Introduction
atomizing metal powder has become an increasingly important material across a wide range of industries. The atomization process produces fine, spherical metallic powders with precise particle size distribution, allowing for improved performance in applications like metal 3D printing, injection molding, and pressing and sintering. As technology develops and new uses for atomized powder emerge, the global market continues to expand rapidly.
This article will provide a comprehensive overview of the atomized metal powder market. It will examine the technology behind atomization, the main applications driving demand, the competitive landscape, and future trends that could disrupt the status quo. Read on for an in-depth look at this vital material that is shaping the future of manufacturing.
What is atomizing metal powder?
Atomized metal powder is produced through a process called atomization, where molten metal is turned into a spray of fine droplets using gas or water pressure. The droplets rapidly cool and solidify into spherical powders with a controlled particle size ranging from a few microns up to around 100 microns.
Compared to conventional metal powders made through milling or electrolysis, atomized powders have superior flowability, packing density, and repeatability. This makes them ideal for industrial applications like metal injection molding, additive manufacturing, and pressing and sintering.
Atomization allows precise control over particle size distribution, morphology, density, and microstructure. By carefully selecting process parameters, powder can be tailored for specific applications and material performance requirements.
The most common techniques for atomization are:
- Gas atomization – High pressure inert gas (usually nitrogen or argon) turns the metal into a spray of droplets. This produces the most spherical particles.
- Water atomization – Similar to gas atomization, but with water as the atomizing medium. Water atomization is cheaper but produces more irregular particles.
- Rotating electrode process – Molten metal driven off a spinning electrode produces finer powders down to 5 microns.
- Plasma atomization – Extremely high temperatures from a plasma torch allow refractory metals like tungsten to be atomized.
Atomization works for almost any alloy system including ferrous alloys like stainless steel, non-ferrous alloys, superalloys, and reactive alloys like titanium and aluminum. The most widely atomized metals are iron, copper, aluminum, nickel, and cobalt.
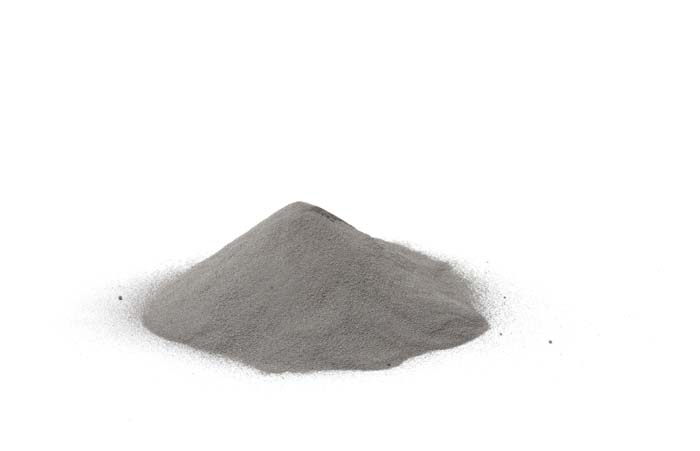
Applications of Atomized metal powder
Atomized metal powders enable improved material properties and part performance across a diverse range of manufacturing processes and end-use applications.
Metal Additive Manufacturing
One of the biggest growth areas for atomized powder is metal additive manufacturing (AM), also known as 3D printing. The fine spherical morphology allows the powder to spread and compact evenly during selective laser melting and other powder bed fusion processes. This facilitates complex geometries with superior mechanical properties to conventional manufacturing.
Common alloys for AM powder include titanium, aluminum, nickel-based superalloys, tool steels, and cobalt-chrome. The global market for metal AM powder reached around $315 million in 2019 and is forecast to exceed $1 billion by 2027.
Metal Injection Molding
Metal injection molding (MIM) uses atomized powder mixed with a binder to create a feedstock that can be shaped using injection molding. After molding, the part undergoes debinding and sintering. MIM can produce complex, high density components combining the design flexibility of plastic injection molding with the strength of metal.
Atomized stainless steel, titanium alloys, and tungsten heavy alloys are popular for MIM. Global demand for MIM powder is estimated to reach over 270,000 metric tons by 2025. Key end-uses include automotive, firearms, medical devices, and consumer products.
Pressing and Sintering
Atomized powders are widely used in pressing and sintering of structural parts and cutting tools. The powder is compacted in a die at high pressure before being sintered just below the melting point. This produces near net-shape parts with controlled material properties.
Iron, copper, and aluminum powders are commonly used in pressing and sintering. Porous filters, bushings, gears, magnets, and more can be manufactured through powder metallurgy techniques with atomized powder.
Thermal Spray Coatings
In thermal spray processes like plasma spraying, atomized powders are heated, accelerated, and sprayed onto a substrate to form a protective coating. The fine spherical shape allows the powder to flow through spray guns smoothly and produce consistent, high-quality coatings.
