Introduction
Additive manufacturing, also known as 3D printing, has revolutionized the way products are designed and manufactured. slm working principle is a powerful and widely used additive manufacturing technique that allows the creation of complex and functional parts. In this article, we will delve into the slm working principle, its advantages and limitations, and explore its various applications across industries.
What is slm working principle?
Definition of SLM
SLM is an additive manufacturing technique that involves the selective melting of metal powders using a high-powered laser. It is a powder-bed fusion process where the material is built layer by layer to create a three-dimensional object. The process enables the production of intricate and customized parts that would be challenging or impossible to achieve using traditional manufacturing methods.
Brief history and development
The concept of SLM can be traced back to the 1990s when researchers began experimenting with laser-based powder fusion methods. Over the years, advancements in laser technology, materials, and process control have significantly improved the capabilities of SLM, making it a key player in the additive manufacturing landscape.
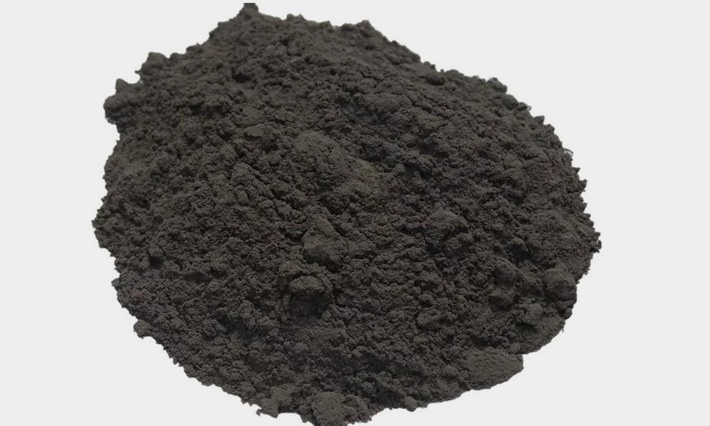
Understanding the Working Principle of SLM
SLM is based on the principle of localized laser melting of metal powders. The process involves several key stages that work together to create a solid object from a digital design.
Additive manufacturing process
The core principle of SLM is the additive nature of the manufacturing process. Unlike subtractive manufacturing, where material is removed from a solid block, additive manufacturing builds up the material layer by layer. This approach minimizes material waste and allows for complex geometries.
The role of lasers in SLM
Lasers play a pivotal role in SLM, providing the energy needed to melt and fuse the metal powders together. The laser selectively scans and melts the powder bed based on the digital design’s specifications, solidifying the material and forming a solid layer.
SLM Process Step by Step
The SLM process can be broken down into several distinct stages:
Pre-processing stage
The first step in SLM involves preparing the digital model of the object to be manufactured. Computer-Aided Design (CAD) software is used to create a 3D model, which is then sliced into thin cross-sectional layers. These slices serve as the blueprint for the manufacturing process.
Powder deposition
In the powder deposition stage, a thin layer of metal powder is evenly spread across the build platform. The layer thickness is precisely controlled to ensure accurate results.
Laser scanning
Once the powder is in place, the high-powered laser starts scanning the surface, tracing the pattern of the first layer. The laser parameters, such as power, speed, and focus, are carefully adjusted to achieve the desired melting and bonding.
Solidification and bonding
As the laser scans the surface, it selectively melts and fuses the metal powder particles, creating a solid layer. This layer adheres to the previous layer, gradually building up the final object.
Post-processing stage
After the printing process is complete, the manufactured part undergoes post-processing, which may include removing excess powder, heat treatment, surface finishing, and inspection for quality control.
Materials Used in SLM
SLM is compatible with a wide range of materials, offering versatility in terms of the final product’s properties and applications.
Metals and alloys
One of the primary materials used in SLM is metal powder, including stainless steel, titanium, aluminum, and nickel-based alloys. These materials are chosen for their strength, durability, and heat resistance, making them suitable for various industrial applications.
Polymers
In addition to metals, SLM can also work with polymer powders, enabling the production of lightweight and flexible parts. Polymers find applications in areas such as healthcare, aerospace, and consumer goods.
