Introduction
3D printing technology has revolutionized manufacturing processes across industries, enabling rapid prototyping and production of intricate, lightweight components. One of the most widely used materials in metal 3D printing is aluminum due to its high strength-to-weight ratio, corrosion resistance, excellent thermal and electrical conductivity, and ease of post-processing.
Among the various aluminum alloys, 7050 aluminium alloy powder is gaining popularity for 3D printing applications requiring high strength and moderate toughness. 7050 aluminum contains zinc, magnesium, and copper as its major alloying elements and offers strengths comparable to some steels. This article provides an overview of 7050 aluminum alloy powder and its applications in 3D printing.
Overview of 7050 aluminium alloy powder
The 7050 aluminium alloy powder was initially developed in the 1950s for high-strength aircraft structural applications. It is part of the 7xxx series of aluminum alloys, which are known for their highest strength among all aluminum alloys.
The typical composition of 7050 aluminium alloy powder is:
- Zinc: 6.2%
- Magnesium: 2.3%
- Copper: 2.2%
- Iron: 0.15%
- Silicon: 0.12%
- Manganese: 0.10%
- Chromium: 0.05%
- Zirconium: 0.25%
The main alloying elements, zinc and magnesium, provide strength through precipitation hardening while copper improves corrosion resistance. Zirconium is added for grain structure control.
The key properties of 7050 aluminium alloy powder are:
- High strength – Yield strength of 500 MPa and tensile strength of 570 MPa in T651 temper.
- Good fracture toughness – Around 33 MPa√m in the T7351 temper.
- Excellent fatigue strength – Fatigue strength of about 310 MPa at 107 cycles in the T7351 temper.
- Good corrosion resistance – Due to copper alloying.
- Medium density – Around 2.83 g/cm3.
- Excellent machinability and dimensional stability during heat treatment.
The combination of high strength, good toughness, and moderate density makes 7050 an ideal choice for structural parts and components aimed at weight savings.
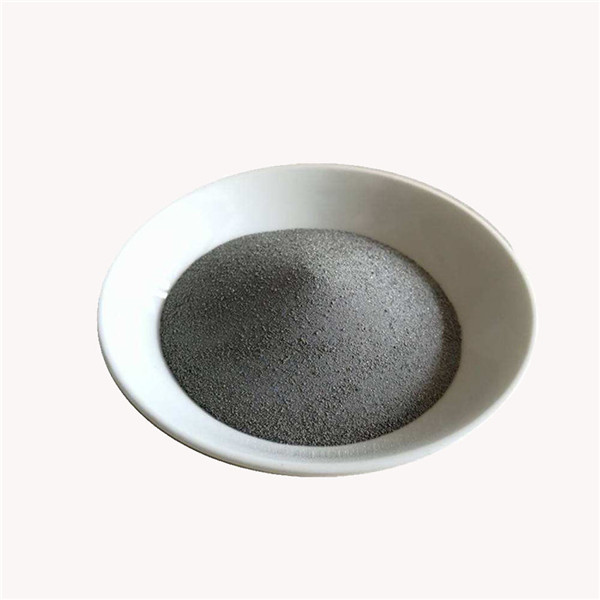
Advantages of 7050 Aluminum Alloy for 3D Printing
The 7050 aluminum alloy offers several benefits that make it suitable for 3D printing applications:
High Strength-to-Weight Ratio
The relatively high strength coupled with medium density results in an excellent strength-to-weight ratio for 7050 aluminum. This allows designing lightweight 3D printed parts with sufficient mechanical properties.
The high strength of 7050 enables 3D printing of components meant to handle high stresses, pressures, and operating loads. At the same time, the lower density compared to steels and titanium alloys results in weight savings.
Good Printability
The 7050 powder particles can be optimally shaped into spherical or near-spherical morphology with proper atomization techniques. This allows smooth flow of the powder and uniform spreading of the powder layers during 3D printing.
The excellent thermal conductivity of aluminum also prevents issues like warping and residual stresses during printing. This results in good printability and dimensional accuracy of printed 7050 aluminium alloy powder parts.