Tungsten carbide-cobalt, chromium carbide, aluminum/zinc alloys, and other wear/corrosion resistant alloys are applied as coatings across industries like oil and gas, aerospace, marine, and mining.
Brazing and Soldering
Atomized powders in alloys like nickel, silver, and aluminum can be used as filler material for brazing and soldering. The powders increase joint strength and ductility. They are also available as pastes mixed with a flux.
Microjoining of electronics as well as aerospace components relies on high performance braze alloys produced through atomization. The fine uniform powder morphology enables excellent melt flow and joint formation.
Other Applications
Other niche applications taking advantage of atomized metal powder include:
- Friction materials like brake pads and clutches
- Bonded magnets
- Metal polishes
- Electrical contacts
- Spark plasma sintering
- Chemical vapor deposition powder feedstock
- Pyrotechnic mixes
Continuing research is also uncovering new possibilities in emerging technologies such as micro-scale welding and smart materials.
Overall, the unique properties of atomized powder have made it an essential material for critical industrial components and cutting-edge manufacturing techniques.
Global Atomized metal powder Market
Worldwide consumption of atomized metal powder was estimated at over 500,000 tons in 2019, corresponding to around $5 billion in market value. The market has experienced sustained growth at 5-6% CAGR over the past decade, driven largely by metal additive manufacturing.
Regional Breakdown
- Asia Pacific – The largest regional market, accounting for close to 40% of global demand as of 2019. High production and consumption in China, widespread use in automotive and industrial manufacturing in Japan and South Korea.
- North America – The second largest share at over 30% of the global market. Major consumption in the United States for aerospace, medical devices, and metal AM.
- Europe – Contributes around 25% of total demand. Automotive and machinery sectors are large consumers in Germany, Italy, France, and the UK.
- Rest of World – Relatively small but fast growing demand from Latin America, Middle East, and Africa.
Key Players
The atomized metal powder industry is fragmented, with over 500 companies worldwide. However, around 15 leading corporations control the majority of the market.
Major global suppliers include:
- Hoeganaes Corporation
- GKN Plc
- Rio Tinto Metal Powders
- JFE Steel Corporation
- Sandvik AB
- Praxair Technology Inc.
- Arconic Inc.
- Miba AG
- Metaldyne Performance Group
- Hitachi Chemicals Co. Ltd
These companies have established expertise and capacity in gas, water, and plasma atomization. Competition is based on consistency, quality, particle size range, alloy capabilities, and pricing.
Pricing Trends
Atomized metal powder is more expensive than conventional milled and electrolytic powder. Cost depends on:
- Alloy – More expensive alloys like titanium generally exceed $50/kg. Common steel grades are $5-20/kg.
- Particle size – Finer powder below 25 microns demands a premium.
- Purity – High purity, alloy-specific powder is costlier than lower grade varieties.
- Quantity – Bulk orders of over 1,000 kg offer significantly lower per-unit pricing.
Despite higher prices, the superior properties continue to drive adoption across end-use sectors. The high margin powder business remains attractive for leading metals companies.
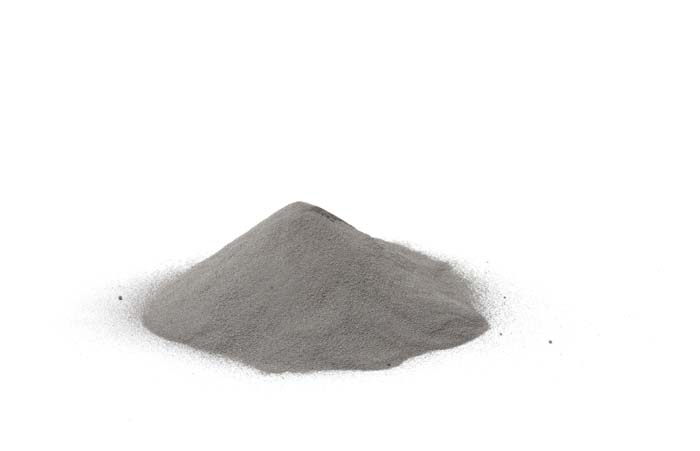
Future Outlook and Growth Opportunities
Multiple factors point towards a bright future for atomized metal powder producers and consumers:
Metal Additive Manufacturing Will Drive Robust Growth
Expanding adoption of 3D printing for production applications is the major catalyst for powder demand. According to estimates, the metal AM powder market will maintain over 25% CAGR over the next five years. New alloys, lower costs, and increased part complexity will support growth.
Increasing Use in Automotive Manufacturing
Lightweighting and performance needs are driving automotive manufacturers towards metal injection molding and sintered components using atomized powders. The shift towards electric vehicles is also positive for demand as companies employ laser powder bed fusion for electric motor parts.
