Introduction
In the realm of advanced manufacturing, Selective Laser Melting (SLM) has emerged as a groundbreaking technology that has the potential to reshape multiple industries. The advent of SLM material, also known as metal 3D printing, has opened up new possibilities for engineers, designers, and manufacturers. This article delves into the world of SLM material, its applications, and its role in transforming industries across the globe.
What is SLM Material?
Selective Laser Melting, or SLM, is an additive manufacturing technique that involves using a high-powered laser to selectively melt and fuse metallic powders together, layer by layer, ultimately creating a three-dimensional object. The process is based on Computer-Aided Design (CAD) data, allowing for intricate and precise structures to be produced with relative ease.
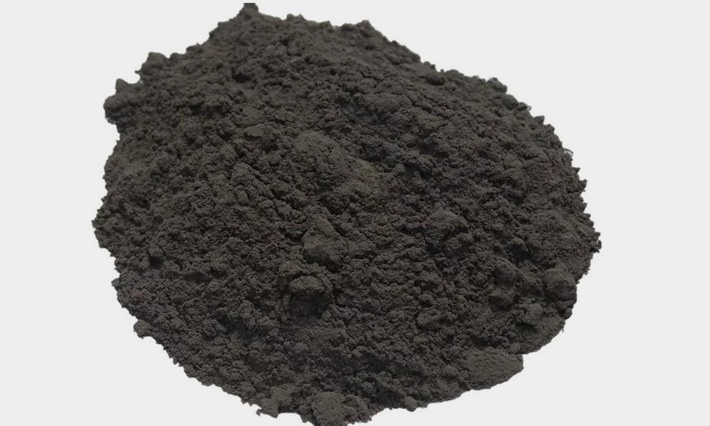
The Advantages of SLM Material in Various Industries
3.1 Aerospace
The aerospace industry has embraced SLM material due to its ability to fabricate lightweight, high-strength components. The reduction in weight is critical for aircraft, leading to improved fuel efficiency and overall performance. Moreover, SLM enables complex geometries that were previously impossible to achieve using traditional manufacturing methods.
3.2 Automotive
In the automotive sector, SLM material has revolutionized the prototyping and production of parts. The technology offers design freedom, cost-effectiveness, and the capability to create custom components tailored to specific vehicle models. Additionally, the use of SLM material results in lighter vehicles, contributing to reduced emissions and enhanced energy efficiency.
3.3 Medical
The medical field has witnessed transformative advancements through SLM material. Custom implants, such as orthopedic implants and dental prosthetics, can be fabricated based on individual patient scans. This personalization not only improves patient outcomes but also reduces the risk of rejection and the need for additional surgeries.
3.4 Engineering
Engineers benefit greatly from SLM material as it allows for rapid prototyping and design iterations. The technology enables the production of complex engineering structures, such as lattice structures, which offer exceptional strength-to-weight ratios. This innovation paves the way for novel engineering solutions in various industries.
The Process of Selective Laser Melting (SLM)
4.1 Powder Preparation
The SLM process begins with the careful preparation of metallic powders. These powders must meet strict requirements in terms of size, morphology, and chemical composition to ensure the desired mechanical properties of the final product.
4.2 3D CAD Model Creation
The next step involves creating a detailed 3D Computer-Aided Design (CAD) model of the desired object. The CAD model serves as the digital blueprint that guides the SLM machine during the printing process.
4.3 Preparing the SLM Machine
Before printing can commence, the SLM machine requires meticulous calibration and setup. The build chamber is filled with an inert gas, typically argon or nitrogen, to prevent oxidation during the printing process.
4.4 The Melting Process
The SLM machine’s high-powered laser selectively melts the powdered material according to the instructions from the CAD model. Layer by layer, the object takes shape, with each layer bonding firmly to the previous one.
4.5 Post-Processing and Finishing
Once the printing is complete, the object undergoes post-processing to remove excess powder and improve surface finish. In some cases, additional treatments like heat treatment and machining may be necessary to achieve the desired mechanical properties.
