aluminum alloy 7075 powder is a strong, hard, lightweight material that has been widely used in aerospace, military vehicles and equipment, marine applications, molds, tools, and high-stress structural parts. Here are some of the key functions and applications of 7075 aluminum alloy:
Strength and Hardness
One of the primary reasons aluminum alloy 7075 powder is used so extensively is its high strength-to-weight ratio. It has excellent strength properties, while still remaining lightweight. 7075 has a tensile strength of 83,000 psi and a yield strength of 73,000 psi in the T6 temper.
This strength comes from alloying elements like zinc, magnesium, and copper which form precipitates that strengthen the aluminum matrix. The T6 heat treatment further enhances strength by forming fine precipitates. The combination of alloying and heat treatment make aluminum alloy 7075 powder significantly stronger than other popular aluminum alloys like 6061.
In addition to high strength, aluminum alloy 7075 powder also has good hardness which provides wear resistance. The typical Brinell hardness is around 150. This hardness comes from those same precipitates that provide strength. This combination of strength and hardness make 7075 suitable for parts that experience high stresses, vibration, impact, or wear.
Toughness and Fatigue Resistance
In addition to being strong and hard, 7075 also retains good toughness and fatigue resistance compared to other high-strength aluminum alloys. This comes from careful control of alloying elements like zinc and magnesium. Too much of these elements can reduce ductility and fracture toughness. But at optimal levels, 7075 is able to achieve 40% elongation and 25% reduction of area in a tensile test.
The toughness and ability to withstand impacts make aluminum alloy 7075 powder a good choice for forgings like aircraft bulkheads that experience fatigue loads. The alloy can be used for high cycle fatigue applications. Proper heat treatment is important to achieving optimal toughness and fatigue resistance.
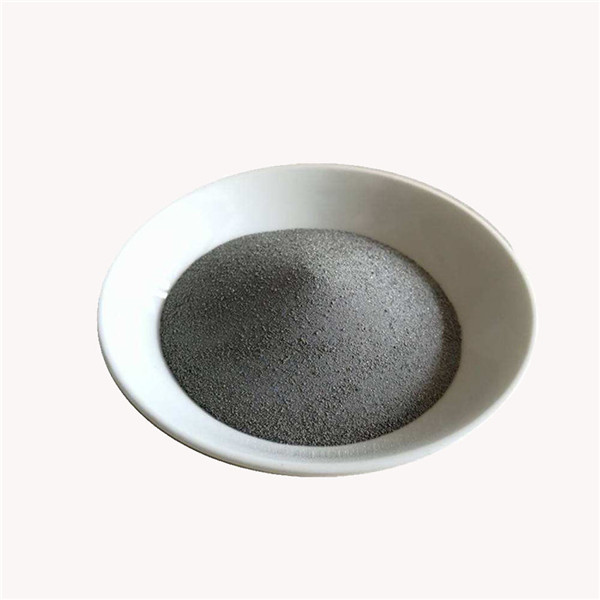
Corrosion Resistance of aluminum alloy 7075 powder
While not as corrosion resistant as some other aluminum alloys, aluminum alloy 7075 powder still provides good resistance to general corrosion in most environments. This comes from the high zinc content which improves corrosion resistance.
In the T6 temper, it is somewhat susceptible to stress corrosion cracking. But in the T73 temper, stress corrosion resistance is improved. Adding chromate conversion coatings or anodizing also improves corrosion protection. Overall, the corrosion resistance of 7075 is sufficient for most applications.
Machinability
7075 has relatively good machinability for a high-strength aluminum alloy, although not as good as softer alloys like 6061. Tools wear faster than with softer alloys, but aluminum alloy 7075 powder produces chips that break readily. This allows it to be machined using high speed mills and lathes. Depth of cut should be lower than with other alloys. Coolants and lubricants should always be used to maximize tool life.
