Nickel-based powders have become a cornerstone of various industries, renowned for their exceptional properties and versatility. These finely-ground materials, primarily composed of nickel and meticulously selected alloying elements, offer a compelling combination of strength, heat resistance, and corrosion defiance, making them ideal for demanding applications.
Physical and Chemical Properties of Nickel-Based Powders
Property | Description |
---|---|
High Purity | Typically exceeding 99% nickel content, ensuring consistent performance. |
Controlled Particle Size and Morphology | Tailored for specific applications, influencing flowability, packing density, and sintering behavior. |
Excellent Thermal Conductivity | Facilitates efficient heat transfer, crucial for applications like heat exchangers and thermal management systems. |
Good Electrical Conductivity | Enables diverse electrical applications, including battery electrodes and electronic components. |
Superior Corrosion Resistance | Exhibits remarkable resistance to oxidation, acidic/alkaline environments, and pitting/crevice corrosion, extending product lifespan. |
Outstanding High-Temperature Performance | Retains structural integrity and mechanical properties even under extreme heat, making them suitable for applications like gas turbines and aerospace engines. |
Impressive Mechanical Strength | Offers exceptional resistance to deformation, cracking, and wear, ideal for components requiring high durability. |
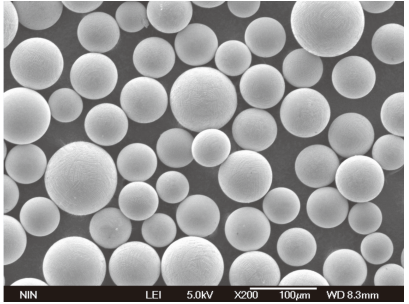
Processing Performance of Nickel-Based Powders
Nickel-based powders are not just remarkable materials themselves, but they also possess a unique advantage: their exceptional processing performance. This translates to their ability to thrive in various manufacturing techniques, making them highly sought-after in numerous industries. Let’s delve deeper into two key areas where these powders truly shine:
1. Powder Metallurgy (PM): This technique involves compacting and sintering metal powders to create near-net-shape components. Nickel-based powders excel in PM due to their:
- Fine and uniform particle size: This allows for efficient packing during compaction, leading to denser and stronger final products.
- Sphericity: Spherical particles flow better, enabling uniform distribution within the mold and reducing the risk of defects during compaction.
- High purity: This ensures consistent material properties and minimizes the formation of unwanted phases during sintering.
As a result, PM with nickel-based powders allows for the creation of intricate components with:
- Enhanced mechanical properties: These include high strength, good ductility, and excellent wear resistance.
- Complex geometries: The ability to create near-net-shape components significantly reduces the need for post-processing, minimizing material waste and production costs.
2. Additive Manufacturing (AM): Also known as 3D printing, AM utilizes computer-aided design (CAD) data to build objects layer-by-layer. Nickel-based powders are ideal for AM due to their:
- Sphericity: This ensures smooth flowability through the printing nozzle, enabling precise deposition and intricate design features.
- High melting point: This allows for the creation of structures with excellent thermal stability, ideal for high-temperature applications.
- Tailorable properties: By manipulating the composition and processing parameters, the properties of the final product can be customized to meet specific requirements.
Therefore, AM with nickel-based powders enables the production of:
Highly complex structures: This unlocks the possibility of creating intricate designs that are impossible with traditional manufacturing methods.
Lightweight components: The efficient use of material in AM combined with the inherent properties of nickel-based powders, such as high strength-to-weight ratio, results in lightweight yet robust structures.
Applications of Nickel-Based Powders
Nickel-based powders find extensive use across various industries due to their unique properties:
Industry | Application Examples |
---|---|
Aerospace: | Turbine blades, rocket engine components, heat exchangers, and landing gear. |
Automotive: | Engine components, exhaust manifolds, and catalytic converters. |
Energy: | Gas turbine components, heat exchangers, and chemical processing equipment. |
Chemical Processing: | Reactors, pumps, and valves for harsh environments. |
Electronics: | Battery electrodes, electrical contacts, and heat sinks. |
Medical: | Prosthetic implants, surgical instruments, and dental applications. |

Specific Metal Powder Models and Their Descriptions
While an exhaustive list exceeds the scope of this article, here are 10 commonly used nickel-based powder models with their defining characteristics:
IN625: This widely used alloy possesses excellent high-temperature strength, oxidation resistance, and fabricability, making it ideal for turbine blades, discs, and combustors in aerospace applications.
Inconel 625: Offers superior creep resistance and strength compared to IN625, making it suitable for hotter sections of gas turbines and combustors.
Inconel 718: Renowned for its exceptional strength, high-temperature performance, and good corrosion resistance, making it a popular choice for aerospace components, discs, and fasteners.
Rene 41: Delivers exceptional creep resistance and strength at very high temperatures, ideal for turbine blades and other hot-section components in jet engines.
AM350: A gas-atomized nickel-based superalloy powder specifically designed for additive manufacturing, offering a balance of strength, ductility, and high-temperature performance.
AWS A5.16 ERNi-1: A nickel welding powder known for its excellent weldability, corrosion resistance, and high-temperature strength, used for joining similar and dissimilar metals.
Nickel 200: A commercially pure nickel powder featuring high ductility, excellent electrical conductivity, and good corrosion resistance, used in electronics, electrodes, and chemical processing equipment.
Nickel 270: Offers better high-temperature strength compared to Nickel 200, making it suitable for applications requiring moderate strength at elevated temperatures.
Nickel 601: A nickel-chromium alloy powder known for its good oxidation resistance and high-temperature strength, used in electrical heating elements, furnace components, and heat exchangers.
