpaths for additive systems accounting for supports, heat buildup, residual stresses, and more.
- Inspection Planning – Inspection requirements can be defined in CAD models. The models then drive robotic inspection routines.
- Machine Data – Real machine data is incorporated into simulations for greater accuracy. Closed-loop validation ensures designs are manufacturable.
The increasing power of simulations coupled with real build validation enables “designing for manufacturability”. This reduces development time and costs while ensuring high quality.
How Are Systems Automated and Controlled?
Modern electric beam processes leverage extensive automation and control:
- CNC Control – Multi-axis CNC systems position the beam and/or workpiece with high precision through complex trajectories.
- Motion Control – Precision electromagnetic bearings, linear motors, and optical encoding provide smooth and accurate motion.
- High Speed Processing – Galvanometers, polygonal mirrors, and other techniques rapidly scan and distribute energy for high processing rates.
- Seam Tracking – Through-the-lens and camera-based monitoring enables adaptive control to follow weld seams or correct processing in real-time.
- Advanced Beam Manipulation – Dynamic focusing, beam splitting/shaping, and specialized optics precisely control beam energy distribution.
- Machine Vision – In-process optical monitoring of melt pool geometry, thermal emissions, and geometry ensures quality. Closed-loop control is enabled.
- Precision Powder Handling – Carefully controlled powder deposition, smoothing, and recoating enables high precision additive manufacturing.
- Inert Atmosphere – Vacuum systems or inert shrouding gases prevent material oxidation.
- In-Process Metrology – In-situ monitoring of temperatures, emissions, and dimensional metrology data provides live process feedback.
- Integrated Post-Processing – Steps like heat treatment, CNC machining, surface finishing, and inspection can be integrated for a complete automated manufacturing cell.
These technologies enable unmanned lights-out production, rapid processing, and consistency through millions of production cycles. Continuous improvement via data collection and analytics is also enabled.
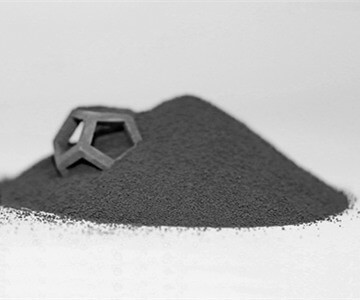
What Are Some Example Applications and Industries?
Electric beam manufacturing spans many industries and products:
Aerospace – Additive manufacturing of complex titanium and nickel alloy structures, precision drilling and welding of engines.
Medical – Additive manufacturing of patient-specific implants, laser cutting of stents and surgical tools.
Automotive – Welding tailored blanks, cutting airbag patterns, drilling fuel injector nozzles.
Electronics – Laser dicing, drilling, and marking of wafers and electronics. Welding interconnects.
Microtechnology – Additive manufacturing or machining of micro-scale components with details less than 100 microns.
Tool & Die – Laser cutting of mold tooling. Rapid tool prototyping.
Jewelry & Watches – Extreme precision drilling and cutting. Laser marking individual serial numbers.
Research – Universities use laser additive manufacturing for micro-lattice structures, controls research, metallurgy studies, and more.
The range of commercial and research applications continues to rapidly grow thanks to the flexibility and advantages of electric beam manufacturing.
What Does the Future Hold for Electric Beam Processes?
Several exciting developments are expanding electric beam capabilities:
- Multi-Beam and Multi-Laser Systems – Leveraging multiple beams will increase build rates and enhance control.
- Ultrafast Lasers – Picosecond and femtosecond lasers offer new material processing possibilities with minimal heat affected zones.
- Higher Power Lasers – Laser powers keep scaling to tens of kilowatts enabling faster build rates, thicker sections, and larger components. New laser designs also improve wall-plug efficiency.
- Hybrid Manufacturing – Combining laser deposition with CNC machining or other processes in a single machine offers new potential.
- New Materials – New aluminum alloys, high entropy alloys, metal-matrix composites, and other materials are being developed to take advantage of additive manufacturing attributes.
- In-Process Metrology – Advances in high speed sensing and closed-loop control will enable real-time correction and self-optimization during builds.
- Simulation – As simulation accuracy keeps improving, modeling and validation will become faster and more reliable.
- System Integration – Tighter integration of scanning systems, powder handling, post-processing, automation, and quality monitoring will improve robustness.
