Introduction to Hot Isostatic Pressing (HIP) 3D Printing
In recent years, the field of additive manufacturing has seen remarkable advancements, and one such technology making waves is Hot Isostatic Pressing (HIP) 3D printing. This innovative manufacturing technique combines the benefits of traditional 3D printing with the power of hot isostatic pressing, resulting in stronger, denser, and more reliable 3D-printed components.
The Advantages of Hot Isostatic Pressing 3D Printing
Improved Material Properties
One of the key advantages of HIP 3D printing is the significant enhancement of material properties. By subjecting the 3D-printed parts to high temperature and pressure, HIP eliminates internal defects, ensuring a more uniform and robust material structure.
Enhanced Part Density
HIP 3D printing boasts superior part density, which translates to increased mechanical strength and better performance under stress. This is particularly valuable for critical applications in aerospace and engineering.
Elimination of Porosity
Traditional 3D printing methods often suffer from porosity issues, leading to weak spots and reduced functionality of the final product. HIP effectively eliminates porosity, resulting in components with consistent material integrity.
Complex Geometries Made Easy
HIP 3D printing allows for the creation of intricate and complex geometries that are challenging or impossible to achieve through conventional manufacturing techniques. This opens up new possibilities in design and engineering.
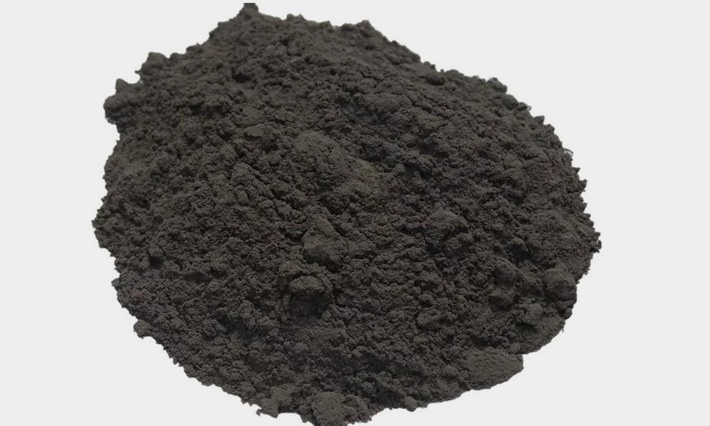
How Hot Isostatic Pressing 3D Printing Works
To understand the process behind HIP 3D printing, let’s delve into its essential steps:
Powder Bed Preparation
The process begins with a powder bed containing the chosen material. This powder bed is spread layer by layer to form the basis of the 3D-printed object.
Application of High Temperature and Pressure
The prepared powder bed is then subjected to high temperature and pressure within a HIP chamber. This combination of heat and pressure helps to consolidate the powder particles and eliminate any internal voids or defects.
Cooling and Densification
After the high-pressure treatment, the object is slowly cooled down while maintaining the pressure. This cooling and densification phase further strengthens the material structure, resulting in a fully consolidated and dense part.
Materials Used in HIP 3D Printing
HIP 3D printing is compatible with various materials, broadening its range of applications:
Metals and Alloys
Metallic materials, such as titanium, stainless steel, and aluminum, are commonly used in HIP 3D printing due to their excellent mechanical properties.
Ceramics
Ceramic materials are popular for their high-temperature resistance and electrical insulating properties, making them ideal for applications in harsh environments.
Composites
Composites, which combine the strengths of different materials, offer unique advantages for specific applications, such as aerospace components.
Applications of HIP 3D Printing
The versatility of HIP 3D printing has led to its adoption in various industries:
Aerospace Industry
HIP 3D-printed components find extensive use in the aerospace sector, where lightweight, durable, and high-performance parts are essential for aircraft and spacecraft.
Medical Implants
The medical field benefits greatly from HIP 3D printing, with the ability to create patient-specific implants that offer better fit and functionality.
Oil and Gas Components
In the oil and gas industry, HIP 3D printing is employed to produce components that withstand the harsh conditions of drilling and exploration.
