1. Introduction
Tungsten is a highly versatile and valuable metal that finds application in various industries due to its exceptional properties. However, before tungsten can be effectively utilized, it requires proper preparation to ensure its quality, performance, and reliability. In this article, we will explore the concept of tungsten prep, its importance in different industries, various techniques and tools involved, safety measures, challenges, and future trends. So let’s dive in and discover the world of tungsten prep.
2. What is Tungsten Prep?
Tungsten prep refers to the process of preparing tungsten for its intended applications. Tungsten, also known as wolfram, is a heavy and hard metal with a high melting point and excellent corrosion resistance. To optimize its functionality, tungsten undergoes specific treatments and modifications to enhance its characteristics, remove impurities, and ensure its suitability for various industrial uses.
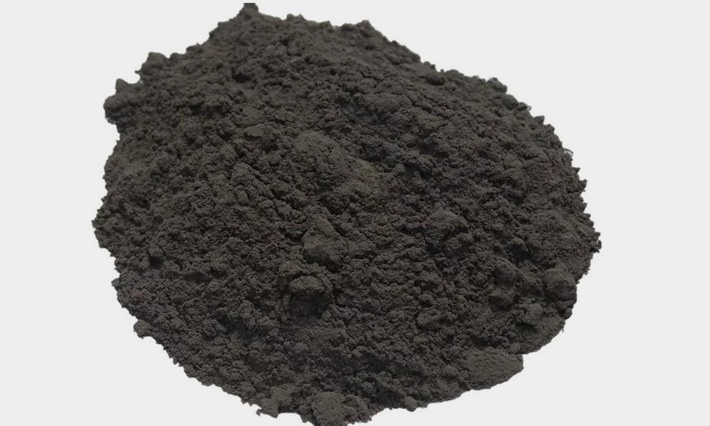
3. Importance of Tungsten Prep in Various Industries
3.1 Aerospace Industry
The aerospace industry heavily relies on tungsten for its exceptional strength, durability, and heat resistance. Tungsten is used in the production of turbine blades, rocket nozzles, and aircraft parts. Effective tungsten prep ensures that these components meet stringent quality standards and can withstand extreme temperatures, pressure, and vibrations.
3.2 Automotive Industry
In the automotive sector, tungsten is utilized in various applications, including piston rings, crankshafts, and ball bearings. Tungsten prep plays a crucial role in improving the wear resistance, hardness, and overall performance of these automotive components, contributing to enhanced engine efficiency and longevity.
3.3 Electronics Industry
The electronics industry benefits greatly from tungsten prep techniques, particularly in the manufacturing of semiconductors, integrated circuits, and electrical contacts. Tungsten’s high conductivity, low coefficient of thermal expansion, and resistance to electromigration make it an ideal material for these electronic components. Proper preparation ensures the purity, cleanliness, and precise deposition of tungsten in microelectronics fabrication processes.
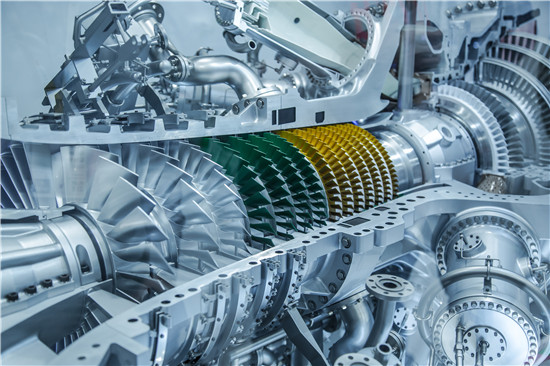
4. Tungsten Prep Techniques
To achieve optimal results in tungsten prep, various techniques are employed depending on the desired application and material properties. The two primary methods are mechanical and chemical.
4.1 Mechanical Methods
Mechanical methods involve processes such as machining, grinding, and polishing. Machining techniques like milling and turning are used to shape and remove excess material from tungsten components. Grinding utilizes abrasive wheels to achieve surface smoothness, while polishing enhances the aesthetics and surface finish.
4.2 Chemical Methods
Chemical methods for tungsten prep involve chemical etching, cleaning, and surface treatments. Acidic or alkaline solutions are utilized to remove impurities, oxides, and contaminants from tungsten surfaces. These chemical processes help improve adhesion, remove residual stress, and enhance the overall surface quality of tungsten components.
