Introduction
Additive manufacturing (AM), also known as 3D printing, is a transformative approach to industrial production that enables the creation of lightweight, durable parts directly from digital models. One of the key enablers of AM technology is the development of advanced materials that can be processed into complex, three-dimensional components with superior mechanical properties. AM materials are essential for producing high-quality parts using 3D printing methods. This article will provide an in-depth look at AM materials, including key properties, categories, metals, polymers, ceramics, composites, and more.
Overview of AM Materials
AM materials refer to the raw materials such as metals, polymers, ceramics, and composites that are used as feedstock for 3D printing processes. The properties of AM materials have a major influence on the mechanical performance, accuracy, surface finish, and other characteristics of printed parts. Materials for AM must possess certain characteristics:
- Ability to be formed into filament, powder, resin, or other formats required by different 3D printing technologies
- Capability to flow, fuse, or bond together during the layer-by-layer build process
- Sufficient structural integrity and strength to form complex 3D objects without defects
- Metallurgical, chemical, and microstructural attributes to deliver required material properties in finished parts
The most commonly used categories of AM materials include metals, polymers, ceramics, and composites. Each material has distinct properties suitable for different applications of additive manufacturing.
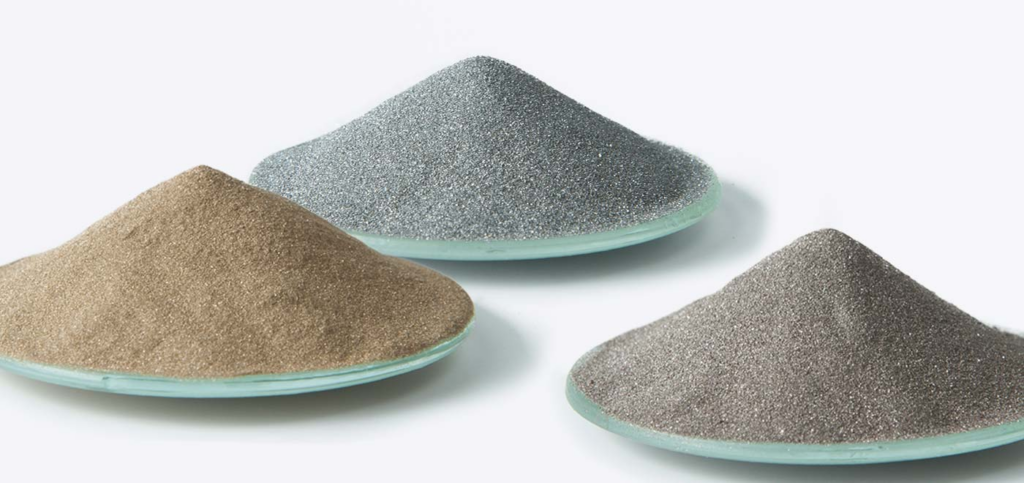
Key Material Properties for AM
There are several important properties of materials that determine their suitability and performance in AM processes:
Printability
Printability refers to the ability of a material to be processed by 3D printing machines into accurate, robust objects. Materials need properties like suitable melt flow, particle morphology, and spreading behavior to be printed successfully.
Strength
AM materials should have high strength to withstand forces and retain their shape without cracking or deforming in finished parts. Strength is important in weight-bearing components.
Toughness
Toughness is the ability to absorb mechanical or thermal stresses without fracturing prematurely. AM materials require good toughness to produce durable components.
Thermal properties
Suitable melting temperature, solidification kinetics, and thermal conductivity allow AM materials to be melted, deposited, and solidified precisely layer-by-layer during printing.
Rheological properties
The flow and viscosity behavior of melted or deposited AM materials impacts the accuracy and surface finish of printed parts. Ideal rheological properties promote smooth flow and bonding.
Density
AM materials should exhibit high density in finished parts to provide functionality, surface quality, and structural integrity to printed components. Lower density can compromise mechanical performance.
Categories of AM Materials
There are four major categories of materials used in additive manufacturing:
Metals for AM
Metals are commonly processed via powder bed fusion and directed energy deposition AM processes. Popular metals include:
- Stainless steel – Excellent strength, corrosion resistance, and biocompatibility make it ideal for manufactured parts in aerospace, automotive, medical, and many other sectors. Various alloy grades are used including 316L, 17-4PH, 15-5PH.