Heat Treatability
The 7050 aluminium alloy powder can be heat treated to achieve desired properties like high strength. Printing in the annealed condition followed by post-print heat treatment allows tailoring the properties as per application requirements.
Solution treatment, quenching, and aging can be used to achieve optimum strength in the T6 and T7 tempers. Cold working between the aging cycles of 7050 can also increase the yield strength beyond 550 MPa.
Corrosion Resistance
The addition of copper provides good corrosion resistance to 7050 aluminum in many structural applications. This avoids the need for specialized coatings in some cases, simplifying the printing and post-processing.
Weldability
7050 aluminium alloy powder has better weldability than many other high-strength 7xxx alloys. This allows welding of 3D printed 7050 parts to each other or to components made using traditional manufacturing, increasing design flexibility.
Friction stir welding and gas tungsten arc welding can be used to join 7050 aluminum without significant loss of base metal properties.
Cost Effectiveness
7050 aluminium alloy powder is more affordable than other high-strength aerospace alloys like titanium. This makes 7050 an economical choice for many industries aiming to reduce weight and material costs.
The good recyclability of aluminum and the ability to reuse scrap powder further improve cost-effectiveness. The buy-to-fly ratio for 3D printed aluminum components can be as low as 1:1.
Applications of 3D Printed 7050 Aluminum Components
The unique properties of the 7050 aluminium alloy powder make it suitable for the following applications:
Aerospace Applications
The aerospace industry is one of the leading adopters of metal 3D printing with aluminum alloys. 7050 aluminum with its high strength, fracture toughness, and fatigue strength can be used to print the following airspace components:
- Structural frames and brackets
- Aircraft seals, ducts, and housings
- Turbine blades, heat exchangers, and powertrain parts
- UAV/drone components like motor mounts and landing gear
3D printing helps make lightweight aerospace parts with optimized designs and complex geometries. GE and Safran use 7050 alloy for printing jet engine parts and achieve 50% weight savings over traditional manufacturing.
Automotive Parts
Aluminum alloys like 7050 can replace heavy steel components in automobiles and help light-weighting. Some examples of 3D printed automotive parts using 7050 aluminum include:
- Chassis, powertrain, and suspension components like control arms
- Wheel rims
- Brake callipers and discs
- Transmission casings and housings
- Heat exchangers and intercoolers
3D printing enables consolidation of multi-part assemblies into single printed components for cars. Ford and Bugatti have tested 3D printed aluminum car parts for racing and production vehicles.
Consumer Electronics
The consumer electronics industry utilizes 3D printing for lightweight, high-strength enclosures, frames, and heat dissipation parts in products like:
- Laptops, mobile phones, tablets, wearables
- Desktop 3D printers and computer hardware
- Gaming consoles and accessories
- High-end audio-video devices
Apple uses 7050 aluminum alloy to make the enclosure of Mac Pro laptops with selective laser sintering 3D printing for maximizing strength and thermal management.
Robotics Components
Various actuators, powertrain parts, joints, mounts, and end effectors in robots can be 3D printed from aluminum alloys for lightweight and high-strength performance under dynamic loads. 7050 aluminium alloy powder is suitable for robotic parts in:
- Industrial robots
- Collaborative robots
- Exoskeletons
- UAVs and drones
- Space robots and rovers
Medical Devices
3D printed surgical instruments, dental implants, prosthetics, medical tooling using 7050 aluminum provide the required strength for load-bearing applications while being biocompatible.
Defense Equipment
Light-weighting military vehicles and equipment like aircraft carriers, tanks, and artillery using 3D printed 7050 components improves mobility. Aluminum armor can also provide protection while saving weight over traditional steel armor.
