Molybdenum metal powder is an important material with growing applications in various industries. This guide provides a detailed overview of molybdenum metal powder, its properties, production methods, applications, suppliers, and more.
Overview of Molybdenum Metal Powder
Molybdenum is a silvery-white transition metal with the symbol Mo and atomic number 42. In its pure metal form, molybdenum has high strength, hardness, thermal conductivity, and resistance to corrosion.
Molybdenum metal powder refers to small particles of pure molybdenum metal or molybdenum alloys produced through various methods into a fine powder form.
Here is a quick reference table summarizing key details about molybdenum metal powder:
Parameter | Details |
---|---|
Chemical Formula | Mo |
Atomic Number | 42 |
Atomic Weight | 95.95 g/mol |
Density | 10.22 g/cm3 |
Melting Point | 2622°C |
Color | Silver-white |
Common Powder Types | Pure molybdenum, molybdenum alloys |
Particle Sizes | 1-100 microns |
Key Properties | High strength, thermal conductivity, corrosion resistance, lubricity |
Main Applications | Metallurgy, chemicals, catalysts, coatings, electronics |
Molybdenum metal powder offers several beneficial properties that make it suitable for use across various high-temperature applications in different industries.
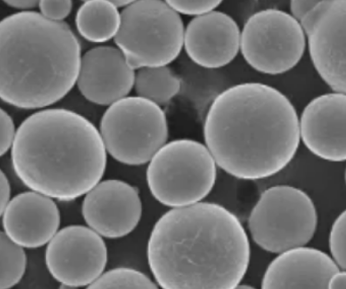
Properties of Molybdenum Metal Powder
Molybdenum metal powder possesses a unique combination of chemical, physical, electrical, and mechanical properties. Here are some of the key properties of molybdenum powder:
High Melting Point
Molybdenum has an extremely high melting point of 2622°C, which is higher than most commercial metals. This allows molybdenum powder to retain its strength and resist deformation under high temperature service conditions above 1000°C.
Thermal Conductivity
Molybdenum has a thermal conductivity of 138 W/m-K, which enables efficient heat transfer in applications like electrodes and heating elements. This improves thermal shock resistance.
Corrosion Resistance
Molybdenum powder exhibits excellent corrosion resistance towards acids, salts and reducing atmospheres even at elevated temperatures. A protective oxide layer forms on the surface.
High Strength
Molybdenum has high tensile strength ranging from 200 to 300 MPa. This gives components good creep resistance and structural integrity.
Lubricity
Molybdenum powder provides solid lubrication in certain applications, reducing friction and wear. The lubricity increases at higher temperatures.
Electrical Conductivity
Molybdenum has electrical resistivity of 5.5 microohm-cm, making it useful as electrodes, contacts and heating elements.
This unique combination of properties makes molybdenum metal powder suitable for specialized high-temperature applications in demanding environments. Proper powder characteristics help utilize these properties.
Production Methods for Molybdenum Metal Powder
Molybdenum metal powder can be produced through various techniques that reduce the particle size of molybdenum metal to achieve a fine powder form:
Mechanical Milling
Molybdenum lumps are crushed into a powder using ball mills or stamp mills. Controlled milling produces fine powder down to 1 micron.
Gas Atomization
Molten molybdenum is atomized by an inert gas jet into small droplets that solidify into fine spherical powder. Powders up to 100 microns can be produced.
Plasma Spheroidization
Irregular molybdenum powder is remelted and spheroidized using a plasma torch to make spherical powder with good flowability.
Chemical Reduction
A molybdenum compound like molybdenum oxide is chemically reduced using hydrogen gas to obtain pure metallic powder.
Electrolysis
Aqueous molybdate salt solution is electrolyzed to deposit molybdenum powder onto the cathode.
Proper control over the production process parameters yields molybdenum powder with customizable particle size, shape, purity, and microstructure suitable for the intended application.
Types of Molybdenum Metal Powder
Molybdenum metal powders are available in different types depending on composition and application requirements:
Powder Type | Description |
---|---|
Pure Molybdenum | Contains 99% or more molybdenum with minimal impurities |
Molybdenum Alloys | Alloyed with other metals like lanthanum, titanium, tungsten, niobium, etc. |
Oxide Coated | Thin oxide layer provides corrosion resistance |
Lubricant Coated | Coated with lubricants like graphite, molybdenum disulfide, tungsten disulfide etc. |
Sintering Aids Coated | With nickel coating to promote sintering of powder compacts |
Pure molybdenum powder provides optimal high temperature performance. Alloying additions like potassium, silicon and boron improve machinability and sinterability. Coatings tailor the powder properties for specific applications.
