Titanium is a strong, lightweight metal that is used in a variety of applications such as aerospace, medical implants, sports equipment, jewelry, and more. TC4 titanium, also known as Grade 5 titanium alloy or Ti-6Al-4V, is one of the most commonly used titanium alloys and accounts for more than 50% of total titanium usage.
Overview of TC4 Titanium
TC4 titanium gets its name from its composition – it contains 6% aluminum, 4% vanadium, 0.25% (maximum) iron, and 0.2% (maximum) oxygen with the remainder being titanium. The addition of aluminum and vanadium stabilizes the titanium crystal structure to strengthen the alloy while maintaining titanium’s excellent corrosion resistance.
TC4 titanium offers an excellent combination of high strength, low weight, corrosion resistance, fracture toughness, and biocompatibility. Some key properties and characteristics of TC4 titanium alloy include:
- High strength-to-weight ratio – TC4 titanium has excellent strength comparable to steel alloys but with a density of only 4.43 g/cm3, nearly half that of steel. This makes it ideal for applications where low weight is critical.
- Corrosion resistance – With the ability to form a passive oxide film on its surface, TC4 titanium exhibits excellent resistance to corrosion and can be used without protective coatings in many environments.
- Biocompatibility – TC4 titanium has low toxicity and good acceptance by the human body making it widely used for surgical implants and medical devices.
- Heat treatability – The microstructure and properties of TC4 titanium can be altered through heat treatment and annealing to tailor it for different applications.
- Weldability – TC4 titanium has relatively good weldability for a titanium alloy allowing the creation of complex shapes and assemblies.
- High fracture toughness – TC4 titanium exhibits good crack propagation resistance and fracture toughness.
Some drawbacks of TC4 titanium include relatively poor elongation, low hardenability, and high reactivity with elements like oxygen, nitrogen, and hydrogen at elevated temperatures. Overall, its versatility and balance of mechanical properties make TC4 an excellent engineering material for demanding applications.
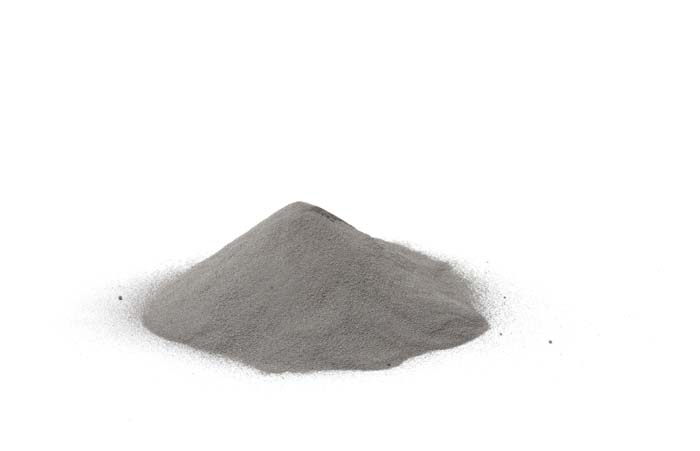
Applications of TC4 Titanium
The unique properties of TC4 titanium make it suitable for use across a diverse range of industries and applications including:
Aerospace Applications
The aerospace industry was the initial driver for the development of titanium alloys. TC4 became the most extensively used titanium alloy in aircraft structures. Its high strength, low density, excellent corrosion resistance, and ability to withstand high temperatures make it an ideal choice for:
- Aircraft structural components – Landing gear, engine components, firewalls, hydraulic tubing, wings, fuselages, fasteners, etc.
- Spacecraft – Structural supports, tanks, thrusters, tubing for rockets and satellites.
- Missiles – Structural casings, fasteners, liquid propellant tanks.
- Helicopters – Rotor hubs, drive shafts, exhaust ducts, engine parts.
In aircraft, every 1 kg of weight reduced from the structure can save up to $1000 per year in fuel costs over the lifetime of the plane. TC4 titanium allows designing lightweight, reliable structures to improve fuel efficiency.
Biomedical Applications
TC4 titanium is one of the most widely used metals for surgical implants in the human body. Its biocompatibility, corrosion resistance, and mechanical properties make it well suited for:
- Orthopedic implants – Joint replacements like hip, knee, and shoulder implants; bone plates, screws, and pins for fractures.
- Dental implants – Roots, crowns, abutments, and wire.
- Cardiovascular stents – Supporting heart valves and blood vessels.
- Surgical instruments – Forceps, retractors, and scissors.
- Body piercing jewelry – Nose, eyebrow, lip, and navel piercings.
