Fabricação de feixes elétricos refere-se a uma variedade de processos de fabricação que utilizam fontes de energia concentradas, como lasers, feixes de elétrons ou arcos de plasma, para derreter, fundir ou vaporizar materiais de forma seletiva. Com o controle preciso da fonte de energia, esses processos permitem uma fabricação extremamente precisa e repetível com o mínimo de distorção térmica. A fabricação por feixe elétrico permite a produção de geometrias complexas e recursos em microescala que não podem ser obtidos pelas técnicas tradicionais de fabricação subtrativa.
Como funcionam os processos de fabricação de feixes elétricos?
A fabricação de feixes elétricos se baseia nos princípios de densidade de energia e transferência de calor. Ao concentrar a energia em um feixe extremamente estreito, é possível obter uma densidade de energia muito alta. Quando essa energia concentrada interage com o material, apenas um pequeno volume é derretido ou vaporizado. O calor se dissipa rapidamente desse pequeno volume de interação para o material ao redor, que permanece mais frio. Isso permite a fusão, o derretimento ou a vaporização extremamente precisos e localizados do material.
Há vários tipos comuns de fabricação de feixes elétricos:
Fabricação de feixes de laser
- Usa um feixe de laser altamente focado como fonte de energia
- Os feixes de laser podem ser focalizados até 0,01 mm ou menos
- Permite uma precisão muito alta e minimiza a distorção térmica
- Usado para soldagem, corte, revestimento, manufatura aditiva, etc.
Fabricação de feixes de elétrons
- Usa um feixe focalizado de elétrons como fonte de energia
- Os feixes de elétrons podem ser focalizados até 0,1 mm
- Permite trabalhar em um ambiente a vácuo
- Usado para soldagem, manufatura aditiva, etc.
Fabricação de arco de plasma
- Usa um jato de plasma como fonte de energia
- Os arcos de plasma oferecem alta densidade de energia
- Permite a soldagem de metais por meio de orifícios
- Usado para soldagem e corte de alta penetração
Em todos os casos, a peça de trabalho e/ou a fonte de feixe são movidas por meio de controle CNC para traçar a geometria desejada. Os controles computadorizados e a automação permitem que o processo seja altamente repetível e consistente.
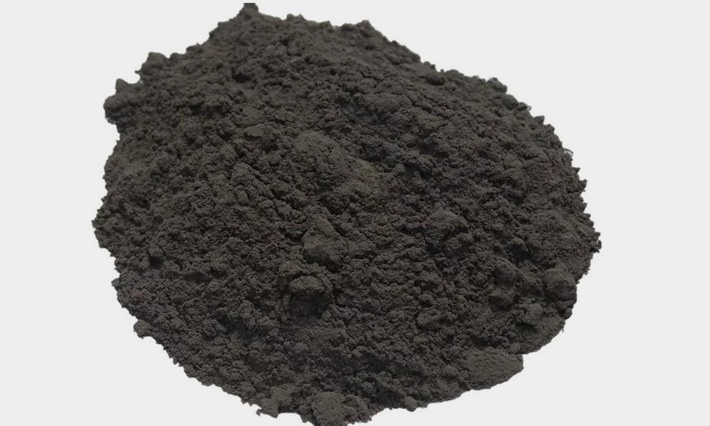
Quais são os benefícios da fabricação de feixes elétricos?
Em comparação com os métodos de fabricação convencionais, a fabricação por feixe elétrico oferece várias vantagens:
- Extrema precisão - Devido aos feixes de energia altamente focados, é possível obter tamanhos e tolerâncias de recursos de até 0,01 mm. Isso permite componentes e eletrônicos em microescala.
- Distorção térmica mínima - Apenas um pequeno volume de material é derretido de cada vez. Isso permite um resfriamento rápido e minimiza os efeitos térmicos prejudiciais. As peças apresentam menos deformações e distorções.
- Não são necessárias ferramentas - O feixe de energia atua essencialmente como uma ferramenta, eliminando a necessidade de ferramentas físicas. Isso permite a prototipagem rápida e a iteração do projeto.
- Altamente repetível - Os feixes controlados por CNC permitem um processamento extremamente consistente e repetitivo, adequado para a produção em massa.
- Sem forças ou tensões - Como não há contato físico, estruturas delicadas podem ser feitas sem danos. Também são possíveis características e geometrias internas.
