Introduction
Inert gas atomization has emerged as a cutting-edge technology in the field of powder metallurgy and advanced materials production. By transforming molten metal into fine spherical powders, this process offers superior material properties and enhanced product performance. In this article, we explore the ins and outs of inert gas atomization, its advantages, applications, and its significance in modern manufacturing.
What is Inert Gas Atomization?
Inert gas atomization is a specialized technique used to produce metal powders with a high degree of purity and uniformity. It involves the conversion of molten metal into droplets and their subsequent solidification into fine particles under the influence of an inert gas, such as nitrogen or argon. The resulting powders exhibit remarkable flowability and excellent packing density, making them ideal for various applications.
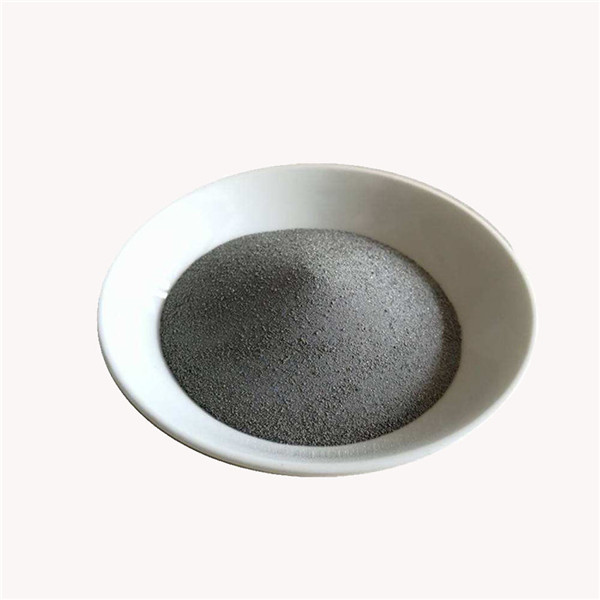
The Process of Inert Gas Atomization
Preparing the Metal
The first step in the inert gas atomization process involves preparing the metal feedstock. The selected metal or alloy is melted using induction or electric arc furnaces, ensuring precise temperature control and compositional accuracy.
Atomization Nozzle
A crucial element in the atomization process is the design of the atomization nozzle. The molten metal is forced through the nozzle, where it disintegrates into small droplets due to the shearing forces induced by the high-speed inert gas.
Inert Gas Selection
Choosing the appropriate inert gas is critical to the success of the atomization process. The selected gas should have high purity to avoid contamination and prevent unwanted chemical reactions with the molten metal.
Atomization Chamber
The atomization chamber is a controlled environment where the atomization process takes place. It is designed to prevent oxidation of the molten metal and to facilitate the uniform cooling and solidification of the droplets.
Cooling and Collection
As the metal droplets form, they are rapidly cooled and solidified in the atomization chamber. The fine spherical powders are then collected and further processed to achieve the desired particle size distribution.
Advantages of Inert Gas Atomization
Enhanced Powder Properties
Inert gas atomization produces powders with excellent flowability and tap density, making them easy to handle and process. The spherical shape of the particles also reduces inter-particle friction, improving their flow characteristics.
Improved Material Performance
The fine and uniform particle size distribution achieved through inert gas atomization results in enhanced material properties, such as mechanical strength, surface finish, and sinterability.
Versatility in Materials
Inert gas atomization can be applied to a wide range of metals and alloys, including stainless steels, titanium, aluminum, and nickel-based superalloys, expanding the possibilities for advanced material development.
Environmental Friendliness
Compared to traditional manufacturing methods, inert gas atomization produces minimal waste and emissions, aligning with sustainable and eco-friendly practices.
