Introduction
Welcome to the world of Metal Injection Molding, commonly known as the MIM process. In this article, we will explore the MIM process, its history, applications, advantages, and challenges. MIM is a revolutionary manufacturing technique that combines the benefits of plastic injection molding with powder metallurgy, offering precision and complexity in producing metal components.
What is MIM Process?
The MIM process is a manufacturing method used to create intricate metal parts with high accuracy and repeatability. It is an ideal solution for producing complex components in large quantities without the need for extensive machining. The MIM process begins with fine metal powders mixed with a binder to create a feedstock, which is then molded into the desired shape.
The History of MIM Process
The MIM process has its roots in the plastic injection molding industry, which dates back to the late 1800s. However, the application of MIM to metals didn’t gain significant attention until the 1970s. Over the years, advancements in materials, technology, and process optimization have turned MIM into a commercially viable and widely used manufacturing technique.
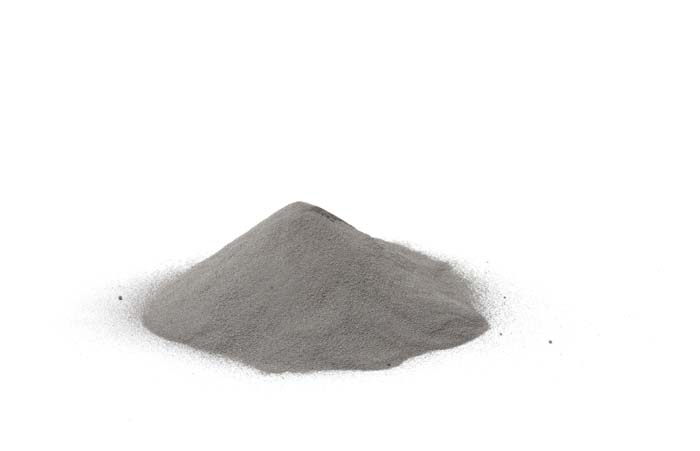
How Does the MIM Process Work?
Step 1: Feedstock Preparation
The first step in the MIM process involves preparing the feedstock. Metal powders are combined with a thermoplastic binder to create a homogeneous mixture. This mixture is then pelletized, creating granules that are ready for injection molding.
Step 2: Injection Molding
In this stage, the feedstock pellets are heated and injected into a mold cavity with the desired shape. The injection molding process gives the flexibility to create intricate geometries with tight tolerances.
Step 3: Debinding
After the injection molding, the green part contains both the metal powder and the binder. The next step is to remove the binder through a debinding process, leaving behind a porous structure known as a brown part.
Step 4: Sintering
The final step is sintering, where the brown part is subjected to high temperatures in a controlled atmosphere. During sintering, the metal particles fuse together, resulting in a fully dense and high-strength metal component.
Advantages of MIM Process
The MIM process offers several advantages over traditional manufacturing methods. Let’s explore some of them:
Precision and Complexity
The MIM process enables the production of complex shapes and geometries with high precision, reducing the need for secondary operations and machining.
Material Versatility
MIM can utilize a wide range of metals and alloys, providing designers with the flexibility to choose the most suitable material for the application.
Cost-Effectiveness
MIM is a cost-effective solution for mass-producing intricate metal components, especially when compared to traditional machining methods.
Time Efficiency
The ability to create multiple components in a single molding cycle significantly reduces the manufacturing time, making MIM an efficient process.
Reduced Waste
With minimal material wastage during the MIM process, it contributes to a more sustainable and environmentally friendly manufacturing approach.