- Aluminum – Known for light weight, thermal properties, and strength. Used for aerospace components, automotive parts, heat exchangers, and consumer goods. Alloy 6061 is very popular.
- Titanium – Extremely strong but lightweight metal valued in aerospace applications. Grades include Ti6Al4V and Ti64. Offers biocompatibility for medical implants.
- Nickel alloys – Heat and corrosion resistant superalloys based on nickel, like Inconel 625 and 718. Used for tooling, turbine blades, and parts in extreme environments.
- Cobalt-chrome – Alloys of cobalt and chromium offering high strength, hardness, and biocompatibility for orthopedic and dental implants.
- Precious metals – Gold, silver, and platinum group metals and alloys used mainly for jewelry, electronics, and decorative parts.
Polymers for AM
Thermoplastic and photocurable polymers are processed using material extrusion, vat photopolymerization, powder bed fusion AM methods. Some common AM polymers:
- ABS (acrylonitrile butadiene styrene) – Strong and lightweight, used for prototyping and end-use parts like enclosures and automotive components.
- PLA (polylactic acid) – Made from corn starch. Used for sustainable packaging, food containers, consumer goods. Offers high rigidity.
- Nylon – Engineering-grade nylon delivers excellent strength, toughness, and thermal resistance. Used for end-use parts and functional prototypes.
- Photopolymers – Photocurable resins cured by UV light. Used in stereolithography and inkjet 3D printing. Offer high precision and surface quality. Examples include epoxy and acrylic resins.
Ceramics for AM
Ceramics and glass offer high heat resistance. Production methods include binder jetting, material extrusion, and stereolithography. Ceramic materials for AM include:
- Alumina (Al2O3) – High strength ceramic used in aerospace components and insulation parts. Offers corrosion resistance and thermal stability.
- Zirconia (ZrO2) – Extreme hardness makes it suitable for tooling, cutting inserts, and wear-resistant parts. Used in dental restorations.
- Silicon carbide (SiC) – Hard, lightweight ceramic used when high stiffness and thermal resistance is needed. Used to manufacture mirrors and semiconductor parts.
Composites for AM
Composite AM materials incorporate two or more constituent materials like polymers, ceramics, or metals. This allows tailoring of properties like strength, hardness, conductivity, etc. Examples include:
- Carbon fiber reinforced polymers – High strength-to-weight ratio. Used to build lightweight structures and components for aerospace and automotive.
- Metal matrix composites – Particulates of ceramics like silicon carbide are combined with aluminum alloys using DED AM to create enhanced properties. Used to make missile components, aircraft parts, etc.
- Photopolymer resin composites – Mixture of photopolymers and ceramic particles to combine toughness and stiffness. Used to 3D print dental restorations.
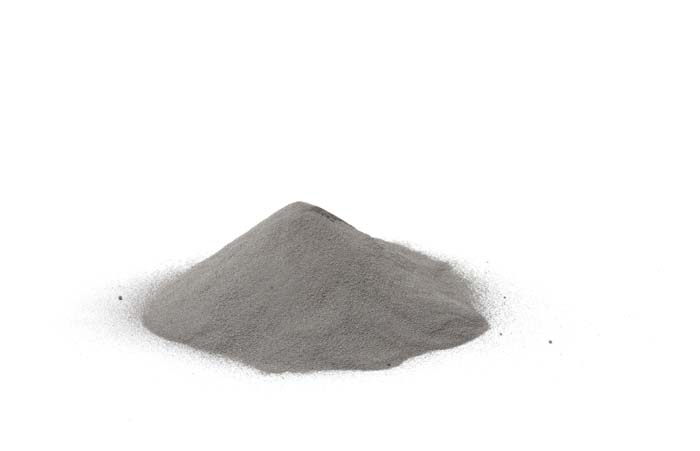
Metals for Additive Manufacturing
Metals account for a major portion of materials used in AM. The most popular metals for 3D printing include stainless steel, aluminum, titanium, nickel alloys, and cobalt chrome.
Stainless Steel
Stainless steel is one of the most widely used metals in AM today. It offers an excellent combination of high strength, good ductility and fracture toughness, corrosion and wear resistance, and biocompatibility. Various grades are used for AM including 316L, 304L, 17-4PH, 15-5PH, maraging steels, and duplex steels. Parts printed from stainless steel include spacecraft and rocket components, impellers, valves, surgical instruments, and automotive parts.
