Atomização de gás é um processo de metalurgia do pó usado para produzir pós metálicos finos. Ele envolve a fusão de uma liga metálica e a desintegração da fusão em gotículas finas usando um jato de gás de alta velocidade. As gotículas se solidificam rapidamente em pós com morfologia esférica e distribuição controlada do tamanho das partículas. Os pós atomizados a gás têm propriedades exclusivas que os tornam adequados para aplicações especializadas em vários setores.
Como funciona a atomização de gás?
O processo de atomização a gás começa com a fusão da liga desejada em um cadinho ou forno de indução. O metal líquido é então despejado em um fluxo fino na câmara de atomização. Jatos de gás de alta pressão (normalmente nitrogênio ou argônio) posicionados ao redor do fluxo de metal o desintegram em gotículas finas. À medida que as gotículas caem pela torre de atomização, elas se solidificam rapidamente em pós esféricos devido à alta relação entre área de superfície e volume. Os pós são coletados na parte inferior da torre e classificados de acordo com o tamanho das partículas usando peneiras.
O tamanho dos pós produzidos depende das taxas de fluxo de gás e da taxa de fluxo de metal. Pressões de gás mais altas e taxas de fluxo de metal mais baixas resultam em pós mais finos. Outros parâmetros do processo, como o ângulo de injeção do gás e o design do bocal de atomização, também afetam as características do pó.
Quais são as vantagens dos pós atomizados a gás?
Em comparação com os pós produzidos por outros métodos, como a atomização com água, os pós atomizados a gás têm as seguintes vantagens:
- Morfologia de partículas altamente esféricas
- Distribuição estreita do tamanho das partículas
- Baixa captação de oxigênio e nitrogênio durante a atomização
- Capacidade de atomizar ligas com altas temperaturas de fusão
- Flexibilidade para modificar os parâmetros do processo e personalizar as características do pó
O formato esférico melhora o fluxo de pó e a densidade de empacotamento. A distribuição controlada do tamanho das partículas permite o controle preciso das propriedades da peça final. A atmosfera de atomização inerte evita a contaminação de produtos químicos de ligas reativas. Essas vantagens permitem que os pós atomizados a gás atendam aos requisitos de processos avançados de AM de metal, como fusão de leito de pó a laser e jato de aglutinante. A alta pureza também os torna adequados para aplicações de metalurgia do pó, como moldagem por injeção de metal, em que a contaminação pode degradar as propriedades.
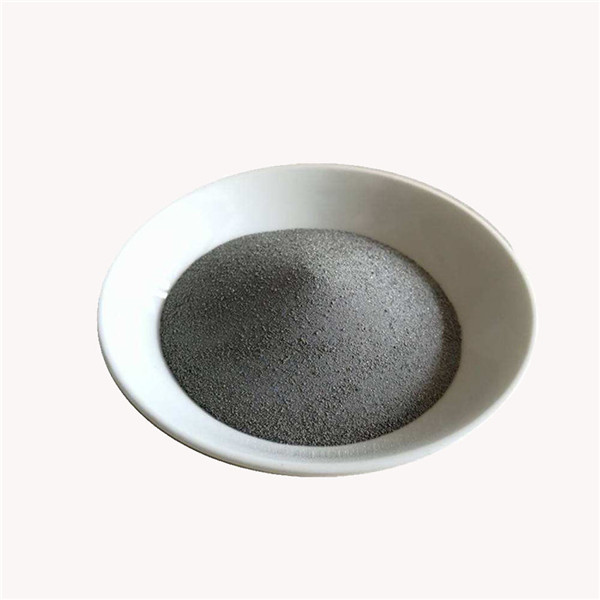
Quais metais e ligas são comumente atomizados com gás?
Alguns dos metais e ligas comuns que são atomizados a gás incluem:
- Ligas de titânio como Ti-6Al-4V
- Superligas à base de níquel, como Inconel 718, Inconel 625
- Ligas de cobalto-cromo
- Aços para ferramentas, como o H13
- Aços inoxidáveis como 316L, 17-4PH
- Ligas de alumínio
- Ligas de cobre
As ligas de alta temperatura à base de titânio, níquel e cobalto são especialmente adequadas para a atomização a gás. A atmosfera de gás inerte evita a captação excessiva de oxigênio nesses pós elementares reativos. Metais refratários, como o tungstênio, também são atomizados com gás, pois seus altos pontos de fusão tornam a atomização com água um desafio.