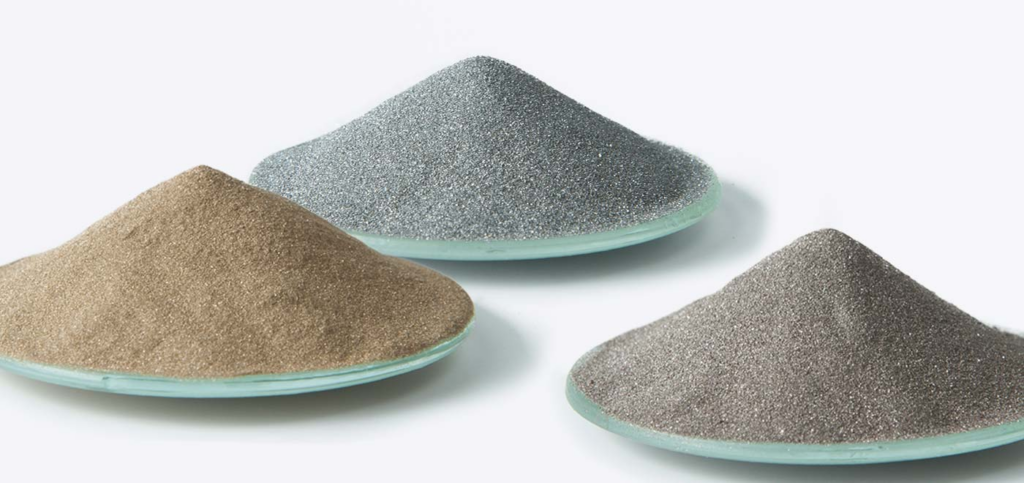
Materials Used in SLM
5.1 Metals
Metals such as stainless steel, titanium, aluminum, and nickel-based alloys are commonly used in SLM. Each metal offers unique properties that make them suitable for specific applications.
5.2 Polymers
SLM is not limited to metals; polymers can also be used. Polyamide (nylon) and polylactic acid (PLA) are popular choices for 3D printing functional plastic parts.
5.3 Ceramics
Ceramic materials, like zirconia and alumina, are employed for their excellent biocompatibility, making them ideal for medical applications.
5.4 Composites
SLM can be used to fabricate composite materials, combining the benefits of different materials into a single component.
Applications of SLM Material in Today’s World
6.1 Prototyping
SLM accelerates the prototyping process, enabling engineers and designers to quickly iterate and refine their designs.
6.2 Customization
The ability to create custom components has opened doors to unique and personalized products for consumers.
6.3 Lightweight Structures
Industries seeking lightweight yet durable structures can benefit greatly from SLM material.
6.4 Repairs and Replacements
SLM is also used for repairing and replacing critical parts, reducing downtime and cost.
6.5 Complex Geometries
SLM allows the realization of intricate and complex geometries that were previously unachievable.
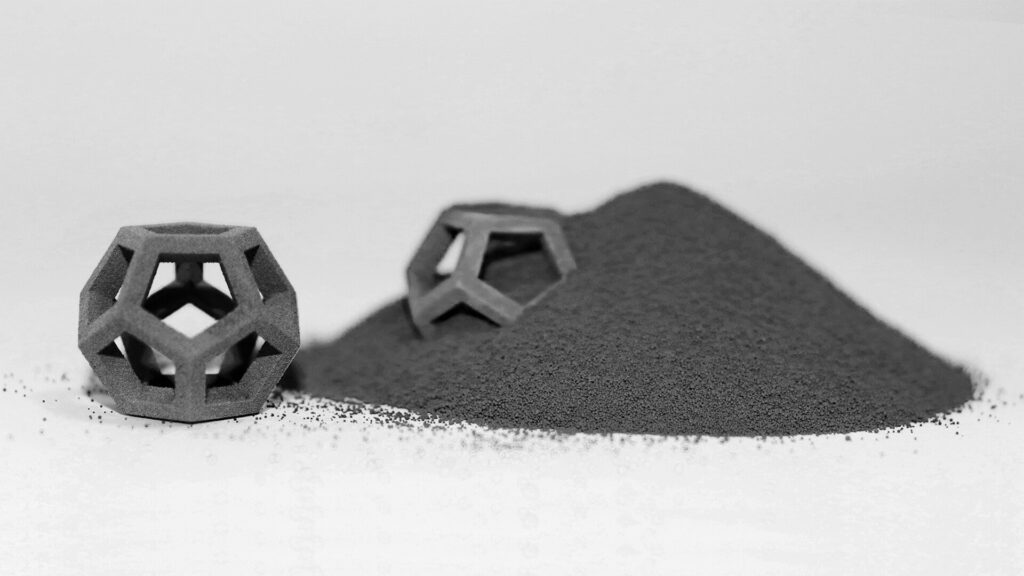
Challenges and Limitations of SLM Material
7.1 Material Properties
Certain material properties, such as porosity and anisotropy, can pose challenges for certain applications.
