316L powder is a common stainless steel powder, because of its excellent corrosion resistance, low-temperature impact resistance and other properties and is widely used in industrial production. The development of additive manufacturing technology and laser cladding technology has also made 316L powder in the additive manufacturing of a wide range of applications, this article will focus on the preparation of 316L powder and the application of the introduction.
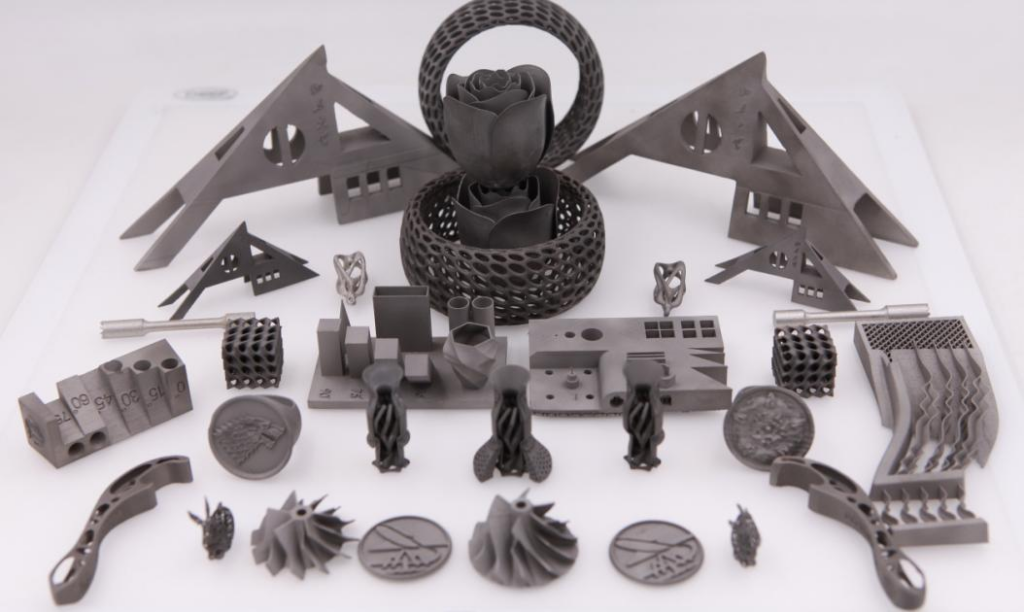
Preparation of 316L Stainless Steel Powder
The following methods of metal powder preparation are commonly used for 3D printing, electrode induction atomization, plasma rotary electrode atomization, plasma periodization, etc.
Electrode induction atomisation (EIGA), due to the use of crucible-free induction melting technology for powder production, effectively ensures the dryness of the raw material and avoids inclusions in the metal powder and pollution problems caused by the melting process.
By adjusting the power and other process parameters, the fine powder yield can reach up to 82% and the powder sphericity up to 99%, which meets the requirements of laser 3D printing on powder particle size; in addition, the EIGA method usually has high efficiency and low energy consumption. In addition, the EIGA method usually has high efficiency and low energy consumption, but the limitation of the induction coil on the size of the electrode restricts the development of large diameter electrode material atomization technology, while the bias of the electrode during melting will to a certain extent cause uneven alloy powder composition, and the “umbrella effect” during powder preparation will lead to a wider overall particle size distribution of the powder, and the particles have more The “satellite powder”, shaped powder and hollow powder, which in turn leads to a decrease in powder fluidity, loose packing density and low density of vibration, in addition, the EIGA method of powder preparation also generally exists easy to bond, high porosity, and other problems.
The rotating electrode method uses a metal or alloy as a self-consuming electrode, the end surfaces of which are heated by an electric arc and melt into a liquid, which is thrown out and crushed into fine droplets by the centrifugal force of the electrode rotating at high speed. The PREP method is based on the formation of spherical particles due to surface tension in an inert atmosphere at high speeds.
The spheroidisation method is mainly used to spheroidise irregular powders produced by crushing and Physico-chemical methods and is one of the most effective means of obtaining dense spherical particles. The principle is to use a high temperature, high energy density heat source (plasma), the powder particles quickly heated melting, and under the action of its surface tension condensed into spherical droplets, into the cooling chamber after rapid cooling to obtain a spherical powder.
Currently, the spheroidisation process is divided into two main types: radio frequency ion spheroidisation and laser spheroidisation. Due to the agglomeration of the initial powder, the spheroidal powder will be melted during the spheroidisation process, resulting in an increase in the particle size of the prepared spherical metal powder.
The powder prepared by plasma spheroidization method is mostly near-spherical, no hollow spherical powder in the powder but a small amount of fine “satellite powder” adhered to the surface, slightly poor flowability, the powder particle size is mainly distributed in 20.7 ~ 45.4μm, fine powder yield up to 60% ~ 70%, suitable for mass production of powder; but due to the use of silk atomization usually, However, as the powder is usually made by atomization of the wire, the raw material is required to have good processing properties, which restricts the preparation of hard-to-deform alloy powder, and the cost is high.
PA method is more used in the radio frequency plasma spheroidization method (RFP), can be irregular powder particles by carrying gas through the charging gun sprayed into the plasma torch, high temperature plasma so that the powder quickly absorb heat melting, in the role of surface tension to form spherical droplets, and in a very short period of time suddenly cold solidification, and finally achieve the shaped powder “plastic The final result is the “shaping” of the heterogeneous powder to obtain a spherical powder. The use of the RFP method to prepare spherical powder usually has the advantages of simple process, fine powder size, high sphericity, high purity, good flowability, etc., but the spherical powder usually requires secondary sieving, the efficiency needs to be improved. Currently, the spheroidisation of Ti, Cu, Ni, W, Ta, Mo, and other metal powders has been successfully achieved.
Application of 316L Stainless Steel Powder
316L and 304L are the most commonly used austenitic stainless steel powders, are excellent structural materials with good overall mechanical properties and a wide range of applications. 316L has superior corrosion resistance and has a large number of applications in aviation, machinery, petrochemical, food, kitchen, and bathroom, medical, jewelry, construction and electrical industries, etc. The Mo content makes the steel grade have excellent resistance to pitting and can be safely It is safe for use in environments containing halogen ions such as Cl-. Stainless steel powders are widely used in sintered parts, porous materials, injection moulded precision parts, sprayed materials, 3D printing, composite materials, metal coatings etc. depending on particle size and morphology. Suitable for PM press sintering, MIM metal injection moulding, HIP hot isostatic pressing, AM additive manufacturing and many other processes…