De modo geral, a atomização a gás pode produzir pós esféricos finos a partir de qualquer liga que derreta sem se decompor. O processo pode ser personalizado para atomizar novas ligas projetadas para aplicações avançadas.
Quais são algumas das aplicações dos pós atomizados a gás?
Algumas das principais áreas de aplicação dos pós de liga atomizada a gás incluem:
Manufatura aditiva de metal
- A fusão em leito de pó a laser usa pós atomizados a gás devido à sua morfologia esférica e distribuição de tamanho controlada. Essas características garantem um bom fluxo e acondicionamento no leito de pó.
- O jato de aglutinante também utiliza pós atomizados a gás para produzir propriedades isotrópicas nas peças impressas. O formato esférico e o controle preciso do tamanho melhoram a densidade da embalagem e o espalhamento do pó.
Metalurgia do pó
- A moldagem por injeção de metal se baseia em pós de matéria-prima atomizados a gás com tamanho de partícula controlado. Isso permite alta carga de pó e encolhimento uniforme.
- A prensagem e a sinterização de pós usam pós pré-ligados atomizados para produzir componentes automotivos, ferramentas de corte e outras peças estruturais.
Spray térmico
- Os pós atomizados a gás alimentados em sistemas de pulverização térmica de plasma, chama ou oxi-combustível de alta velocidade (HVOF) produzem revestimentos superiores devido à morfologia esférica.
Assistência médica
- Estruturas porosas feitas com titânio atomizado a gás e pós de cobalto-cromo são usadas para implantes ortopédicos.
- Os pós finos de aço inoxidável são usados para fabricar instrumentos cirúrgicos por meio de moldagem por injeção de metal.
A combinação de pureza, repetibilidade e características das partículas torna os pós atomizados a gás ideais para essas aplicações críticas em todos os setores.
Qual distribuição de tamanho de partícula é usada para diferentes aplicações?
A distribuição ideal do tamanho das partículas depende da aplicação pretendida:
- Para a fusão de leito de pó a laser, a faixa típica é de 15 a 45 mícrons. Os pós muito finos, abaixo de 10 mícrons, podem causar problemas de manuseio. A faixa de tamanho de 25 a 35 mícrons é comumente usada.
- O jato de aglutinante usa pós mais finos na faixa de 5 a 25 mícrons para melhorar a sinterização. A espessura da camada também determina o tamanho mínimo das partículas.
- A moldagem por injeção de metal usa distribuições bimodais com tamanhos de pó abaixo de 25 mícrons. Isso melhora a densidade e o fluxo da embalagem.
- A pulverização térmica requer partículas maiores, acima de 45 mícrons, para melhor transferência de momento e densidade do revestimento. As faixas de tamanho entre 45 e 100 mícrons são comumente usadas.
- Para implantes ortopédicos, os tamanhos de pó abaixo de 75 mícrons promovem o crescimento do tecido na estrutura porosa.
Os parâmetros do processo de atomização a gás podem ser otimizados para produzir pós com a distribuição de tamanho de partícula desejada para a aplicação pretendida.
Quais são os desenvolvimentos mais recentes na tecnologia de atomização de gás?
Alguns dos mais recentes avanços na tecnologia de processo de atomização de gás incluem:
- A atomização de acoplamento fechado usa um forno de eletrodo consumível integrado ao bocal de atomização para um processo mais controlado. Isso melhora a limpeza da massa fundida.
- Vários injetores de gás dispostos concentricamente podem produzir distribuições de tamanho de partículas exclusivas. A variação da pressão do gás entre os injetores aumenta a flexibilidade da atomização.
- Os atomizadores de pré-filtragem usam um filme líquido fino para gerar gotículas atomizadas mais finas em comparação com os fluxos de metal em queda livre. Isso amplia a capacidade de pós abaixo de 10 mícrons.
- Os sistemas de controle de feedback que usam sensores ópticos permitem o ajuste dinâmico das pressões de gás e da taxa de fluxo de metal para manter a distribuição do tamanho do pó. Isso melhora a consistência.
- A atomização por indução usa levitação eletromagnética e bobinas de indução para controlar com precisão a poça de fusão. Isso permite um processo de atomização muito uniforme e sem contato.