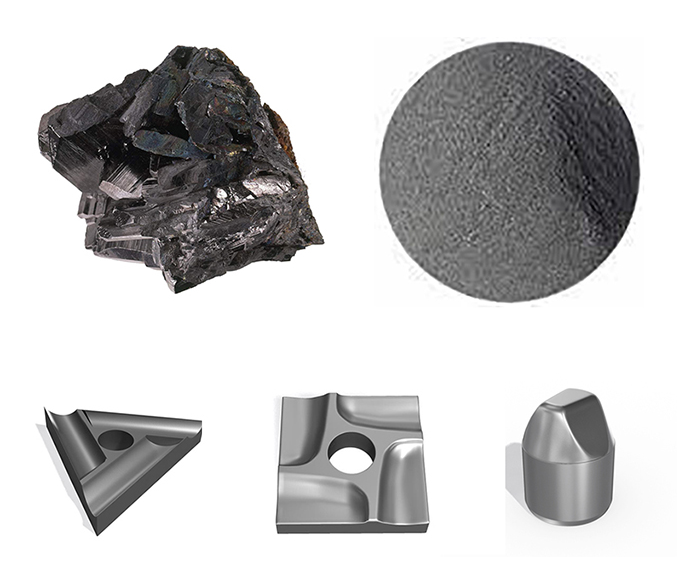
Process Parameters for 3D Printing 7050 Aluminum
The most suitable 3D printing process for aluminum alloys is powder bed fusion, which utilizes a focused heat source like a laser or electron beam to selectively melt and fuse powder particles layer-by-layer.
The different powder bed technologies used for 7050 aluminum are:
- Direct Metal Laser Sintering (DMLS)
- Selective Laser Melting (SLM)
- Electron Beam Melting (EBM)
The typical range of process parameters for 7050 aluminum are:
Laser and Optics
- Laser power: 100-500 W
- Laser scanning speed: 100-1000 mm/s
- Hatch spacing: 0.1-0.2 mm
- Layer thickness: 20-100 μm
Powder Bed
- Powder particle size: 15-45 μm
- Powder bed temperature: Room temperature for SLM/DMLS, 600-850°C for EBM
Inert Atmosphere
- Oxygen content below 0.1% for SLM/DMLS
- Vacuum for EBM
For DMLS/SLM, preheating to just below the melting point, i.e. around 500°C, helps reduce residual stresses. The elevated powder bed temperature in EBM also minimizes stresses.
Part orientation, support structures, and scanning strategies additionally impact residual stresses and print quality. Both SLM and EBM allow rapid printing of dense 7050 aluminum parts with properties close to traditional manufacturing.
Post-Processing of 3D Printed 7050 Aluminum Parts
After printing, the following post-processing steps are typically used:
- Removal from the build plate: Traditional methods like band sawing, cutting, and electrical discharge machining. Minimized for easier part detachment by using interfaces like release layers.
- Support removal: Supports are removed using pliers, cutters, or dissolution in caustic baths.
- Heat treatment: To achieve desired mechanical properties and material microstructure. For 7050, this involves solution treatment, quenching, and aging.
- Surface finishing: Involves removal of surface irregularities using techniques like sand blasting, grinding, linishing, and polishing. Shot peening can also be done to induce compressive stresses.
- Quality inspection: Ensures dimensions, tolerances, and final material properties are as per specified requirements. Testing methods like coordinate metrology, tensile testing, and non-destructive evaluation are used.
- Part certification: Validates aviation part quality to ensure compliance with regulatory standards in the aerospace industry. Dramatically reduces lead time compared to traditional workflows.
Automating post-processing operations improves repeatability and reduces overall part production time. Integration of printing and post-processing into a single machine tool is an emerging trend.
Benefits and Challenges of 7050 Aluminum 3D Printing
Some of the major benefits of 3D printing 7050 aluminum parts include:
- Weight reduction – Reduces weight by over 50% compared to steel parts, improves fuel efficiency
- Cost efficiency – Lower costs compared to titanium alloys, reduced scrap losses
- Part consolidation – Allows complex, optimized geometries, combines assemblies into single parts
- Rapid manufacturing – Significantly shorter lead times, accelerates product development
- High strength – Mechanical properties exceed traditionally manufactured aluminum
- Customization – Facilitates parts with customer-specific design features
- Sustainability – Reuses aluminum powder, relatively environmentally friendly
However, certain challenges need consideration:
- High equipment costs – Printers, powder handling systems require major investments
- Process optimization – Multiple parameters need adjustment for high quality prints
- Material qualifications – Mechanical properties depend on optimized printing process
- Post-processing – Involves multiple steps, time and cost intensive
- Part size limitations – Constrained by printer envelope dimensions
- Surface finish – May require traditional machining or other finishing
Overall, the advantages of lightweight construction, part consolidation, and design flexibility outweigh the challenges highlighted above for most applications.