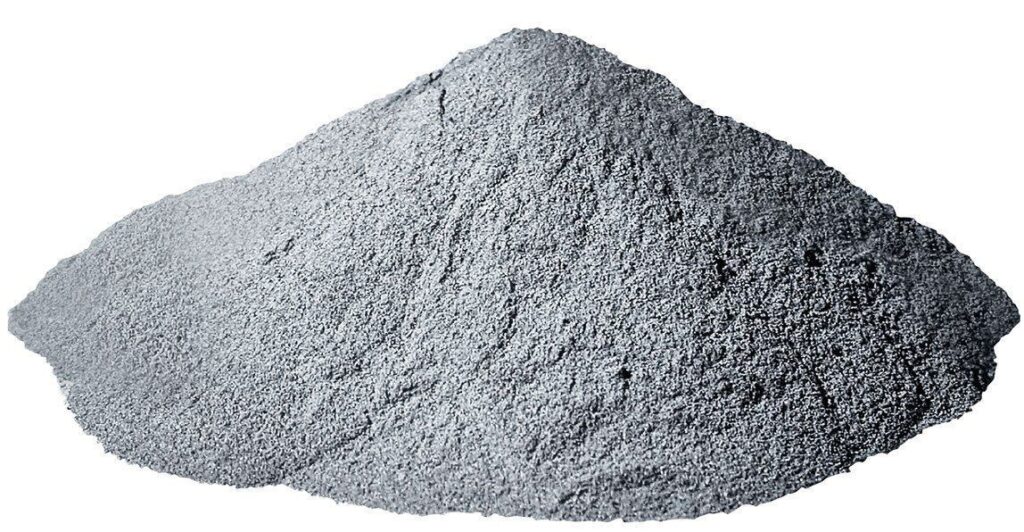
Applications of MIM Process
The versatility and precision of the MIM process make it suitable for various industries. Some of the common applications include:
Aerospace Industry
The aerospace sector benefits from MIM’s ability to create lightweight, high-strength components that meet strict industry standards.
Medical Devices
MIM is widely used in manufacturing intricate medical devices with complex geometries, ensuring high quality and accuracy.
Automotive Components
The automotive industry relies on MIM for producing components such as gears, sensors, and fuel injection nozzles.
Electronics
MIM finds applications in electronics manufacturing, producing connectors, contacts, and other miniaturized components.
Firearms and Defense
In the firearms and defense industry, MIM is used to create small, intricate parts that contribute to the overall performance of the equipment.
Comparison with Traditional Manufacturing Methods
Injection Molding vs. MIM Process
Both injection molding and MIM are capable of producing complex parts, but the latter offers the advantage of working with metal materials, providing higher strength and durability.
CNC Machining vs. MIM Process
CNC machining is subtractive manufacturing, while MIM is additive. MIM can produce intricate shapes without the material wastage associated with CNC machining.
Powder Metallurgy vs. MIM Process
Powder metallurgy and MIM share similarities, but the MIM process allows for greater complexity and precision in the final product.
Challenges and Limitations of MIM Process
Despite its advantages, the MIM process has some challenges and limitations that need to be considered:
Material Constraints
Not all metals can be used in the MIM process, limiting the range of materials available for specific applications.
Design Limitations
Certain design features may be challenging to achieve due to the limitations of the molding and sintering processes.
Surface Finish and Tolerance
Achieving tight tolerances and specific surface finishes might require additional post-processing steps.
High Initial Investment
Setting up MIM production can be capital-intensive, making it less suitable for low-volume productions.
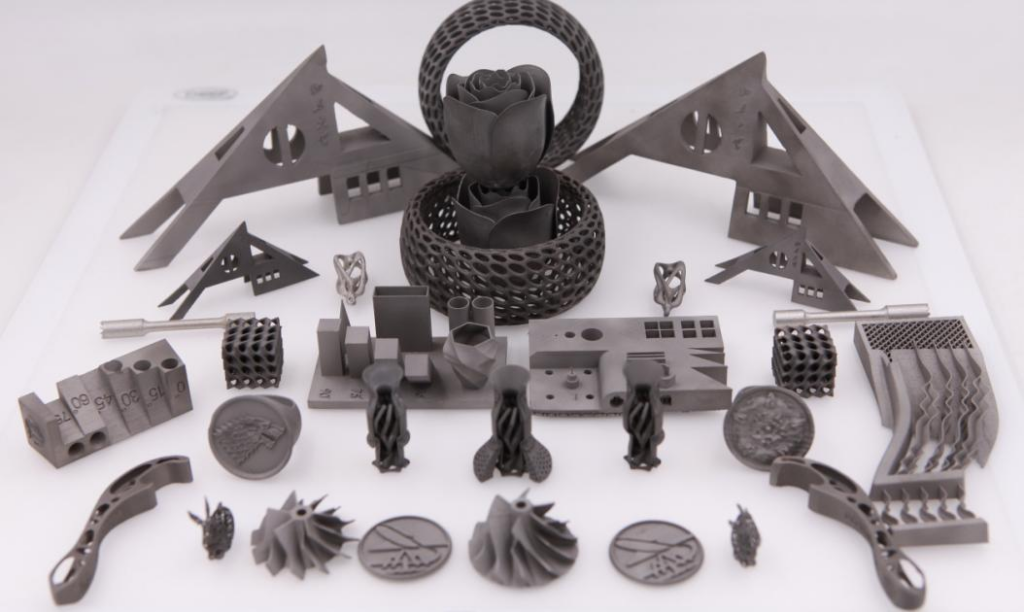
Future Trends in MIM Process
As technology advances, several trends are shaping the future of the MIM process:
Advanced Materials
Research is ongoing to expand the range of materials available for the MIM process, including superalloys and high-performance ceramics.
