Introduction
In today’s rapidly evolving industries, materials with exceptional properties are in high demand. Gas atomized powders have emerged as a game-changing solution, offering superior characteristics and unmatched versatility. In this article, we will explore the fascinating world of gas atomized powders, understanding their production process, advantages, applications, and future prospects.
What are Gas Atomized Powders?
Gas atomized powders are finely divided particles produced by the atomization of molten metal or alloy. The process involves melting the raw material and then dispersing it into fine droplets using a high-velocity gas stream. These droplets rapidly solidify into spherical powders during their descent, resulting in a uniform and highly controlled particle size distribution.
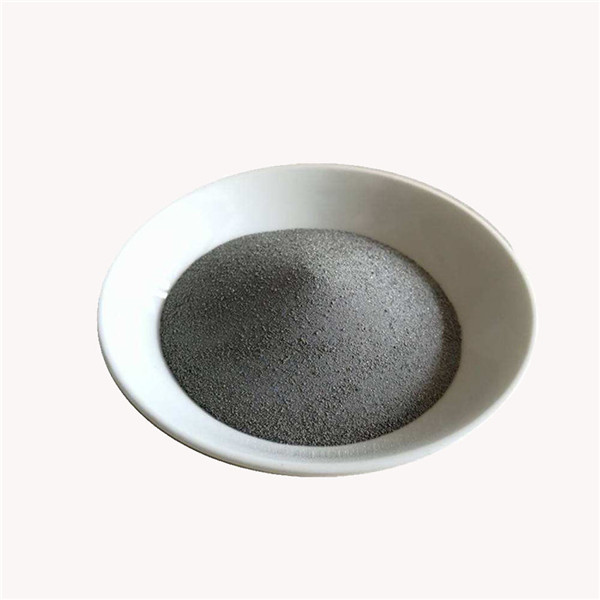
How are Gas Atomized Powders Produced?
Step 1: Selection of Raw Materials
The first crucial step in gas atomization is the careful selection of raw materials. The desired chemical composition and properties of the final powder guide this selection process.
Step 2: Melting Process
Once the raw materials are chosen, they are melted in a controlled environment to maintain purity and consistency. Induction melting or electric arc melting is commonly employed for this purpose.
Step 3: Atomization Process
The molten metal is then forced through a nozzle, where it comes into contact with a high-velocity gas stream, typically argon or nitrogen. The gas breaks the liquid metal into tiny droplets through shear forces.
Step 4: Collection and Handling
As the droplets fall, they solidify into spherical particles due to rapid cooling. These gas atomized powders are collected and undergo post-processing, including sieving and packaging.
Advantages of Gas Atomized Powders
Gas atomized powders offer several advantages that make them highly sought after in various industries:
High Purity
The gas atomization process ensures minimal contamination, resulting in powders with high purity levels, making them suitable for critical applications.
Superior Particle Size Distribution
Gas atomized powders exhibit a narrow particle size distribution, contributing to better consistency and homogeneity in the final product.
Enhanced Flowability
The spherical shape of gas atomized powders allows for excellent flowability, facilitating smoother processing in various applications.
Improved Sphericity
The spherical morphology of these powders leads to improved packing density and reduced porosity, enhancing the overall performance of the material.
Customizability
Gas atomization allows for precise control over particle size, chemical composition, and morphology, enabling tailor-made powders for specific needs.
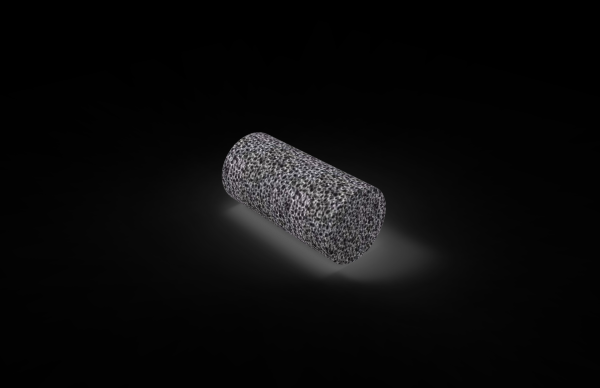
Applications of Gas Atomized Powders
Gas atomized powders find extensive applications in various cutting-edge technologies:
Additive Manufacturing (3D Printing)
Gas atomized powders serve as a crucial feedstock for metal additive manufacturing processes like selective laser melting (SLM) and electron beam melting (EBM), enabling the production of complex, high-performance components.
Metal Injection Molding (MIM)
In MIM, gas atomized powders are mixed with a binder to create a feedstock suitable for injection molding. This process is widely used to manufacture small, intricate components with exceptional mechanical properties.
Thermal Spray Coatings
Gas atomized powders are employed in thermal spray coatings to enhance the surface properties of substrates, providing wear resistance, corrosion protection, and thermal insulation.
Powder Metallurgy
The versatility of gas atomized powders makes them ideal for powder metallurgy processes, where they are compacted and sintered to produce parts for automotive, aerospace, and medical applications.
Brazing and Soldering
Gas atomized powders with tailored compositions are utilized in brazing and soldering applications, ensuring strong and reliable joints in various metal assemblies.