- Excelentes propriedades metalúrgicas - Taxas de resfriamento rápidas podem criar estruturas de granulação fina e propriedades materiais exclusivas.
- Ampla compatibilidade de materiais - Metais, polímeros, compostos e cerâmicas podem ser processados com sucesso com a seleção adequada de parâmetros.
Essas vantagens permitem que a fabricação por feixe elétrico seja usada para uma ampla gama de aplicações que não são facilmente produzidas por outros meios. Os processos continuam a melhorar em termos de precisão, repetibilidade e custo-benefício.
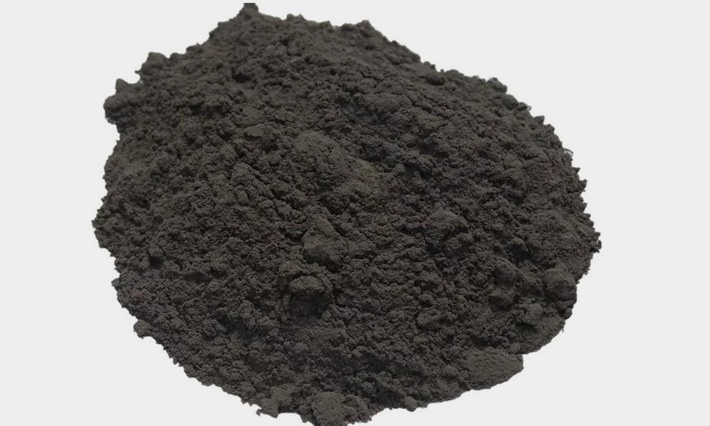
Quais materiais podem ser processados?
Muitos materiais diferentes são compatíveis com a fabricação de feixes elétricos:
Metais - Todos os metais comuns podem ser processados, incluindo aço, alumínio, titânio, ligas de níquel e outros. Diferentes ligas e têmperas podem exigir parâmetros ajustados. Os lasers de fibra oferecem vantagens com materiais altamente refletivos, como cobre ou ouro.
Polímeros - Os lasers de alta potência podem derreter seletivamente uma ampla gama de polímeros termoplásticos para soldagem ou manufatura aditiva. Alguns polímeros, como o PTFE, exigem fontes de feixe especializadas.
Compostos - Os polímeros reforçados com fibras podem ser processados em uma extensão limitada se os parâmetros forem controlados para evitar danos térmicos às fibras.
Cerâmica - Os materiais cerâmicos exigem lasers de alta potência muito especializados para o processamento, devido à sua natureza refratária e à baixa condutividade térmica.
Silício - Os lasers podem aparar, perfurar e cortar wafers de silício para aplicações microeletrônicas. O corte a plasma também está sendo adotado.
Diamante - Devido à sua dureza e resistência química, o diamante só pode ser usinado de forma prática com o uso de lasers.
A seleção e o controle adequados dos parâmetros do feixe são cruciais para obter um bom processamento e evitar danos térmicos descontrolados ao trabalhar com diferentes materiais. O desenvolvimento do processo é uma primeira etapa importante.
Quais são os processos comuns de feixe elétrico?