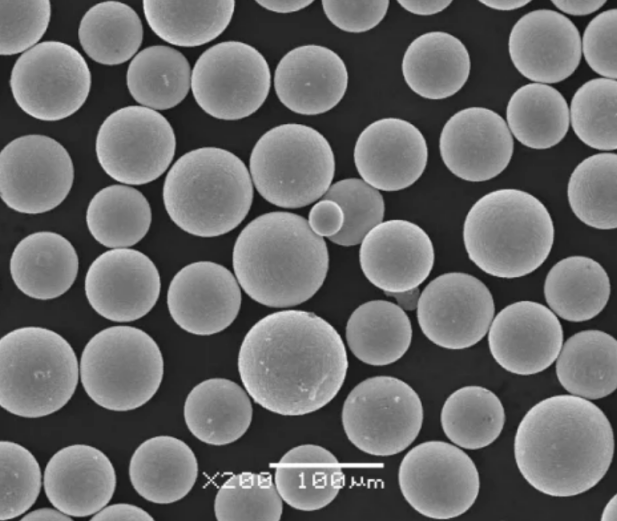
5. Tungsten Prep Tools and Equipment
To carry out tungsten prep effectively, specialized tools and equipment are required. These include:
- Lathe machines for machining and shaping tungsten components.
- Grinding wheels and abrasives for surface grinding and polishing.
- Chemical etchants and cleaning solutions for chemical preparation.
- Ultrasonic cleaners for thorough cleaning of tungsten surfaces.
- Protective gear such as gloves, goggles, and respirators for safety during prep processes.
Investing in high-quality tools and equipment ensures precise and efficient tungsten prep, resulting in superior end products.
6. Tungsten Prep Safety Measures
Safety is of utmost importance during tungsten prep due to the potential health hazards associated with the handling of tungsten and the chemicals used in the process. Some essential safety measures include:
- Adequate ventilation in workspaces to minimize exposure to hazardous fumes.
- Wearing appropriate personal protective equipment (PPE) like gloves, goggles, and respirators.
- Proper storage and handling of chemicals, following safety guidelines.
- Training and awareness programs for employees to understand the risks and preventive measures.
By prioritizing safety, workers can carry out tungsten prep procedures with confidence and minimize any potential risks.
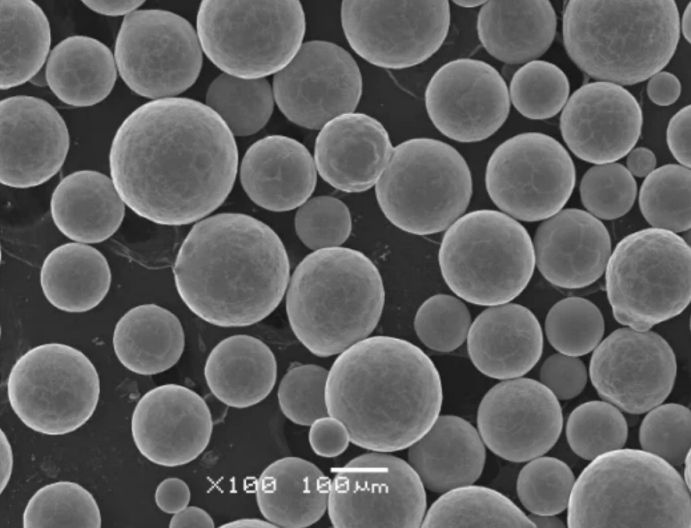
7. Challenges in Tungsten Prep
Tungsten prep is not without its challenges. Some common hurdles include:
- High material hardness, requiring specialized cutting tools and abrasives.
- Tungsten’s brittleness, which can lead to cracking or chipping during machining.
- Chemical reactivity, necessitating careful handling and storage of etchants.
- Surface contamination and oxidation, impacting the quality of tungsten components.
Overcoming these challenges requires expertise, precision, and adherence to best practices in tungsten prep.
8. Tungsten Prep Tips and Best Practices
To achieve optimal results in tungsten prep, consider the following tips and best practices:
- Select the appropriate prep method based on the desired outcome and material characteristics.
- Ensure the tools and equipment used are suitable for tungsten machining and surface treatments.
- Implement proper cooling techniques to prevent overheating during machining.
- Regularly clean and maintain equipment to minimize the risk of contamination or poor performance.
- Adhere to recommended safety measures and guidelines to protect workers and the environment.
- Continuously monitor and evaluate the prep processes to identify areas for improvement.
By following these tips and best practices, the efficiency, accuracy, and quality of tungsten prep can be significantly enhanced.