Aluminum
Aluminum alloys like AlSi10Mg possess properties like low density, good thermal conductivity, and excellent strength that make them attractive for AM. Key applications include complex airframe, engine, and drone components in aerospace, automotive parts including wheels, frames, and cylinders, customized lightweight structures for motorsports, heat exchangers, and consumer goods. Advantages over conventional manufacturing include optimized topology, part consolidation, and fracture resistance.
Titanium
Titanium alloys are valued in aerospace applications for properties like high strength-to-weight ratio, fracture resistance, fatigue life, and corrosion resistance. Over 75% of AM titanium usage is in aerospace. The most popular alloy is Ti6Al4V, followed by Ti64. Titanium AM parts include structural airframe components, turbine blades, spacecraft parts, and lightweight bone implants that integrate well with biological tissue. Challenges include high material costs and difficulties in machining AM titanium.
Nickel Superalloys
Nickel-based superalloys leverage strengths like retaining mechanical properties at high temperatures, corrosion and creep resistance to be widely used in extreme environments. Common alloys include Inconel 718, Inconel 625 and Inconel 939 printed by DED or powder bed methods. AM is used to manufacture turbine blades, tooling, rocket motor components, and parts in the nuclear, chemical processing, and energy industries.
Cobalt Chrome Alloys
Cobalt-chrome alloys like CoCrMo possess high hardness, strength, and excellent biocompatibility. They are the most widely used metals for printing dental prosthetics like crowns and bridges as well as orthopedic implants for knee, hip, and shoulder. AM enables customized designs and lattice structures in implants with bone-like mechanical properties and porous integration with tissue. The challenge is achieving smooth surface finishes.
Polymers for Additive Manufacturing
Polymers are commonly processed using material extrusion, powder bed fusion, and vat photopolymerization methods. Thermoplastics like ABS and PLA are widely used for concept models, functional prototypes, and end-use parts across industries. Photopolymers enable smooth finishes and fine features.
ABS – Acrylonitrile Butadiene Styrene
ABS offers properties like high impact resistance, toughness, and relatively high temperature resistance that make it suitable for 3D printing complex geometries. ABS finds use in visual concept models, prototyping consumer goods, automotive parts, enclosures, and snap-fit assemblies across aerospace, healthcare, and industrial sectors. Limitations include lower maximum working temperature compared to metals and limited UV resistance.
PLA – Polylactic Acid
PLA is a biodegradable thermoplastic derived from renewable corn starch or sugarcanes. It is widely used in 3D printing various products like food containers, tea bags, water bottles as well as medical implants and scaffolds that can safely degrade inside the body. Benefits include high rigidity, low toxicity, and relatively low printing temperatures. Limitations include low heat resistance and low impact strength.
Nylon
Nylon offers excellent tensile strength, surface finish, chemical resistance, abrasion resistance, and flexibility. This makes it useful for functional prototypes and end-use parts like gears, tooling, load-bearing components, food containers etc. in automotive, consumer goods, and industrial applications. Nylon powder can be processed using selective laser sintering and multi-jet fusion techniques. The low friction surface enables low wear sliding contact applications.
Photopolymers
UV-curable photopolymer resins allow remarkably high accuracy and surface finish in AM processes like stereolithography and digital light processing. Photopolymers solidify rapidly when exposed to UV light. Materials include epoxy, acrylic, and acrylate resins used for manufacturing lenses, medical models, jewelry, implants, high precision castings for aerospace, and other quality-critical components. Limitations include lower strength compared to industrial-grade thermoplastics.
Ceramics for Additive Manufacturing
Ceramics possess high strength and hardness at elevated temperatures, good electrical insulation and low thermal expansion properties. This makes them useful for hot section components in turbine engines, thermal protection systems, and other applications where refractory materials are needed. AM enables complex ceramic geometries unattainable by conventional methods.
Alumina
Alumina or aluminum oxide Al2O3 offers very high hardness, wear resistance, corrosion resistance, and temperature stability. AM is used to manufacture high-performance alumina components for aerospace and astronautics applications. Parts include rocket nozzles, radiation shields, and thermal insulation components, taking advantage of design freedoms enabled by AM. Limitations include lower fracture toughness and tensile strength that can cause unexpected failures in finished parts.