Miniaturization
With the demand for smaller and more intricate components, MIM is likely to find increasing use in miniaturized applications.
Industry 4.0 Integration
Industry 4.0 concepts, such as data-driven production and automation, are expected to enhance the efficiency and productivity of the MIM process.
Sustainability and MIM Process
MIM also offers environmental benefits and contributes to sustainability in manufacturing:
Reduced Carbon Footprint
The energy-efficient MIM process results in lower greenhouse gas emissions compared to traditional manufacturing methods.
Recycling and Reusing
MIM allows for the recycling of metal powders and the reuse of scrap materials, reducing overall waste.
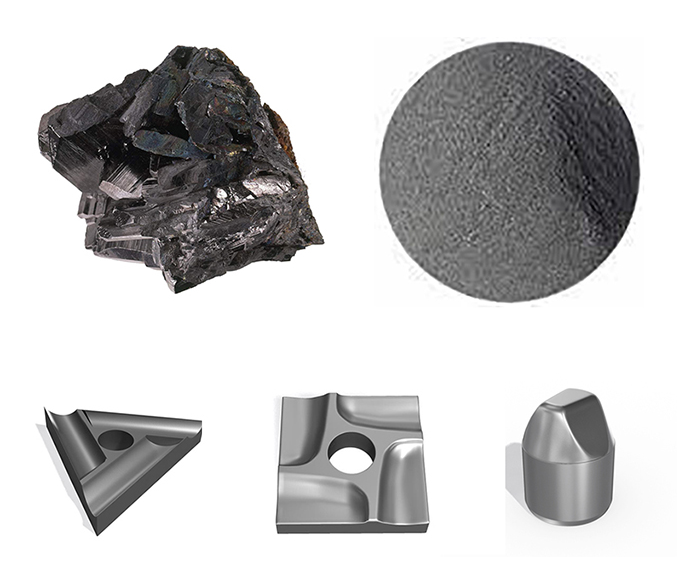
Conclusion
The MIM process has revolutionized the way complex metal components are manufactured. By combining the advantages of plastic injection molding and powder metallurgy, MIM offers precision, material versatility, cost-effectiveness, and reduced waste. It finds applications in various industries, including aerospace, medical, automotive, electronics, firearms, and defense.
Despite its advantages, the MIM process does have some challenges and limitations, such as material constraints and design limitations. However, ongoing research and advancements in technology promise to overcome these limitations and open up new possibilities for the future of MIM.
In the pursuit of sustainability, the MIM process plays a crucial role in reducing the carbon footprint of manufacturing. By minimizing material wastage and offering recycling opportunities, MIM aligns with the principles of environmental responsibility.
As we move forward, the MIM process will continue to evolve, driven by innovations in materials, miniaturization, and industry 4.0 integration. The manufacturing landscape will witness the growing prominence of MIM as a go-to solution for intricate metal component production.
FAQs
- What industries benefit the most from the MIM process?
- Industries such as aerospace, medical devices, automotive, electronics, firearms, and defense benefit significantly from the MIM process due to its ability to create complex and precise metal components.
- How does MIM compare with traditional manufacturing methods like CNC machining and injection molding?
- MIM offers distinct advantages over traditional methods, including cost-effectiveness, reduced material wastage, and the ability to produce intricate shapes and geometries.
- Is the MIM process environmentally friendly?
- Yes, the MIM process contributes to environmental sustainability by reducing material wastage, minimizing energy consumption, and offering recycling opportunities.
- What are the limitations of the MIM process?
- Some limitations include material constraints, design limitations, surface finish, tolerance challenges, and high initial investment costs.
- What are the future trends in the MIM process?
- The future of MIM involves advancements in materials, miniaturization, and integration with Industry 4.0 concepts, such as automation and data-driven production.