Introduction
Titanium alloys, particularly Ti-6Al-4V (also known as TC4 or Ti64), have become a staple material in additive manufacturing and 3D printing. TC4’s unique properties, including high strength-to-weight ratio, corrosion resistance, and biocompatibility, make it an ideal choice for a wide range of 3D printed parts and applications.
In this article, we will explore the key properties and characteristics of TC4 that lend itself well to 3D printing, the common TC4 powder types and parameters used in various 3D printing technologies, the applications and benefits of 3D printed TC4 components, and the future outlook for this versatile titanium alloy powder in additive manufacturing.
Key Properties of Titanium alloys for 3D Printing
TC4’s balance of mechanical properties, corrosion resistance, and biocompatibility stem from its composition and microstructure. Here are some of the key properties that make this titanium alloy a top choice for 3D printing:
High Strength-to-Weight Ratio
With a density of 4.43 g/cm3, TC4 is almost half the density of steels. Yet its tensile strength ranges from 1000 to 1100 MPa, comparable to many steels. This gives TC4 an excellent strength-to-weight ratio, making it suitable for lightweight structural components.
Corrosion Resistance
The addition of aluminum to titanium gives TC4 excellent corrosion resistance against many acids, alkalis, and chlorides. This resistance allows TC4 printed parts to be used in harsh environments. The oxide layer that forms on TC4 also provides biocompatibility.
Weldability
TC4 can be fusion welded using traditional welding methods like TIG and laser. This aids in joining 3D printed TC4 components with conventionally manufactured titanium parts and assemblies.
High Temperature Properties
TC4 retains decent mechanical properties at elevated temperatures of up to 400°C for short periods. This allows TC4 printed components to be used in high-temperature applications in aerospace, automotive, and more.
Biocompatibility
The oxide layer and lack of cytotoxicity make TC4 highly biocompatible. This allows its use in biomedical implants and devices that interface with the human body. Common applications include dental implants, orthopedic implants, and surgical instruments.
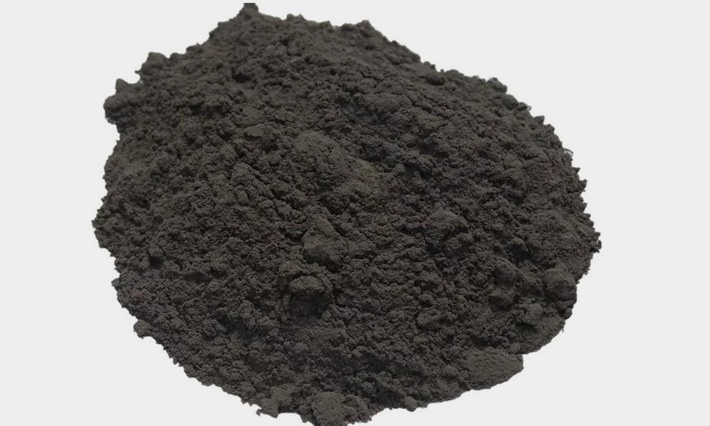
TC4 Powder Types for 3D Printing
TC4 is available in various powder types to suit different 3D printing processes:
Plasma Atomized Powder
Plasma atomization uses high temperature plasma gas to melt and atomize the liquid titanium alloy into fine spherical powders. This gives powder particles with good flowability and packing density suited for binder jetting and material extrusion 3D printing.
Gas Atomized Powder
In inert gas atomization, the alloy melt stream is broken into droplets that solidify into spherical powders. Gas atomized TC4 powder has higher purity and more consistent particle sizes ideal for laser powder bed fusion 3D printing.
Blended Elemental Powder
Blended elemental powder starts with pure titanium, aluminum and vanadium powders that are mechanically blended. This gives irregular shaped particles optimized for laser directed energy deposition 3D printing processes.