Future Outlook for 7050 aluminium alloy powder 3D Printing
The use of lightweight, high-strength aluminum alloys is projected to grow exponentially in 3D printing across aviation, automotive, and other industries aiming for lightweight design.
Within aluminum alloys, 7050 will continue to find increasing applications due to its superior strength properties close to steels combined with moderate density. Aluminum alloys are forecast to account for over 25% of the total metal AM parts produced by 2025.
Key trends that will expand adoption of 7050 aluminum 3D printing are:
- Process improvements – Parameter optimization, integrated post-processing, and quality control will enable 3D printing on par with traditional manufacturing.
- Cost reductions – Increased productivity, supply chain improvements, and recycling will lower costs.
- New applications – Innovation across sectors like medical, marine, space, defense, will drive demand for 3D printed aluminum parts.
- Expanded capabilities – Larger build volumes, multi-material printing, and rapid certification will facilitate applications.
- Automation integration – Embedding 3D printing into digital manufacturing ecosystems will improve adoption.
In the long term, 3D printing using 7050 aluminum alloy powder will become a mainstream production technology across several industrial sectors owing to its unique benefits.
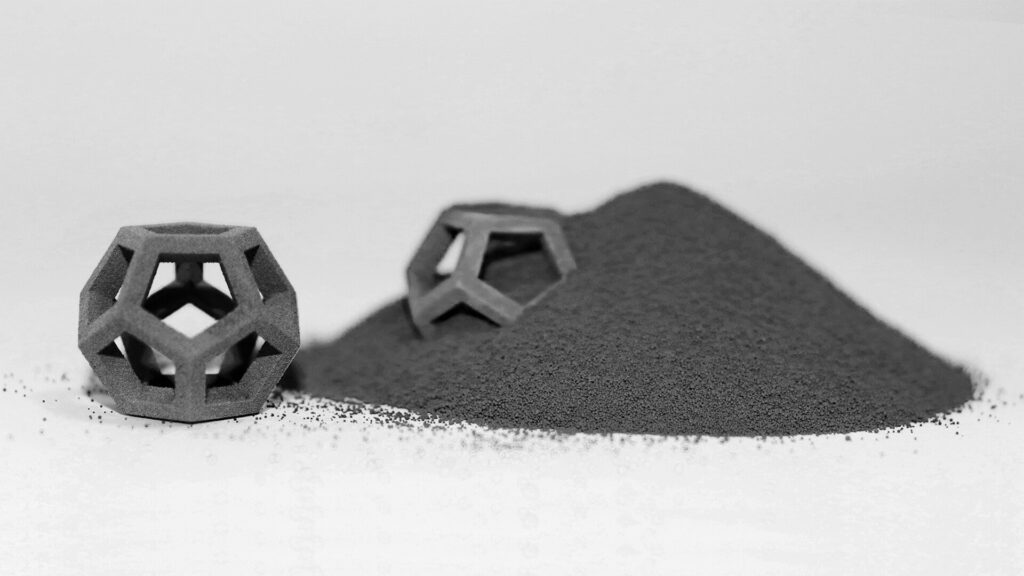
Conclusion
The 7050 aluminum alloy provides an optimal combination of high strength, fracture toughness, weldability, and corrosion resistance required in structural and load-bearing components for aviation, automotive, and other demanding applications.
3D printing using 7050 aluminum powder facilitates complex geometries, lightweight structures, and rapid manufacturing unachievable through traditional techniques. It offers significant opportunities for weight reduction, cost savings, lead time reduction, and design flexibility across multiple industries.
With ongoing improvements in 3D printing processes, material properties, quality standards, and part certification, 7050 aluminum alloy is poised to become a highly valued material for digital manufacturing in the coming years. Its applications will continue rising driven by the motivation for lightweight design across transportation, defense, consumer goods, and industrial sectors.