High-entropy alloys (HEA for short) are alloys formed from five or more metals in equal or approximately equal amounts. High entropy alloy powders have broad application prospects as raw materials for the preparation of blocks, coatings, thin-film materials, and other functional materials.
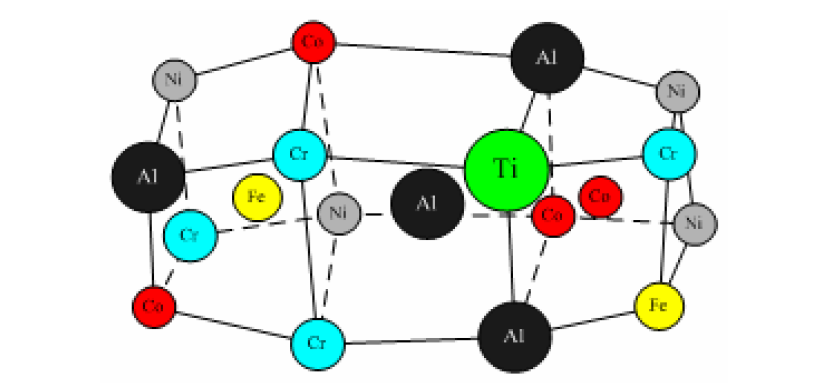
High Entropy Alloy (HEA) alloys are made up of 5 or more elements in equal or near-equal atomic ratios, each containing between 5% and 35% of each element. This concept is a break with the traditional design of alloys based on one or two elements. This concept is a break from the traditional design of alloys based on one or two elements and opens up a whole new path for alloy development.
Ultra-fine high entropy alloy powders with homogeneous structures can not only be used to prepare blocks and coatings but also to replace other high-temperature alloy powders used under special conditions for 3D printing, laser cladding, laser alloying, laser repair, laser quenching, and 3D rapid prototyping technologies, which greatly reduce material losses in machining and achieve low cost and high performance of products. Current The main methods of preparing ultra-fine high entropy alloy powders are mechanical alloying and gas/water atomization.
Mechanical Alloying (MA) is a powder preparation technique in which metal or alloy powders are alloyed in a high energy ball mill through prolonged and intense impact and collision between the powder particles and the grinding balls, resulting in repeated cold welding and fracture of the powder particles, leading to the diffusion of atoms in the powder particles, thus obtaining an alloyed powder.
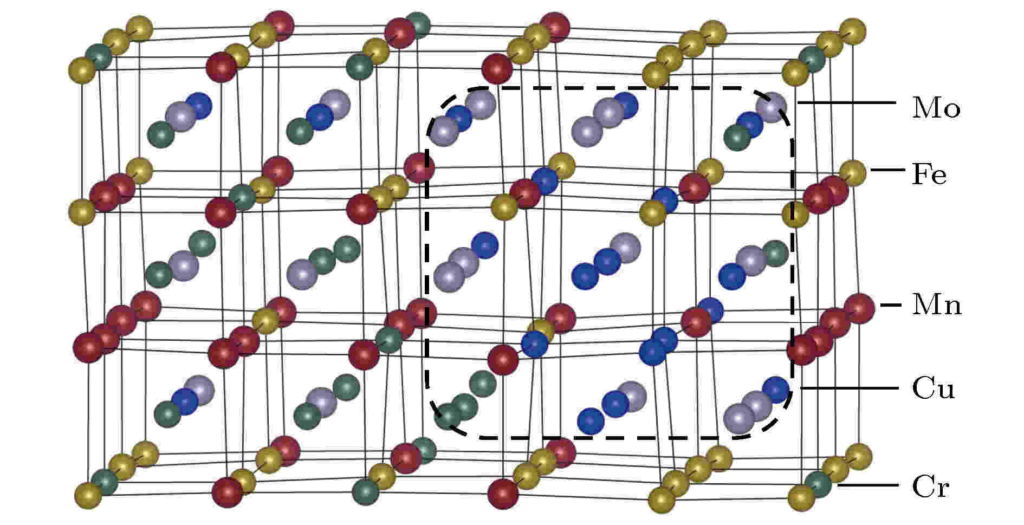
The working principle of the vacuum atomization powder making device is that the metal or metal alloy is melted under vacuum conditions, and under the condition of gas protection, the metal liquid is atomized and broken into a large number of fine metal droplets by the high-pressure airflow through the nozzle in the process of flowing down through the insulated intermediate ladle and guide tube, and the fine droplets are formed into spheres and solidified into particles under the action of surface tension in the flight process to achieve the powder making The fine droplets are formed into spheres and solidified into particles under surface tension during flight to achieve powder production.
The novel properties of high entropy alloy powders, such as superb specific strength, excellent mechanical properties at high temperatures, excellent toughness, and fracture strength at low temperatures, superb magnetic properties, and superconductivity, pave the way for high entropy alloy powders to be used in aerospace, transportation, energy, electronics, biomedical, molds, precision shear tools, and other applications. High entropy alloy powders are used as hydrogen storage materials, radiation protection materials, diffusion barrier layers for electrons, precision shear, electromagnetic shielding materials, thermal spray materials, hard, low coefficient of friction and biological coatings, binders, and soft magnetic and hot spot materials.
With recent advanced developments in powder technology, improvements in printing processes and printed product performance have led to the use of high entropy alloy powders in 3D printing. The rapid solidification of DEDs and PBFs results in superior properties of printed HEA products compared to conventional manufacturing processes, resulting from the grain refinement caused by rapid solidification. 3D printing allows material selection, design, and free fabrication of lightweight materials, individual design, and nano-assembly to be combined. The need for new material development and structural optimization of high entropy alloy powders has facilitated the printing of HEA products that can achieve the complex shapes required for applications in aerospace, energy, molds, tools, and other fields.
High entropy alloy powder materials can be used widely.
High entropy alloy powder materials can be used on the one hand to prepare blocks, coatings, thin-film materials, but also as a substitute for other high-temperature alloy powders used under special conditions for 3D printing, laser cladding, laser alloying, laser repair, laser quenching, and 3D rapid prototyping. laser repair, laser quenching, and three-dimensional rapid prototyping technologies.
The material loss in machining can be greatly reduced, thus realizing the products’ low cost and high performance. On the other hand, nano-high entropy alloy powder materials can also be used as functional materials in catalysis, surface plasmon resonance, electronics, magnetism, energy storage, and high entropy alloy nanomaterials can be used as functional materials in the fields of catalysis, surface plasmon resonance, electronics, magnetics, energy storage, and bio/plasma imaging.
High entropy alloy powders can be used as raw materials for the preparation of blocks, plates, coatings, or films with excellent overall mechanical, physical, and chemical properties. The high entropy alloy powder can be used as a raw material for the preparation of blocks, sheets, coatings, or films. Considering the practicality, processability, and environmental friendliness of high-entropy alloys, they are promising as raw materials for structural and functional materials. The high entropy alloy powders have a wide range of applications as raw materials for the production of structural and functional materials. The high entropy alloys have a great potential for use as raw materials for structural and functional materials.