Zirconia
The extreme hardness, wear resistance, and low thermal conductivity of zirconia ZrO2 makes it useful for AM manufacturing of cutting tools, drills, extrusion dies, and other components subjected to high wear. In dentistry, it is used to print strong, aesthetic dental restorations like crowns and bridges that mimic the appearance of natural teeth. Fine particle size distribution is critical for high density and performance of finished zirconia parts.
Silicon Carbide
Silicon carbide SiC possesses very high hardness and strength, especially at high temperatures beyond the capability of metals. AM is ideally suited to manufacture SiC mirrors, optical components, and structures for space telescopes where temperature swings are vast. On earth, SiC is used in AM of semiconductor manufacturing equipment, nuclear fuel pellets, and turbine engine components. SiC parts often require secondary finishing to achieve mirror-smooth surfaces.
Metal AM Processes
The most widely used methods for printing metals include powder bed fusion and directed energy deposition:
Powder Bed Fusion
This includes selective laser sintering (SLS) and electron beam melting (EBM). SLS uses a laser while EBM uses an electron beam to selectively fuse metal powder particles layer-by-layer based on a cross section of the part geometry. After each layer, more powder is spread and compacted for the next layer. Stainless steel and titanium are commonly processed, delivering high accuracies and fine microstructures. Limitations include slow build rates.
Directed Energy Deposition
DED focuses a laser or electron beam to melt feedstock metal wire, powder, or blown powder at specific locations to stack material and fabricate a desired geometry. DED is often used to repair or add features to existing components. Advantages include faster build rates and ability to mix metal compositions. But accuracy and surface finish is lower than powder bed fusion.
Polymer AM Processes
Thermoplastics are commonly processed using material extrusion and powder bed fusion methods. Vat photopolymerization is used to process photocurable resins into high accuracy polymer parts.
Material Extrusion
Material extrusion heated thermoplastic filament and extrudes it layer-by-layer through a nozzle to fabricate a part. Fused deposition modeling (FDM) from Stratasys and fused filament fabrication (FFF) are material extrusion technologies widely used to 3D print ABS, PLA, nylon, and PC parts. Benefits include low machine and material costs. Downsides include lower accuracy, weak interlayer bonding, and visible layer lines on surfaces.
Powder Bed Fusion
Direct laser sintering (DLS) uses a laser to selectively fuse polymer powder particles laid in a thin bed. After each layer, a fresh layer of powder is deposited and sintered. DLS can build highly complex geometries in production thermoplastic materials like nylon with mechanical properties approaching that of injection molding. Multi-jet fusion (MJF) is a powder-based process from HP that uses fusing and detail agents for superior isotropic properties and accuracy.
Vat Photopolymerization
Stereolithography (SLA) converts liquid resin into solid 3D objects using ultraviolet light to selectively cure photosensitive resin. Digital light processing (DLP) also uses a vat of photocurable resin but cures each layer using a light projector system. These processes enable remarkably smooth surfaces and capturing of fine details for manufacturing patterns, investment castings, medical models, and jewelry patterns.
Ceramic AM Processes
Binder jetting and material extrusion methods are popularly used to process ceramics and ceramic-polymer composites into complex but robust 3D printed parts.
Binder Jetting
In this powder bed process, a liquid binding agent is selectively deposited to join ceramic powder particles during printing. Once completed, the green part is sintered to burn off binder and densify the part. Alumina, zirconia, silicon carbide and glass powders have been printed using binder jetting. It enables high ceramic content in parts. Limitations include lower achievable density relative to solid ceramics.
Material Extrusion
Also called robocasting or direct ink writing, material extrusion prints ceramic slurries through a nozzle to build structures layerwise. The composition typically combines ceramic powder, monomers, dispersant, and initiator. Once printed, the parts are cured then sintered. Silicon carbide and alumina composites with >50% ceramic content can be printed using this method. But shrinkage during drying and sintering can induce shape distortions.
Composite AM Materials
Additive manufacturing allows different base materials like polymers, metals, and ceramics to be combined into composite materials with tailored properties.
Metal Matrix Composites
Metal powders can be blended with hard reinforcements like silicon carbide or alumina during DED processing to achieve superior hardness, strength, and wear resistance compared to unreinforced metals. Nickel and titanium matrix composites have been augmented with SiC particles and nanotubes for enhanced stiffness and thermal stability in turbine and rocket engine hot section parts.