- Implantable medical devices – Pacemaker casings, bone growth stimulators, insulin pumps.
Titanium implants avoid stress shielding effects, integrate well with bone, and do not degrade inside the body. TC4’s biocompatibility minimizes the risk of inflammation and rejection.
Chemical Processing Industry
The chemical industry leverages TC4 titanium’s excellent corrosion resistance for:
- Heat exchangers, condensers, and tubing for carrying highly corrosive fluids. The passive oxide layer allows it to withstand even acidic environments.
- Storage tanks and process vessels for reactive chemicals like chlorine.
- Valves, pumps, and pipes for handling corrosive liquids.
- Lining of steel tanks and structures to protect from corrosion.
Marine Applications
In marine environments, TC4 titanium performs well due to its corrosion resistance in saltwater along with strength retention at low temperatures. It is commonly used in:
- Propellers, drive shafts, rudders, and pump impellers.
- Seawater piping systems.
- Heat exchangers for desalination plants and offshore oil platforms.
- Components for subsea vehicles, offshore rigs, and pipelines.
Automotive Uses
The automotive industry utilizes TC4 titanium to reduce weight and improve performance including applications such as:
- Connecting rods, intake valves, valve springs, and rocker arms in racing engines and high-performance sports cars.
- Exhaust systems – Manifolds, mufflers, tailpipes, clamps and hangers.
- Wheels, axles, drive shafts, and chassis components.
- Luxury vehicle trim parts like grilles, badges, and decorative hardware.
Other Uses
Some other common applications of TC4 titanium include:
- Sports equipment – Golf club heads, tennis rackets, bicycle frames, hockey sticks, lacrosse sticks, etc.
- Consumer products – Eyeglass frames, watches, jewelry, backpacks, mobile cases.
- Power generation – Condenser tubing for nuclear, geothermal, and solar electricity generation.
- Desalination – Heat exchangers, piping, pump impellers.
- Architecture – Decorative cladding, panels, roofs for buildings.
- Food processing – Tanks, valves, tubing, pumps for food manufacturing.
- Petrochemical – Crackers, distillation columns, heat exchangers.
Production of TC4 Titanium
TC4 titanium is created by adding aluminum and vanadium to refined titanium metal in a tightly controlled melting process. It is challenging to manufacture because of titanium’s high reactivity at elevated temperatures. Some key steps in producing TC4 titanium alloy include:
Melting and Alloying
- Pure titanium ingots are loaded into a vacuum induction melting furnace along with pieces of aluminum and vanadium master alloy.
- The charge is repeatedly melted and poured into a water-cooled copper crucible to allow thorough mixing and dissolve oxygen.
- The melting is done under vacuum or in an inert argon atmosphere to prevent contamination.
- The molten alloy is cast into ingots or directly fed into processes like hot rolling.
Hot Working
- The TC4 ingots are preheated and processed through multiple hot rolling passes to break down the cast structure.
- Hot rolling reduces the thickness of the metal and forms plate, sheet, and bar stock while improving mechanical properties.
- Forging or extrusion can also be used to produce more complex TC4 titanium shapes.
Heat Treatment
- Solution treatment involves heating TC4 alloy to just below the beta transus temperature to form a uniform phase, followed by rapid cooling or quenching.
- Aging treatment then reheats the alloy to a lower temperature to allow fine precipitates to form which strengthen the material.
- The combination of solution and aging can significantly enhance the strength, hardness, and creep resistance.
Machining and Finishing
- TC4 titanium is very difficult to machine because of its low thermal conductivity, chemical reactivity, and tendency to work harden.
- Slow speeds, specialized tooling, abundant cooling, and careful process control are required for machining operations like milling, drilling, boring, and turning.
- Abrasive waterjet cutting and EDM are common non-traditional machining processes used for TC4 parts.
- Various surface finishing processes like grinding, linishing, anodizing, pickling, and passivation may be used to improve surface quality.