Há vários processos de fabricação bem estabelecidos que utilizam fontes de energia de feixe elétrico:
Corte a laser
- O corte a laser usa um laser focado de alta potência para derreter/vaporizar o material e induzir o corte
- Pode cortar perfis 2D complexos de chapas metálicas, placas e tubos com distorção mínima
- O processo é muito preciso e repetível para automação
Soldagem a laser
- A energia focalizada do laser permite a soldagem precisa de componentes miniaturizados ou materiais finos
- A baixa entrada de calor minimiza a distorção, o que é crucial para peças delicadas
- Pode soldar materiais dissimilares e reativos, desde que o projeto da junta seja adequado
Perfuração/ablação a laser
- Os lasers podem fazer furos em metais, polímeros e compostos sem desgaste da ferramenta
- As técnicas de percussão e trepanação podem criar furos com diâmetros finos e acabamento
- O processamento de múltiplos pulsos permite furos de proporção muito alta
Marcação a laser
- A marcação a laser é uma forma sem contato de marcar peças para identificação, marca ou rastreabilidade
- Cria marcas permanentes na superfície sem remoção ou distorção do material
- Pode marcar metais, plásticos, cerâmicas, papel, couro e muitos outros materiais
Revestimento a laser
- O revestimento a laser deposita um material de revestimento em uma peça usando um feixe de laser focalizado
- Obtém a ligação metalúrgica à medida que o pó de revestimento derrete no substrato
- Permite a criação de revestimentos resistentes ao desgaste ou à corrosão
Peening por choque a laser
- O laser shock peening usa pulsos de alta potência para criar ondas de choque que transmitem tensões de compressão
- As tensões compressivas inibem o início de trincas por fadiga e melhoram a vida útil da peça
- São criadas tensões compressivas mais profundas em comparação com o shot peening convencional
Manufatura aditiva a laser
- Também conhecido como fusão de leito de pó a laser, sinterização direta de metal a laser ou fusão seletiva a laser
- Processo de impressão 3D camada por camada usando pó metálico e fusão a laser
- Permite geometrias complexas e peças personalizadas diretamente dos dados de CAD 3D
Soldagem por feixe de elétrons
- Usa um feixe de elétrons focalizado para proporcionar alta penetração de solda no vácuo
- Ideal para unir metais reativos, como o titânio, que são propensos à contaminação atmosférica
- Pode soldar seções muito espessas devido à capacidade de penetração total
Manufatura aditiva por feixe de elétrons
- Também conhecido como fusão em leito de pó por feixe de elétrons ou fusão por feixe de elétrons
- Constrói peças metálicas em 3D a partir de pó metálico usando uma fonte de calor de feixe de elétrons
- O processo controlado pelo meio ambiente evita problemas com a oxidação do material
Soldagem a arco plasma
- A soldagem a arco de plasma usa um jato de plasma restrito para concentrar a energia térmica
- Pode penetrar totalmente em seções espessas em um único passe, ao contrário da soldagem tradicional
- Produz cordões de solda com distorção mínima e excelentes propriedades metalúrgicas
Corte a arco plasma
- Usa um jato de plasma de alta temperatura para derreter/oxidar o material e induzir o corte
- Tem capacidade de alta velocidade de corte para chapas grossas e pode produzir bordas de boa qualidade
- O fluxo de plasma concentra o calor em uma área restrita para um corte preciso
Há muitos outros processos de nicho, como peening a laser, vitrificação a laser, recozimento a laser, perfuração de buraco de fechadura a plasma, etc., que aproveitam a energia do feixe de maneiras especializadas. A lista continua a crescer com os avanços na tecnologia de geração de feixes e nos recursos de controle.
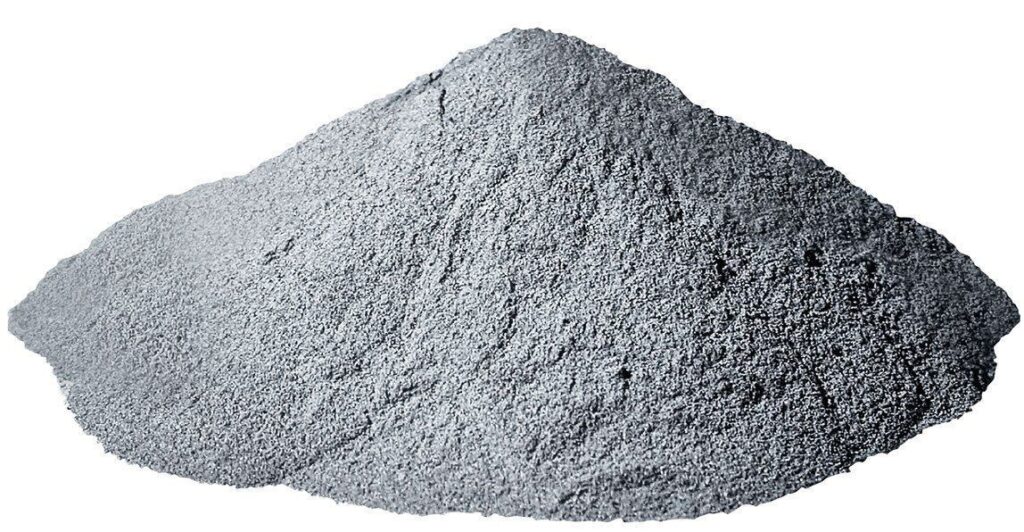
Como a garantia de qualidade funciona com esses processos?