Tooling and Molds
HIP 3D printing helps create tooling and molds with intricate geometries, enhancing the efficiency and quality of manufacturing processes.
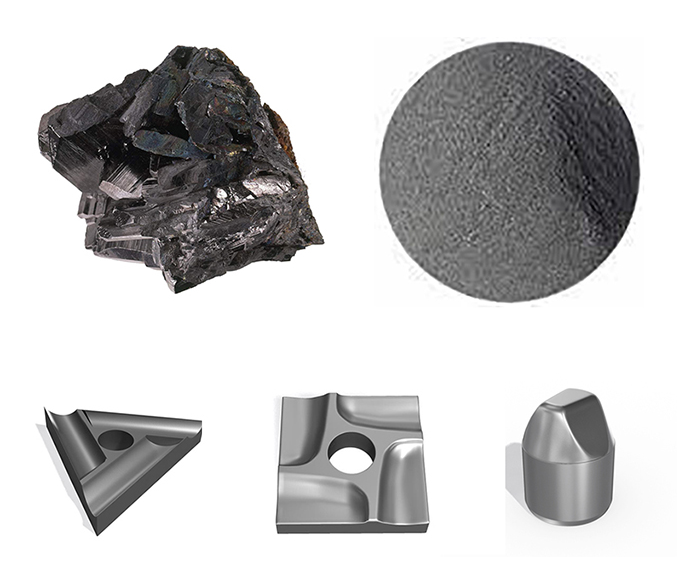
A Comparison Between HIP 3D Printing and Traditional 3D Printing Techniques
To fully appreciate the advantages of HIP 3D printing, it is essential to compare it with traditional 3D printing methods:
Strength and Durability
While traditional 3D printing offers convenience and rapid prototyping, HIP 3D printing excels in producing parts with superior strength and durability. This makes HIP more suitable for demanding applications in engineering and heavy industries.
Surface Finish
In terms of surface finish, traditional 3D printing may exhibit visible layer lines and roughness, especially in large-scale parts. HIP 3D printing, on the other hand, produces smoother surfaces due to its densification process, reducing the need for additional post-processing.
Production Speed
Traditional 3D printing is generally faster in producing prototypes and small-scale objects due to its layer-by-layer deposition. In contrast, HIP 3D printing involves additional steps of pressurization and cooling, making it relatively slower. However, the trade-off lies in the quality and strength of the final product.
Challenges and Limitations of HIP 3D Printing
As with any technology, HIP 3D printing also faces certain challenges and limitations:
Cost of Equipment and Materials
The initial investment in HIP equipment can be substantial, making it a considerable barrier for smaller manufacturers or startups. Additionally, some high-performance materials used in HIP 3D printing can be costly, further impacting the overall production cost.
Size Limitations
HIP chambers have size limitations, restricting the maximum dimensions of 3D-printed objects. Larger components may require multiple prints and subsequent assembly, which could affect the overall integrity of the final product.
Design Complexity Constraints
While HIP 3D printing is excellent for intricate geometries, certain designs may present challenges, leading to potential weak points or difficulties in the densification process. Iterative design improvements are necessary to optimize complex structures for HIP.
Future Developments in Hot Isostatic Pressing 3D Printing
The future of HIP 3D printing is promising, with ongoing research and development aiming to overcome current limitations and expand its capabilities:
Advancements in Materials
Researchers are actively exploring new materials with improved properties for HIP 3D printing. The development of innovative alloys, ceramics, and composites will open new horizons for the technology.
Increased Production Scale
Advancements in HIP equipment and processes may lead to the ability to produce larger and more complex objects. This will widen the scope of applications in various industries.
Integration with Other Manufacturing Processes
The integration of HIP 3D printing with other manufacturing techniques, such as CNC machining or injection molding, could result in hybrid processes that combine the strengths of each method, further enhancing the versatility of the technology.