7.2 Design Constraints
Designing for SLM requires specific considerations to ensure successful printing and optimal performance.
7.3 Production Time
The printing process can be time-consuming, especially for large and intricate objects.
7.4 Cost
The initial investment in SLM technology can be substantial, and the cost of materials can also be high.
The Future of SLM Material
As SLM technology continues to advance, we can expect even greater material options, faster printing speeds, and improved cost-effectiveness. The future of SLM material holds the promise of transforming more industries and making additive manufacturing increasingly accessible.
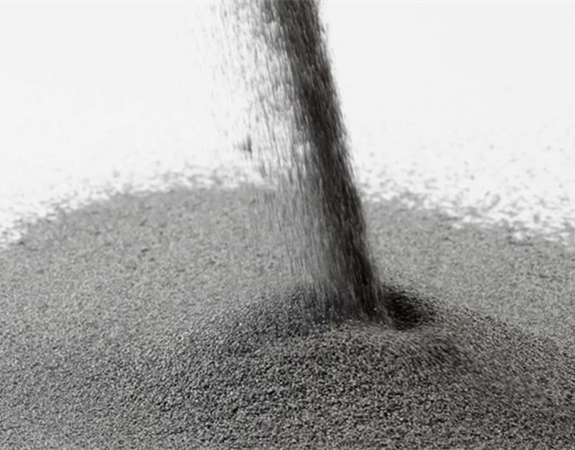
Conclusion
Selective Laser Melting (SLM) material has emerged as a transformative force in the world of advanced manufacturing. Its ability to create complex geometries, lightweight structures, and custom components has revolutionized industries like aerospace, automotive, medical, and engineering. The process of SLM involves carefully preparing metallic powders, creating a detailed 3D CAD model, calibrating the SLM machine, selectively melting the material with a high-powered laser, and finishing the object post-printing.
Metals, polymers, ceramics, and composites are among the materials used in SLM, each with its own unique set of properties suited for specific applications. The versatility of SLM has led to its adoption in various fields, including rapid prototyping, customized products, lightweight structures, repairs, and intricate designs.
However, along with its advantages, SLM material also faces certain challenges and limitations. Material properties, design constraints, production time, and costs are among the factors that need to be carefully considered when utilizing SLM technology.
Despite the challenges, the future of SLM material is bright. Continued advancements in technology are expected to lead to a wider range of material options, faster printing speeds, and improved cost-effectiveness. This, in turn, will expand its applications and bring additive manufacturing to new heights.
FAQs
1. What is SLM material?
SLM material refers to the application of Selective Laser Melting technology in additive manufacturing, where metallic powders are selectively melted using a high-powered laser to create three-dimensional objects.
2. What industries benefit from SLM material?
SLM material finds applications in various industries, including aerospace, automotive, medical, and engineering.
3. What are the advantages of SLM material in the aerospace industry?
In the aerospace industry, SLM material allows for the fabrication of lightweight, high-strength components, leading to improved fuel efficiency and performance.
4. Can SLM be used with materials other than metals?
Yes, SLM can also be used with materials like polymers, ceramics, and composites, providing a wide range of possibilities for different applications.
5. What are the challenges of using SLM material?
Challenges of using SLM material include managing material properties, design constraints, production time, and costs.