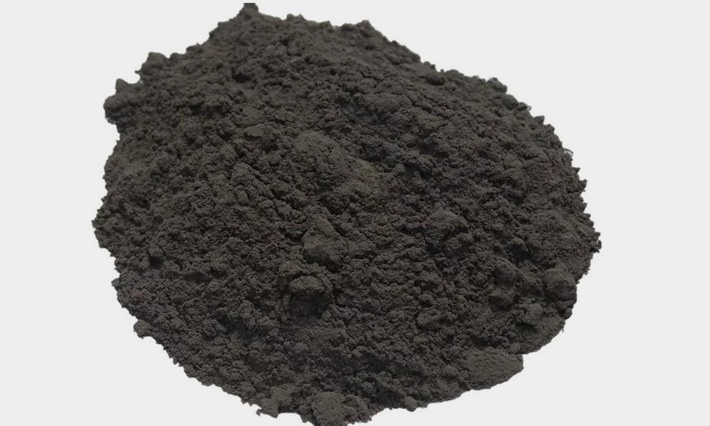
Applications of Inert Gas Atomization
Powder Metallurgy
Powder metallurgy processes benefit greatly from the use of high-quality spherical powders produced by inert gas atomization. These powders are utilized in pressing and sintering operations to create complex shapes and components with superior properties.
Additive Manufacturing
Inert gas-atomized powders are widely employed in metal additive manufacturing, commonly known as 3D printing. The powders’ high flowability and consistency ensure excellent layer-by-layer deposition and high-density parts.
Thermal Spray Coatings
Inert gas-atomized powders find applications in thermal spray coatings, where they provide exceptional bonding and mechanical properties, resulting in durable and corrosion-resistant coatings.
Brazing and Soldering
Fine powders produced through inert gas atomization are used in brazing and soldering applications, enabling strong joints and reducing the need for additional fluxes.
Specialty Alloys
Inert gas-atomized powders are essential for the production of specialty alloys used in industries like aerospace, automotive, and medical, where precise material characteristics are vital.
Comparison with Other Atomization Techniques
Water Atomization
Water atomization is a common method for producing metal powders, especially for larger-scale production. It involves spraying a high-pressure stream of water onto a molten metal stream, causing the metal to break up into fine droplets. While water atomization is cost-effective, it may result in irregular particle shapes and oxide contamination due to the presence of oxygen in water.
Gas Atomization
Gas atomization is similar to inert gas atomization but uses reactive gases like hydrogen instead of inert gases. It offers the advantage of producing extremely fine powders with high purity but requires careful handling due to the flammability of hydrogen.
Centrifugal Atomization
Centrifugal atomization relies on a rapidly rotating disk or wheel to disperse molten metal into droplets. It is suitable for producing small quantities of specialized powders, but the resulting particles may have a broader size distribution.
Plasma Atomization
Plasma atomization utilizes a plasma arc to melt and atomize the metal feedstock. This technique can produce ultrafine powders but is energy-intensive and requires advanced equipment.
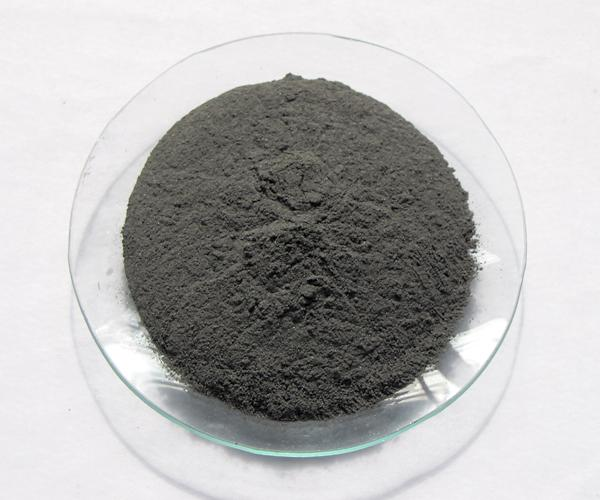
Challenges and Limitations
Cost Considerations
Inert gas atomization can be relatively expensive compared to other atomization methods, especially for small-scale production.
Particle Size Distribution
Obtaining a precise and narrow particle size distribution can be challenging, depending on the metal composition and atomization parameters.
Oxidation Concerns
Despite efforts to prevent oxidation during the atomization process, some metals may still be susceptible to surface oxidation, affecting the powder’s properties.