Práticas consistentes de controle e garantia de qualidade são importantes para qualquer processo de fabricação. Alguns dos principais aspectos de qualidade dos processos de feixe elétrico incluem:
- Monitoramento de processos - Muitas máquinas têm sensores para monitorar a potência do feixe, a posição, o foco, os fluxos de gás, os níveis de vácuo etc. durante o processamento. Os dados são registrados e analisados.
- Inspeção em processo - Os sistemas de visão mecânica podem inspecionar opticamente as peças em processo, procurando defeitos e processamento inadequado. Isso permite uma ação corretiva rápida.
- Inspeção pós-processo - As peças são inspecionadas após a produção usando metrologia óptica, radiografia de raios X, testes ultrassônicos, testes mecânicos, metalografia, etc.
- Otimização de parâmetros - O projeto de experimentos ajuda a determinar os parâmetros ideais para atender aos requisitos. Os parâmetros são validados em várias compilações.
- Manutenção e calibração - Os geradores de feixe e os sistemas de posicionamento exigem manutenção e recalibração regulares para garantir uma operação estável.
- Treinamento de operadores - Um treinamento abrangente para operadores de máquinas e engenheiros de processo garante a operação adequada.
- Rastreabilidade - A identificação da peça e os dados de produção ajudam a rastrear as peças finais até todos os parâmetros do processo e lotes de matéria-prima.
- Conformidade com os padrões - São implementados princípios rigorosos de gerenciamento de qualidade de acordo com as normas ISO e do setor.
- Controle de processos - O controle estatístico de processos por meio de gráficos de controle rastreia a estabilidade do processo e detecta desvios das condições nominais.
Com uma infraestrutura de qualidade adequada, os processos de feixe elétrico oferecem um processamento muito consistente e repetível. Tolerâncias estreitas, propriedades do material e desempenho são facilmente alcançáveis.
Quais são as precauções de segurança necessárias?
A fabricação de feixes elétricos exige algumas medidas de segurança exclusivas:
- Segurança a laser - Devem ser tomadas precauções para evitar a exposição direta dos olhos ou queimaduras na pele. São necessários óculos de proteção, barreiras, peles, alarmes e travas.
- Perigos de feixes de elétrons - São gerados raios X farádicos que exigem blindagem. Os feixes de elétrons dispersos também exigem contenção.
- Extração de fumaça - Muitos processos de feixe geram fumaça de solda, partículas ou gases perigosos que exigem extração localizada de fumaça.
- Riscos elétricos - Os geradores de feixe envolvem altas tensões, o que garante isolamento, separação e intertravamentos de acesso adequados.
- Riscos de incêndio - Vapores, óleos e poeiras inflamáveis criam um risco de incêndio com a energia do feixe. A limpeza adequada é fundamental.
- Exposição ao ruído - Alguns processos de feixe, como o corte a arco de plasma, produzem ruídos altos que exigem proteção auditiva.
- Riscos ergonômicos - O levantamento, a flexão e os movimentos repetitivos inadequados podem causar distensões ou outras lesões.
Com os devidos controles de engenharia, políticas administrativas, equipamentos de proteção individual (EPI) e treinamento, esses riscos podem ser gerenciados de forma eficaz para um local de trabalho seguro. Também é necessário um projeto cuidadoso das instalações e dos equipamentos para isolar os perigos dos feixes.
Como as peças são projetadas e simuladas para processos de vigas?
Várias ferramentas de software auxiliam no projeto e na simulação de peças para a fabricação de feixes elétricos:
- Software CAD - Os programas de CAD permitem a modelagem 3D detalhada de geometrias de componentes otimizadas para a manufatura aditiva. As restrições de projeto podem ser incorporadas.
- Otimização de topologia - Os algoritmos podem otimizar o layout do material para melhorar o desempenho sob carga. Isso permite uma redução significativa do peso.
- Software de simulação - A análise de elementos finitos e a dinâmica de fluidos computacional simulam tensões, temperaturas, efeitos de distorção, interações térmico-estruturais, tensões residuais, etc. Isso permite a validação do projeto.
- Modelagem de processos - Um software especializado pode simular a interação do feixe de energia com leitos de pó para modelar poças de fusão, gradientes de temperatura, vaporização, etc. Isso garante a viabilidade do processo.
- Planejamento de construção - Os processadores de construção cortam modelos CAD e geram percursos de ferramenta ideais para sistemas aditivos, levando em conta suportes, acúmulo de calor, tensões residuais e muito mais.