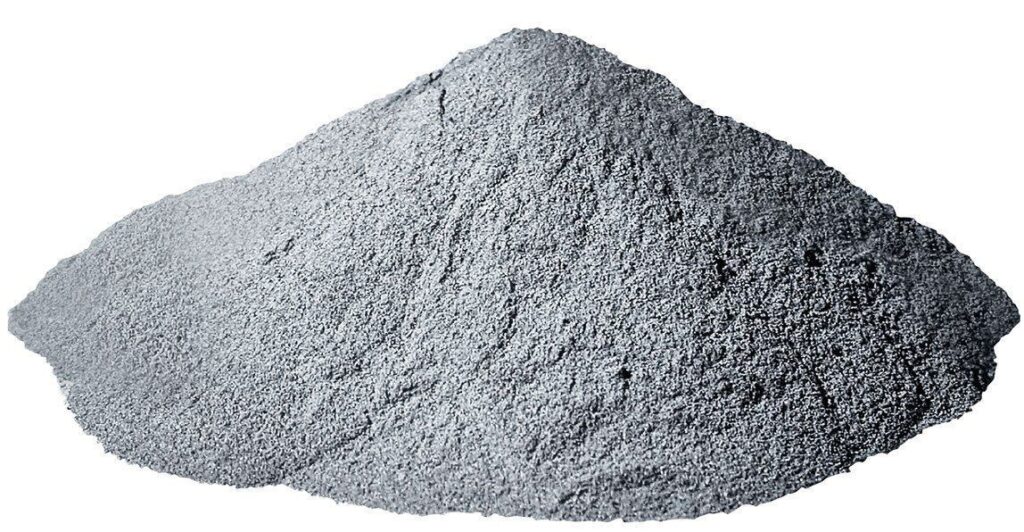
Properties of TC4 vs Commercially Pure Titanium
TC4 titanium has higher strength than commercially pure titanium grades, but slightly reduced ductility and toughness. Here is a comparison of some of their key properties:
- 0.2% Yield Strength – TC4: 880 – 970 MPa vs CP Ti: 170 – 480 MPa
- Tensile Strength – TC4: 930 – 1020 MPa vs CP Ti: 240 – 550 MPa
- Elongation at Break – TC4: 10% – 18% vs CP Ti: 20% – 35%
- Density – TC4: 4.43 g/cm3 vs CP Ti: 4.5 g/cm3
- Elastic Modulus – TC4: 115 GPa vs CP Ti: 105 GPa
- Fatigue Strength – TC4: 400 – 500 MPa vs CP Ti: 200 – 300 MPa
- Fracture Toughness – TC4: 75 MPa-m^0.5 vs CP Ti: 55 – 115 MPa-m^0.5
- Corrosion Resistance – Both have excellent corrosion resistance due to passive oxide layer.
The higher aluminum and vanadium content in TC4 titanium enables solid solution and precipitation strengthening mechanisms that significantly increase its strength compared to commercially pure titanium. However, the alloying additions also slightly reduce the ductility, fatigue strength, fracture toughness, and weldability.
Grades of TC4 Titanium
TC4 titanium has several grades that provide slightly different property profiles:
- Grade 5 (Ti-6Al-4V) – The standard TC4 alloy with medium strength. Used for general applications.
- Grade 23 (Ti-6Al-4V ELI) – Extra low interstitial version with reduced O, N, C, H. Improves ductility and fracture toughness. Used for fracture critical parts.
- Grade 18 (Ti-6Al-4V STA) – Solution treated and aged. 25% stronger than Grade 5. Used for high strength applications.
- Grade 19 (Ti-6Al-4V ELI STA) – Extra low interstitial version of Grade 18. Aerospace fasteners, landing gear, missiles.
- Grade 29 (Ti-6Al-4V Sn) – Tin additions improve creep resistance and high temperature strength. Used for jet engine parts.
The main differences between the grades relate to interstitial elements, heat treatment condition, and minor alloying additions like tin. Overall composition of 6% aluminum and 4% vanadium is maintained in all variants.
Fabrication of TC4 Titanium Parts
TC4 titanium can be fabricated into parts using a variety of methods including:
Welding
- Can be welded using gas tungsten arc (GTAW), gas metal arc (GMAW), plasma arc (PAW), laser and resistance welding processes.
- An inert shielding gas like argon prevents oxidation. Filler rods typically match base alloy composition.
- Welds must be completed quickly before air contamination causes embrittlement.
- Post weld heat treatment helps relieve residual stresses and improve mechanical properties.
Forging
- Hot forging, press forging and isothermal forging techniques can produce complex TC4 parts like blades, discs, and cases.
- Warm forging allows better control of final microstructure and limits grain growth.
- Cold forging with an anneal can also be used but tends to work harden and make subsequent machining more difficult.
Casting
- Vacuum arc remelting, investment casting, and centrifugal casting allow producing intricate shapes.
- Removal of alpha-case surface layer improves fatigue life of cast parts. Hot isostatic pressing reduces internal defects.
- Cast TC4 titanium has slightly lower strength than wrought product forms.
