3D printing, also known as additive manufacturing, is a process of making three dimensional solid objects from a digital file. The creation of a 3D printed object is achieved using additive processes. In an additive process, an object is created by laying down successive layers of material until the object is created. Each of these layers can be seen as a thinly sliced horizontal cross-section of the eventual object.
3D printing is the opposite of subtractive manufacturing which is cutting out / hollowing out a piece of metal or plastic with for instance a milling machine.
3D printing enables you to produce complex (functional) shapes using less material than traditional manufacturing methods.
How 3D Printing Works
The 3 basic steps in the 3D printing process are:
- Designing and digitally modeling the object you want to create
- Preparing and setting up the 3D printer
- Printing the object layer by layer
Designing The 3D Model
The first step in 3D printing is to make a virtual design of the object you want to build. 3D modeling software enables you to make this design.
Popular 3D modeling software includes:
- Blender
- AutoCAD
- SketchUp
- Fusion 360
- Tinkercad
- 3ds Max
- Maya
3D scanners can also be used to create a digital model by scanning an existing object. The obtained scan data is then converted into a 3D model.
CAD (computer-aided design) software is often used for modeling machine parts and tools. The design is made up of 2D sketches which are extruded or revolved into 3D objects.
After the digital model is completed, 3D printer software slices the model into hundreds or thousands of horizontal layers.
The sliced file shows the path the print head has to follow to recreate the object layer by layer. The file also contains information on infill patterns and material densities.
Slicing software takes parameters such as layer height, infill percentage, and print speed into account when it creates the printing layers.
Popular slicing software includes:
- Cura
- Slic3r
- Simplify3D
- KISSlicer
Preparing The 3D Printer
To prepare a 3D printer, the fabrication stage needs to be leveled and the right printing material should be loaded.
- For filament printers, the filament guide tube is threaded through to the extruder.
- For powder bed printers, the powder reservoir is filled.
- Resin tanks are filled with liquid resin in the case of stereolithography printers.
The right print bed surface should be installed and prepared according to the material being printed. Examples include painter’s tape, PEI sheets, glue, etc.
Once the 3D printer is set up with the right material, the sliced file is transferred to the printer. This can be done via USB stick, Wi-Fi, or wired connection.
The final preparation step is to adjust the settings in the printer software, such as:
- Print resolution
- Print speed
- Supports
- Cooling fan speed
- Bed temperature
- Extruder temperature
- And various other custom settings
When the print is started, the first layer is printed onto the build platform. The rest of the object is then built up layer by layer until completion.
How The Layers Are Formed
There are several ways layers can be formed in 3D printing to construct an object. The main 3D printing technologies are briefly explained below.
Material Extrusion
Material extrusion, also known as Fused Deposition Modeling (FDM), is the most common consumer 3D printing technology. It’s used by affordable home 3D printers.
In FDM, thermoplastic filament such as PLA, PETG, or ABS is unwound from a coil and fed into an extruding nozzle head. The nozzle can move in both horizontal and vertical directions by the use of precisely controlled motors.
The nozzle heats up the filament above its melting point and extrudes it onto the build platform (or the latest printed layer) where it hardens. The object is built up layer by layer, where each layer solidifies and adheres to the layer below.
Supports structures are built-up during overhangs and bridging. After the print finishes, the support structure can be removed.
The most popular application of FDM is in prototyping.
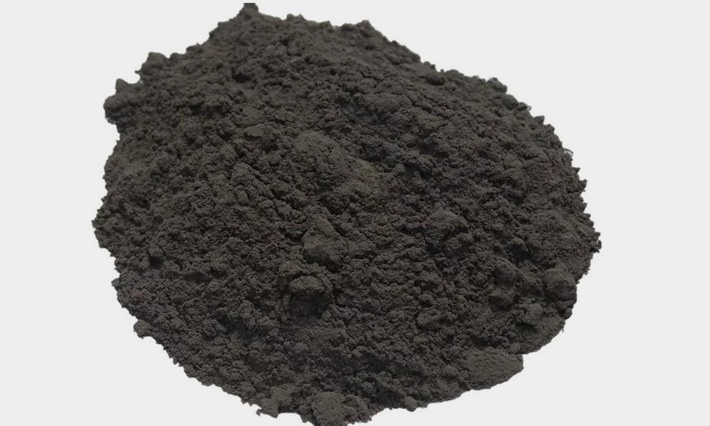
VAT Polymerization
The most common technology in VAT polymerization is stereolithography (SLA).
