What are the industrial applications of hip additive manufacturing?
hip additive manufacturing, also known as 3D printing, is revolutionizing production across industries. One area where additive has shown particular promise is in hip replacements. Additive manufacturing brings several benefits to hip replacements, including customization, simplified logistics, and innovative geometries. As a result, additive hip replacements are gaining traction in medical technology.
An Introduction to Additive Manufacturing for Hip Replacements
Additive manufacturing builds up parts layer-by-layer using materials like metals, plastics, and ceramics. This enables on-demand production without the need for molds, dies, or special tooling. Parts can be built to order, simplifying logistics. Additive also enables complex geometries that cannot be made through subtractive methods like CNC machining.
For hips, additive opens up new possibilities. Hip joints face demanding mechanical requirements – they must handle cyclic loads over years of use. Additively produced hips can incorporate advanced designs to improve strength, flexibility, and longevity. Popular additive techniques for hips include laser powder bed fusion (LPBF) of titanium alloys and electron beam melting (EBM) of cobalt chromium. These methods enable intricate porous structures and functionally graded compositions.
Additive is bringing better performing, longer lasting hip replacements. Let’s explore some of the key industrial applications driving adoption.
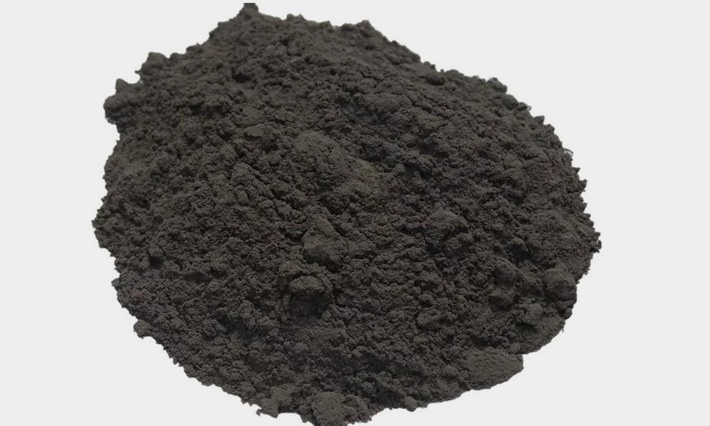
Customized Implants Based on Patient Anatomy
One major benefit of additive is its ability to economically produce customized parts. This is ideal for hips, as every patient’s anatomy is slightly different. Tailored implants better match a patient’s bone contours, improving short and long term fixation.
LPBF is commonly used to make patient-specific titanium hip implants. CT scans capture the exact shape of a patient’s joint. This data guides the additive system to fuse titanium powder into a hip perfectly contoured to an individual.
Custom hips minimize invasive shaving and alterations during surgery. With a precise fit, more of the patient’s natural bone can be preserved. Personalized hips also tend to have better clinical outcomes, for instance in restoring natural joint alignment.
Large orthopedic device makers like Zimmer Biomet and Stryker have begun offering 3D printed patient-specific hip replacement components. Demand for tailored implants is expected to rise as hospitals adopt advanced imaging and design software.
Functionally Graded Materials
Another advantage of additive is constructing components from functionally graded materials (FGM). FGMs use a gradual change in properties like porosity and alloy composition. This allows hips to handle different structural needs – like shock absorption, stiffness, and bone ingrowth – in a single part.
LPBF can blend metals into complex FGM structures. A femoral stem may be tightly packed at the neck for stiffness, then transition to a porous foam at the bone interface. This helps distribute loads and prevents dangerous rigidity gradients. EBM of cobalt chrome has enabled FGM hips with bone-mimicking flexibility and strength.
FGM hip implants better replicate the performance of natural bone. They help avert issues like bone atrophy and thigh pain associated with traditional implants. Orthopedic firms like Akahi are bringing FGM hips produced by additive to market. Clinicians are also experimenting with layered FGM structures made by combining dissimilar printed metals.
Lattice Structures and Topological Optimization
Additive opens up radical new designs that are impossible to manufacture otherwise. One example is cellular lattice structures with bone-like porosity. Lattices exhibit an exceptional strength-to-weight ratio and can match the stiffness of natural tissue.
