Gas atomization is a powder metallurgy process used to produce fine metallic powders. It involves melting a metal alloy and disintegrating the melt into fine droplets using a high-velocity gas jet. The droplets rapidly solidify into powders with a spherical morphology and controlled particle size distribution. Gas atomized powders have unique properties that make them suitable for specialized applications across various industries.
How does gas atomization work?
The gas atomization process starts by melting the desired alloy in a crucible or induction furnace. The liquid metal is then poured in a thin stream into the atomization chamber. High pressure gas (typically nitrogen or argon) jets positioned around the metal stream disintegrate it into fine droplets. As the droplets fall through the atomization tower, they rapidly solidify into spherical powders due to the high surface area to volume ratio. The powders are collected at the bottom of the tower and classified according to particle size using sieves.
The size of the powders produced depends on the gas flow rates and the metal stream flow rate. Higher gas pressures and lower metal flow rates result in finer powders. Other process parameters like the gas injection angle and design of the atomization nozzle also affect powder characteristics.
What are the advantages of gas atomized powders?
Compared to powders made by other methods like water atomization, gas atomized powders have the following advantages:
- Highly spherical particle morphology
- Tight particle size distribution
- Low oxygen and nitrogen pickup during atomization
- Ability to atomize alloys with high melting temperatures
- Flexibility to modify process parameters and customize powder characteristics
The spherical shape improves powder flow and packing density. The controlled particle size distribution allows precise control over final part properties. The inert atomization atmosphere prevents contamination of reactive alloy chemistries. These advantages enable gas atomized powders to meet the requirements of advanced metal AM processes like laser powder bed fusion and binder jetting. The high purity also makes them suitable for powder metallurgy applications like metal injection molding where contamination can degrade properties.
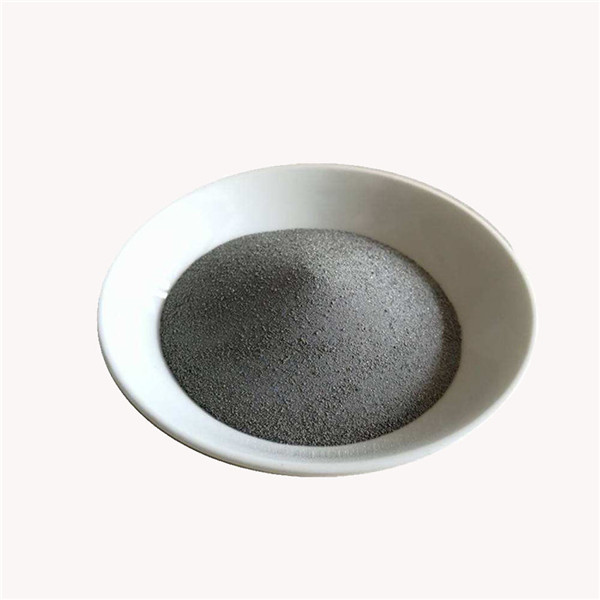
What metals and alloys are commonly gas atomized?
Some of the common metals and alloys that are gas atomized include:
- Titanium alloys like Ti-6Al-4V
- Nickel-based superalloys like Inconel 718, Inconel 625
- Cobalt-chrome alloys
- Tool steels like H13
- Stainless steels like 316L, 17-4PH
- Aluminum alloys
- Copper alloys
High temperature alloys based on titanium, nickel, and cobalt are especially well suited for gas atomization. The inert gas atmosphere prevents excessive oxygen pickup in these reactive elemental powders. Refractory metals like tungsten are also gas atomized since their high melting points make water atomization challenging.
Overall, gas atomization can produce fine spherical powders from any alloy that melts without decomposing. The process can be customized to atomize novel alloys designed for advanced applications.
What are some applications of gas atomized powders?
Some of the major application areas of gas atomized alloy powders include:
Metal Additive Manufacturing
- Laser powder bed fusion uses gas atomized powders due to their spherical morphology and controlled size distribution. These characteristics ensure good flow and packing in the powder bed.
- Binder jetting also utilizes gas atomized powders to produce isotropic properties in the printed parts. The spherical shape and precise control over size improve packing density and powder spreading.