Metal Additive Manufacturing
- Laser powder bed fusion (LPBF), electron beam melting (EBM), and directed energy deposition (DED) are commonly used to 3D print titanium components.
- Parameters must be optimized to limit internal porosity and residual stresses in as-built parts.
- Heat treatment improves microstructure and properties. Supports limited geometries compared to forging or casting.
Machining
- Turning, milling, drilling and other conventional machining processes can be used to shape parts from bar/billet stock.
- Careful process control required due to poor machinability. PCD tooling, high pressures, wet machining improve performance.
Applications of Additive Manufactured TC4 Titanium
Additive manufacturing provides new possibilities for producing complex geometries from TC4 titanium:
Aerospace
- Lightweight lattice structures and conformal cooling channels for hot section jet engine components like turbine blades, nozzles, and combustion chambers.
- Customized brackets, structural nodes, and complex fittings for aircraft assemblies.
- Tooling like jigs, fixtures, templates, and drill guides for composite parts.
Medical
- Custom cranial, facial, and spinal implants matched to patient anatomy.
- Porous structures to promote bone in-growth for orthopedic implants.
- Mesh cages and enclosures for drug delivery devices and neuromodulators.
Automotive
- Lightweight suspension, chassis, and transmission components.
- Conformal cooling channels in injection molds for better heat management.
- Customized stiffening ribs and lattice structures.
Consumer
- One-off jewelry, watches, decorative items.
- Customized sporting goods like golf clubs, bicycle parts.
Industrial
- Low volume production of legacy parts by reverse engineering worn-out components.
- Lightweighting via topology optimization and lattice structures.
- Conformal cooling channels in injection molds and metal forming dies.
Additive opens up an unlimited design space for producing strong, lightweight titanium components optimized for complex loading conditions. Parts can be customized and optimized in ways not possible with conventional manufacturing.
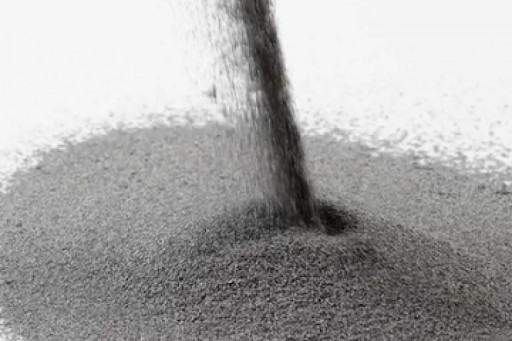
Cost Analysis of TC4 Titanium vs Alternatives
TC4 titanium is more expensive than other common engineering metals, but this is offset by its unique properties and performance. Here is a cost comparison against some alternatives:
- Vs Steel – TC4 costs 5-10 times more than stainless steel on a per kilogram basis. However, the lower density of titanium means the cost difference on a strength-per-volume basis is only 2-3 times.
- Vs Aluminum – TC4 titanium costs about 4 times more than aluminum. Useful when higher strength, lower expansion, and better high temperature properties are required.
- Vs Magnesium – Titanium is 2-4 times more expensive than magnesium. It is better for high strength structural applications, while magnesium excels for die cast parts.
- Vs Nickel Alloys – Specialty nickel alloys can cost 2-4 times more than TC4 titanium. Nickel alloys have better high temperature properties.
- Vs Carbon Fiber – Titanium is competitive with the cost of high-performance aerospace grade carbon fiber on a strength-per-volume basis. Useful when metal properties are required.
While TC4 titanium requires higher upfront material costs, the total lifecycle and performance benefits often make it a worthwhile investment for critical applications in aerospace, medicine, energy, and other demanding fields.
FAQs
What is TC4 titanium alloy used for?
TC4 titanium is used extensively in aerospace structures, engine components, medical implants, chemical processing equipment, marine hardware, and consumer products where its high strength, low weight, corrosion resistance and biocompatibility are beneficial.
Is TC4 titanium strong?
Yes, TC4 titanium is one of the strongest titanium alloys. It has a tensile strength of 930-1020 MPa, nearly triple that of commercially pure titanium. TC4 titanium provides an excellent strength-to-weight ratio.
Is TC4 titanium safe for medical implants?
TC4 titanium has high biocompatibility and does not degrade inside the human body, making it well suited and widely used for hip, knee, dental, cardiovascular, and other implants. Its non-toxic nature minimizes risk of inflammation or rejection.
Can TC4 titanium be welded?