Gas Atomized Powders vs. Other Powder Production Methods
Gas atomization is just one of several techniques used to produce metal powders. Let’s explore how it compares to other common powder production methods:
Water Atomization
Water atomization is a similar process to gas atomization, but instead of using gas, water is employed as the atomizing medium. While water atomization is more energy-efficient, it may lead to higher levels of oxygen and hydrogen contamination in the powders, making gas atomization the preferred choice for high-purity applications.
Plasma Atomization
Plasma atomization involves using a plasma arc to melt the raw material, and then the molten metal is atomized using gas. This method is often used to produce specialty alloys and materials with unique properties.
Mechanical Alloying
Mechanical alloying is a solid-state powder processing technique where powders are mixed and subjected to high-energy ball milling. While it can produce nanostructured powders, gas atomization offers better control over particle size and composition.
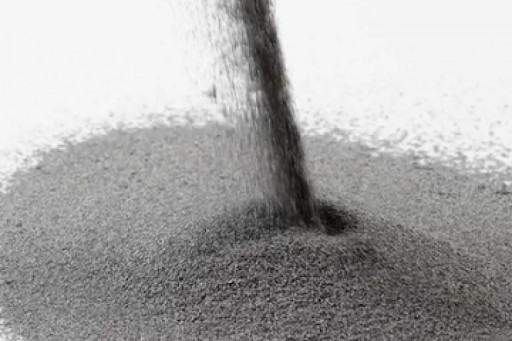
Quality Control in Gas Atomization
Ensuring the quality of gas atomized powders is vital for their successful applications. Several factors contribute to quality control:
Gas Selection and Atmosphere Control
The choice of atomizing gas and the control of the atmosphere during the process play a significant role in preventing contamination and maintaining the desired composition.
Particle Size Analysis
Accurate particle size analysis is essential for verifying the powder’s conformity to specifications, ensuring consistent performance in various applications.
Chemical Composition Analysis
Thorough chemical analysis confirms the powder’s composition, verifying that it meets the required standards and properties.
Powder Handling and Packaging
Proper handling and packaging of gas atomized powders are critical to prevent contamination and preserve their properties during storage and transportation.
Challenges in Gas Atomization
While gas atomization offers numerous advantages, it also faces some challenges:
Porosity and Oxidation
The rapid solidification of gas atomized powders can sometimes lead to porosity and surface oxidation, which may affect the material’s mechanical properties.
Particle Agglomeration
During atomization, particles may agglomerate, leading to irregularities in particle size distribution. Careful process control is necessary to minimize agglomeration.
Energy Consumption
The gas atomization process can be energy-intensive, especially when dealing with high-melting-point alloys. Continued research aims to optimize energy efficiency.
Future Trends in Gas Atomization Technology
Gas atomization continues to evolve, with exciting future prospects:
Nanostructured Powders
Advancements in gas atomization techniques will enable the production of nanostructured powders with enhanced properties for cutting-edge applications.
Composite Powders
Researchers are exploring the possibility of producing composite powders through gas atomization, combining different materials to create new, multifunctional materials.
Additive Manufacturing Advancements
The growth of additive manufacturing will drive further innovations in gas atomization, tailoring powders for more complex and demanding applications.
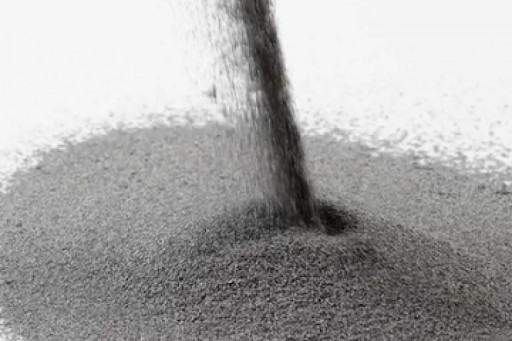
Conclusion
Gas atomized powders have become indispensable in modern industries, revolutionizing materials science and manufacturing processes. Their unique advantages, including high purity, controlled particle size distribution, and customizability, make them a prime choice for a wide range of applications. As technology advances, we can expect even more remarkable developments in gas atomization, leading to novel materials and groundbreaking innovations across industries.
FAQs
Are gas atomized powders only used for metal applications?Gas atomized powders are primarily used in metal applications due to their excellent properties. However, they can also be employed for some non-metallic materials in specialized applications.
What are the main factors affecting powder quality during gas atomization?The main factors include gas selection, atmosphere control, melting process parameters, and the post-processing steps like sieving and packaging.
Can gas atomized powders be used for medical implants?Yes, gas atomized powders are commonly used for medical implants, where high purity and controlled properties are crucial for biocompatibility and performance.
What is the typical particle size range of gas atomized powders?Gas atomized powders typically have a particle size range between a few micrometers to a few hundred micrometers, depending on the specific application requirements.
How does gas atomization compare to other powder production methods in terms of cost?The cost-effectiveness of gas atomization depends on the specific application and the material being produced. In some cases, gas atomization may offer a more efficient and cost-effective solution compared to other methods, while in others, alternative techniques may be preferred.