Ceramics
SLM has also shown promise in printing ceramic materials. Ceramic parts manufactured through SLM can exhibit excellent thermal and electrical properties, making them useful in electronics and high-temperature applications.
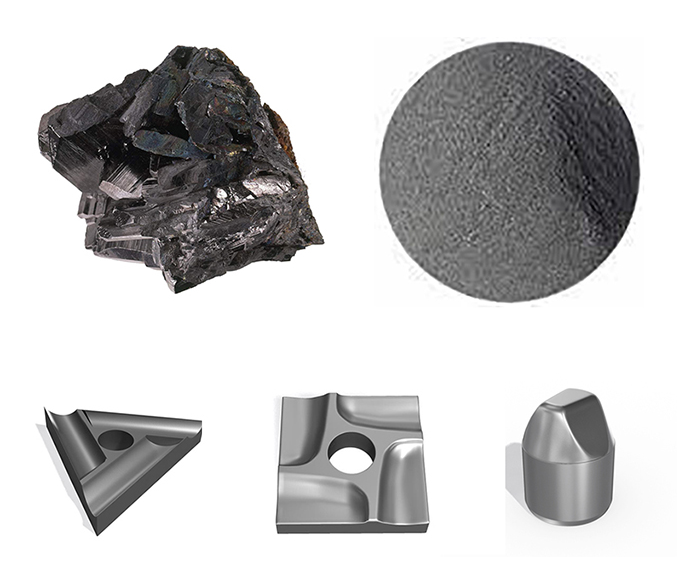
Advantages of SLM
SLM offers several advantages that have contributed to its widespread adoption across industries.
Complex geometries
One of the key advantages of SLM is its ability to produce complex geometries with internal structures that would be challenging or impossible to achieve using traditional manufacturing methods. This capability opens up new design possibilities for engineers and designers.
Reduced material waste
Traditional manufacturing methods often result in significant material waste due to the need for subtractive processes. SLM, being an additive technique, significantly reduces material waste, making it more environmentally friendly and cost-effective.
Rapid prototyping
SLM enables rapid prototyping, allowing designers to quickly iterate and test their designs before mass production. This speed of development accelerates the overall product development cycle.
Customization and personalization
The additive nature of SLM makes it well-suited for producing customized and personalized parts. This is especially valuable in fields like medicine, where patient-specific implants and prosthetics can be created with precision.
Materials diversity
The wide range of materials that can be used in SLM opens up possibilities for various industries. From metals to polymers to ceramics, each material brings its own set of unique properties, expanding the potential applications of the technology.
Limitations of SLM
Despite its many advantages, SLM also has some limitations that need to be considered.
Limited size capabilities
The size of the objects that can be produced using SLM is limited by the build chamber’s dimensions and the capabilities of the equipment. Large-scale manufacturing of certain objects may not be feasible with current SLM technology.
Surface finish and porosity
SLM parts can sometimes exhibit rough surface finishes and porosity, especially in larger and complex parts. Post-processing techniques may be required to improve the surface quality.
Residual stresses
The rapid heating and cooling during the SLM process can result in residual stresses within the manufactured part. Managing these stresses is critical to ensuring the part’s mechanical properties and long-term performance.
Cost considerations
While SLM offers numerous advantages, the equipment, materials, and post-processing costs can be higher than traditional manufacturing methods, making it more suitable for small-scale production or specialized applications.
Applications of SLM
Despite its limitations, SLM has found extensive applications across various industries, revolutionizing the way certain products are manufactured.
Aerospace industry
The aerospace sector has been quick to adopt SLM due to its ability to produce lightweight and complex components. SLM is used to manufacture critical parts like turbine blades, fuel nozzles, and structural components, where weight reduction and performance optimization are essential.
Medical and dental field
In the medical and dental field, SLM has made significant strides in the production of customized implants, prosthetics, and dental crowns. The ability to create patient-specific parts has improved treatment outcomes and patient satisfaction.
Automotive sector
In the automotive industry, SLM is utilized to produce high-performance components like engine parts, exhaust systems, and lightweight structural elements. SLM’s ability to optimize designs for specific applications helps enhance overall vehicle performance.
