Introduction
Inconel has long been revered as a formidable material in various industries due to its exceptional properties, but the emergence of 3D printing has taken its utility to new heights. This article delves into the world of Inconel 3D printing, exploring its advantages, challenges, applications, and its potential to reshape the future of manufacturing.
What is Inconel?
Before we explore the world of Inconel 3D printing, it’s essential to understand what Inconel is. Inconel is a family of superalloys known for their remarkable resistance to corrosion, heat, and extreme environments. These alloys are primarily composed of nickel, chromium, and other elements, making them ideal for high-temperature applications and harsh conditions.
The Rise of 3D Printing
The advent of 3D printing, also known as additive manufacturing, has transformed the traditional manufacturing landscape. The technology allows for the creation of complex geometries and customized designs, reducing material waste and lead times significantly. This has opened up new possibilities for utilizing materials like Inconel in ways that were previously unfeasible.
Inconel in Traditional Manufacturing
Inconel has been extensively used in traditional manufacturing processes like casting, forging, and machining. While it has proven its worth in critical applications, these methods often come with limitations in terms of design flexibility and lead times. This is where Inconel 3D printing comes into play, overcoming the constraints of traditional techniques.
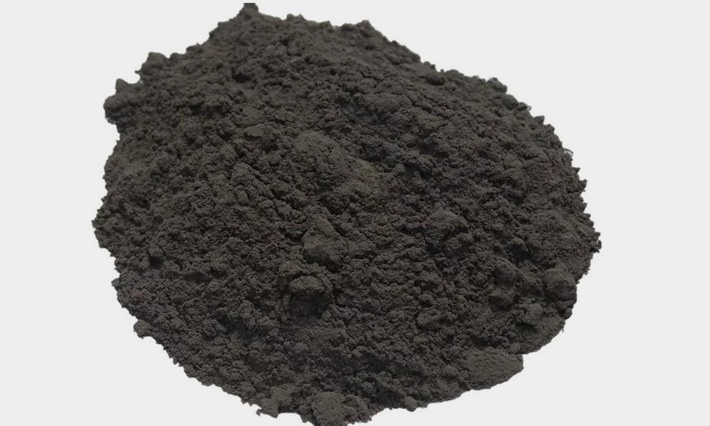
Advantages of Inconel 3D Printing
Design Flexibility
One of the most significant advantages of Inconel 3D printing is the unparalleled design flexibility it offers. Complex geometries, including lattice structures and internal channels, can be effortlessly fabricated, opening up new possibilities for engineers and designers.
Reduced Material Waste
Traditional manufacturing methods often lead to significant material wastage. In contrast, 3D printing is an additive process, where material is deposited layer by layer, reducing wastage to a minimum. This makes Inconel 3D printing more environmentally friendly and cost-effective.
Rapid Prototyping
Inconel 3D printing enables rapid prototyping, allowing engineers to quickly iterate and improve their designs. This accelerates the product development cycle and saves valuable time in bringing new products to the market.
Complex Geometries
With Inconel 3D printing, the limitation of traditional manufacturing to produce intricate geometries is no longer a concern. The technology allows for the creation of highly complex and sophisticated parts, unlocking new frontiers in engineering.
Customization
Every industry has unique requirements, and Inconel 3D printing empowers manufacturers to customize parts according to specific needs. This level of personalization can lead to better performance and enhanced functionality.
Challenges in Inconel 3D Printing
High Material Cost
As with any advanced material, Inconel comes with a higher price tag compared to conventional metals. The cost of Inconel powder and filament used in 3D printing can be a significant factor in the overall production expenses.
Process Complexity
Inconel 3D printing is a complex process that demands strict control over parameters such as temperature, atmosphere, and cooling rates. Any deviation from optimal conditions can result in defects and compromise the mechanical properties of the final product.
Post-Processing Requirements
While 3D printing is lauded for its near-net-shape capabilities, most Inconel parts require post-processing treatments to achieve the desired material properties and surface finish. This can add extra steps and time to the manufacturing process.
Surface Finish
Inconel 3D-printed parts often have a rough surface finish, which may not be acceptable in certain applications. Additional post-processing techniques, such as machining or polishing, might be necessary to achieve the desired surface quality.
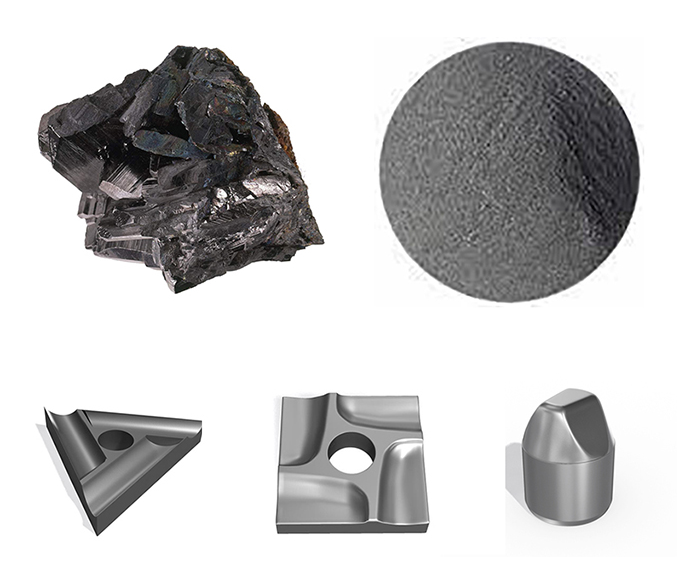
Applications of Inconel 3D Printing
Aerospace Industry
The aerospace sector demands materials that can withstand extreme temperatures and harsh environments. Inconel 3D printing has found extensive use in manufacturing turbine blades, fuel nozzles, and other critical components.