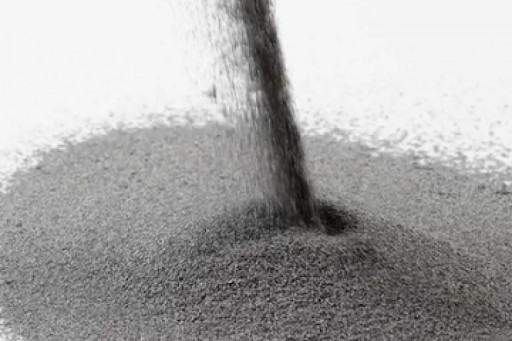
Real-world Examples of HIP 3D Printing Success Stories
To illustrate the impact of HIP 3D printing, let’s explore some notable success stories:
GE’s Aviation Engine Components
General Electric (GE) has adopted HIP 3D printing to produce critical engine components, such as turbine blades and fuel nozzles. The use of HIP ensures the highest level of performance and safety in their aviation engines.
Medical Implants by DiSanto Technology
DiSanto Technology leverages HIP 3D printing to create customized medical implants tailored to each patient’s unique anatomy. This approach improves patient outcomes and accelerates recovery times.
Environmental Impact and Sustainability Considerations
The sustainable aspects of HIP 3D printing are becoming increasingly relevant in today’s environmentally conscious world:
Reduced Material Waste
HIP 3D printing generates less material waste compared to subtractive manufacturing methods, where excess material is cut away. The near-net-shape production approach minimizes material consumption.
Energy Efficiency
With the ability to produce complex parts in a single build, HIP 3D printing can be more energy-efficient than traditional manufacturing methods, where multiple processes are often required.
Recycling and Reusability
HIP 3D printing encourages recycling and reusing materials, reducing the overall environmental impact. Leftover or rejected prints can often be recycled back into the powder supply for future use.
The Future of Manufacturing with HIP 3D Printing
The widespread adoption of HIP 3D printing is likely to revolutionize various industries:
Potential Disruption in Industries
The introduction of HIP 3D printing may disrupt traditional supply chains and manufacturing processes, leading to more localized and agile production.
Adoption and Acceptance
As the technology becomes more accessible and cost-effective, the adoption of HIP 3D printing is expected to rise across industries, accelerating innovation and customization.
Customization and Personalization
HIP 3D printing’s ability to create personalized and bespoke components will revolutionize industries like healthcare and consumer goods, where tailored products are increasingly in demand.
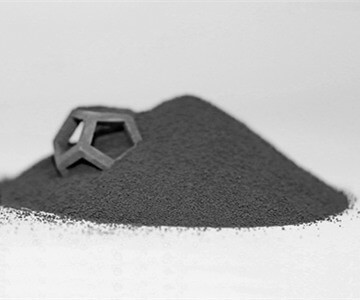
Conclusion
Hot Isostatic Pressing 3D printing represents a significant advancement in additive manufacturing technology. Its ability to enhance material properties, eliminate porosity, and produce complex geometries has positioned it as a valuable tool for various industries, from aerospace to medical applications. While facing some challenges, ongoing research and development are poised to overcome these obstacles and unlock new possibilities for the future of manufacturing. As HIP 3D printing continues to evolve, we can expect to witness further advancements, expanding its reach and transforming how we create and use objects in the world around us.
FAQs
What is the main advantage of HIP 3D printing over traditional methods?
HIP 3D printing offers superior material properties and densification, resulting in stronger and more reliable components compared to traditional 3D printing techniques.
Can HIP 3D printing be used with non-metallic materials?
Yes, HIP 3D printing can work with a variety of materials, including metals, ceramics, and composites, making it suitable for a wide range of applications.
How does HIP 3D printing contribute to sustainable manufacturing?
HIP 3D printing reduces material waste, encourages recycling, and can be more energy-efficient compared to traditional manufacturing processes, contributing to a more sustainable approach to production.
Are there any size limitations for objects produced with HIP 3D printing?
Yes, HIP chambers have size limitations, and larger objects may require multiple prints and subsequent assembly. However, ongoing developments aim to increase the production scale of HIP 3D printing.
What industries are benefitting the most from HIP 3D printing?
The aerospace industry, medical field, oil and gas sector, and tooling and mold manufacturing are among the industries benefiting the most from the advantages of HIP 3D printing.