The alloy’s strength does present some challenges with machining. Work hardening needs to be minimized by using sharp cutting tools, avoiding excessive speeds/feeds, and taking light finishing cuts. Annealed aluminum alloy 7075 powder offers improved machinability if the slightly lower strength is acceptable.
Weldability
The weldability of aluminum alloy 7075 powder is considered poor compared to other aluminum alloys. Issues like solidification cracking can occur while welding 7075. The high zinc content causes the liquid metal to shrink considerably during solidification, increasing hot cracking susceptibility.
Special filler rods like 5356 are used to improve weldability. Precautions like preheating, maintaining interpass temperature, and post weld heat treatment need to be exercised. Friction stir welding offers better results than fusion welding methods. Overall, welding of aluminum alloy 7075 powder requires care, but sound welds are possible using proper procedures.
Formability
aluminum alloy 7075 powder has relatively low formability compared to other aluminum alloys, as you might expect given its high strength. In the peak aged T6 temper, it has poor forming properties. Annealing the alloy prior to forming improves ductility and bendability.
For complex shapes, a W temper or O temper with maximum forming characteristics may be used prior to final heat treatment. Things like drawing, bending, flanging, and crimping can be done in properly annealed or overaged tempers. Stretching and deep drawing response is fair. Alloys like 5052 and 3003 are better choices when formability is critical.
Availability and Cost
aluminum alloy 7075 powder is widely available from major aluminum suppliers in a range of product forms like sheet, plate, bar, rod, tube, and wire. Various tempers are available, but T651 and T7351 plate and sheet are the most common.
As an aerospace grade aluminum, 7075 does have a higher cost than more general purpose alloys. But it’s not prohibitively expensive, especially for the improved strength and performance it provides. Its extensive use in aircraft means demand is high and availability good.
Key Applications
Some of the most common applications that take advantage of aluminum alloy 7075 powder properties include:
- Aircraft structures – Used extensively in airframe components like wings, skins, ribs, and bulkheads where strength and low weight are critical.
- Aerospace parts – Used for highly stressed parts in launch vehicles and spacecraft like fuselage sections, cryogenic tanks, thrust structures.
- Military vehicles – Used in critical structural parts for vehicles like trucks, helicopters, ships, and submarines. Provides strength at lower weight.
- Molds and tooling – Provides good balance of strength, hardness, and machinability for prototyping molds and durable tooling applications.
- Marine applications – Popular for boat and ship components like hulls, superstructures, masts, and rigging where corrosion resistance is also important.
- Bicycles – Often used for high-end bicycle frames and components where low weight and good fatigue resistance are desired.
- Automotive parts – Used in some critical engine and drivetrain components and racing applications.
- Recreation products – Used in products like archery equipment, ski and hiking poles, and gear where strength and low weight are priorities.
So in summary, aluminum alloy 7075 powder provides an exceptional combination of high strength, good toughness and fatigue resistance, hardness and wear properties, adequate corrosion resistance, and reasonable machinability and formability that make it ideal for highly stressed structural applications where low weight is critical. Its high cost is offset by the performance benefits it provides in aerospace, military, marine, and other demanding applications.
Chemical Composition
The typical chemical composition of aluminum alloy 7075 powder is:
- Aluminum: 87.1 to 91.4%
- Zinc: 5.1 to 6.1%
- Magnesium: 2.1 to 2.9%
- Copper: 1.2 to 2.0%
- Iron: Max 0.5%
- Silicon: Max 0.4%
- Manganese: Max 0.3%
- Chromium: 0.18 to 0.28%
- Other elements (total): Max 0.15%
Key alloying elements like zinc, magnesium, and copper primarily contribute to strength through precipitation hardening. Chromium improves stress corrosion cracking resistance. Iron, silicon, and manganese are present as impurities. The ratios of the major alloying elements as well as limits on impurities are carefully controlled to ensure optimal properties in the alloy.