Healthcare Sector
Inconel’s biocompatibility and corrosion resistance make it a valuable material for medical applications. 3D printing allows the production of patient-specific implants and surgical instruments with high precision.
Automotive Applications
In the automotive industry, lightweight and high-strength materials like Inconel are sought after. 3D-printed Inconel parts contribute to improved fuel efficiency, performance, and overall vehicle durability.
Oil and Gas Sector
The oil and gas industry requires materials capable of withstanding aggressive environments. Inconel’s resistance to corrosion and high temperatures makes it an attractive choice for downhole tools and components.
Future Prospects
The future of Inconel 3D printing looks promising as the technology continues to advance. Further research and development may lead to cost reduction, improved process efficiency, and expanded material choices.
Inconel vs. Other Metals in 3D Printing
While Inconel is a prominent player in the 3D printing arena, it is essential to compare it with other metals like titanium and stainless steel to understand its advantages and limitations.
Tips for Successful Inconel 3D Printing
Achieving success with Inconel 3D printing requires careful planning and execution. These tips will help manufacturers optimize their processes and produce high-quality components.
Environmental Impact
As industries strive to become more environmentally conscious, understanding the environmental impact of materials like Inconel is crucial. Inconel 3D printing, despite its advantages, also brings certain environmental considerations.
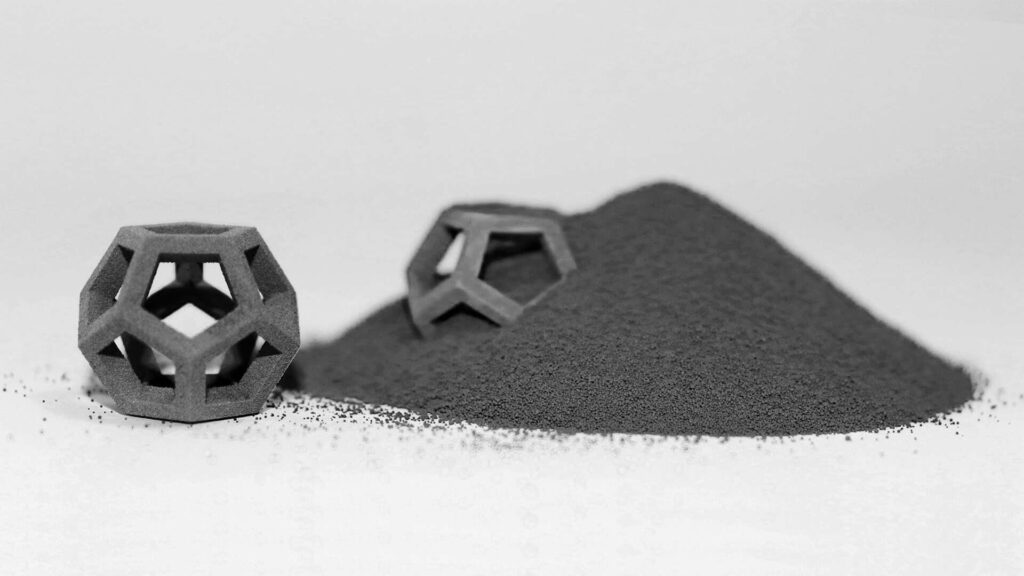
Conclusion
Inconel 3D printing represents a revolutionary shift in the world of manufacturing. The combination of Inconel’s exceptional properties with the design freedom and rapid prototyping capabilities of 3D printing opens up new possibilities across various industries. From aerospace to healthcare and automotive to oil and gas, the applications of Inconel 3D printing continue to expand.
While the technology offers numerous benefits, it also faces challenges, such as high material costs and post-processing requirements. However, ongoing research and advancements in 3D printing technology are likely to address these challenges, making Inconel 3D printing even more accessible and cost-effective.
As we move forward, it’s essential for industries to adopt sustainable practices, including responsible material usage and efficient manufacturing processes. Inconel 3D printing presents an opportunity for manufacturers to reduce material waste and energy consumption, contributing to a greener future.
FAQs
13.1 Is Inconel suitable for high-temperature applications?
Yes, Inconel is highly suitable for high-temperature applications due to its exceptional heat resistance and mechanical properties.
13.2 Can Inconel 3D-printed parts replace traditional manufacturing components?
In some cases, yes. Inconel 3D-printed parts offer unique advantages, such as design flexibility and rapid prototyping, but there are still certain applications where traditional manufacturing methods may be more appropriate.
13.3 What are the key considerations for Inconel 3D printing in aerospace applications?
In aerospace applications, factors like material integrity, mechanical properties, and surface finish are critical. Strict process control and post-processing treatments may be necessary to meet the stringent requirements of the aerospace industry.
13.4 How does the cost of Inconel 3D printing compare to traditional manufacturing costs?
The cost of Inconel 3D printing can be higher initially due to the expense of Inconel powder or filament. However, in many cases, the advantages of reduced material waste and shorter lead times can offset the initial costs.
13.5 What post-processing methods are commonly used for Inconel 3D-printed parts?
Common post-processing methods for Inconel 3D-printed parts include heat treatment, machining, and surface finishing techniques like polishing or shot peening.