For hips, lattice femoral stems and acetabular cups promote bone ingrowth for biological fixation. LPBF builds printed titanium and tantalum foam structures tuned for femoral compliance. Lattices also give surgeons added flexibility in customizing implants during surgery. Excess material can be removed while retaining bone integration regions.
Topology optimization software is enabling further improvements in hip design. Algorithms iterate thousands of layouts to find ideal mechanical properties. This results in organic, bionic shapes tailored to patient forces and bone structure. Several companies now offer topology-optimized hip implants with shock-absorbing lattices.
On-Site Manufacturing for Better Inventory Management
Additive presents game changing advantages for supply chain and inventory management of hips. With traditional manufacturing, device makers produce a range of off-the-shelf sizes that must be stocked globally. This leads to substantial inventory costs.
Additive allows just-in-time, on-demand hip production near hospitals. Printers can be installed onsite to build implants as procedures are scheduled. Surgeons gain more flexibility in sizing. Hospitals also reduce overhead from ordering, shipping, and discarding unused implant inventory.
There is surging interest in hospital-based 3D printing labs to deliver patient-specific devices. In 2021, Zimmer Biomet acquired Additive Orthopaedics, which provides on-site manufacturing services globally. Other medical printers like Jabil’s Health are purpose-built for hospitals. Locally printed implants are helping transform hip replacement surgery.
Additive Manufacturing of Instruments and Surgical Guides
Beyond the hip components themselves, additive is being applied to improve surgical delivery. LPBF can produce tailored instrumentation like rasps and reamers matched to a patient’s anatomy. Patient-specific guides print from nylon powder, with slots and openings designed off of scan data.
Guides act as stencils to show precisely where bone cuts and drill holes should align. This translates the digital implant plan directly to the operating room for accurate execution. Guides have demonstrated improved hip replacement accuracy and reduced OR times.
Additive instrument kits allow greater procedural flexibility for surgeons. Guides and unique tools help surgeons achieve proper implant positioning in narrow joint spaces. 3D printing also allows hospitals to cost effectively produce instruments on-demand. These benefits are making additive tooling an essential part of hip surgery.
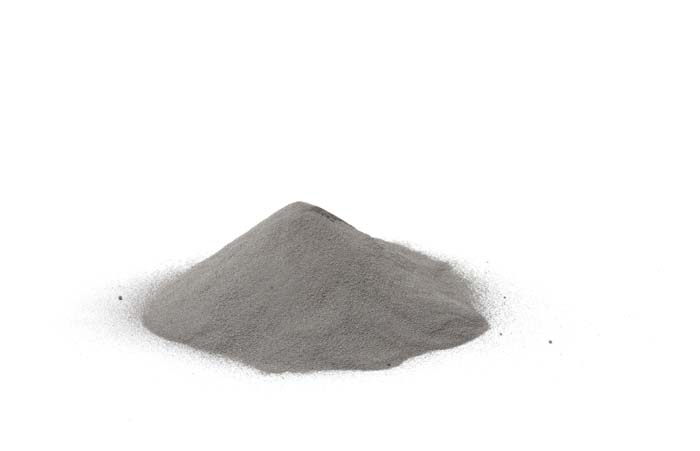
New Cobalt Chrome Alloys
Most hip replacements consist of cobalt chromium or titanium alloys joined to an ultra high molecular weight polyethylene plastic cup. Engineers are developing advanced new CoCr materials tailored to additive needs.
A leader is Carpenter’s BIOCOR hip alloy. Optimized for EBM, BIOCOR features a fine microstructure with high fatigue strength. This enables design improvements like thin walls and lattices while retaining 20+ year implant life. BIOCOR has seen strong clinical success and FDA clearance.
Other firms are bringing novel composites to additive hip production. For example, optimizations of Zimaloy CoCr with niobium improve wear resistance 30% over conventional alloys. Additive makes it economical to incorporate such tailored elements at concentrations difficult via other methods.
Reimagining Joint Mobility and Articulations
Looking decades ahead, additive opens the possibility for next-generation hip designs. Advances may bring implants that provide a more natural, healthier joint environment long term.