Mechanical Properties
The typical mechanical properties of aluminum alloy 7075 powder in the T6 temper are:
- Tensile Strength: 83,000 psi
- Yield Strength: 73,000 psi
- Elongation: 11%
- Reduction of Area: 15%
- Hardness: 150 Brinell
- Modulus of Elasticity: 10,200 ksi
- Shear Strength: 48,000 psi
- Fatigue Strength: 28,000 psi
Properties vary some based on product form and exact temper. But you can see the exceptional strength properties, while still retaining reasonable ductility and toughness for an alloy this strong. Keep in mind mechanical properties decline at elevated temperatures.
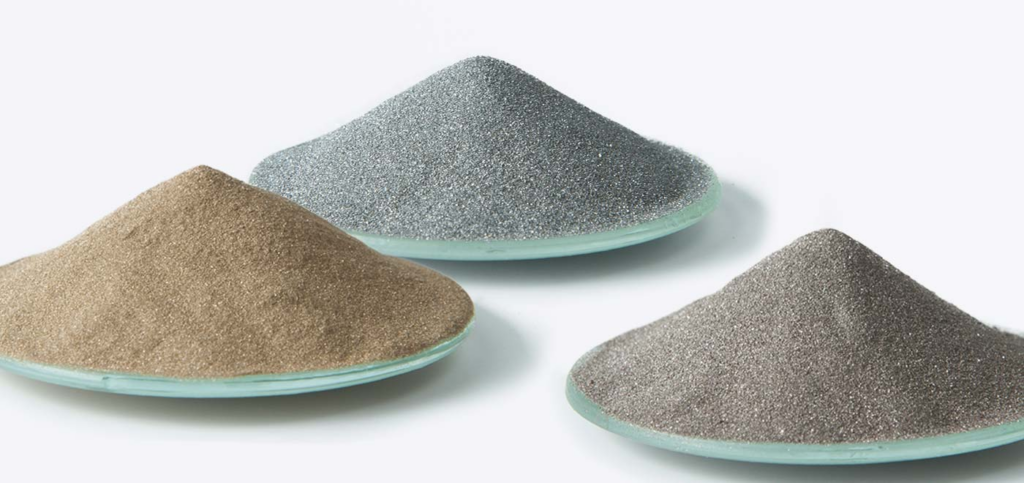
Heat Treatment
A key step in achieving optimal properties in aluminum alloy 7075 powder is heat treatment, usually done in the T6 temper. The main heat treatment steps include:
1. Solution heat treatment – The alloy is heated to a temperature of 875-885°F and held for 1-2 hours. This takes the alloy into the single phase region and dissolves soluble particles.
2. Quenching – After heating, the alloy is rapidly cooled or quenched, usually in water. This produces a supersaturated solid solution.
3. Aging – The alloy is then aged at 250-350°F for times ranging from 4-36 hours depending on desired strength. Age hardening precipitates form during this step.
4. Stretching – A 2-5% strength stretch is commonly performed after aging to straighten the material and provide some dislocation hardening.
The T6 temper provides optimal strength. Underaged T7 tempers trade some strength for improved toughness. Overaged T73 tempers improve corrosion resistance and formability at a lower strength level.
Microstructure
The microstructure of aluminum alloy 7075 powder consists of:
- An aluminum rich matrix – This forms the bulk of the microstructure and gives the alloy its lightweight character. The actual grains are fairly coarse.
- Intermetallic precipitates – Particles containing strengthening solutes like MgZn2, Al2CuMg, Al2Cu form during heat treatment and provide considerable precipitation hardening.
- Dispersoid particles – Finer particles containing manganese help control grain structure and recrystallization during hot working and heat treatment.
- Alpha phase particles – Coarser insoluble particles with iron and silicon improve high temperature properties but lower fracture toughness.
The interaction between the ductile matrix and dispersed hardening particles gives the alloy its unique combination of strength, hardness, and toughness. Careful control of precipitates through alloying and heat treatment is key.