SLA uses a container filled with liquid photopolymer resin which is hardened by a UV laser.
The build platform is situated just below the surface of the resin tank. The laser beam traces out the pattern of the first layer on the liquid resin which solidifies.
The platform then raises slightly and the laser traces out the next layer just above the previous one. This continues until the full object has been constructed.
Excess fluid resin is continuously drained. After printing, the object needs to be rinsed in a solvent to remove excess resin.
Supports are needed during printing but are relatively easy to detach after printing due to the resin’s properties.
The smooth printing layer lines combined with the self-leveling properties of the resin enable this process to create highly accurate parts with excellent surface quality.
SLA is often used for assemblies, prototypes and end-use parts.
Powder Bed Fusion
Powder bed fusion works by selectively fusing regions of a powder bed. The most common technologies are:
Selective Laser Sintering (SLS): Uses a high power laser to fuse small particles of polymer powder. The powder is spread evenly across a build platform with a roller or blade. The laser selectively sinters powder particles in the cross-section of the object. After a layer is finished the platform lowers, more powder is spread across the bed and the process repeats until the part is finished. Excess powder supports the object during printing and does not require any other support structures.
Selective laser melting (SLM): SLM is similar to SLS but uses metal powder instead of plastics. The high-power laser melts the metal powder rather than sintering it. Titanium alloys, tool steels, stainless steel and aluminium are often used in SLM.
Electron Beam Melting (EBM): Uses an electron beam instead of a laser to selectively melt metal powder layers. Build rates are fast but the process requires a vacuum which makes EBM expensive. Commonly used for medical implants and aerospace components.
Material Jetting
Material jetting is often referred to as PolyJet printing and works similarly to 2D inkjet paper printers. But instead of jetting drops of ink onto paper, UV-curable photopolymer resin is jetted onto a build platform.
The layers are cured with UV light after each pass of the print head. Uncured resin is removed at the end of the build process leaving only the solid 3D object.
Support structures are also printed, in a removable gel-like material, whenever required.
Material jetting allows for multi-material prints by using multiple print heads. Some materials are rubber-like, transparent or high temperature resistant.
Accuracy is excellent and layer lines are hard to see. The process enables the creation of highly detailed objects. Material jetting is primarily used for rapid prototyping.
Binder Jetting
In binder jetting two materials are used:
- A powder based material such as sandstone, ceramics, stainless steel or cobalt-chrome.
- A binder which is a liquid bonding agent.
The binder is selectively dropped onto the powder bed to bind the powder particles together. The build platform lowers, powder is spread across the bed using a roller and the process repeats.
Once printing is finished, unbound excess powder is removed, leaving only the bound object. Sintering can be done as a final step to increase part density, strength and smoothness.
This process allows for fast print speeds and the printing of large objects. Binder jetting is applicable to sand casting, metal casting and ceramics. It’s also used in full color printing.
Sheet Lamination
In laminated object manufacturing (LOM), sheets of material are bonded to form an object. The most common material is paper.
A laser cuts each sheet of paper into the shape required for that particular layer.
The cut paper is then laminated onto the previous layer using heat and pressure. Lasers cut cross-hatch patterns into the laminated layers for better adhesion.
Once the object is finished, excess material is cut away. LOM produces inexpensive prototypes and custom paper products.
Directed Energy Deposition
Direct metal deposition methods fuse metal as it is being deposited. A nozzle extrudes metal powder or wire which is met with a high-energy laser or electron beam at the extrusion point.
The heat source melts the material to deposit beads of molten metal onto a base plate or existing part.
The nozzle and heat source can be moved across the x, y and z axes to deposit material exactly where needed. Excess material acts as support during printing.
DED methods enable repairs and modifications of existing metal parts. This also allows hybrid manufacturing by combining additive and subtractive techniques.