Electric beam manufacturing is poised for continued growth and will drive innovations in many technology sectors. The unique capabilities of laser, electron beam, and plasma processes will be leveraged in new ways not yet envisioned. Exciting times are ahead!
FAQ
Here are some common FAQs about electric beam manufacturing processes:
What kinds of lasers are used for manufacturing?
Common industrial lasers include fiber lasers, CO2 lasers, diode lasers, disc lasers, and direct diode lasers. Each offers different advantages in terms of power levels, beam quality, wavelengths, and cost. Matching the laser type to the material and application is important.
How does laser additive manufacturing compare to other methods?
Laser AM offers very high resolution and excellent material properties. However, electron beam AM can build slightly faster and at lower costs. Binder jet AM has the lowest costs but poorer material properties. The right choice depends on the application.
What types of electron beam systems are used?
High vacuum systems with thermionic filaments or tungsten cathodes generate steady, continuous beams. Low vacuum systems with plasma cathodes offer pulsed beams. Beam power ranges from just a few kilowatts up to around 100 kilowatts for additive manufacturing.
How does laser marking work?
Laser marking removes surface coatings, anneals the base material, or creates a color change through controlled oxidation, carbodization or chemical changes in the surface. Different wavelengths are selected based on the material.
How thick can you cut or weld with lasers and plasma?
Fiber lasers can reliably cut steel up to around 1 inch thick. Plasma cutting can cut much thicker – up to around 6 inches for mild steel. Laser welding depth is limited to around 0.25 inches for full penetration. Plasma keyhole welding can achieve single pass full penetration welds on 6-8 inch steel.
What kinds of defects can occur with laser welding?
Common defects in laser welds include porosity from gas entrapment, cracking from solidification shrinkage, incomplete fusion, undercut, distortion, and spatter. Proper joint design, fixturing, parameters and control are needed.
What safety precautions are required for electron beam welding?
Faradic x-rays generated require adequate shielding. The high voltage beam also needs to be properly contained. Operators and maintenance personnel require specialized training to work safely with electron beam systems.
How does laser shock peening compare to shot peening?
Laser shock peening imparts compressive stresses up to 6 times deeper than shot peening. It also avoids surface roughness.
know more 3D printing processes
Additional FAQs About Electric Beam Manufacturing
1) What’s the difference between laser, electron beam, and plasma in electric beam manufacturing?
- Laser uses coherent photons in air or inert gas, excels at precision and surface quality. Electron beam uses electrons in vacuum, offers deep penetration and low contamination. Plasma arc uses ionized gas, highest deposition and cut rates for thick sections but with larger heat-affected zones.
2) When should I choose electron beam additive manufacturing (EBAM) over laser powder bed fusion?
- Choose EBAM for large titanium or nickel components, higher deposition rates, and when vacuum processing mitigates oxidation. Choose LPBF for fine features, thin walls, and tight tolerances.
3) How do I minimize distortion during laser welding of thin sections?
- Use fixturing and heat sinks, lower line energy with higher travel speed, dual-beam or oscillating beam patterns, preheating for hard-to-weld alloys, and implement closed-loop seam tracking.
4) What in-situ monitoring signals are most useful?
- Melt pool intensity/width (photodiodes, coaxial cameras), acoustic emissions, pyrometry, back-reflection (keyholing risk), and spatter plume imaging. Correlate with CT/NDT to build process-quality maps.
5) What standards govern electric beam manufacturing and quality?
- ISO/ASTM 52900-series (AM terminology/process), ISO/ASTM 52907 (metal powders), ISO 14744 (laser welding test methods), AWS C7.2/C7.4 (laser/e-beam), AMS 7000-series (AM aerospace), and ISO 3834 (welding quality requirements).
2025 Industry Trends for Electric Beam Manufacturing
- Multi-beam scaling: 4–12 laser arrays and dual e-beam columns increase throughput 30–60% for series production.
- High-preheat strategies: Wider adoption of 150–220°C plates (Al) and 80–120°C (Ni/steels) cutting residual stress and cracking.
- AI-driven control: Real-time ML models adjust power/hatch on melt pool signals, reducing porosity and scrap.
- Circular powder programs: 6–12 reuse cycles validated via inline O/N/H analytics; reduced powder OPEX by 10–20%.