Particle Size Distribution
Molybdenum powder is available in different particle size distributions categorized as per the mesh sizes:
Powder Grade | Particle Size (microns) |
---|---|
Ultrafine | 1-10 |
Submicron | 1-20 |
Fine | 10-30 |
Medium | 30-75 |
Coarse | 75-150 |
Ultrafine and submicron powders provide higher sintered density and uniform microstructure. But they can be pyrophoric. Coarse powders offer better flowability for industrial handling. A suitable particle size is chosen based on final part requirements.
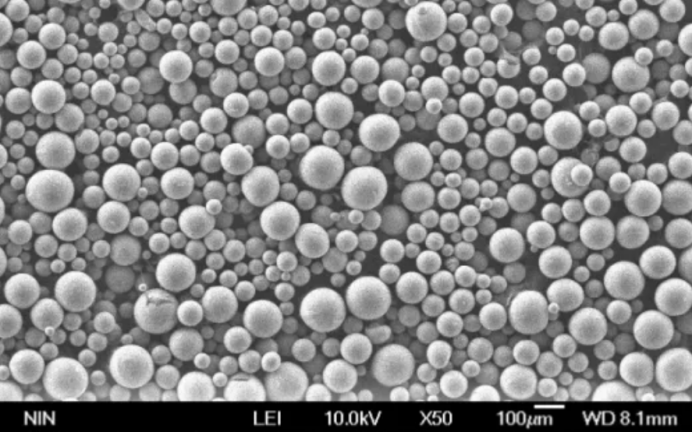
Characteristics of Molybdenum Powder
Molybdenum powders are characterized by various attributes that determine their performance:
Parameter | Significance |
---|---|
Particle Size | Affects sintered density, shrinkage, microstructure, surface area |
Particle Shape | Spherical shape provides good flowability |
Purity | High purity optimizes high temperature behavior |
Apparent Density | Influences compliance with net-shape processing |
Specific Surface Area | Determines sintering kinetics and densification |
Sintering Activity | Ability to densify into a pore-free microstructure |
Oxygen Content | Lower oxygen improves ductility and conductivity |
The powder characteristics are tailored to meet the needs of specific applications during powder production itself.
Applications of Molybdenum Metal Powder
Molybdenum metal powder finds uses in diverse high temperature applications across different industries:
Automotive Parts
- Pistons
- Engine valves
- Nozzle parts
Electrical Contacts
- Relays
- Switches
Heating Elements
- High temperature furnaces
- Kilns
Welding Products
- Welding rods
- Wire fluxes
Chemical Equipment
- Reactor vessels
- Heat exchangers
Electronics
- Conductive pastes
- Metallization of ceramics
Coatings
- Thermal spray coatings
- Corrosion resistant coatings
Composites
- Reinforcements
- Microwave absorbers
Catalysts
- Hydrotreating catalysts
- Hydrocracking catalysts
Molybdenum powder imparts high temperature strength, conductivity, corrosion resistance, and other benefits to components across these applications.
Global Suppliers of Molybdenum Powder
Some of the major global suppliers of molybdenum metal powder include:
Company | Location |
---|---|
H.C. Starck | Germany |
Molymet | Chile |
JDC-Moly | China |
Exploiter Molybdenum | China |
Shandong Guangchuan Molybdenum | China |
Jiangsu Fengfeng Tungsten & Molybdenum | China |
These companies can provide molybdenum powders customized for various applications in terms of composition, particle size, shape, and powder characteristics.
Pricing of Molybdenum Powder
The price of molybdenum metal powder depends on various factors:
- Purity: High purity (99.9%) powder is more expensive than lower purity grades.
- Particle Size: Ultrafine and submicron powders are more costly than coarse powders.
- Composition: Alloy powders and coated powders cost more than pure molybdenum.
- Quantity: Prices decrease for bulk orders due to economies of scale.
- Supplier: Prices vary between different global suppliers.
Typical price ranges:
Powder Grade | Price Range |
---|---|
Pure Molybdenum | $30-50 per kg |
Alloy Powder | $50-100 per kg |
Ultrafine Powder | $80-150 per kg |
Contact suppliers for exact price quotes based on your specific requirements.
Processing Molybdenum Powder into Parts
Molybdenum powder can be converted into parts using various techniques:
Press and Sinter
Compacting into a green compact using presses, followed by vacuum sintering. This is the most common method.
Metal Injection Molding (MIM)
Mixing with binder into a feedstock and injection into a mold to produce complex shapes.
Additive Manufacturing
3D printing of molybdenum parts using laser or electron beam powder bed fusion.
Thermal Spraying
Spray coating using molybdenum powder to deposit coatings.
Process | Advantages | Disadvantages |
---|---|---|
Press and Sinter | Simple, low cost | Limited complexity, machining required |
Metal Injection Molding (MIM) | Complex shapes, net shape | Multi-step process, binder removal |
Additive Manufacturing | Custom designs, fast turnaround | High equipment costs, size limitations |
Thermal Spraying | Low equipment cost, large parts | Porous coatings, line-of-sight process |
The optimum powder metallurgy process is selected based on part size, shape, quantity and properties.