Carbon Fiber Composites
Chopped or continuous carbon fibers can reinforce photopolymers in SLA 3D printing or thermoplastics in FDM/FFF. This improves stiffness, static strength, thermal resistance, and dimensional stability of parts like drone frames and aircraft interior components while reducing weight. Excellent fiber orientation control is possible during AM.
Photocurable Resin Composites
SLA polymers are combined with ceramic particles and nanotubes to modify resin properties like modulus, heat deflection temperature, hardness, and thermal conductivity based on application requirements while retaining dimensional accuracy and surface finish benefits. This enables 3D printed dental bridges and crowns with enhanced mechanical properties and aesthetics.
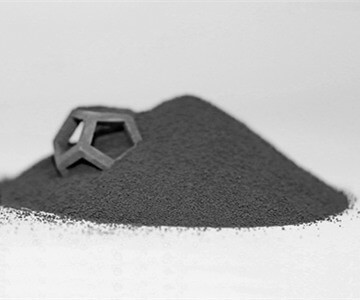
Advantages of AM Materials
AM materials unlock performance benefits and design possibilities unachievable through conventional manufacturing:
- Complexity – Intricate hollow and cellular structures can be produced directly from CAD models that would be impossible to manufacture otherwise. This enables lightweight, optimized designs.
- Customization – Patient-matched implants, insoles, prosthetics that perfectly fit an individual’s anatomy can be 3D printed from medical scan data for better comfort and restoration of function.
- Assembly Consolidation – Reducing part count by printing consolidated components improves reliability, reduces inventories, and enables faster production.
- High Performance – Directions strengthening of metals via epitaxial solidification and composites with oriented microstructures result in superior mechanical properties.
- Sustainability – Additive enables on-demand production with minimal waste. Some AM materials like biopolymers made from renewable sources also support sustainability.
Challenges for AM Materials
While AM materials offer many benefits, there are certain challenges that must be addressed for more widespread adoption:
- Standards – Lack of industry-wide specifications and standards for most AM materials makes consistency challenging. Material quality can vary across suppliers and printer technologies.
- Certification – Rigorous certification and documentation is required particularly for metal alloys used in mission-critical defense, aerospace, and medical applications before AM can be accepted for end-use production components.
- Defects – Some AM processes suffer from porosity, microcracking, delamination flaws in finished parts that compromise mechanical performance. Further improvements in material properties, quality control, and process parameters are needed.
- Surface Finish – Stair stepping and layer lines from AM can necessitate extensive manual polishing of surfaces. Some materials also suffer from grain structure roughness. Better understanding the causes and solutions for poor surface finish is required.
- Cost – AM material costs are often high due to proprietary formulations, limited suppliers, and low production volumes. Scaling up AM materials production can improve cost-competitiveness with conventional materials.
- Anisotropy – Some heavily oriented or layered AM microstructures result in directional variability in properties like higher strength parallel to build vs perpendicular. Improved material bonding and deposition techniques help overcome anisotropy.
The Future of AM Materials
AM materials innovation is vital for continued expansion of additive manufacturing. Some key areas that show promise for the future:
- Multimaterials – Single parts combining different metals, ceramics, polymers will enable true multifunctionality. This is being researched using multi-nozzle 3D printing.
- Smart materials – 4D printing incorporates shape memory alloys, hydrogels, liquid crystal elastomers to make objects that reconfigure shape/color/transparency when exposed to stimuli like heat, moisture, light, or magnetic fields.
- Biocompatible – Novel tissue engineering materials and stem cell carriers will drive adoption of AM in medical treatments to improve integration and regeneration.
- Sustainable – Eco-friendly, non-toxic AM materials derived from abundant and renewable resources need to be developed as alternatives to petroleum-based polymers.
- Nanocomposites – Polymer and metal matrices reinforced with nanotubes/nanoparticles to substantially enhance mechanical, thermal, electrical properties will open up new high-performance applications.
- Design tools – Physics-based multi-scale computer modeling of AM processes will lead to better predictions of microstructures and properties for qualification of new materials and optimization.
Conclusion
In summary, AM materials are vital enablers of functional 3D printed components across industries. Metals, polymers, ceramics, and composites each offer distinct capabilities to produce high-performance, complex parts using additive manufacturing processes. While challenges exist, AM materials innovation will continue to expand the design possibilities and benefits of 3D printing technology.