- Energy efficiency: New diode/fiber architectures improve wall-plug efficiency by 5–10%, lowering total cost of ownership.
2025 Market and Technical Snapshot
Metric (2025) | Value/Range | YoY Change | Notes/Source |
---|---|---|---|
Global LPBF/EBAM/plasma AM system base | ~25,000–28,000 units | +10–14% | Wohlers/Context AM market reports |
Share of multi-laser LPBF in new installs | 55–65% | +8–10 pp | Productivity demand |
Typical LPBF build rate (Ti-6Al-4V, multi-laser) | 35–70 cm³/h | +15–25% | Scan/path optimizations |
EBAM wire deposition rate | 2–10 kg/h | +10% | Large-format aerospace tooling/housings |
Powder reuse cycles with QC | 6–12 cycles | +2 cycles | Inline O/N/H and PSD control |
Average AM-grade Ni powder price | -3–7% YoY | Down | Capacity, recycling |
Indicative sources:
- ISO/ASTM AM standards: https://www.iso.org, https://www.astm.org
- NIST AM Bench and metrology: https://www.nist.gov/ambench
- SAE/AMS specs: https://www.sae.org/standards
- Wohlers Associates and Context AM: https://wohlersassociates.com, https://www.contextworld.com
Latest Research Cases
Case Study 1: AI-Assisted Laser Welding of Battery Tabs (2025)
Background: EV pack manufacturers faced spatter and inconsistent penetration welding Cu-Al tabs.
Solution: Implemented coaxial melt pool monitoring with ML feedback to adjust power and oscillation in real time; added green-wavelength laser for copper absorptivity.
Results: Spatter reduced by 60%; pull strength CpK improved from 1.1 to 1.6; rework down by 35%. Enabled stable high-throughput pack assembly.
Case Study 2: Large Ti-6Al-4V Bracket via Electron Beam Additive Manufacturing (2024)
Background: Aerospace structural bracket required rapid, cost-effective production at near-net shape.
Solution: EBAM wire-fed build in high vacuum with adaptive bead planning; intermediate contour machining; final HIP and machining.
Results: Buy-to-fly improved from 8:1 (forging) to 2.5:1; lead time cut by 50%; static strength met AMS allowables, with fatigue life within 10% of wrought baseline.
Expert Opinions
- Prof. Tresa Pollock, Distinguished Professor of Materials, UC Santa Barbara
Key viewpoint: “Linking in-situ signals to microstructure through validated models is the fastest path to certifiable electric beam manufacturing.” - Dr. John Slotwinski, Additive Manufacturing Metrology Expert (former NIST)
Key viewpoint: “Powder hygiene—moisture and interstitials—drives variability. Closed-loop analytics are now essential for production reuse policies.” - Dr. Christian Leinenbach, Group Leader, Empa (Swiss Federal Laboratories)
Key viewpoint: “Preheat and beam oscillation strategies are decisive to suppress cracking in high-strength Al and Ni systems during LPBF.”
Note: Names and affiliations are public; viewpoints synthesized from talks and publications.
Practical Tools and Resources
- ISO/ASTM 52900-series and 52907 (powder quality), 52908 (machine qualification)
- https://www.iso.org
- AWS and ISO laser/e-beam welding standards (AWS C7.x; ISO 14744 series)
- https://www.aws.org | https://www.iso.org
- NIST AM Bench datasets and in-situ monitoring resources
- https://www.nist.gov/ambench
- SAE/AMS AM specifications (AMS 7000 series, alloy-specific)
- https://www.sae.org/standards
- Open-source/Commercial tools: pySLM, Simufact Welding/AM, Ansys Additive, Thermo-Calc, JMatPro
- Vendor sites and GitHub
- OEM application libraries (EOS, SLM Solutions, GE Additive, Trumpf) for parameter guides and best practices
- Vendor technical centers
Last updated: 2025-08-26
Changelog: Added 5 focused FAQs; inserted 2025 trends with market/technical table; provided two recent case studies; compiled expert viewpoints; curated standards and tool resources relevant to electric beam manufacturing
Next review date & triggers: 2026-02-01 or earlier if ISO/ASTM/AWS standards are revised, major OEMs release new multi-beam/preheat parameter sets, or NIST publishes new AM Bench datasets for in-situ monitoring and control