The world of manufacturing is undergoing a significant transformation. Traditional techniques, while well-established and reliable, are facing increasing challenges in an era that demands innovation, customization, and lightweight, high-performance parts. Enter Nickel-based powder 3D printing, a revolutionary technology that’s shaking things up. But how does it stack up against the tried-and-true methods? Buckle up, because we’re diving deep into the fascinating world of nickel-based 3D printing, comparing it head-to-head with traditional manufacturing technologies.
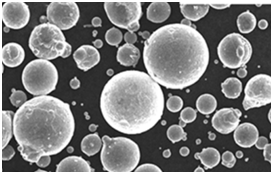
Comparison of Process Characteristics
Traditional Manufacturing: Think of it like baking a cake. You have a mold (think casting or forging), you pour in the “batter” (molten metal), and let it cool and solidify in the desired shape. Common traditional techniques for nickel alloys include:
- Casting: Molten nickel alloy is poured into a mold cavity that replicates the final part’s geometry. Once cooled, the casting is removed, and excess material is machined away.
- Forging: A heated nickel bar is hammered or pressed into a specific shape using dies. This process strengthens the grain structure of the metal.
- Machining: A solid block of nickel alloy is sculpted into the desired shape using computer-controlled cutting tools.
Nickel-Based Powder 3D Printing: Here, imagine building your cake layer by layer. A high-powered laser melts tiny nickel alloy particles together, following a digital blueprint. Let’s break down the process:
- Powder Preparation: Nickel alloy is atomized into a fine powder with specific particle size and distribution for optimal printing.
- Printing Process: A layer of powder is spread across a build platform. A laser beam selectively melts the powder particles according to the design, creating a single layer of the part. This process repeats, building the object layer by layer.
- Post-Processing: The printed part may undergo heat treatment for stress relief or improved mechanical properties. Support structures used during printing are removed.
At a Glance:
Feature | Traditional Manufacturing | Nickel-Based Powder 3D Printing |
---|---|---|
Process | Subtractive (removing material) or Additive (shaping molten metal) | Additive (building layer by layer) |
Tooling | Requires complex and expensive molds or dies | Minimal tooling needed, design data drives the process |
Design Flexibility | Limited by mold or die complexity | Highly complex and intricate geometries are achievable |
Material Waste | Can be significant, especially with machining | Minimal waste, unused powder can be recycled |
Production Volume | Ideal for high-volume production runs | More suited for low-volume, custom, or complex parts |
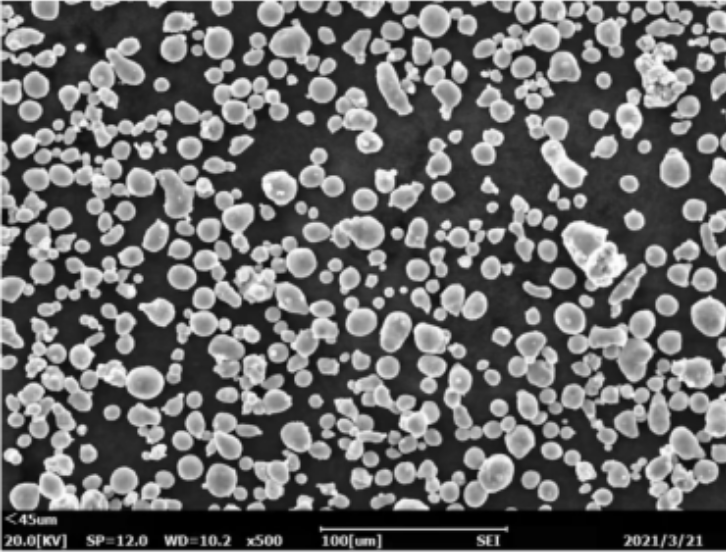
Comparison of Advantages and Disadvantages
Now that we understand the basic processes, let’s see how they fare in a head-to-head battle:
Traditional Manufacturing:
Advantages:
- Cost-effective for high volumes: For mass production of simple parts, traditional methods offer lower per-unit costs.
- Established technology: These methods have been refined over decades, resulting in reliable and predictable outcomes.
- Wide material selection: Traditional techniques can handle a broader range of metal alloys compared to 3D printing.
Disadvantages:
- Limited design complexity: Creating intricate geometries can be difficult and expensive with traditional methods.
- High upfront tooling costs: Molds and dies for casting or forging can be a significant investment.