Powder Metallurgy
- Metal injection molding relies on gas atomized feedstock powders with controlled particle size. This allows high powder loading and uniform shrinkage.
- Powder pressing and sintering uses atomized pre-alloyed powders to produce automotive components, cutting tools, and other structural parts.
Thermal Spray
- Gas atomized powders fed into plasma, flame, or high velocity oxy-fuel (HVOF) thermal spray systems produce superior coatings due to the spherical morphology.
Healthcare
- Porous structures made using gas atomized titanium and cobalt-chrome powders are used for orthopedic implants.
- Fine stainless steel powders are used to manufacture surgical instruments by metal injection molding.
The combination of purity, repeatability, and particle characteristics makes gas atomized powders ideal for these critical applications across industries.
What particle size distribution is used for different applications?
The optimal particle size distribution depends on the intended application:
- For laser powder bed fusion, the typical range is 15-45 microns. Very fine powders below 10 microns can cause handling issues. Size range of 25-35 microns is commonly used.
- Binder jetting uses finer powders in the 5-25 micron range to improve sintering. Layer thickness also dictates minimum particle size.
- Metal injection molding uses bimodal distributions with powder sizes under 25 microns. This improves packing density and flow.
- Thermal spray requires larger particles over 45 microns for better momentum transfer and coating density. Size ranges between 45-100 microns are commonly used.
- For orthopedic implants, powder sizes below 75 microns promote tissue ingrowth into the porous structure.
The gas atomization process parameters can be optimized to produce powders with the desired particle size distribution for the intended application.
What are the latest developments in gas atomization technology?
Some of the latest advances in gas atomization process technology include:
- Close-coupled atomization uses a consumable electrode furnace integrated to the atomization nozzle for a more controlled process. This improves melt cleanliness.
- Multiple gas injectors arranged concentrically can produce unique particle size distributions. Varying the gas pressure between injectors increases atomization flexibility.
- Pre-filming atomizers use a thin liquid film to generate finer atomized droplets compared to free-falling metal streams. This expands the capability for sub-10 micron powders.
- Feedback control systems using optical sensors allow dynamic adjustment of gas pressures and metal flow rate to maintain powder size distribution. This improves consistency.
- Induction atomization uses electromagnetic levitation and induction coils to precisely control the melt pool. This enables a very uniform, contactless atomization process.
- Additive manufacturing is being used to manufacture complex atomizer nozzle geometries not possible with conventional machining. This provides increased atomization control.
These process innovations are expanding the alloy systems and particle characteristics achievable through gas atomization.
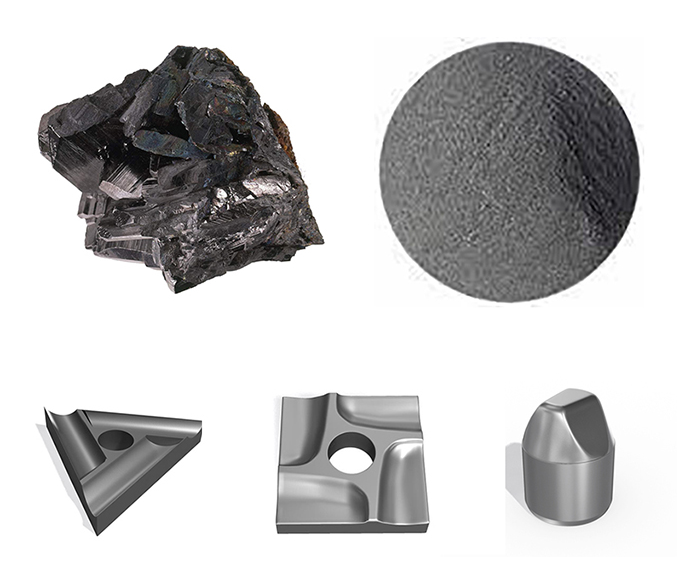
What are some challenges in gas atomization?
Some of the key challenges associated with gas atomization include:
- Contamination of reactive alloys by oxygen/nitrogen pickup – Using higher purity inert gases and vacuum chambers minimizes this.