- Planejamento de inspeção - Os requisitos de inspeção podem ser definidos em modelos CAD. Os modelos, então, conduzem as rotinas de inspeção robótica.
- Dados da máquina - Os dados reais da máquina são incorporados às simulações para maior precisão. A validação em circuito fechado garante que os projetos sejam fabricáveis.
O poder cada vez maior das simulações, juntamente com a validação de construção real, permite "projetar para a capacidade de fabricação". Isso reduz o tempo e os custos de desenvolvimento e, ao mesmo tempo, garante alta qualidade.
Como os sistemas são automatizados e controlados?
Os processos modernos de feixes elétricos utilizam automação e controle abrangentes:
- Controle CNC - Os sistemas CNC de múltiplos eixos posicionam o feixe e/ou a peça de trabalho com alta precisão por meio de trajetórias complexas.
- Controle de movimento - Os rolamentos eletromagnéticos de precisão, os motores lineares e a codificação óptica proporcionam movimentos suaves e precisos.
- Processamento de alta velocidade - Galvanômetros, espelhos poligonais e outras técnicas digitalizam e distribuem rapidamente a energia para altas taxas de processamento.
- Rastreamento de costura - O monitoramento através da lente e baseado em câmera permite o controle adaptativo para acompanhar as costuras de solda ou corrigir o processamento em tempo real.
- Manipulação avançada de feixes - A focalização dinâmica, a divisão/formatação do feixe e a óptica especializada controlam com precisão a distribuição de energia do feixe.
- Visão mecânica - O monitoramento óptico durante o processo da geometria da poça de fusão, das emissões térmicas e da geometria garante a qualidade. O controle de loop fechado está habilitado.
- Manuseio preciso de pós - A deposição, o alisamento e o recobrimento de pó cuidadosamente controlados permitem a manufatura aditiva de alta precisão.
- Atmosfera inerte - Os sistemas de vácuo ou os gases de cobertura inertes evitam a oxidação do material.
- Metrologia em processo - O monitoramento in-situ de temperaturas, emissões e dados de metrologia dimensional fornece feedback ao vivo do processo.
- Pós-processamento integrado - Etapas como tratamento térmico, usinagem CNC, acabamento de superfície e inspeção podem ser integradas para uma célula de fabricação automatizada completa.
Essas tecnologias permitem a produção não tripulada com luzes apagadas, o processamento rápido e a consistência em milhões de ciclos de produção. O aprimoramento contínuo por meio da coleta e análise de dados também é possível.
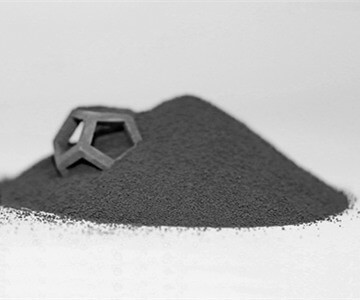
Quais são alguns exemplos de aplicativos e setores?
A fabricação de feixes elétricos abrange muitos setores e produtos:
Aeroespacial - Fabricação aditiva de estruturas complexas de titânio e ligas de níquel, perfuração de precisão e soldagem de motores.
Médico - Fabricação aditiva de implantes específicos para pacientes, corte a laser de stents e ferramentas cirúrgicas.
Automotivo - Soldagem de peças em bruto sob medida, corte de padrões de airbag, perfuração de bicos injetores de combustível.
Eletrônicos - Corte, perfuração e marcação a laser de wafers e componentes eletrônicos. Soldagem de interconexões.
Microtecnologia - Fabricação ou usinagem aditiva de componentes em microescala com detalhes inferiores a 100 mícrons.
Ferramentas e matrizes - Corte a laser de ferramentas de moldes. Prototipagem rápida de ferramentas.
Joias e relógios - Perfuração e corte de extrema precisão. Marcação a laser de números de série individuais.
Pesquisa - As universidades usam a manufatura aditiva a laser para estruturas de microrrede, pesquisa de controles, estudos de metalurgia e muito mais.
A gama de aplicações comerciais e de pesquisa continua a crescer rapidamente graças à flexibilidade e às vantagens da fabricação por feixe elétrico.
O que o futuro reserva para os processos de feixe elétrico?
Vários desenvolvimentos interessantes estão expandindo os recursos de feixe elétrico:
- Sistemas com vários feixes e vários lasers - A utilização de vários feixes aumentará as taxas de construção e aprimorará o controle.