- A manufatura aditiva está sendo usada para fabricar geometrias complexas de bicos atomizadores que não são possíveis com a usinagem convencional. Isso proporciona maior controle da atomização.
Essas inovações de processo estão expandindo os sistemas de ligas e as características das partículas que podem ser obtidas por meio da atomização a gás.
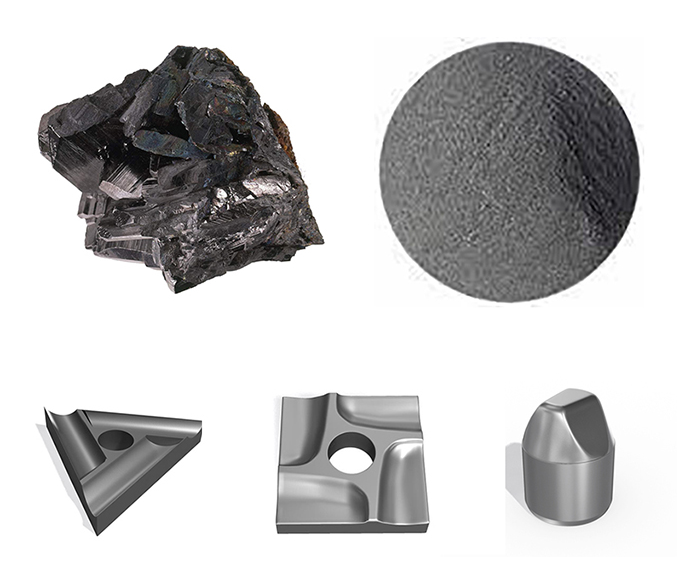
Quais são alguns dos desafios da atomização de gás?
Alguns dos principais desafios associados à atomização de gás incluem:
- Contaminação de ligas reativas por captação de oxigênio/nitrogênio - O uso de gases inertes de maior pureza e de câmaras de vácuo minimiza esse problema.
- Formação de satélites durante a atomização devido à formação de ligamentos entre as gotículas - A geometria do bocal e a otimização do fluxo de gás reduzem os satélites.
- Produção de formas de partículas irregulares e não esféricas - O controle cuidadoso dos parâmetros do processo garante uma morfologia esférica suave.
- Obtenção de taxas de resfriamento uniformes entre partículas grandes e pequenas - Projetos de bicos modificados ajudam a equalizar as taxas de solidificação de gotículas.
- Manuseio de alta reatividade e oxidação de pós quentes abaixo do ponto de fusão - O manuseio de pós sob atmosfera inerte suprime a oxidação.
- Custo e complexidade associados ao uso de sistemas de gás de alta pressão - Inovações recentes estão melhorando a produtividade e reduzindo os custos.
O foco da pesquisa contínua é compreender e controlar a física da atomização por fusão para melhorar ainda mais a qualidade e a consistência do pó atomizado a gás.
Quais são as alternativas à atomização de gás?
Alguns processos de produção de pó alternativos à atomização a gás incluem:
- Atomização com água - Barato, mas causa oxidação e formas irregulares de pó
- Atomização por plasma - Produz pós altamente esféricos, mas com produtividade muito baixa
- Atomização de gás de fusão por indução de eletrodo - Bom para ligas reativas, mas com maior captação de O2
- Processo de eletrodo rotativo - promissor para a produção de pós metálicos esféricos, mas ainda em desenvolvimento
- Esferoidização por plasma - Esferodiza pós irregulares, mas não produz pó de liga nova
- Moagem mecânica - contamina o pó por atrito e abrasão
Para a maioria das aplicações, a atomização a gás atinge o melhor equilíbrio entre custo, produtividade e qualidade do pó. Mas novas técnicas de atomização continuam surgindo como alternativas para aplicações de nicho.
Como será o futuro dos pós atomizados a gás?
Os pós atomizados a gás continuarão a ganhar destaque com o crescimento da manufatura aditiva de metais. O controle preciso das características do pó possível por meio da atomização de gás é fundamental para as exigentes aplicações de AM aeroespacial e médica. Isso está gerando investimentos e inovações significativas na tecnologia de atomização.
