¿Cuáles son las aplicaciones industriales de fabricación aditiva de caderas?
a fabricación aditiva de caderas, también conocida como impresión 3D, está revolucionando la producción en todos los sectores. Un ámbito en el que la fabricación aditiva se ha mostrado especialmente prometedora es el de las prótesis de cadera. La fabricación aditiva aporta varias ventajas a las prótesis de cadera, como la personalización, la simplificación de la logística y las geometrías innovadoras. Como resultado, las prótesis de cadera aditivas están ganando terreno en la tecnología médica.
Introducción a la fabricación aditiva de prótesis de cadera
La fabricación aditiva crea piezas capa a capa utilizando materiales como metales, plásticos y cerámicas. Esto permite la producción bajo demanda sin necesidad de moldes, matrices o herramientas especiales. Las piezas pueden fabricarse por encargo, lo que simplifica la logística. La aditividad también permite geometrías complejas que no pueden fabricarse con métodos sustractivos como el mecanizado CNC.
En el caso de las caderas, los aditivos abren nuevas posibilidades. Las articulaciones de cadera se enfrentan a exigentes requisitos mecánicos: deben soportar cargas cíclicas durante años de uso. Las caderas producidas aditivamente pueden incorporar diseños avanzados para mejorar su resistencia, flexibilidad y longevidad. Entre las técnicas aditivas más populares para caderas se encuentran la fusión de lecho de polvo con láser (LPBF) de aleaciones de titanio y la fusión por haz de electrones (EBM) de cromo-cobalto. Estos métodos permiten crear estructuras porosas complejas y composiciones funcionales graduadas.
Los aditivos están mejorando el rendimiento y la duración de las prótesis de cadera. Exploremos algunas de las principales aplicaciones industriales que impulsan su adopción.
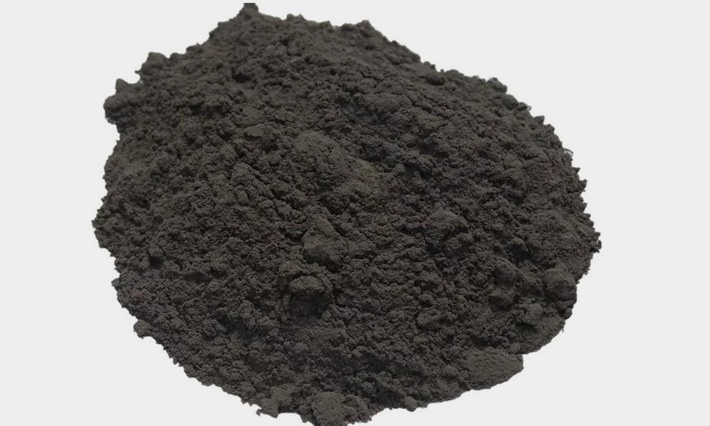
Implantes personalizados según la anatomía del paciente
Una de las principales ventajas de los aditivos es su capacidad para producir piezas personalizadas de forma económica. Esto es ideal para las caderas, ya que la anatomía de cada paciente es ligeramente diferente. Los implantes a medida se adaptan mejor al contorno óseo del paciente, mejorando la fijación a corto y largo plazo.
El LPBF se utiliza habitualmente para fabricar implantes de cadera de titanio específicos para cada paciente. Las tomografías computarizadas capturan la forma exacta de la articulación del paciente. Estos datos guían al sistema de aditivos para fusionar el polvo de titanio en una cadera perfectamente adaptada a cada persona.
Las caderas a medida reducen al mínimo el afeitado invasivo y las alteraciones durante la intervención quirúrgica. Con un ajuste preciso, puede conservarse más hueso natural del paciente. Las caderas personalizadas también suelen tener mejores resultados clínicos, por ejemplo al restablecer la alineación natural de la articulación.
Grandes fabricantes de dispositivos ortopédicos como Zimmer Biomet y Stryker han empezado a ofrecer componentes de prótesis de cadera impresos en 3D específicos para cada paciente. Se espera que la demanda de implantes a medida aumente a medida que los hospitales adopten programas avanzados de imagen y diseño.
Materiales funcionales
Otra ventaja de los aditivos es la construcción de componentes a partir de materiales funcionalmente graduados (FGM). Los FGM modifican gradualmente propiedades como la porosidad y la composición de la aleación. De este modo, las caderas pueden responder a distintas necesidades estructurales -como la absorción de impactos, la rigidez y el crecimiento óseo- en una sola pieza.