- Lasers ultrarrápidos - Os lasers de picossegundos e femtossegundos oferecem novas possibilidades de processamento de materiais com zonas mínimas afetadas pelo calor.
- Lasers de alta potência - As potências do laser continuam aumentando para dezenas de quilowatts, permitindo taxas de construção mais rápidas, seções mais espessas e componentes maiores. Novos projetos de laser também melhoram a eficiência do plugue de parede.
- Fabricação de híbridos - A combinação da deposição a laser com a usinagem CNC ou outros processos em uma única máquina oferece um novo potencial.
- Novos materiais - Novas ligas de alumínio, ligas de alta entropia, compostos de matriz metálica e outros materiais estão sendo desenvolvidos para aproveitar os atributos da manufatura aditiva.
- Metrologia em processo - Os avanços na detecção de alta velocidade e no controle de loop fechado permitirão a correção em tempo real e a auto-otimização durante as construções.
- Simulação - Como a precisão da simulação continua melhorando, a modelagem e a validação se tornarão mais rápidas e mais confiáveis.
- Integração de sistemas - Uma integração mais estreita dos sistemas de escaneamento, manuseio de pó, pós-processamento, automação e monitoramento de qualidade aumentará a robustez.
A fabricação por feixe elétrico está pronta para um crescimento contínuo e impulsionará inovações em muitos setores tecnológicos. Os recursos exclusivos dos processos de laser, feixe de elétrons e plasma serão aproveitados de novas maneiras ainda não imaginadas. Tempos empolgantes estão por vir!
Perguntas frequentes
Aqui estão algumas perguntas frequentes sobre os processos de fabricação de feixes elétricos:
Que tipos de lasers são usados na fabricação?
Os lasers industriais comuns incluem lasers de fibra, lasers de CO2, lasers de diodo, lasers de disco e lasers de diodo direto. Cada um oferece vantagens diferentes em termos de níveis de potência, qualidade do feixe, comprimentos de onda e custo. É importante combinar o tipo de laser com o material e a aplicação.
Como a manufatura aditiva a laser se compara a outros métodos?
A AM a laser oferece resolução muito alta e excelentes propriedades de material. No entanto, a AM com feixe de elétrons pode ser construída um pouco mais rapidamente e a custos mais baixos. A AM com jato de aglutinante tem os custos mais baixos, mas as propriedades do material são piores. A escolha certa depende da aplicação.
Que tipos de sistemas de feixe de elétrons são usados?
Os sistemas de alto vácuo com filamentos termiônicos ou cátodos de tungstênio geram feixes contínuos e estáveis. Os sistemas de baixo vácuo com cátodos de plasma oferecem feixes pulsados. A potência do feixe varia de apenas alguns quilowatts até cerca de 100 quilowatts para manufatura aditiva.
Como funciona a marcação a laser?
A marcação a laser remove revestimentos de superfície, recoze o material de base ou cria uma mudança de cor por meio de oxidação controlada, carbodização ou mudanças químicas na superfície. Diferentes comprimentos de onda são selecionados com base no material.
Qual a espessura que pode ser cortada ou soldada com lasers e plasma?
Os lasers de fibra podem cortar aço de forma confiável até cerca de 1 polegada de espessura. O corte a plasma pode cortar com muito mais espessura, até cerca de 6 polegadas para aço doce. A profundidade da soldagem a laser é limitada a cerca de 0,25 polegada para penetração total. A soldagem por plasma pode realizar soldas de penetração total em um único passe em aço de 6 a 8 polegadas.
Que tipos de defeitos podem ocorrer com a soldagem a laser?
Os defeitos comuns em soldas a laser incluem porosidade por aprisionamento de gás, rachaduras por encolhimento da solidificação, fusão incompleta, rebaixamento, distorção e respingos. São necessários projeto, fixação, parâmetros e controle adequados da junta.
Quais são as precauções de segurança necessárias para a soldagem por feixe de elétrons?
Os raios X farádicos gerados exigem blindagem adequada. O feixe de alta tensão também precisa ser adequadamente contido. Os operadores e a equipe de manutenção precisam de treinamento especializado para trabalhar com segurança com sistemas de feixe de elétrons.
Como o laser shock peening se compara ao shot peening?
O shock peening a laser transmite tensões de compressão até 6 vezes mais profundas do que o shot peening. Ele também evita a rugosidade da superfície.