Além da AM, o aumento do uso da metalurgia do pó no setor automotivo e em outros setores também acelerará a adoção da atomização a gás. A mudança para matérias-primas de pó metálico permite geometrias complexas de componentes e composições de ligas que não são viáveis com produtos forjados.
A atomização a gás também possibilitará novos materiais, como pós de ligas amorfas com propriedades exclusivas. O controle das taxas de resfriamento durante a atomização pode produzir ligas personalizadas e fases metaestáveis.
De modo geral, os aprimoramentos na qualidade e na relação custo-benefício expandirão a atomização de gás para sistemas de materiais e aplicações industriais mais amplos no futuro.
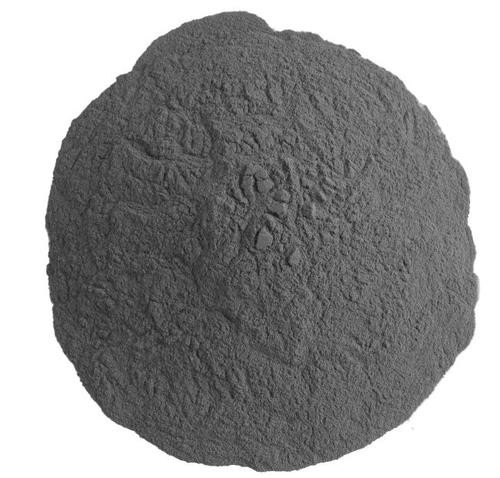
Perguntas frequentes
Qual é o menor tamanho de partícula que pode ser produzido por atomização de gás?
A atomização a gás pode produzir pós com tamanho de até 5 mícrons. Bicos especiais que utilizam fluxo de pré-filtragem geraram partículas na faixa de tamanho submicrônico. Mas a produção em escala abaixo de 10 mícrons continua sendo um desafio.
Como a atomização do gás fornece essas partículas esféricas?
A alta tensão superficial das gotículas de metal, combinada com a rápida solidificação na atmosfera de gás inerte, preserva o formato esférico. Os ligamentos entre as gotículas que causam irregularidades são minimizados com parâmetros de atomização ideais.
Qual é a vantagem de uma distribuição de tamanho estreita?
Uma distribuição estreita proporciona propriedades e desempenho consistentes na aplicação final. Por exemplo, fusão e fluxo uniformes durante o processamento de metal AM. Problemas de segregação e porosidade são evitados.
Qual é a taxa máxima de produção de pós atomizados a gás?
As taxas de produção do atomizador de gás comercial estão normalmente na faixa de 5 kg a 20 kg de pó por minuto. Com sistemas otimizados, foram registradas taxas de produção de até 100 kg/min para algumas ligas de ponto de fusão mais baixo.
Como os materiais reativos, como o gás de alumínio, são atomizados?
Gases inertes altamente puros (argônio, nitrogênio) devem ser usados para evitar a captação excessiva de oxigênio e nitreto. O manuseio e a coleta sob atmosferas protetoras também são fundamentais. Também podem ser usadas câmaras de vácuo.
Existem maneiras de produzir pós atomizados a gás de forma mais econômica?
Inovações recentes, como bicos de acoplamento fechado, atomizadores avançados de pré-filtragem, injeção múltipla de gás e cadinhos de eletrodos, estão melhorando a eficiência energética. A fabricação aditiva de bicos também reduz os custos. Taxas de produção mais altas ajudam a melhorar as economias de escala.
A atomização de gás pode alcançar as propriedades dos produtos forjados?
Com o processamento otimizado, os pós atomizados a gás podem atingir propriedades mecânicas próximas às das ligas forjadas convencionais em determinados materiais. Mas as propriedades ainda são limitadas pela porosidade residual nos produtos de metalurgia do pó.
Quais setores representam os maiores consumidores de pós atomizados a gás atualmente?
Atualmente, os setores aeroespacial e médico são os maiores consumidores de pós atomizados a gás para fabricação de aditivos e moldagem por injeção de metal. O uso em aplicações automotivas também está aumentando rapidamente.
A atomização a gás permite composições de ligas que não podem ser processadas convencionalmente?
Sim, a atomização a gás tem taxas de resfriamento muito altas que podem suprimir reações de decomposição e permitir fases de liga metastáveis e amorfas. Ela também permite que as composições de ligas com baixa capacidade de fundição ou de trabalho sejam produzidas como pós.