El LPBF puede mezclar metales en estructuras FGM complejas. Un vástago femoral puede ser muy rígido en el cuello y luego pasar a una espuma porosa en la interfaz ósea. Esto ayuda a distribuir las cargas y evita peligrosos gradientes de rigidez. La EBM de cromo-cobalto ha permitido fabricar caderas con FGM que imitan la flexibilidad y resistencia del hueso.
Los implantes de cadera FGM reproducen mejor el comportamiento del hueso natural. Ayudan a evitar problemas como la atrofia ósea y el dolor de muslo asociados a los implantes tradicionales. Empresas ortopédicas como Akahi están introduciendo en el mercado caderas de MGF fabricadas mediante aditivos. Los médicos también están experimentando con estructuras estratificadas de MGF fabricadas combinando metales impresos distintos.
Estructuras reticulares y optimización topológica
La aditividad abre la puerta a diseños radicalmente nuevos, imposibles de fabricar de otro modo. Un ejemplo son las estructuras celulares enrejadas con porosidad similar a la de los huesos. Las celosías presentan una excepcional relación resistencia-peso y pueden igualar la rigidez del tejido natural.
En el caso de las caderas, los vástagos femorales enrejados y las cazoletas acetabulares favorecen el crecimiento óseo para una fijación biológica. LPBF fabrica estructuras impresas de titanio y espuma de tantalio adaptadas a la conformidad femoral. Los entramados también ofrecen a los cirujanos una mayor flexibilidad a la hora de personalizar los implantes durante la intervención. El material sobrante puede eliminarse conservando las regiones de integración ósea.
Los programas informáticos de optimización topológica permiten mejorar aún más el diseño de caderas. Los algoritmos iteran miles de diseños para encontrar las propiedades mecánicas ideales. El resultado son formas orgánicas y biónicas adaptadas a las fuerzas del paciente y a la estructura ósea. Varias empresas ofrecen ahora implantes de cadera con topología optimizada y celosías amortiguadoras.
Fabricación in situ para una mejor gestión del inventario
La aditiva presenta ventajas que cambian las reglas del juego para la cadena de suministro y la gestión del inventario de caderas. Con la fabricación tradicional, los fabricantes de dispositivos producen una gama de tamaños estándar que deben almacenarse en todo el mundo. Esto conlleva importantes costes de inventario.
La tecnología aditiva permite la producción de caderas justo a tiempo y a demanda cerca de los hospitales. Las impresoras pueden instalarse in situ para fabricar implantes a medida que se programan los procedimientos. Los cirujanos ganan flexibilidad en el dimensionamiento. Los hospitales también reducen los gastos generales derivados de pedir, enviar y desechar el inventario de implantes no utilizados.
Crece el interés por los laboratorios hospitalarios de impresión 3D para fabricar dispositivos específicos para cada paciente. En 2021, Zimmer Biomet adquirió Additive Orthopaedics, que presta servicios de fabricación in situ en todo el mundo. Otras impresoras médicas, como Jabil's Health, están diseñadas específicamente para hospitales. Los implantes impresos localmente están ayudando a transformar la cirugía de prótesis de cadera.
Fabricación aditiva de instrumentos y guías quirúrgicas
Más allá de los propios componentes de la cadera, la aditividad se está aplicando para mejorar la aplicación quirúrgica. El LPBF puede producir instrumentos a medida, como escofinas y escariadores, adaptados a la anatomía del paciente. Las guías específicas para cada paciente se imprimen a partir de polvo de nailon, con ranuras y aberturas diseñadas a partir de datos de escaneado.
Las guías actúan como plantillas para mostrar con precisión dónde deben alinearse los cortes óseos y los orificios de perforación. Esto traslada el plan de implante digital directamente al quirófano para una ejecución precisa. Las guías han demostrado mejorar la precisión de las prótesis de cadera y reducir el tiempo de quirófano.
Los kits de instrumentos aditivos permiten a los cirujanos una mayor flexibilidad en los procedimientos. Las guías y herramientas exclusivas ayudan a los cirujanos a colocar correctamente los implantes en espacios articulares estrechos. La impresión en 3D también permite a los hospitales producir instrumentos bajo demanda de forma rentable. Estas ventajas están convirtiendo el instrumental aditivo en una parte esencial de la cirugía de cadera.
