Among 3D printing technologies, SEBM (Selective electron beam melting) technology allows for fast scanning speeds, no pollution, and high utilization. Spherical metal powders are the key to the application of SEBM technology. As regards the preparation of spherical metal powders, PREP(Plasma Rotating Electrode System) technology can achieve the good spherical and low hollow powder required by SEBM technology. Therefore, in this article, we will discuss the application and characteristics of spherical metal powders made using PREP technology for 3D printing.
SEBM technology is an important method in additive manufacturing with high energy utilization, fast scanning speed, a non-polluting vacuum environment, and high molding efficiency compared to other technologies. It is an effective method for the rapid forming of high-strength stainless steels, titanium alloys, and high-temperature alloys. As a result, this technology has been strongly promoted by experts in additive manufacturing in recent years.
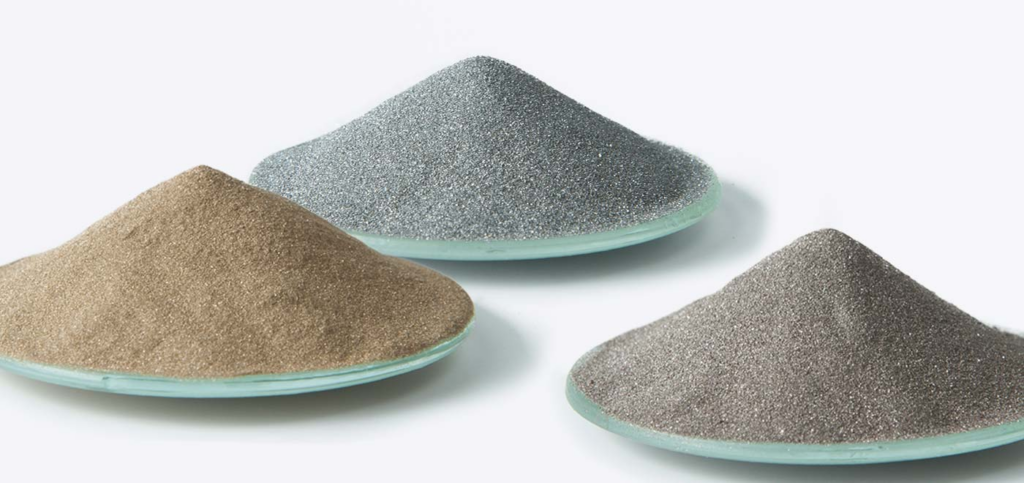
Spherical metal powders are the key raw material for the application of SEBM technology
which requires high sphericity, good flowability, low impurity content, high apparent density and vibrational density, low hollow powder, and a particle size concentration of 45-106μm.
The methods of preparation metal powder have water atomization(WA), gas atomization( GA), plasma atomization( PA), plasma rotating electrode process( PREP), hydride-dihydride(HDH), and so on. Each method of powder preparation has its own characteristics and advantages. However, compared to the powders produced by these processes, the powders produced by the PREP plant better meet the raw material requirements of SEBM technology for metal spherical powders.
The SEBM forming principle is that the 3D CAD model of the part is sliced and layered and the resulting discrete data is fed into the forming system. A preheating process is carried out in the forming system, which reduces the temperature gradient between the powder layers, thereby reducing the residual stresses in the part and reducing the deformation of the formed part. After the preheating process, the electron beam selectively scans and melts the powder pre-layered on the table based on the CAD data for each layer cross-section of the part.
The unmelted powder remains loose and can be used as a support. Once a layer has been machined, the table is lowered by one layer thickness, and the next layer is laid and melted, while the new layer is fused to the previous one. The process is repeated until the part is finished, the part is removed from the vacuum box and the loose powder is blown out using a high-pressure gas from the powder recovery system (PRS) to obtain a 3D part. Throughout the forming process, the formed part remains in the powder bed and undergoes shape-following heat treatment, equivalent to a subsequent annealing heat treatment, which can significantly reduce residual stresses within the part.
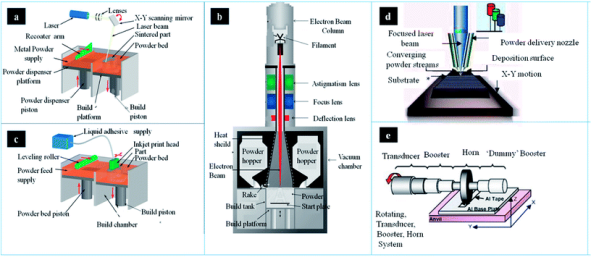
As spherical metal powders play a vital role in SEBM. The indicators for evaluating the quality of the powder usually lie in the following areas.