Nickel-Copper: Combining nickel’s corrosion resistance with copper’s superior electrical conductivity, this powder finds application in brazing alloys, electrical contacts, and heat sinks.
Advantages and Limitations of Nickel-Based Powders
Pros:
- Exceptional mechanical properties: Nickel-based powders offer outstanding strength, wear resistance, and high-temperature performance, making them ideal for demanding applications.
- Superior corrosion resistance: They exhibit remarkable resistance to various corrosive environments, ensuring long-lasting performance and reduced maintenance costs.
- Versatility: These powders can be processed using various techniques like powder metallurgy and additive manufacturing, enabling the creation of complex and diverse components.
- Tailorable properties: By adjusting the composition, particle size, and processing methods, the properties of nickel-based powders can be fine-tuned for specific applications.
Cons:
- High cost: Compared to other materials, nickel-based powders can be more expensive due to the high cost of raw materials and complex processing involved.
- Brittleness: Certain types of nickel-based powders can be brittle, requiring careful handling and processing techniques to avoid cracking.
- Limited ductility: Compared to some materials like steel, nickel-based powders may exhibit lower ductility, limiting their suitability for applications requiring significant deformation.
Choosing the Right Powder
Selecting the most suitable nickel-based powder for your application requires considering several crucial factors:
- Intended application: The specific function and operating conditions of the component will significantly influence the required properties of the powder.
- Processing method: Whether you plan to use powder metallurgy, additive manufacturing, or other techniques will impact the powder’s desired characteristics.
- Mechanical properties needed: Consider the required strength, wear resistance, and high-temperature performance for your application.
- Corrosion resistance requirements: Evaluate the specific corrosive environment the component will encounter and choose a powder with adequate resistance.
- Cost considerations: While nickel-based powders offer exceptional properties, their cost might be a factor depending on your budget constraints.
Expert Opinions and Industry Trends
Industry experts acknowledge the growing demand for nickel-based powders driven by their unique combination of properties and the increasing adoption of additive manufacturing technologies. Advancements in powder production methods are expected to lead to more cost-effective and efficient production processes, further expanding their applications across various industries.
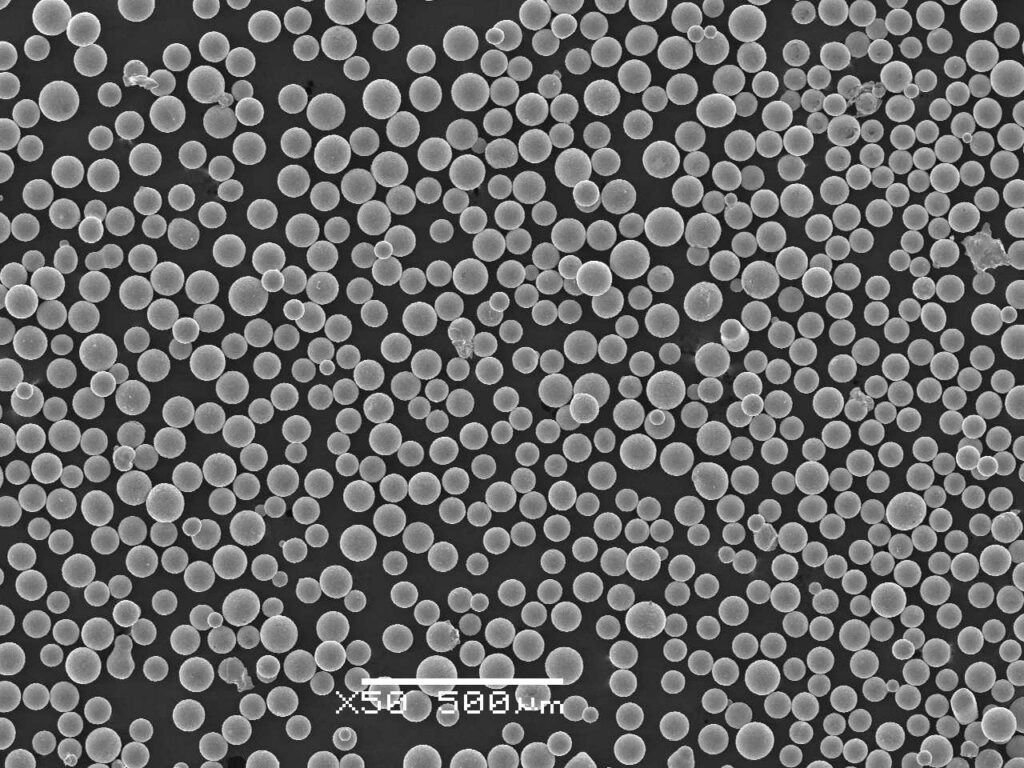
Conclusion
Nickel-based powders have established themselves as a valuable material in diverse industrial sectors due to their exceptional properties, versatility, and potential for advanced manufacturing techniques. By understanding their characteristics, advantages, limitations, and selection criteria, you can unlock their potential for creating high-performance and durable components in various demanding applications.
FAQs
Q: What are the typical particle sizes of nickel-based powders?
A: The particle size of nickel-based powders can vary depending on the application. They typically range from 10 to 150 microns, with finer particles offering better surface area and packing density, while coarser particles might improve flowability and reduce processing costs.
Q: Are nickel-based powders safe to handle?
A: Nickel dust can be harmful if inhaled. Proper safety precautions, including wearing appropriate personal protective equipment (PPE) such as masks and gloves, are crucial when handling and processing nickel-based powders.
Q: What are some emerging applications of nickel-based powders?
A: The increasing adoption of additive manufacturing is opening new possibilities for nickel-based powders in creating lightweight and intricate components for aerospace, medical implants, and other demanding applications. Research is also ongoing to explore their potential in energy storage solutions and catalysts.