- Material waste: Significant material removal in machining or excess material from casting can lead to higher costs and environmental impact.
Nickel-Based Powder 3D Printing:
Advantages:
- Unmatched design freedom: Highly complex geometries, internal channels, and lightweight structures are easily achievable.
- Reduced lead time: No need for complex tooling allows for faster production cycles, especially for prototypes or low-volume runs.
- Minimal material waste: Unused powder can be recycled, minimizing material consumption and environmental impact.
- Lightweight parts: The ability to create intricate internal structures allows for significant weight reduction.
Disadvantages:
- Higher cost per unit: Currently, 3D printing nickel-based alloys can be more expensive than traditional methods for high-volume production.
- Limited material selection: The range of printable nickel alloys is still evolving compared to traditional methods.
- Post-processing requirements: Printed parts may require heat treatment or support structure removal, adding to processing time.
The Verdict: There’s no clear winner here. The choice between traditional manufacturing and nickel-based powder 3D printing depends on your specific needs. For high-volume production of simple parts, traditional methods might be the better option. However, if design complexity, rapid prototyping, or lightweight parts are critical, then nickel-based powder 3D printing emerges as a compelling choice. As 3D printing technology matures, production costs are expected to decrease, making it a more viable option for a wider range of applications.
Applications of Nickel-Based Powder 3D Printing
Nickel alloys are known for their exceptional strength, high-temperature resistance, and corrosion resilience. These properties make them ideal for demanding applications in various industries:
- Aerospace: Nickel-based 3D printing is being used to create lightweight, high-strength components for jet engines, airframes, and spacecraft. The ability to produce intricate cooling channels within parts allows for improved thermal management.
Imagine a jet engine combustor. Traditionally, this critical component is a complex assembly of many parts. Nickel-based 3D printing allows engineers to create a single, intricate combustor with internal cooling channels, reducing weight and complexity while improving performance.
- Oil & Gas: Nickel alloys can withstand harsh downhole environments. 3D printing enables the creation of custom well components, flow control devices, and even downhole tools with complex internal features for enhanced functionality.
Think about a downhole pressure sensor. Traditionally, this would be a complex machined component. 3D printing allows for a lighter, more intricate design with internal channels for fluid flow and pressure measurement, all within a single piece.
- Medical: Biocompatible nickel alloys are finding use in implants and prosthetics. 3D printing allows for customized designs that perfectly match a patient’s anatomy, leading to improved fit and function.
- Automotive: Nickel-based 3D printing is being explored for creating high-performance components like pistons, connecting rods, and even brake calipers. The ability to design lightweight structures with high strength is particularly attractive for the automotive industry.

The Future of Nickel-Based Powder 3D Printing
The future of nickel-based powder 3D printing is bright. As research and development continue, we can expect to see:
- Reduced production costs: Advancements in printing technology and materials are expected to bring down the cost per unit, making 3D printing more competitive for broader applications.
- Expanded material selection: The range of printable nickel alloys will continue to grow, offering engineers more options for specific performance needs.
- Faster printing speeds and larger build volumes: Advancements in printing technology will lead to faster printing times and the ability to create larger and more complex parts.
- Integration with other technologies: 3D printing might be combined with other advanced manufacturing techniques like machining or surface finishing for a complete solution.
FAQ
Here are some frequently asked questions about nickel-based powder 3D printing:
Question | Answer |
---|---|
What are the surface finish characteristics of nickel-based 3D printed parts? | The surface finish can vary depending on the printing process and post-processing techniques. Parts may require additional machining or polishing to achieve a desired surface finish. |
Can nickel-based 3D printed parts be welded or joined to other components? | Yes, nickel-based 3D printed parts can be welded using specialized techniques. However, the weldability can vary depending on the specific alloy and printing parameters. |
What are the environmental benefits of nickel-based 3D printing? | Compared to traditional methods, 3D printing offers reduced material waste and lower energy consumption due to minimal material removal. |
Is nickel-based 3D printing safe? | Nickel powder can be a health hazard if inhaled. Proper safety protocols and ventilation systems are essential when working with nickel powder in a 3D printing environment. |
In Conclusion
Nickel-based powder 3D printing is a transformative technology with the potential to revolutionize various industries. While it may not replace traditional manufacturing entirely, it offers unique advantages for applications requiring complex geometries, lightweight parts, and rapid prototyping. As the technology matures and costs decrease, we can expect to see nickel-based 3D printing play an increasingly significant role in the future of manufacturing.