Currently, the types of 3D printing metal powder materials include stainless steel powder, mould steel powder, nickel alloy powder, titanium alloy powder, cobalt-chromium alloy powder, aluminium alloy powder and bronze alloy powder.
Metal powder preparation methods can be divided according to the preparation process: reduction, electrolysis, grinding, atomization, etc. The two most advanced powder preparation processes in common use are argon atomization and plasma rotary electrode methods.
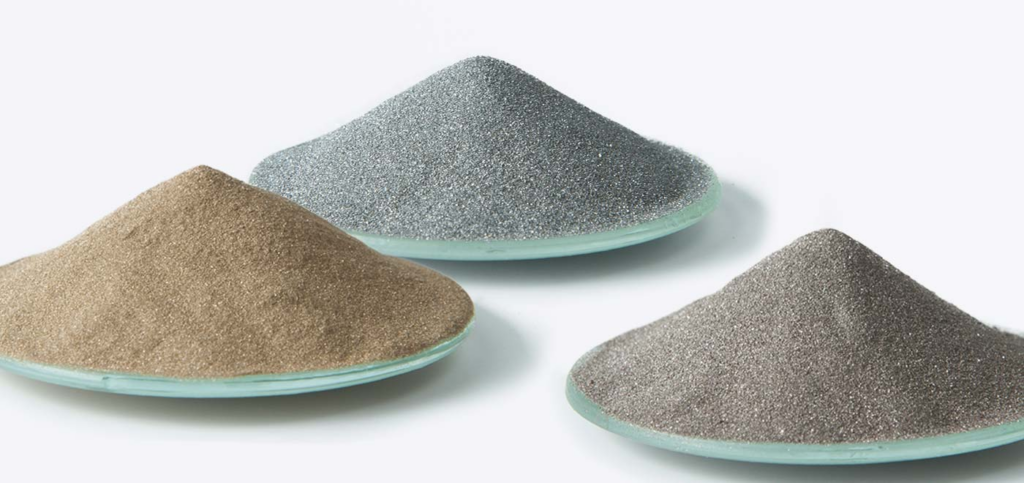
There are several performance indicators for metal powders for 3D printing.
Purity. Ceramic inclusions can significantly reduce the performance of the final part and these inclusions generally have a high melting point, making them difficult to sinter and therefore require a powder free of ceramic inclusions. In addition to this
In addition, the oxygen and nitrogen content also needs to be strictly controlled. Current powder preparation techniques for metal 3D printing are mainly based on atomisation (including aerosolisation and rotating electrode atomisation), where the powder has a large specific surface area and is easily oxidised.
In special applications such as aerospace, the customer In special applications such as aerospace, the customer’s requirements for this index are more stringent, such as high temperature alloy powder oxygen content 0.006% to 0.018%, titanium alloy powder oxygen content of 0.007% to 0.013%, stainless steel powder oxygen content of 0.007% to 0.013%. 0.013%, stainless steel powder oxygen content of 0.010% ~ 0.025% (all for mass fraction). For titanium alloy powders, nitrogen, hydrogen and titanium at high temperature will form TiN and TiH2, reducing the plasticity and toughness of the titanium alloy. This reduces the plasticity and toughness of the titanium alloy. Therefore, the atmosphere should be strictly controlled during powder preparation.
Powder particle size distribution. Different 3D printing machines and forming processes require different powder particle size distributions. The particle size range of powders commonly used in metal 3D printing is 15-53 μm (fine powder), 53-105 μm (coarse powder), which can be relaxed to 105-150 μm (coarse powder) in some cases. The powder size of 15 to 53 μm is used as consumables, and the powder is replenished layer by layer; electron beam is used as the energy source.
The electron beam is used as the energy source for the powder laying type printer, the focus spot is slightly coarser, more suitable for melting coarse powder, suitable for the use of 53 to 105 μm coarse powder as the main; for the coaxial powder feeding type printer can use the powder size of 105 to 150 μm as consumables.
Powder morphology. Powder shape and powder preparation method is closely related, generally from the metal gas or molten liquid into powder, powder particle shape tends to spherical; from the solid state into powder, powder particles are mostly irregular shape; and by the aqueous solution electrolysis method of powder preparation is mostly dendritic. In general, the higher the sphericity, the better the fluidity of the powder particles. 3D printed metal powders require a sphericity of 98% or more, which makes it easier to spread and feed the powder during printing.
powder prepared by all methods, except for the aerosolisation method and the rotating electrode method, are non-spherical. The shape of the powder is non-spherical. Therefore, the aerosolisation method and the rotating electrode method are the main methods for the preparation of high quality 3D printed metal powders.
Powder flow and loose packing density. Powder flow directly affects the uniformity of the powder spread during printing and the stability of the powder feeding process. The powder flowability is related to the powder shape, particle size distribution and bulk density. The fluidity is related to the powder morphology, particle size distribution and bulk density.
The larger the powder particles, the larger the particle size distribution and the density of the powder. The larger the powder particles, the more regular the particle shape and the smaller the proportion of very fine powder in the particle size composition The larger the powder particles, the more regular the particle shape and the smaller the proportion of very fine powder in the particle size composition, the better the mobility. Particle The density remains the same, the relative density increases and the powder mobility increases. Particles The adsorption of water, gases etc. on the surface will reduce the fluidity of the powder. Loose packing density is a unit volume of powder when the powder specimen naturally fills the specified container. The mass of the powder. In general, the coarser the powder size, the higher the bulk density. The coarser the powder, the higher the bulk density. Loose
The effect of apparent density on the density of the final metal printing product is not conclusive. There is no conclusive evidence on the effect of bulk density on the density of the final metal print product, but an increase in bulk density can improve the flow of the powder.