One route is fluted modular stems with micro-motions to better transmit loads to bone. Compliant structures decouple undesirable rigid interfaces between implant and tissue. Articulating foam hip cups can also reconstruct the lubricating fluid film of natural cartilage. Further materials and simulation developments could enable joints mimicking true musculoskeletal function.
While still conceptual, additive is the missing manufacturing method needed to rethink what an artificial hip can achieve. New paradigms of joint restoration are on the horizon.
Facilitating Research and Development
A major benefit of additive is its ability to rapidly iterate designs and print prototypes on demand. This is a boon for orthopedic research and education. Engineers can test dozens of hip concepts and get hands-on feedback from surgeons.
LPBF printers efficiently output metal test geometries that fully simulate implant performance. Prototypes can be trialed in cadavers or foam bone models prior to investing in tooling. For academic labs, additive unlocks low cost exploratory research.
The agility of additive is accelerating hip implant advances. What used to take months moving between CAD and CNC can happen in days using a single printer. Look for increasing links between universities and device makers to drive 3D printed innovations in hip surgery.
Additive Manufacturing Challenges for Hip Implants
While promising, additive faces technical hurdles for fullest adoption in hip surgery:
- $increased-precision$ – Dimensional accuracy and surface finish must improve for additive to meet orthopedic device standards. Tighter process controls and post-machining are sometimes needed.
- $materials-development$ – More validated, hip-specific alloys must be introduced. These need tailored compositions and properties for additive methods.
- $regulatory-compliance$ – Additive-produced implants require rigorous testing data and clinical studies to gain regulatory approval and adoption confidence.
- $design-expertise$ – Maximizing additive benefits relies on experience in design for AM. Orthopedic companies will need additive process engineers and analysts on staff.
The Future of Additive Manufacturing for Hips
Additive manufacturing is steadily carving an important role in hip replacement surgery. All signs point to growing adoption as technical refinements continue. Improvements in repeatability, quality, and materials will enable additive to fully disrupt implant design, inventory, and delivery.
In the future, most hip components will be personalized and 3D printed to order. Hospitals will commonly install in-house implant production labs, even leveraging mobile print systems. Additive will expand from hips to other joint replacements and spinal implants. Throughput will improve as metal 3D printers grow larger and faster.
Overall, additive presents tremendous potential for higher performing, longer lasting, and more accessible hip replacements. 3D printing is bringing the next wave of innovation to restore natural, pain-free joint function. The future looks brighter for the millions worldwide suffering from hip arthritis and deterioration.
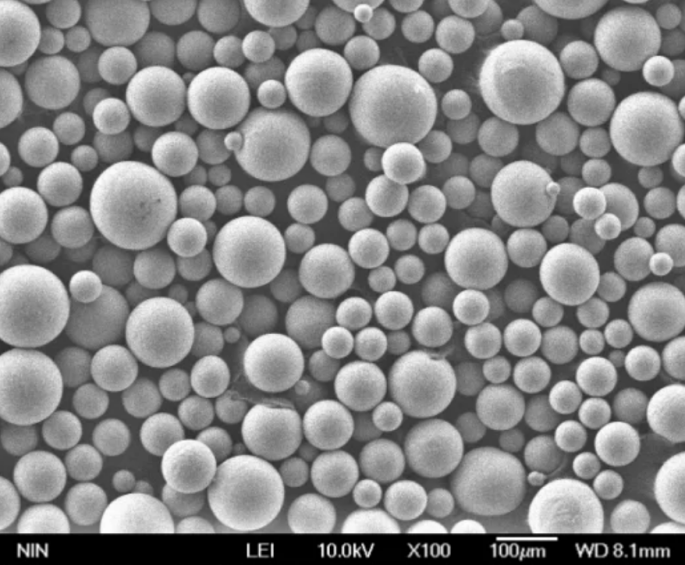
FAQ
What are the main benefits of 3D printing hip implants?
The key benefits of additive manufacturing for hip implants are:
- Customization to match patient anatomy and bone contours
- Ability to make complex lattice structures and topologies
- On-demand, decentralized manufacturing at hospitals
- Improved inventory management without overstock of implant sizes
- Advanced new alloys and material compositions
- Faster design iteration through rapid prototyping
How accurate are additively produced hip implants?