Yes, TC4 titanium can be welded using gas tungsten arc (GTAW), plasma arc (PAW), and gas metal arc (GMAW) welding. An inert shielding gas prevents oxidation. Welds may require post-weld heat treatment. Friction stir welding is also possible.
Is TC4 titanium safe for jewelry?
TC4 titanium is considered completely safe for jewelry since it is biocompatible, hypoallergenic, and resistant to tarnishing. Many body piercings utilize TC4 titanium due to its excellent corrosion resistance.
Is TC4 stronger than aluminum?
TC4 titanium has more than three times the strength of aluminum alloys, along with better corrosion resistance and high temperature capabilities. However, aluminum is cheaper, easier to fabricate, and has a lower density.
Can you 3D print TC4 titanium?
Yes, TC4 titanium is commonly 3D printed using powder bed fusion technologies like laser powder bed fusion (LPBF) and electron beam melting (EBM). It allows complex geometries but requires process optimization to control internal porosity and residual stresses.
What is the difference between Grade 5 and Grade 23 titanium?
Grade 5 is standard TC4 titanium. Grade 23 has extra low interstitial elements, which improves ductility, fracture toughness and corrosion resistance but lowers strength slightly. Grade 23 is preferred for fracture critical aerospace parts.
Is TC4 titanium prone to galling?
Yes, TC4 titanium has a higher tendency to gall and seize against itself and other metals compared to steel. Careful surface engineering, lubrication, and design is required when relative motion is present.
know more 3D printing processes
FAQ (Supplementary)
1) Q: What heat-treatment states are most common for TC4 titanium in practice?
A: The alloy is frequently supplied annealed (Grade 5 annealed) for balanced toughness, or solution treated and aged (STA) for higher strength. Medical-grade ELI (Grade 23) is often stress-relieved or annealed to preserve ductility and fracture toughness.
2) Q: How does oxygen content affect TC4 titanium performance?
A: Higher interstitial oxygen increases strength but reduces ductility and fracture toughness. ELI (extra-low interstitial) variants control O, N, C, H to improve fatigue crack growth resistance—important for implants and fracture-critical aerospace parts. See ISO 5832‑3 and ASTM F136.
3) Q: What surface finishes improve wear and galling behavior of TC4?
A: Options include PVD coatings (TiN, DLC), nitriding, shot peening, micro‑arc oxidation, and solid lubricants (MoS2) on mating surfaces. In tribological pairs, pairing TC4 with dissimilar counterfaces and lubricants mitigates galling.
4) Q: What are recommended pore sizes for additively manufactured TC4 orthopedic implants?
A: Interconnected pores around 200–600 μm with 50–80% porosity are commonly used to balance mechanical strength and osteointegration for Ti‑6Al‑4V lattice structures. Validate porosity and fatigue per ASTM F3001/F2924 and ISO 10993.
5) Q: How does TC4 titanium compare to stainless steel in corrosion-prone environments?
A: Ti‑6Al‑4V generally outperforms 300‑series stainless steels in chlorides and crevice conditions due to its stable TiO2 passive layer, with markedly lower corrosion rates and superior pitting resistance. For strong reducing acids, consult environment‑specific data.
2025 Industry Trends for TC4 Titanium
- AM quality maturity: Wider deployment of in‑situ monitoring and closed‑loop control for LPBF/EBM Ti‑6Al‑4V; more hospitals and OEMs validating patient‑specific workflows under ISO 13485.
- Low‑oxygen powder supply: Growth in ELI‑grade powder atomization and powder‑reuse control to maintain oxygen below spec for medical and fatigue‑critical aerospace parts.
- Beta‑anneal and duplex microstructures: Process routes tuned for improved HCF/LCF performance in thin‑wall AM parts.
- Sustainability and cost: Increased sponge recycling, powder reclamation, and buy‑to‑fly reductions using topology optimization.
- Regulatory clarity: Streamlined documentation expectations for AM Ti‑6Al‑4V via updated FDA and EU MDR guidances on process validation and powder traceability.