Installation, Operation and Maintenance
Proper installation, operation and maintenance practices must be followed when handling molybdenum powder:
- Use inert gas gloves during powder handling to prevent oxidation. Molybdenum oxidizes readily in air at high temperatures.
- Store powder sealed and dry to prevent any moisture pick up. Moisture can make the powder pyrophoric.
- Handle powder in well-ventilated areas away from sparks or ignition sources. Finely divided molybdenum powder may be flammable.
- Dispose according to local environmental regulations. Molybdenum may present hazards if released into the environment.
- Develop standard operating procedures for safe handling, processing and maintenance. Provide training to personnel.
- Inspect equipment regularly for leaks, damaged seals or clogged powder transfer lines. Perform preventive maintenance.
- Follow recommended practices by occupational health and safety organizations to minimize risks.
Proper handling is vital for optimizing powder quality, equipment lifespan and operational safety.
Choosing a Reliable Molybdenum Powder Supplier
Here are some tips for selecting a suitable molybdenum powder supplier:
Experience
- Look for an established company with years of experience in producing molybdenum powders specifically.
Technical Capability
- Ensure the supplier has expertise in manufacturing powders with customized characteristics using various techniques.
Quality Systems
- Select a supplier certified for quality standards like ISO 9001 that follows strict quality control practices.
R&D Competence
- Give preference to suppliers investing in R&D to continually improve their powder production processes.
Customer Service
- Choose a responsive supplier focused on understanding customer needs and providing personalized service.
Logistics Infrastructure
- Opt for suppliers with warehousing and transportation capabilities to ensure timely worldwide delivery.
Pricing
- Compare price quotations from shortlisted suppliers to strike an optimal balance between cost and quality.
Choosing an experienced and reliable molybdenum powder manufacturer helps obtain a consistent supply of high-quality powder tailored for specific requirements.
Pros and Cons of Molybdenum Metal Powder
Molybdenum powder offers several benefits along with some limitations:
Pros
- Excellent high temperature strength
- High thermal conductivity
- Strong corrosion resistance
- Good wear resistance
- High electrical conductivity
- Low thermal expansion
- Net-shape manufacturability
Cons
- Relatively high cost
- Low machinability in sintered form
- Susceptible to oxidation at high temperatures
- Limited weldability in some forms
- Brittle behavior at low temperatures
For applications requiring stable performance at temperatures above 1000°C with thermal cycling, molybdenum powder provides unique capabilities despite its higher cost.
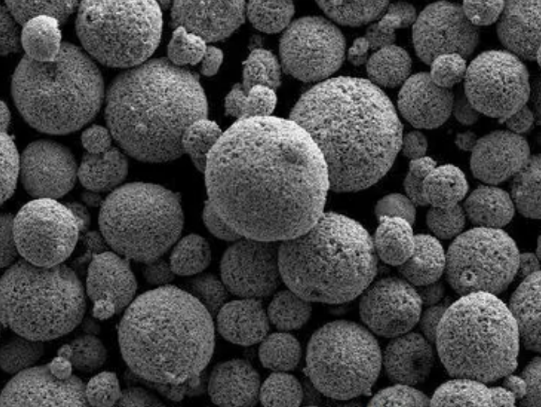
FAQs
Q: What is molybdenum metal powder used for?
A: The main uses of molybdenum powder are in metallurgy, chemicals, coatings, electronics, welding, automotive parts, heating elements, and other high-temperature applications.
Q: Does molybdenum powder require special handling?
A: Yes, molybdenum powder may be flammable when finely divided. It also readily oxidizes at high temperatures. Proper inert atmosphere handling and storage is required.
Q: Is molybdenum powder toxic?
A: Molybdenum has low toxicity but molybdenum powder may present health hazards like eye or respiratory irritation upon prolonged exposure. Adequate safety precautions are advised.
Q: What methods can shape molybdenum powder into components?
A: The main powder processing methods are press-and-sinter, metal injection molding, additive manufacturing, and thermal spraying. The method is selected based on part size, shape, and requirements.
Q: Does molybdenum powder require sintering aids?
A: For press-and-sinter processing, small amounts of nickel or iron are often added to molybdenum powder to promote sintering. Other sintering aids can also assist densification.
Conclusion
Molybdenum metal powder is a versatile high-performance material suitable for specialized applications involving high temperatures, thermal cycling, and corrosive environments where other materials are inadequate. Continued advances in molybdenum powder production and processing are expanding its utilization across more industries. With proper handling and processing, components produced from molybdenum powder can provide exceptional performance under demanding service conditions.