Laser additive manufacturing technology is a manufacturing method that uses laser as the heat source and uses the high-energy beam focusing effect of laser to quickly melt metal powder.
Due to the high energy density of laser, it can realize the manufacturing of difficult-to-machine metals, such as titanium alloys and high-temperature alloys used in aerospace, etc. Laser additive manufacturing technology also has the advantage of not being limited by the structure of the parts, which can be used for the processing and manufacturing of complex structures, difficult processing and thin-walled parts.
At present, laser additive manufacturing technology has been applied to materials covering titanium alloys, high-temperature alloys, iron-based alloys, aluminum alloys, refractory alloys, amorphous alloys, ceramics and gradient materials, etc. It has significant advantages in the manufacture of high-performance complex components in the aerospace field and porous complex structures in the biomanufacturing field.
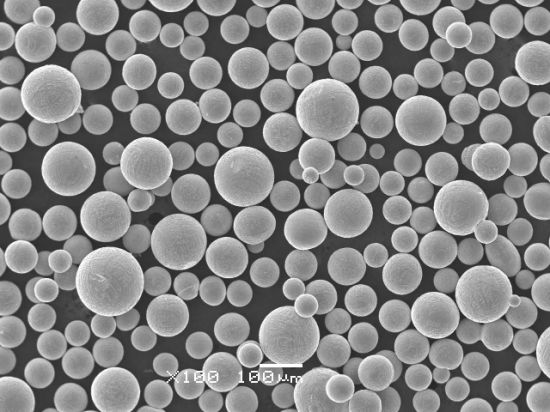
Additive manufacturing technology with laser as the heat source is mainly divided into laser deposition process based on powder feeding and laser selected area melting technology based on powder spreading.
Due to the different names of the units, the powder feeding-based laser melting deposition technology is also known as directed energy deposition, DED, laser solid forming, LSF, direct metal deposition, DMD, laser melting deposition, LMD, etc. Regardless of the name, the principle is to use the basic principle of rapid prototyping, using metal powder as the raw material, using a high-energy laser as the energy source, in accordance with the predetermined processing path, the synchronization of the metal powder given to the layer by layer melting, rapid solidification and layer by layer deposition, so as to achieve the direct manufacturing of metal parts.

Typically, the laser metal forming system platform consists of a laser, CNC table, powder feed nozzle, high precision adjustable powder feeder and other auxiliary devices as shown in the figure below. The lasers available for the pattern preparation process are mainly divided into semiconductor continuous lasers, fiber continuous lasers, CO2 continuous lasers and YAG:Nd pulsed lasers according to the beam pattern. According to the placement of nozzles, mainly divided into coaxial powder feeding nozzle group and lateral powder feeding nozzle.
Laser selective melting technology uses high brightness laser to directly melt metal powder material without binder, and 3D models are directly formed into any complex structural parts with comparable performance to forgings, and the parts only need surface finishing to be used. The main laser additive technologies include Selective Laser Melting (SLM), powder bed deposition process, etc.
The basic principle of laser zone melting is that the laser beam is scanned according to a pre-planned path to melt the pre-laid metal powder; after completing a level of scanning, the working chamber drops a layer in height and the powder layer re-laid a layer of powder, and so on repeatedly, layer by layer, until the required metal parts are manufactured, the whole process is in a vacuum environment, which can effectively avoid the influence of harmful impurities in the air.
The laser selective melting process can be directly made into end metal products, eliminating the intermediate transition. The prepared parts have high dimensional accuracy and good surface roughness (Ra 10~30μm) which is suitable for various complex shapes of workpieces, especially for complex workpieces with complex internal shaped structures. It cannot be manufactured by traditional methods; suitable for single and small batch complex structural parts without mold, rapid The machine is suitable for single-piece and low-volume complex structural parts without mold and rapid response manufacturing.