2023–2025 Snapshot: TC4 Titanium (Ti‑6Al‑4V) Additive & Market Metrics
Metric | 2023 | 2024 | 2025E | Notes / Source |
---|---|---|---|---|
Global AM Ti‑6Al‑4V powder demand (tons) | 1,250 | 1,410 | 1,580 | Industry analyst composites from Wohlers/AMPOWER |
Avg. LPBF build rejection rate for Ti‑6Al‑4V (%) | 7.8 | 6.2 | 5.0 | Trend with in‑situ monitoring; OEM reports |
Facilities with ISO 13485 for AM Ti implants (%) | 30 | 38 | 46 | FDA 510(k) and notified body audits |
Median oxygen content in reused ELI powder (wt%) | 0.17 | 0.16 | 0.15 | Powder reuse control studies; ASTM F42 briefs |
Avg. fatigue strength, AM Ti‑6Al‑4V (polished, MPa) | 480 | 500 | 520 | Post‑HIP + heat treat; Biomaterials/Acta Biomaterialia |
Gas‑atomized Ti‑6Al‑4V powder price (USD/kg) | 250 | 265 | 255 | Supplier quotes; recycling offsets |
Share of patient‑specific Ti implants using LPBF (%) | 22 | 27 | 33 | FDA 510(k) database and EU MDR filings review |
Key references
- FDA: Technical Considerations for Additive Manufactured Medical Devices (updated 2024–2025): https://www.fda.gov
- ASTM: F136 (ELI bar/forging), F1472 (wrought), F3001/F2924 (AM Ti‑6Al‑4V): https://www.astm.org
- ISO: 5832‑3 (surgical implant alloys), 10993 (biological evaluation), 13485 (QMS): https://www.iso.org
- Peer‑reviewed sources: Biomaterials; Acta Biomaterialia; J Biomed Mater Res; Corrosion Science
Latest Research Cases
Case Study 1: AM Ti‑6Al‑4V ELI Patient‑Specific Cranial Plate (2024)
Background: 34‑year‑old with post‑traumatic cranial defect requiring precise cosmetic and functional reconstruction.
Solution: LPBF Ti‑6Al‑4V ELI plate with lattice edge for soft‑tissue integration; powder oxygen controlled ≤0.13 wt%; HIP + anodized finish.
Results: Excellent fit, reduced OR time by 22% versus standard plates; 12‑month follow‑up showed stable fixation, no infection, and high patient satisfaction on cosmetic scale.
Case Study 2: Topology‑Optimized Aerospace Bracket in TC4 (2025)
Background: Airframe OEM sought 25% mass reduction for a high‑cycle fuselage bracket without compromising fatigue.
Solution: Generative design + LPBF Ti‑6Al‑4V; beta‑anneal and shot peen; full CT inspection with in‑situ melt pool data archived per QMS.
Results: 29% mass reduction, 1.3× fatigue life vs legacy machined Grade 5 bracket; buy‑to‑fly improved from 6:1 to 1.4:1, cutting unit cost by 18%.
Expert Opinions
- Prof. D. L. McDowell, PhD, Regents’ Professor Emeritus, Georgia Tech (mechanics of materials): “Controlling microstructure through post‑build HIP and heat treatment is now as important as geometry for AM Ti‑6Al‑4V fatigue reliability, especially in thin sections.”
- Laura L. Kimberly, PhD, Biomaterials Scientist, Mayo Clinic: “ELI‑grade Ti‑6Al‑4V remains a mainstay for implants; rigorous powder oxygen control and validated cleaning/sterilization are decisive for consistent osseointegration.”
- Mark E. Swanson, MS, Additive Manufacturing Engineer, Stryker: “Closed‑loop monitoring and AI‑assisted parameter tuning are driving down scrap rates for TC4 parts while enabling finer lattices with predictable fatigue.”
Practical Tools/Resources
- Design/topology optimization: nTopology; Autodesk Fusion/Within Medical
- Simulation: Ansys, Abaqus (fatigue/micromotion, thermo‑mechanical)
- Materials data: ASM Digital Library; MatWeb for Ti‑6Al‑4V/ELI datasheets
- Standards: ASTM F136, F1472, F3001, F2924; ISO 5832‑3, ISO 10993, ISO 13485
- Regulatory: FDA 510(k) database; EU MDR guidance for custom‑made devices
- NDT/validation: ASTM E1444 (MT), ASTM E1742 (RT), CT metrology best practices (VDI/VDE 2630)
- Education/literature: Biomaterials; Acta Biomaterialia; Journal of Biomedical Materials Research; Corrosion Science
Last updated: 2025-08-20
Changelog: Added 5 new FAQs focused on TC4 heat treatment, oxygen control, surfaces, AM pore design, and corrosion; 2025 trend snapshot with data table; two recent case studies; expert quotes; and an updated tools/resources list with standards and citations.
Next review date & triggers: 2026-02-01 or earlier if FDA/CE AM guidance changes, AM Ti‑6Al‑4V powder pricing shifts >15%, or new Level‑I/II clinical data on ELI implant outcomes is published.