- Satellite formation during atomization due to ligaments forming between droplets – Nozzle geometry and gas flow optimization reduces satellites.
- Production of irregular, non-spherical particle shapes – Careful control of process parameters ensures smooth spherical morphology.
- Achieving uniform cooling rates between large and small particles – Modified nozzle designs help equalize droplet solidification rates.
- Handling high reactivity and oxidation of hot powders below melting point – Powder handling under inert atmosphere suppresses oxidation.
- Cost and complexity associated with using high pressure gas systems – Recent innovations are improving productivity and reducing costs.
Continued research is focused on understanding and controlling melt atomization physics to further improve gas atomized powder quality and consistency.
What are the alternatives to gas atomization?
Some alternative powder production processes to gas atomization include:
- Water atomization – Inexpensive but causes oxidation and irregular powder shapes
- Plasma atomization – Produces highly spherical powders but very low productivity
- Electrode induction melting gas atomization – Good for reactive alloys but higher O2 pickup
- Rotating electrode process – Promising for producing spherical metal powders but still in development
- Plasma spheroidization – Spherodizes irregular powders but doesn’t produce fresh alloy powder
- Mechanical milling – Contaminates powder through attrition and abrasion
For most applications, gas atomization strikes the best balance between cost, productivity, and powder quality. But new atomization techniques continue to emerge as alternatives for niche applications.
What does the future look like for gas atomized powders?
Gas atomized powders will continue gaining prominence with the growth of metal additive manufacturing. The precise control of powder characteristics possible through gas atomization is critical for demanding aerospace and medical AM applications. This is driving significant investment and innovations in atomization technology.
Besides AM, increasing use of powder metallurgy in automotive and other industries will also accelerate gas atomization adoption. Moving to metal powder feedstocks allows complex component geometries and alloy compositions not feasible with wrought products.
Gas atomization will also enable new materials like amorphous alloy powders with unique properties. Control over cooling rates during atomization can produce customized alloys and metastable phases.
Overall, enhancements in quality and cost-effectiveness will expand gas atomization into wider material systems and industry applications in the future.
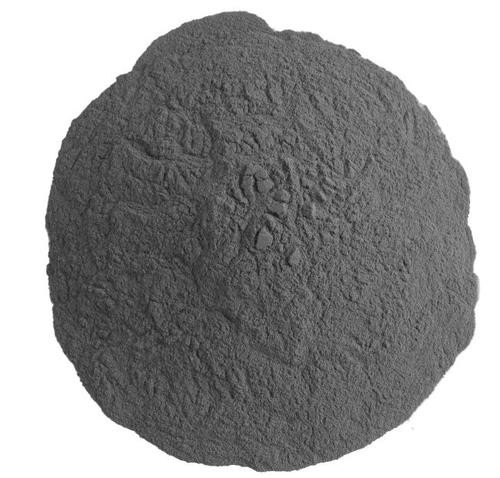
FAQ
What is the smallest particle size that can be produced by gas atomization?
Gas atomization can produce powders down to around 5 microns in size. Special nozzles utilizing pre-filming flow have generated particles in the sub-micron size range. But scaled production below 10 microns remains a challenge.
How does gas atomization provide such spherical particles?
The high surface tension of the metal droplets combined with rapid solidification in the inert gas atmosphere preserves the spherical shape. Ligaments between droplets that cause irregularities are minimized with optimal atomization parameters.
What is the benefit of a narrow size distribution?
A narrow distribution provides consistent properties and performance in the final application. For example, uniform melting and flow during metal AM processing. Segregation and porosity issues are avoided.
What is the maximum production rate for gas atomized powders?
Commercial gas atomizer production rates are typically in the range of 5kg to 20kg of powder per minute. With optimized systems, production rates up to 100kg/min have been reported for some lower melting point alloys.
How are reactive materials like aluminum gas atomized?
Highly pure inert gases (argon, nitrogen) must be used to prevent excessive oxygen and nitride pickup. Handling and collection under protective atmospheres is also critical. Vacuum chambers can also be used.