Materials Used in 3D Printing
Many different materials can be used for 3D printing. The available materials depend on the printing process.
Plastics
The most common plastics used in 3D printing are:
- ABS: Durable, impact resistant plastic. Used for functional prototypes and end-use products.
- PLA: Made from corn starch, PLA is biodegradable. Used for prototyping and hobbyist printing.
- PETG: Stronger than PLA, PETG is often used to make tooling and products that require higher strength.
- Nylon: Engineering-grade nylon filaments have high strength, toughness and wear resistance. Often used for end-use parts.
- Polycarbonate: Extremely strong with heat resistance up to 110oC. Used for durable finished products.
- Photopolymer resins: Used in SLA, PolyJet and similar vat processes. Resins provide excellent accuracy and surface finish.
Other specialized plastics include conductive PLA and ABS, PVA supports, high-temperature thermoplastics (PEEK, PEI, PEKK), flexible resins (TPU), composite materials, and more.
Metals
Various metals widely used in 3D printing include:
- Aluminum: Lightweight but strong. Used in aerospace applications.
- Stainless steel: Corrosion resistant metal suitable for products requiring high strength and sterilizability.
- Titanium: Extremely strong with low density. Used for medical implants and aerospace components.
- Cobalt-Chrome: Biocompatible metal often used for dental implants and orthopaedic implants.
- Nickel Superalloys: Heat resistant alloys used in parts for turbines and aircraft engines.
- Precious metals: Gold, silver and platinum jewelry can be 3D printed.
Other Materials
A range of other materials 3D printed include:
- Sandstone: Printed with binder jetting for casting and architectural purposes.
- Ceramics: Used in technical ceramic engineering components.
- Wax: Suitable for jewelry patterns and casting.
- Concrete: Printed buildings and architectural constructions.
- Food: Chocolate, cookies, pasta, and other foods can be printed.
- Cells: Organ printing uses bio-ink spheroids containing living cells.
- Composites: Mixtures of metals, plastics and ceramics can be printed.
As 3D printing technology develops, more and more materials become printable. Research is ongoing into areas such as glass, fabric textiles and electronics printing.
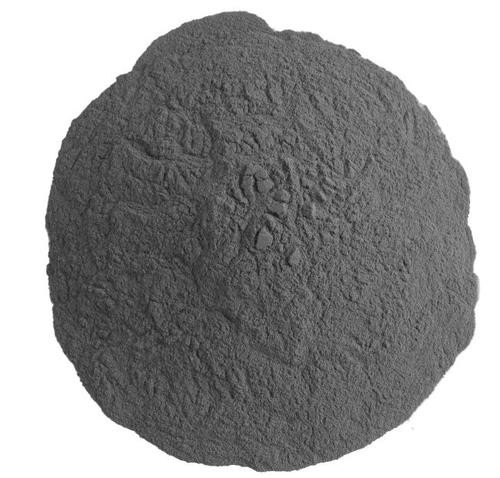
Key Benefits of 3D Printing
3D printing provides several advantages over traditional manufacturing:
- Design freedom – Unique and complex geometries are printable that are not possible with injection molding or machining. Light-weighting and part consolidation also enables improved functionality.
- Customization – Mass customization and personalization is possible by modifying digital CAD files for each print. Small custom batches and tailored products can be produced.
- Speed – Prototyping happens rapidly within days compared to weeks using conventional techniques. Parts can also be produced on-demand when needed.
- Cost efficiency – Eliminating tooling in manufacturing results in lowered costs for small batch productions. Material waste is reduced by only using required amounts.
- Decentralized manufacturing – Digital part files can be sent quickly and cheaply to 3D printers distributed globally. Enables on-site manufacturing and repairs.
- Innovation – Complexity is free and trial-and-error prototyping fosters increased innovation opportunities. Products can be improved iteratively.
3D printing enables new manufacturing possibilities not achievable using legacy methods. It has found applications in healthcare, dental, automotive, aerospace, architecture, jewelry, and many other sectors.
Applications of 3D Printing
3D printing technology has many applications across different industries. Here are some of the main application areas:
- Prototyping – Rapidly iterate and optimize product designs. Validate functionality, fit and manufacturability.