Effects of Alloying Elements
The major alloying elements in aluminum alloy 7075 powder serve the following key functions:
- Zinc – The primary alloying addition, zinc forms strengthening precipitates and improves strength substantially. It also assists in precipitation hardening and improves fatigue strength. Higher levels reduce corrosion resistance slightly.
- Magnesium – Magnesium also provides substantial precipitation hardening through particles like MgZn2. It increases strength with minimal decrease in corrosion resistance. Improves hardness and mechanical properties at elevated temperatures.
- Copper – Copper increases strength through precipitation of Al2CuMg particles. Also improves machinability by making chips more brittle. However, excessive copper reduces fracture toughness.
- Chromium – Added in small amounts, chromium forms particles that mitigate stress corrosion cracking. Provides resistance to pitting corrosion. Has a slight strengthening effect.
- Iron – Present as an impurity, iron reduces fracture toughness and ductility in high amounts. Contributes to greater heat treat response. Lower limits are desirable.
Alternate Designations and Grades
Given its extensive use in the aerospace industry, aluminum alloy 7075 powder also goes by a number of alternate aircraft aluminum designations and grades including:
- Aluminum 7075-T6
- Aluminum 7075-T651
- Aluminum 7075-T7351
- AA7075-T6
- AA 7075-T651
- Alclad 7075-T6
- AMS 4045
- AMS 4130
- AMS 7010
- AMS 7090
- QQ-A-225/9
- MIL-A-7075
- UNS A97075
- ALCOA 7075-T6
The 7075 dash number indicates the aluminum alloy, while the second number denotes the temper. T6 and T651 are the most common tempers, providing optimal strength. There are slight compositional differences between some specifications.
Forms and Finishes Available
aluminum alloy 7075 powder is available from suppliers in a wide variety of product forms, shapes, and finishes including:
- Sheet – Available in thicknesses from 0.025 inches to 6 inches. Stock widths up to 49 inches.
- Plate – Available in thicknesses up to 10 inches. Can be cut into bar, strip, and other shapes.
- Rod – Diameters from 0.125 to 10 inches. Simple round sections.
- Bar – Rectangular bar in a range of sizes. Also square, hex, and oval bars.
- Tube – Seamless or welded tube in diameters from 0.125 to 12 inches with variety of wall thicknesses.
- Wire – Available in spooled wire form in different diameter and spool sizes.
- Extrusions – Available as extrusions in angles, channels, tee shapes, tubes, and other special profiles.
- Castings – Available as sand, investment, and permanent mold castings.
- Forgings – Can be forged into complex shapes with improved strength properties.
Common finishes include mill finish, anodized, painted, powder coated, lacquered, and chemical conversion coatings.
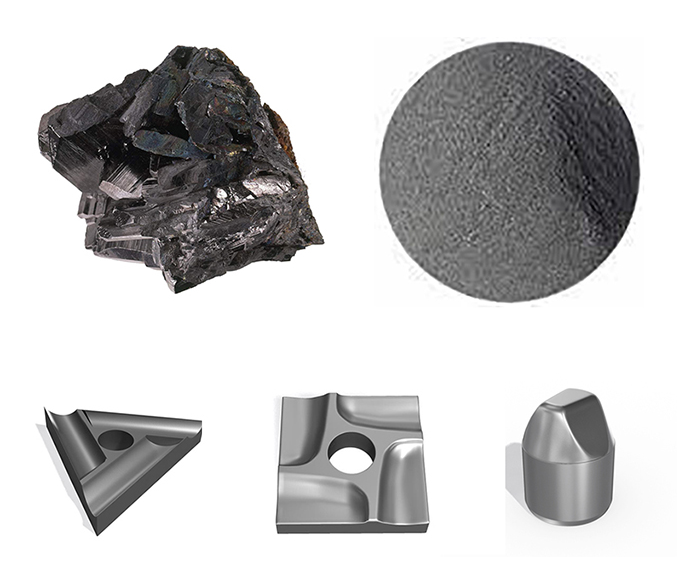
Cost and Availability
aluminum alloy 7075 powder has good availability through major suppliers of aluminum products and metals service centers. Lead times vary from around 1-4 weeks for common sizes and forms. Made globally but especially well represented by US producers.