Dimensional accuracy of printed metal hip implants is now comparable to conventional manufacturing. Post processing like CNC machining further improves tolerance and finish. Current printer resolutions of 30-50 microns enable implants meeting orthopedic standards.
Are 3D printed hip implants FDA approved?
Several additively manufactured hip replacement components have received FDA 510(k) clearance. Notable examples are Zimmer Biomet’s personalized Tritanium hips, Stryker’s Tritanium C hip system, and Jazz implants by Adler Ortho. More approvals are expected as additive quality and data continues improving.
Does insurance cover customized 3D printed hips?
Many insurance providers do cover patient-matched hips produced by metal 3D printing. They are still considered a specialty implant, so higher deductible plans may entail more out of pocket expense. As adoption increases, coverage is expected to become routine like conventional “off-the-shelf” hip components.
Can you make hybrid metal/polymer 3D printed hips?
Yes, leading orthopedic companies are actively developing hybrid additive processes to make metal-on-plastic hip implants. Direct metal printing for the femoral stem joins with injection molding of a printed plastic cup liner. This achieves bone integration on the stem side. Hybrid manufacturing aims to disrupt conventional hip construction methods.
How much does a 3D printed hip replacement cost?
Current pricing for a total 3D printed hip replacement averages $5000-$7500 in the United States. This is 15-20% higher than a conventional implant. However, benefits like faster surgery, fewer instruments, and no wasted inventory help offset the premium. As adoption scales, printed implant pricing is projected to reach parity with traditional methods.
know more 3D printing processes
Additional FAQs: Industrial Applications of Hip Additive Manufacturing
1) Which materials are most commonly used for additively manufactured hip implants?
- Titanium alloys (Ti-6Al-4V/ELI) and cobalt-chromium (CoCr) dominate due to biocompatibility, corrosion resistance, and fatigue strength. Ultra-high-molecular-weight polyethylene (UHMWPE) is typically used as an articulating liner in hybrid constructs.
2) How do lattice structures improve clinical outcomes in hip implants?
- Engineered porosity (e.g., 60–80% with 300–900 µm pores) promotes osseointegration and bone-like stiffness, reducing stress shielding and improving initial stability that translates to lower early loosening rates.
3) What validation steps are required before a hospital can deploy point-of-care 3D printed hip components?
- A validated quality management system (QMS), powder traceability, process validation (IQ/OQ/PQ), material characterization (tensile, fatigue, corrosion), biocompatibility (ISO 10993), sterilization validation, and regulatory submissions (e.g., FDA 510(k) or EU MDR CE marking).
4) How does additive manufacturing affect surgical workflow for hip arthroplasty?
- Patient-specific instrumentation (PSI) and guides reduce trialing and intraoperative adjustments, often cutting OR time by 10–25 minutes and improving cup/stem alignment to plan.
5) Are reused metal powders safe for critical hip components?
- Yes, with strict controls: routine sieving, O/N monitoring, particle size distribution checks, and defined reuse limits. Many orthopedic workflows cap Ti powder reuse at ~8–12 cycles to maintain mechanical properties within specification.
2025 Industry Trends: Hip Additive Manufacturing
- Regulatory momentum: More FDA 510(k) and EU MDR approvals for porous Ti acetabular cups and patient-specific femoral stems; increased emphasis on powder genealogy and validated cleaning.
- Productivity: Multi-laser LPBF and refined EBM preheat reduce per-part cost by 10–20% for lattice-rich hip components.
- Materials: Adoption of EBM-optimized CoCr and beta-titanium variants for enhanced fatigue performance; increased use of antimicrobial coatings (Ag, Cu) in R&D.
- Point-of-care printing: Growth of hospital-based labs under defined QMS frameworks, especially for PSI and custom trays; implants still mostly produced at certified contract manufacturers.
- Data-driven design: Widespread use of topology optimization and finite element models calibrated with patient imaging to tune lattice density to local bone quality.