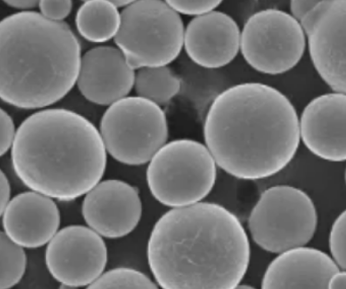
9. Tungsten Prep Cost Considerations
The cost of tungsten prep can vary depending on several factors, including the complexity of the prep process, the volume of tungsten being treated, and the required precision and quality standards. It is essential to consider these cost factors while determining the overall budget for tungsten prep, balancing the expenses with the desired end product’s performance and reliability.
10. Future Trends in Tungsten Prep
The field of tungsten prep continues to evolve, driven by technological advancements and industry demands. Some future trends to watch out for include:
- Development of advanced machining techniques for better precision and efficiency.
- Introduction of innovative surface treatment methods to enhance tungsten’s properties.
- Integration of automation and robotics for increased productivity and consistency.
- Advancements in non-destructive testing techniques to ensure the quality of tungsten components.
- Exploration of sustainable and eco-friendly prep processes to minimize environmental impact.
As these trends unfold, the future of tungsten prep looks promising, with improved capabilities and novel applications on the horizon.
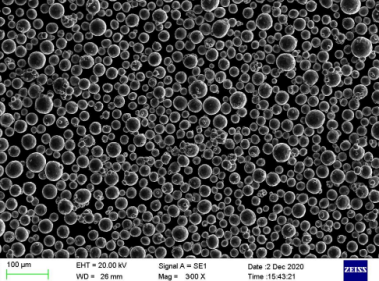
11. Conclusion
Tungsten prep is a vital process that unlocks the full potential of tungsten in various industries. By effectively preparing tungsten through mechanical and chemical methods, using specialized tools and equipment, adhering to safety measures, and following best practices, industries can harness the exceptional properties of tungsten for enhanced performance, durability, and reliability. As the field of tungsten prep continues to evolve, embracing future trends and advancements will unlock new possibilities and further expand the applications of this remarkable metal.
FAQs
Q1. Is tungsten prep necessary for all tungsten applications?
Yes, tungsten prep is necessary for all tungsten applications. Proper preparation ensures that tungsten meets the required quality standards, performance criteria, and safety regulations. Without adequate prep, tungsten components may suffer from inferior quality, reduced durability, or compromised functionality.
Q2. What are the common safety measures during tungsten prep?
Common safety measures during tungsten prep include:
- Ensuring proper ventilation in workspaces to minimize exposure to fumes.
- Wearing appropriate personal protective equipment (PPE) such as gloves, goggles, and respirators.
- Handling chemicals safely, following guidelines and storing them properly.
- Providing training and awareness programs to employees regarding safety protocols.
Q3. What are the challenges in tungsten prep?
Some common challenges in tungsten prep include:
- Tungsten’s hardness, which requires specialized tools and abrasives.
- Brittleness of tungsten, leading to potential cracking or chipping during machining.
- Chemical reactivity of tungsten, requiring careful handling of etchants and cleaning solutions.
- Surface contamination and oxidation, affecting the quality of tungsten components.
Q4. How can tungsten prep costs be managed effectively?
To manage tungsten prep costs effectively, consider:
- Optimizing the prep process to reduce material waste and maximize efficiency.
- Choosing cost-effective tools, equipment, and chemical solutions without compromising quality.
- Implementing preventive maintenance measures to prolong the lifespan of machinery.
- Evaluating different prep techniques and selecting the most cost-efficient approach.
- Partnering with reputable suppliers who offer competitive pricing and quality materials.
Q5. What are the future trends in tungsten prep?
Future trends in tungsten prep include:
- Development of advanced machining techniques for improved precision and efficiency.
- Introduction of innovative surface treatment methods to enhance tungsten’s properties.
- Integration of automation and robotics for increased productivity and consistency.
- Advancements in non-destructive testing techniques to ensure the quality of tungsten components.
- Exploration of sustainable and eco-friendly prep processes to minimize environmental impact.
These trends signify the continuous growth and innovation in tungsten prep, paving the way for new applications and improved performance.
Remember, the world of tungsten prep is vast and constantly evolving. By understanding its importance, techniques, safety measures, challenges, and future trends, industries can unlock the full potential of tungsten and leverage its remarkable properties for various applications.