Key Printing Parameters for TC4
The printing parameters for TC4 vary based on the specific 3D printing process used:
Laser Powder Bed Fusion
- Layer thickness: 20-50μm
- Laser power: 100-400W
- Scan speed: 800-1200mm/s
- Hatch spacing: 80-200μm
- Supports are needed during printing to avoid thermal stresses and warping
Binder Jetting
- Layer thickness: 80-150μm
- Binder saturation: 90-100%
- Curing temperature: 180°C
- Infiltration required post-printing to achieve full density
Directed Energy Deposition
- Powder feed rate: 3-12 g/min
- Laser power: 500-1000W
- Travel speed: 5-25 mm/s
- Multiple passes and scanning strategies are used to control properties
Applications of 3D Printed TC4 Parts
Thanks to its well-balanced material properties, TC4 is used in 3D printing across diverse industries:
Aerospace
Lightweight structural brackets, fuselage components, turbine blades, heat exchangers and more demanding aerospace parts are printed from TC4.
Medical Implants
TC4’s biocompatibility allows printed production of patient-specific implants like hip stems, spinal cages, cranial plates, and dental implants.
Automotive
Lightweight powertrain, engine, and suspension components like pistons, turbochargers, valves, and gears are increasingly 3D printed in TC4.
Chemical Processing
Corrosion-resistant TC4 is used to print agitators, housings, valves and other components for handling corrosive chemicals.
Benefits of 3D Printing TC4 vs Traditional Processing
Additive manufacturing of TC4 components provides several advantages compared to traditional subtractive methods:
Design Freedom
3D printing enables complex geometries like lattices, internal channels, and organic shapes that cannot be cast or machined easily.
Weight Reduction
Lighter components can be printed by optimizing the design for weight reduction and using only the required amount of material.
Part Consolidation
Multiple components can be consolidated into a single 3D printed part, reducing assembly requirements.
Customization
Patient-specific implants, jigs and fixtures for manufacturing lines, and design iterations can be easily customized and printed without tooling.
Reduced Wastage
Significantly less material is wasted in 3D printing compared to machining from billets.
Shorter Lead Times
The additive process avoids long and costly tooling and setup associated with conventional titanium component manufacturing.
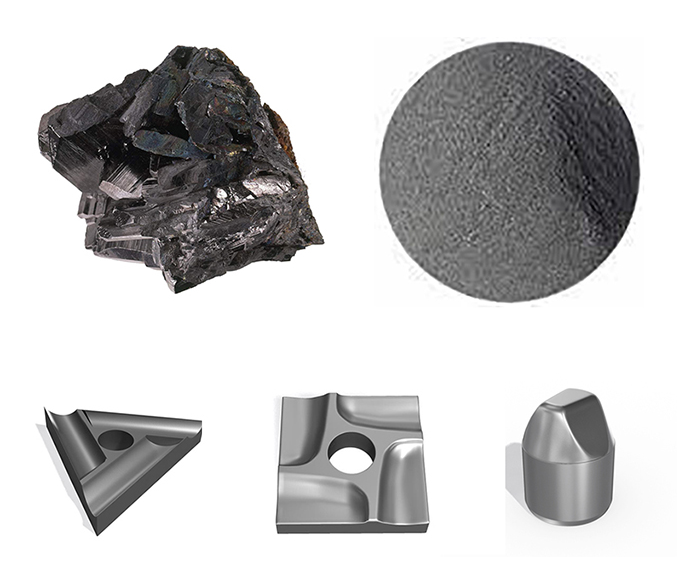
Challenges in 3D Printing TC4
While 3D printing TC4 opens new doors, some challenges still remain:
Anisotropic Properties
The properties of printed TC4 components can vary based on build orientation due to layer-by-layer fabrication. Orientation needs optimization to maximize strength where needed.
Porosity Control
Lack of full density and porous defects could occur without optimized processing parameters. This requires adapting parameters for different geometries and 3D printing process nuances.
High Cost
Both TC4 powder and 3D printing using titanium alloys is more expensive than other materials and processes. The higher cost limits wider adoption.
Post-Processing
Significant post-print machining and finishing may still be required to achieve final dimensions, surface finish, aesthetics and correct microstructure.
Qualification Standards
Industry-specific codes and standards for qualification and certification of 3D printed titanium components are still evolving and maturing.
Future Outlook
As 3D printing technology continues advancing rapidly, TC4 will continue increasing in usage across industries. Here are some future trends:
Process Improvements
Processes like laser powder bed fusion and directed energy deposition will continue improving build rates, part density, material properties and surface finish.
Larger Components
Size limitations in powder bed fusion will expand with larger build volumes, allowing printing of bigger TC4 parts for aerospace and other sectors.