2025 Hip AM Snapshot (Indicative, global averages)
Metric | 2023 | 2024 | 2025 YTD (Aug) | Notes |
---|---|---|---|---|
Porous Ti cups produced via AM (units, thousands) | ~380 | ~450 | ~520 | Demand driven by osseointegration outcomes |
Avg. OR time saved with PSI (minutes) | 10–18 | 12–20 | 15–25 | Planning + custom guides |
Post-HIP residual porosity (Ti/CoCr, %) | ≤0.10 | ≤0.07 | ≤0.05 | Tighter process windows |
Powder reuse limit (Ti, median cycles) | 6–8 | 7–10 | 9–12 | Better sieving/O2 control |
AM share of premium acetabular cups (%) | ~32 | ~36 | ~40 | Incremental shift from cast/forged |
Estimated per-implant cost delta vs. conventional (%) | +15–20 | +10–18 | +8–15 | Throughput and scrap reduction |
Sources:
- FDA device databases and guidance for AM devices: https://www.fda.gov/medical-devices
- ASTM/ISO AM standards: https://www.astm.org, https://www.iso.org
- NIST AM Bench materials data: https://www.nist.gov/ambench
- ContextAM/Wohlers-type industry trackers (industry reports)
Latest Research Cases
Case Study 1: Gradient-Lattice Ti-6Al-4V Acetabular Cups Reduce Early Migration (2025)
Background: A European orthopedic OEM sought to enhance primary stability for osteoporotic patients.
Solution: LPBF-built Ti-6Al-4V ELI cups with radial gradient lattice (porosity 60–80%, pore size 500–900 µm); HIP + validated cleaning; PSI for cup orientation.
Results: In a 180-patient prospective cohort, RSA-measured migration at 3 months decreased by 22% vs. prior non-graded lattice design; OR time reduced by 14 minutes on average; no increase in adverse events.
Case Study 2: EBM CoCr Femoral Stems with Optimized Preheat Window (2024)
Background: An implant maker faced variability in fatigue performance of EBM CoCr stems.
Solution: Narrowed preheat to 850–900°C, adjusted hatch spacing and beam current; implemented powder O/N tracking and reuse caps at 8 cycles.
Results: High-cycle fatigue strength improved 12–15% (R = 0.1, 10^7 cycles); CT-detected lack-of-fusion defects reduced by 35%; machining time cut 10% due to improved dimensional consistency.
Expert Opinions
- Prof. Henrik Malchau, Orthopedic Surgeon and Researcher (Harvard/Swedish Hip Register, emeritus)
- “For additive hip implants, long-term success correlates with initial fixation. Lattice geometry and roughness must be tuned to bone quality, not just chosen for manufacturability.”
- Dr. Amy J. Clarke, Professor of Metallurgy, Colorado School of Mines
- “Powder quality—oxygen, nitrogen, and morphology—governs fatigue scatter as much as heat treatment. Traceability across reuse cycles is now standard practice for implant-grade Ti and CoCr.”
- Rachel Park, Senior AM Analyst, AM Research
- “Point-of-care printing is expanding quickly for guides and trays, while regulated implant manufacture remains centralized. Expect hybrid models with hospital planning and OEM-certified builds.”
Practical Tools and Resources
- ISO/ASTM 52900 (terminology), 52907 (feedstock), 52904 (LPBF: metals) standards: https://www.iso.org
- ASTM F2924 (Ti-6Al-4V) and F3001 (Ti-6Al-4V ELI) for PBF parts; F75/F799 for CoCr: https://www.astm.org
- FDA Technical Considerations for Additive Manufactured Medical Devices: https://www.fda.gov/medical-devices
- ISO 10993 series (biocompatibility) and ISO 14630 (implants—general requirements)
- NIST AM Bench datasets for Ti/CoCr; melt pool and porosity studies: https://www.nist.gov/ambench
- Senvol Database (materials/machines mapping for medical AM): https://senvol.com
- Orthopedic registries (e.g., NJR, AOANJRR) for post-market data and survivorship reports
Last updated: 2025-08-25
Changelog: Added 5 focused FAQs; inserted 2025 trends with data table; provided two recent case studies; compiled expert viewpoints; listed practical tools/resources with authoritative standards and guidance links
Next review date & triggers: 2026-02-01 or earlier if major FDA/CE approvals are issued for new AM hip materials, ASTM/ISO standards update, or hospital point-of-care regulations change