Pricing can vary based on alloy temper, form, size, quantity ordered, and other factors. Some approximate costs:
- Sheet/plate: $6-12 per pound
- Bar: $4-15 per pound
- Tube: $6-20 per pound
- Wire: $5-15 per pound
As an aerospace grade alloy, aluminum alloy 7075 powder does come at a premium cost compared to more standard alloys like 6061 and 7050 aluminum. However, it provides mechanical properties that justify the additional cost for demanding applications.
FAQs
Here are some commonly asked questions about aluminum alloy 7075 powder:
Q: What are the main differences between 7075-T6 and 7075-T651 aluminum?
A: The T6 vs T651 temper designations both refer to a peak-aged temper. The only difference is that T651 material is stress relieved by stretching. This helps to straighten any residual stresses from quenching but has minimal effect on overall mechanical properties.
Q: Is aluminum alloy 7075 powder weldable?
A: Yes, 7075 can be welded but it is more difficult and crack-prone than softer alloys like 5XXX and 6XXX series aluminum. Precautions like choosing the proper filler metal, preheating, and postweld heat treatment are necessary to obtain sound welds. Friction stir welding generally gives better results.
Q: What thickness is 7075 aluminum available in?
A: In sheet form, 7075 can be obtained in thicknesses ranging from 0.025 inches to 6 inches. Plate is available up to 10 inches thick, and bar/rod up to 10 inches in diameter. So 7075 is readily available in thick sections suitable for structural applications.
Q: Can you machine aluminum alloy 7075 powder-T6 aluminum?
A: Yes, 7075-T6 can be machined using conventional or CNC machine tools, but care must be taken because of its high strength and hardness. Slow speeds, light depths of cut, sharp tools, and coolant are recommended. Annealed tempers machine more easily if required.
Q: Is 7075 aluminum used in aircraft?
A: Yes, aluminum alloy 7075 powder is used extensively in aircraft. It is commonly found in structural parts like fuselage skins, ribs, bulkheads, wings, and empennage components where low weight plus high strength are critical. Its good fatigue resistance is also important for aircraft design.
Q: What corrosion protection is used on 7075 aluminum?
A: 7075 relies on its natural surface oxide for corrosion resistance. Added protection like anodizing, chromate conversion coatings, powder coating, or paint are sometimes applied depending on the service environment. Cladding with a more corrosion resistant alloy is also used for some applications.
Q: What welding process is used for 7075 aluminum?
A: Gas tungsten arc welding (GTAW) and gas metal arc welding (GMAW) are most common for welding 7075, using filler metals like 5356. Friction stir welding can also be used. Precautions should be taken to minimize hot cracking. Postweld heat treatment helps strengthen the weld.
Q: Can you anneal 7075 aluminum?
A: Yes, 7075 aluminum can be annealed to improve ductility and formability in the O or W tempers. A typical anneal involves heating to 415°C for 1-3 hours followed by slow cooling. Annealing restores some ductility but sacrifices strength – the alloy will need to be re-aged after forming to regain its high strength.
Q: Is 7075-T6 aluminum stronger than 6061-T6?
A: Yes, 7075-T6 provides substantially higher strength than 6061-T6 aluminum. 7075 has a tensile strength of around 83,000 psi compared to 45,000 psi for 6061, almost double the strength. The higher zinc and copper content in 7075 creates more strengthening precipitates.
Q: What are some alternatives to 7075 aluminum?
A: Some potential alternatives with similar properties include 2024, 6013, 6061, 7050, and 7150 aluminum for moderate strength applications. 2024, 2324, 2524, 7055, 7175, 7475 for higher strength requirements. 6061, 5005, 5050 for improved corrosion resistance.