- Tooling – 3D print production tools like jigs, fixtures, inspection gauges and assembly aids for the manufacturing floor.
- Part production – End-use parts can be additively manufactured for custom or small batch orders. Reduces operational costs.
- Aerospace – Aircraft and rocket manufacturers print lightweight parts to reduce fuel usage. Also used for on-demand spare parts.
- Automotive – Automakers use 3D printing for prototyping and to produce specialized low-volume parts. Customized interiors and air ducts are also printed.
- Healthcare – Custom prosthetics, implants and anatomical models assist doctors and improve surgical planning. Printed pharmaceuticals provide more accurate dosing.
- Education – Schools utilize 3D printers for teaching design principles. Students can get hands-on with technology.
- Construction – 3D printed houses and concrete structures are taking shape. On-site automated construction enables unique architectures.
- Food – 3D printers produce customized chocolates, snack foods and intricate cake decorations. Nutritional meals can be printed for space travel.
- Fashion – Several designers now integrate 3D printing into their footwear and clothing lines. Accessories and jewelry are also manufactured.
- Art & Design – Artists use 3D printing for sculptures, light fixtures, furniture and other expressive pieces. The technology provides limitless creative potential.
These are just some of the many applications 3D printing provides. As the capabilities of additive manufacturing improves, more industries will adopt the technology.
The Future of 3D Printing
3D printing technology has developed tremendously over the past decade. However, it still has lots of room and potential to grow. Here are some of the advancements we can expect:
- Materials expansion – More engineering materials like high-performance polymers and metal alloys will become printable. Biocompatible materials will progress medical 3D printing applications. Electronics printing will enable smart components and IoT devices.
- System size – Larger scale systems will accommodate printing full-size human-scale objects in one piece. Smaller systems will provide desktop manufacturing solutions.
- Speed & resolution – Faster build rates will enable mass-manufacturing. Improved resolution will increase geometric complexity and surface finish. Additional print heads will allow multi-material sophistication.
- Industry 4.0 integration – 3D printing systems will integrate with the digital thread across the product lifecycle. Design, simulation, production, quality control and part tracking will become more automated.
- Distributed manufacturing – Increased adoption of localized production. Engineers can print customized designs on-location for replacements and repairs. Reduces shipping costs and environmental impact.
- Construction & architecture – Large-scale 3D printers will help construct future infrastructures using concrete and custom composites. Unique structural shapes will be printable.
3D printing technology will transform manufacturing towards a more sustainable, distributed and customer-centric model. It empowers businesses to unlock greater innovation capabilities while saving time and money.
FAQ
How does 3D printing work?
3D printing works by building up objects layer by layer using an additive process. A digital 3D model is sliced into layers and the printer deposits material in each cross section until the part is complete. Technologies like fused deposition modeling, stereolithography, selective laser sintering, and others are used.
What materials can you 3D print with?
3D printing can use plastics like ABS, PLA, PETG, nylon, and photopolymers. Metals like stainless steel, aluminum, titanium, cobalt-chrome, and precious metals can be printed. Other materials include sandstone, ceramics, wax, concrete, food, and bio-inks. New materials are continually being introduced.
What are the benefits of 3D printing?
Benefits of 3D printing include:
- Design freedom to make complex shapes
- Customization and personalization of products
- Rapid prototyping and validation of designs
- Lower costs for small batch manufacturing
- Ability to decentralize manufacturing
- Less material waste and optimized designs
- Innovation through iterative development
What are the applications of 3D printing?
3D printing has many applications across industries:
- Prototyping product designs
- Manufacturing custom end-use parts
- Producing specialized tooling
- Aerospace and automotive components
- Customized medical devices and implants
- Pharmaceutical research and drug dosing
- Teaching and educational aids
- Construction of houses and buildings
- Food printing customized meals
- Fashion and costume accessories
- Art sculptures and design pieces
What is the future of 3D printing?
The future of 3D printing includes:
- Expanded material capabilities and electronics printing
- Larger and smaller scale systems
- Increased speed and resolution
- Integration of 3D printing into digital manufacturing
- Growth of distributed localized production
- Construction of infrastructure and architectural structures