Hybrid Manufacturing
Hybrid manufacturing using additive and subtractive processes together will enable efficient production of complex TC4 components with minimal lead time.
New Applications
3D printing will drive increased use of TC4 in diverse applications ranging from sporting goods to marine hardware that benefit from light weight and corrosion resistance.
Design Software Integration
Advances in design software will tightly integrate simulation, topology optimization, support generation and other tools for seamless design for additive manufacturing.
Cost Improvements
Increased adoption, process improvements and higher powder reuse will bring down costs, making more applications of 3D printed TC4 financially viable.
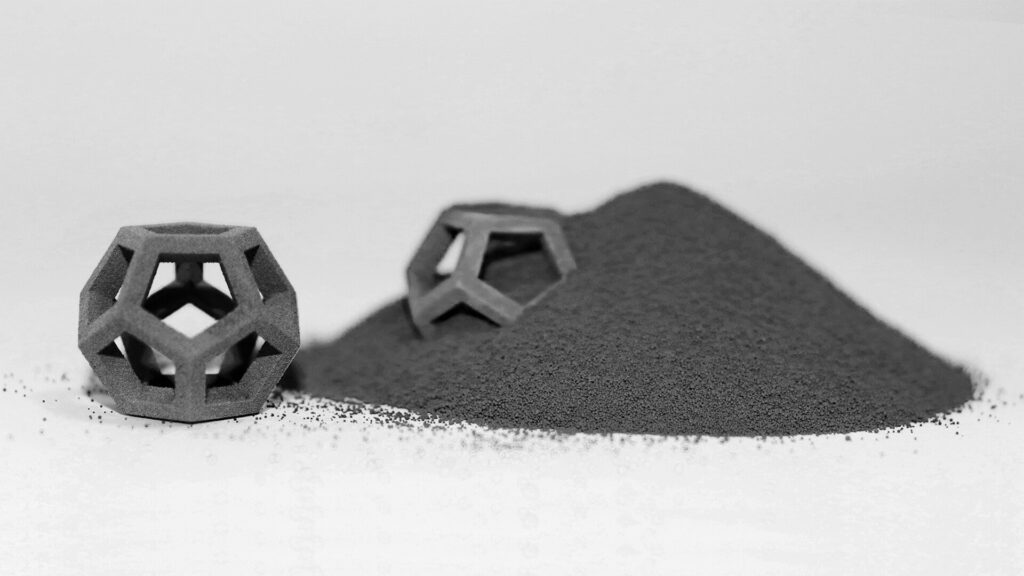
Summary
In summary, Ti-6Al-4V or TC4 possesses an optimal mix of properties like high strength, low density, temperature resistance, weldability and corrosion resistance that make it well-suited for 3D printing of critical components across aerospace, medical, automotive, chemical and other demanding industries.
As 3D printing technology continues its rapid evolution, TC4 will become the material of choice for an increasing number of additively manufactured components and use cases that benefit from its unique capabilities. With improved economics, process capabilities and application understanding, TC4 is slated to be a foundational material for 3D printing and a key enabler of innovative component designs well into the future.
FAQ
What makes TC4 suitable for 3D printing?
TC4 possesses properties like high strength, low density, temperature resistance, corrosion resistance and biocompatibility that make it an ideal material for 3D printing complex and demanding components for aerospace, medical and other applications.
What are the main 3D printing processes used with TC4?
The most common 3D printing processes for TC4 are laser powder bed fusion, binder jetting, and directed energy deposition. Each process requires specific powder characteristics and printing parameters.
What are some typical applications of 3D printed TC4 parts?
TC4 parts are 3D printed for diverse applications including aerospace components, biomedical implants, automotive parts, chemical equipment, and consumer products like sporting goods that benefit from TC4’s properties.
How does 3D printing compare to traditional processing of TC4?
3D printing TC4 enables lighter designs, part consolidation, customization, reduced waste, and faster production compared to limitations like design constraints, high buy-to-fly ratios, and long lead times with conventional subtractive manufacturing.
What are some of the challenges in 3D printing TC4?
Some key challenges are anisotropic mechanical properties, porosity defects, high material and process cost, significant post-processing requirements, and evolving qualification standards. Further process refinements and improvements will help address these.