Process Complexity
Inert gas atomization requires precise control of various parameters like gas flow rates, atomization pressure, and chamber conditions, adding complexity to the production process.
Improving Inert Gas Atomization Techniques
Gas Selection and Purity
Continuous research is focused on optimizing the choice of inert gas and ensuring its high purity to minimize contamination during atomization.
Nozzle Design Optimization
Advancements in nozzle design play a significant role in achieving better atomization efficiency and producing powders with narrower particle size distributions.
Post-Atomization Treatments
Post-atomization treatments, such as annealing or heat treatment, can be employed to modify the powder properties and address issues like oxidation.
Monitoring and Control Systems
Incorporating advanced monitoring and control systems can enhance the reproducibility and consistency of the atomization process, ensuring high-quality powder production.
Future Trends in Inert Gas Atomization
Nanostructured Powders
The demand for nanostructured powders is increasing, and inert gas atomization is expected to play a vital role in producing nanomaterials with tailored properties.
Recycling and Sustainability
Efforts to recycle metal scrap and waste materials using inert gas atomization contribute to a more sustainable and environmentally friendly powder production process.
In-Situ Alloying
Inert gas atomization can be combined with in-situ alloying techniques to create unique compositions and multifunctional materials.
Integration with Industry 4.0
Automation and digitization of inert gas atomization processes will enhance efficiency, data analysis, and overall productivity, aligning with the principles of Industry 4.0.
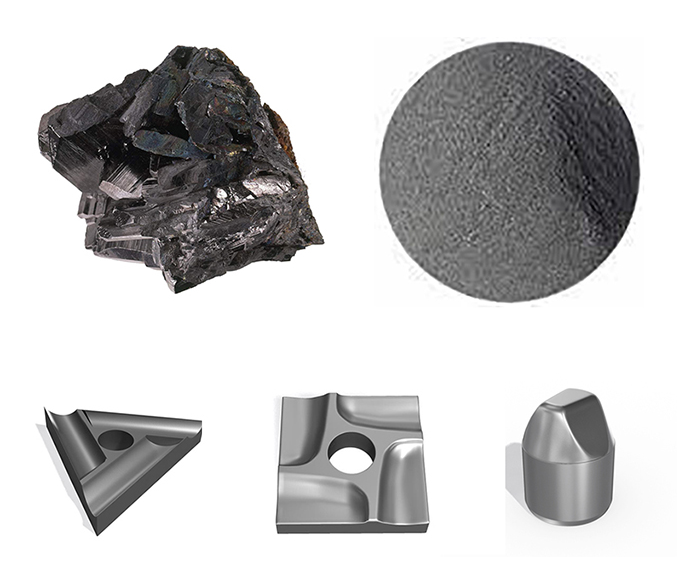
Conclusion
Inert gas atomization has become a game-changer in the world of advanced materials and powder production. Its ability to create fine, spherical powders with superior properties has opened up new possibilities in various industries, from aerospace to healthcare. Despite some challenges, ongoing research and advancements promise to further improve the process and unlock its full potential. As the demand for high-quality powders continues to grow, inert gas atomization remains at the forefront of modern manufacturing, shaping the future of materials science.
FAQs
1. Is inert gas atomization safe for the environment? Yes, inert gas atomization is considered environmentally friendly as it produces minimal waste and emissions compared to traditional manufacturing processes.
2. What types of metals can be processed using inert gas atomization? Inert gas atomization can be applied to a wide range of metals and alloys, including stainless steels, aluminum, titanium, and superalloys.
3. How does inert gas atomization improve material performance? Inert gas atomization results in powders with a fine and uniform particle size distribution, leading to improved mechanical properties, surface finish, and sinterability.
4. What are the potential applications of inert gas-atomized powders? Inert gas-atomized powders find applications in powder metallurgy, additive manufacturing, thermal spray coatings, brazing, soldering, and the production of specialty alloys.
5. What are the future trends in inert gas atomization? The future of inert gas atomization lies in producing nanostructured powders, incorporating recycling and sustainability practices, exploring in-situ alloying, and integrating the process with Industry 4.0 technologies.