Tooling and manufacturing
SLM is also used for creating complex tooling and molds for manufacturing processes. The rapid prototyping capability of SLM enables designers to validate and refine tool designs quickly.
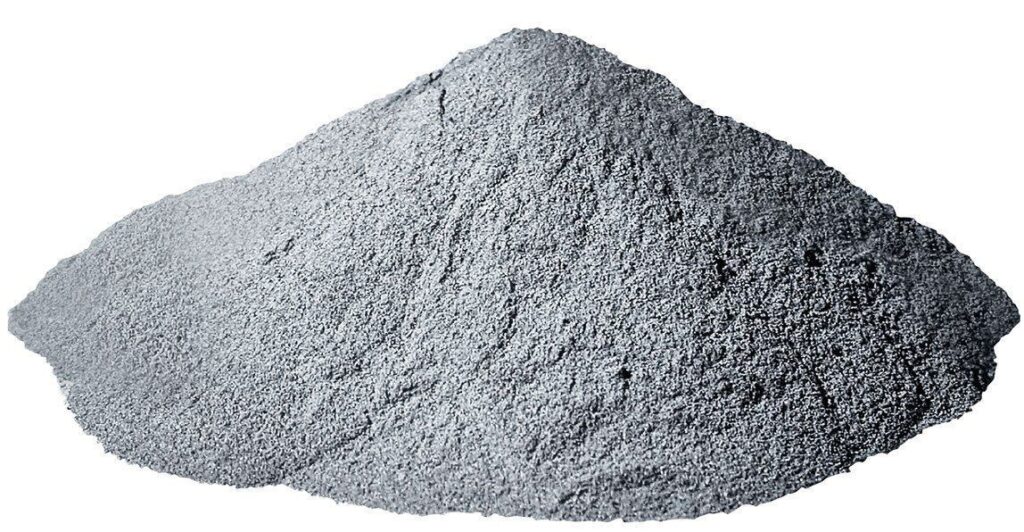
Future Trends in SLM
As technology advances, the potential for SLM continues to expand. Several trends are shaping the future of SLM.
Improved materials
Research and development efforts are focused on enhancing the properties of materials used in SLM. This includes developing new metal alloys, polymers, and ceramics with improved strength, thermal resistance, and biocompatibility.
Enhanced process control
To overcome current limitations, there is a push to improve process control in SLM. Advanced monitoring and sensing technologies are being integrated into SLM systems to ensure more precise and reliable outcomes.
Integration with other technologies
SLM is likely to merge with other manufacturing technologies, such as robotics and AI, to create more automated and efficient production systems. This integration will streamline the manufacturing process and lead to higher productivity.
Conclusion
Selective Laser Melting (SLM) has emerged as a game-changer in the field of additive manufacturing. By harnessing the power of lasers to selectively melt metal powders, SLM enables the creation of intricate, customized, and functional parts. Its applications span across industries, from aerospace and automotive to medical and tooling.
While SLM offers many advantages, it also comes with certain limitations, such as size constraints, surface finish issues, and cost considerations. However, ongoing research and technological advancements are steadily addressing these challenges.
As SLM continues to evolve, it is poised to play an even more significant role in reshaping the manufacturing landscape. With improved materials, better process control, and integration with other cutting-edge technologies, the future of SLM looks promising, offering endless possibilities for innovation and design.
FAQs
- What is SLM in 3D printing?
SLM stands for Selective Laser Melting, a 3D printing technique that uses a high-powered laser to selectively melt metal powders and build up a three-dimensional object layer by layer.
- What materials can be used in SLM?
SLM can work with a variety of materials, including metals, alloys, polymers, and ceramics.
- What are the advantages of SLM?
Some advantages of SLM include the ability to produce complex geometries, reduced material waste, rapid prototyping, customization options, and the diversity of materials available.
- What are the limitations of SLM?
SLM has limitations in terms of the size of objects that can be produced, surface finish and porosity issues, residual stresses, and higher costs compared to traditional manufacturing methods.
- How is SLM being used in the aerospace industry?
In the aerospace industry, SLM is used to manufacture lightweight and complex components like turbine blades, fuel nozzles, and structural elements to improve performance and fuel efficiency.