Are there ways to produce gas atomized powders more economically?
Recent innovations like close-coupled nozzles, advanced pre-filming atomizers, multiple gas injection, and electrode crucibles are improving energy efficiency. Additive manufacturing of nozzles also reduces costs. Higher production rates help improve economies of scale.
Can gas atomization achieve the properties of wrought products?
With optimized processing, gas atomized powders can achieve mechanical properties close to conventional wrought alloys in certain materials. But properties are still limited by residual porosity in powder metallurgy products.
What industries represent the largest consumers of gas atomized powders today?
Currently, aerospace and medical sectors are the largest consumers of gas atomized powders for additive manufacturing and metal injection molding. Use in automotive applications is also rapidly increasing.
Does gas atomization allow alloy compositions that cannot be processed conventionally?
Yes, gas atomization has very high cooling rates that can suppress decomposition reactions and allow metastable and amorphous alloy phases. It also enables alloys compositions with poor castability or workability to be produced as powders.
know more 3D printing processes
Additional FAQs About Gas Atomization
1) What CoA data should buyers require for gas atomized powders?
- Chemistry, PSD (D10/D50/D90), flow (Hall/Carney), apparent/tap density, O/N/H, moisture, and for AM grades: image‑based sphericity/satellite %, CT‑measured hollow fraction, and lot traceability with test methods (ASTM/ISO).
2) How do gas‑to‑metal ratio and melt superheat affect PSD and satellites?
- Higher gas‑to‑metal ratio and adequate superheat generally reduce D50 and narrow PSD, while stable superheat and optimized nozzle/plume alignment lower ligament formation, cutting satellite content.
3) When is vacuum gas atomization (VGA/EIGA) preferred over inert gas atomization?
- For reactive alloys (Ti, Al, Mg) and aerospace/medical grades requiring very low O/N/H and minimal inclusions; VGA/EIGA often yields fewer hollows and better sphericity than standard inert gas atomization.
4) Can gas atomized powders be reused in AM, and what should be monitored?
- Yes, commonly 5–10 cycles with sieving. Track PSD shift, flow, apparent/tap density, and O/N/H; monitor satellite/hollow fractions via image analysis/CT; refresh with virgin powder when thresholds drift.
5) How does gas atomization compare to water atomization for binder jetting?
- Water‑atomized powders are cheaper and common in BJ steels/Cu but have higher oxide and irregular shapes. Gas atomized variants offer better packing and lower impurity pickup, helping achieve higher sintered density or reduced HIP reliance.
2025 Industry Trends for Gas Atomization
- CoA transparency: Growing inclusion of sphericity, satellite %, and CT hollow fraction alongside O/N/H and PSD for AM‑grade lots.
- Energy and argon savings: Argon recirculation and heat recovery cut Ar consumption by 15–30% and total energy 5–12% in modern atomizers.
- Regional supply: New atomization lines in NA/EU/APAC shorten lead times for Ti/Ni/SS AM powders.
- Advanced controls: Closed‑loop gas‑to‑metal ratio, melt superheat control, and plume vision reduce satellites and improve yield.
- Binder jet adoption: Engineered bimodal PSD steels achieve 97–99.5% sintered density; HIP used selectively for critical parts.