The particle size distribution of a spherical powder is one of the key indicators of the final formed sample.
Particle size refers to the size of the powder. Particle size distribution refers to the percentage of the volume of different sizes of powder within a certain range. SEBM technology usually requires a concentrated particle size distribution and a particle size range of 45-106 μm.
The chemical composition is the second important indicator of the quality of the powder. the percentage of various elements in the powder. Oxygen content, nitrogen content, etc. is usually an important factor in measuring the quality of a powder.
Sphericity is the third most important indicator of powder quality, and PREP machines typically achieve sphericity of over 90%, a figure that is much higher than that of powders produced using VIGA, EIGA, PA, and PS technology.
The flowability of a powder is expressed in terms of the time it takes for a quantity of powder to flow through a standard funnel of a defined aperture. Flowability is related to sphericity, the better the sphericity, the higher the flowability, and the easier it is to control the spreading of powder during the printing process. As a result, spherical powders have more advantages in this process compared to other forms.
Apparent density is the volume of powder measured after it has been freely filled into a standard container. Vibrational density refers to the mass per unit volume measured after the powder in the container has been vibrated under the specified conditions. The higher the apparent density and vibrating density of the powder the smaller the voids between the powders and the higher the densities of the formed parts. Influence the powder apparent density and vibration density, is the powder particle size powder.
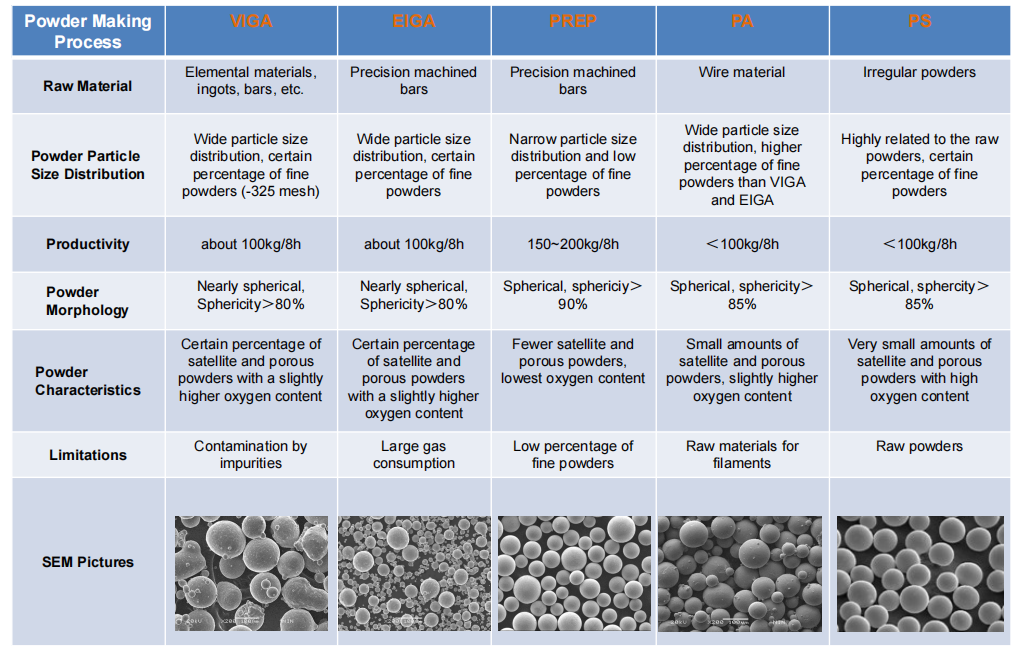
The plasma rotary electrode atomization method uses an electrode or plasma torch as the heat source and a metal or alloy bar as the self-consuming electrode. The bar is rotated at high speed and the molten metal stream on its end face is thrown out by centrifugal force and rapidly cooled in an inert gas to form a metal powder. This method can be used to produce titanium alloys, nickel-based high-temperature alloys, cobalt-based high-temperature alloys, stainless steel, and refractory metal powders. The sphericality of the spherical powder prepared using this technique is over 90%.
Above, we have described some of the features and applications of spherical powders made with PREP equipment in the SEBM technology for 3D printing. We will analyze the application and characteristics of spherical powders in 3D printing again in a subsequent article through the properties and characteristics of specific grades of spherical powders.