High-Performance Materials Advancement
Superalloys, refractory metals, and MIM alloys are achieving higher strengths and working temperatures. This supports substitution of metal parts for ceramics in extreme environments. Advanced alloy development will require specialized atomization techniques.
Supply Chain Localization
Growing focus on resilient regional supply chains could lead more metals companies to establish local atomization capacity rather than importing powder. This may increase competition but will ultimately benefit end-users.
Market Consolidation
Mergers and acquisitions are expected among powder producers as competition intensifies. Larger players will gain economies of scale while also developing differentiated product offerings and services. But ample room will remain for smaller niche powder manufacturers.
Metal Recycling Opportunities
The high value of atomized powders means recycling and reusing scrap powder will become more common. This will lower waste while moderately decreasing demand for newly produced powder over the long term.
Key Challenges Facing the Industry
Amid the positive outlook, there are a few potential hurdles facing atomized metal powder over the next decade:
Price Volatility
As a high value material, atomized powder pricing fluctuates with metal costs. Nickel and cobalt price spikes can rapidly raise powder prices, hurting profit margins for manufacturers. End-users may delay orders or qualify alternative alloys to manage costs.
Excess Capacity
Leading powder producers have invested heavily in additional atomization capacity expecting strong growth. However, short-term reductions in demand could lead to oversupply and intensify pricing competition.
Custom Alloy Development
Requirements for custom alloys with unique properties is increasing, especially for metal AM. This will strain the R&D resources of some smaller powder manufacturers.
Safety Concerns
Fine metal powders can combust or cause respiratory health hazards. Meeting increasingly stringent safety regulations will raise production and handling costs. But safety is essential to prevent accidents which could impact industry growth.
Trade Protectionism
Atomized metal powder are widely exported and imported for optimum supply chain efficiency. However, trade restrictions related to national security or local production mandates may disrupt established powder trade flows.
Overcoming these obstacles through technology, improved practices, and collaborative policy will ensure the atomized metal powder industry remains dynamic and profitable.
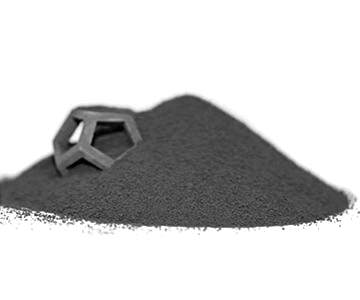
Conclusion
Atomized metal powder has cemented itself as an essential advanced material supporting superior performance and efficiency across manufacturing industries. Though a mature market, new applications in metal additive manufacturing, automotive, and other sectors will drive healthy growth over the next five to ten years.
Leading global suppliers have invested in expanded atomization capacity and new alloys to reap the benefits of rising demand. At the same time, challenges like volatile metal costs and trade issues will need to be navigated. Overall, the unique properties and capabilities enabled by atomized powder mean its bright future is likely assured.
The atomized metal powder market will remain at the crossroads of material science, industrial technology, and precision manufacturing for years to come.
FAQ
What are the main benefits of using atomized metal powder?
Atomized powders provide excellent flowability, spreadability, packing density and repeatability thanks to the precise spherical morphology. This leads to optimal material properties and performance.
What is the typical particle size range for atomized powder?
Most commonly between 5-100 microns. Finer powder below 25 microns is used for additive manufacturing and sintering applications. Coarser powder up to around 100 microns suits pressing/compaction and thermal spray.
What is the difference between gas atomization and water atomization?
Gas atomization using nitrogen or argon produces the most spherical powder. Water atomization is a simpler, cheaper process but generates more irregular powder shapes.
What are the newest technologies for producing atomized metal powder?
Rotating electrode processes can produce ultrafine powder down to just a few microns. Plasma atomization allows high temperature alloys like tungsten to be atomized.
Which metal alloys are commonly atomized today?
Iron, copper, aluminum, nickel, and cobalt alloys are the most widely atomized metals. Titanium, refractory metals, stainless steels, tool steels, and superalloys are gaining in popularity.
What industry consumes the most atomized metal powder?
Metal additive manufacturing has become the biggest demand driver, but automotive and industrial presses also consume large volumes of atomized powder.
Which geographic region dominates the atomized powder market?
Asia Pacific accounted for around 40% of global demand in 2019 thanks to high production and consumption levels in China. North America and Europe each hold over 25% market share.
Are prices expected to increase or decrease over the next five years?
Prices will likely remain stable or see moderate increases as new alloys and finer powders gain share. But volatility due to changing bulk alloy costs will continue.
What is the future outlook for the atomized metal powder industry?
Forecasts remain strongly positive, predicting over 25% average annual growth over the next five years driven by metal AM, automotive, and aerospace demand.