2025 Market and Technical Snapshot (Gas Atomization)
Metric (2025) | Typical Value/Range | YoY Change | Notes/Source |
---|---|---|---|
Gas‑atomized 316L price | $10–$18/kg | −2–5% | Supplier/distributor indices |
Gas‑atomized 17‑4PH price | $12–$20/kg | −2–5% | PSD/alloy dependent |
Ti‑6Al‑4V (VGA/EIGA) | $150–$280/kg | −3–7% | Aerospace/medical grades |
Common AM PSD cuts (LPBF/BJ/DED) | 15–45 or 20–63 µm / 20–80+ µm / 53–150 µm | Stable | OEM guidance |
Sphericity (image analysis) | ≥0.93–0.98 | Slightly up | Supplier CoAs |
Satellite fraction (image) | ≤3–6% | Down | Process tuning |
CT hollow particle fraction | 0.5–1.5% | Down | VGA/EIGA + CT QC |
Argon use reduction (recirc) | 15–30% | Up | Energy/LCA initiatives |
Indicative sources:
- ISO/ASTM 52907 (Metal powders), 52908 (AM process qualification): https://www.iso.org | https://www.astm.org
- ASTM B214/B213/B212/B962 (powder tests), MPIF references: https://www.astm.org | https://www.mpif.org
- NIST AM Bench and powder metrology: https://www.nist.gov
- ASM Handbooks (Powder Metallurgy; Additive Manufacturing): https://www.asminternational.org
- NFPA 484 (Combustible metal dusts): https://www.nfpa.org
Latest Research Cases
Case Study 1: Closed‑Loop Plume Control Cuts Satellites in 316L (2025)
Background: An AM service bureau reported recoater jams tied to high satellite content from a key supplier’s gas atomized 316L.
Solution: Supplier implemented real‑time plume imaging, closed‑loop gas‑to‑metal ratio, and tighter melt superheat; added post‑classification air elutriation.
Results: Satellite fraction reduced from 8.1% to 3.1% (image analysis); Hall flow +14%; LPBF relative density rose from 99.4% to 99.8%; unplanned stoppages −40%.
Case Study 2: VGA with CT Screening for Ti‑6Al‑4V Fatigue Scatter Reduction (2024)
Background: An aerospace OEM needed lower hollow particle fraction to improve fatigue consistency in PBF Ti‑6Al‑4V.
Solution: Vacuum gas atomization (EIGA electrodes), in‑line oxygen monitoring, and lot‑level CT to cap hollows ≤1.0%; argon recirculation to lower cost.
Results: Median hollows 0.6%; O = 0.12 wt% ±0.01; HIP’d coupons showed ~2× reduction in HCF scatter band; powder cost −6% via gas reuse.
Expert Opinions
- Prof. Diran Apelian, Distinguished Professor (emeritus), Metal Processing
Key viewpoint: “Melt cleanliness plus stable gas‑to‑metal ratio and superheat set the quality ceiling in gas atomization—post‑screening can’t fully recover poor plume dynamics.” - Dr. John Slotwinski, Additive Manufacturing Metrology Expert (former NIST)
Key viewpoint: “Reporting sphericity, satellite %, and CT‑quantified hollows on CoAs is now a leading indicator of PBF defect propensity—buyers should require these metrics.” - Prof. Tresa Pollock, Distinguished Professor of Materials, UC Santa Barbara
Key viewpoint: “For reactive alloys, vacuum/inert control during atomization fundamentally influences downstream fatigue and corrosion performance, even after HIP.”
Note: Viewpoints synthesized from public talks and publications; affiliations are publicly known.
Practical Tools and Resources
- Standards and testing
- ISO/ASTM 52907, 52908; ASTM B214 (sieves), B213 (flow), B212 (apparent density), B962 (tap density): https://www.iso.org | https://www.astm.org
- Safety and compliance
- NFPA 484 combustible metal dust guidance; ATEX/DSEAR resources for Dust Hazard Analysis: https://www.nfpa.org
- Metrology and QC
- NIST powder characterization; LECO O/N/H analyzers; industrial CT for hollow/satellite quantification: https://www.nist.gov
- Technical references
- ASM Digital Library (Powder Metallurgy; Additive Manufacturing; Stainless/Titanium/Nickel): https://www.asminternational.org
- Buyer’s QC checklist
- CoA completeness (chemistry, PSD, flow, densities, O/N/H, sphericity, satellites, hollows), genealogy/traceability, SPC dashboards, sample builds/sinter coupons, local inventory and refresh policies
Last updated: 2025-08-26
Changelog: Added 5 targeted FAQs; inserted 2025 market/technical snapshot table with sources; provided two recent gas atomization case studies; compiled expert viewpoints; curated practical tools/resources
Next review date & triggers: 2026-02-01 or earlier if ISO/ASTM/MPIF standards update, major OEMs revise AM powder specs, or new NIST/ASM datasets link morphology/interstitials to AM defect rates and fatigue performance