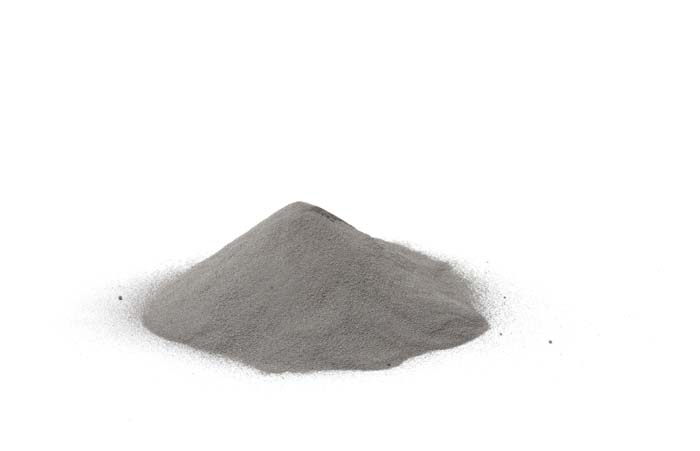
Nuevas aleaciones de cromo-cobalto
La mayoría de las prótesis de cadera consisten en aleaciones de cromo-cobalto o titanio unidas a un cotilo de plástico de polietileno de ultra alto peso molecular. Los ingenieros están desarrollando nuevos materiales avanzados de CoCr adaptados a las necesidades aditivas.
Uno de los líderes es la aleación de cadera BIOCOR de Carpenter. Optimizada para EBM, BIOCOR presenta una microestructura fina con alta resistencia a la fatiga. Esto permite mejoras en el diseño, como paredes finas y celosías, al tiempo que mantiene una vida útil del implante de más de 20 años. BIOCOR ha obtenido un gran éxito clínico y la autorización de la FDA.
Otras empresas están incorporando nuevos compuestos a la producción de caderas aditivas. Por ejemplo, las optimizaciones de Zimaloy CoCr con niobio mejoran la resistencia al desgaste 30% respecto a las aleaciones convencionales. La aditivación hace que resulte económico incorporar estos elementos a medida en concentraciones difíciles de conseguir por otros métodos.
Reimaginar la movilidad articular y las articulaciones
De cara a las próximas décadas, la aditividad abre la posibilidad de diseños de cadera de nueva generación. Los avances pueden traer implantes que proporcionen un entorno articular más natural y saludable a largo plazo.
Una vía son los vástagos modulares estriados con micromovimientos para transmitir mejor las cargas al hueso. Las estructuras flexibles desacoplan las indeseables interfaces rígidas entre implante y tejido. Las copas de cadera de espuma articulada también pueden reconstruir la película de fluido lubricante del cartílago natural. Otros desarrollos en materiales y simulación podrían permitir articulaciones que imiten la verdadera función musculoesquelética.
Aunque todavía es conceptual, el aditivo es el método de fabricación que falta para replantear lo que puede conseguir una cadera artificial. Se vislumbran nuevos paradigmas de restauración articular.
Facilitar la investigación y el desarrollo
Una de las principales ventajas de los aditivos es su capacidad para iterar rápidamente los diseños e imprimir prototipos bajo demanda. Esto supone una gran ventaja para la investigación y la enseñanza ortopédicas. Los ingenieros pueden probar docenas de conceptos de cadera y obtener información práctica de los cirujanos.
Las impresoras LPBF producen con eficacia geometrías metálicas de prueba que simulan plenamente el rendimiento del implante. Los prototipos pueden probarse en cadáveres o modelos óseos de espuma antes de invertir en herramientas. Para los laboratorios académicos, la tecnología aditiva permite realizar investigaciones exploratorias de bajo coste.
La agilidad de los aditivos está acelerando los avances en implantes de cadera. Lo que antes llevaba meses entre CAD y CNC puede hacerse en días con una sola impresora. Es de esperar que los vínculos entre las universidades y los fabricantes de dispositivos aumenten para impulsar las innovaciones impresas en 3D en la cirugía de cadera.
Retos de la fabricación aditiva para implantes de cadera
Aunque prometedores, los aditivos se enfrentan a obstáculos técnicos para su plena adopción en la cirugía de cadera:
- $precisión aumentada$ - La precisión dimensional y el acabado superficial deben mejorar para que los aditivos cumplan las normas de los dispositivos ortopédicos. A veces son necesarios controles de proceso más estrictos y un mecanizado posterior.
- $desarrollo de materiales$ - Hay que introducir aleaciones más validadas y específicas para la cadera. Estas necesitan composiciones y propiedades a medida para los métodos aditivos.
- 1TP4Cumplimiento de la normativa$ - Los implantes producidos mediante aditivos requieren rigurosos datos de pruebas y estudios clínicos para obtener la aprobación reglamentaria y la confianza de los usuarios.
- $experiencia en diseño$ - Para aprovechar al máximo las ventajas de los aditivos es necesario tener experiencia en diseño para AM. Las empresas ortopédicas necesitarán ingenieros y analistas de procesos aditivos en plantilla.
El futuro de la fabricación aditiva de caderas
La fabricación aditiva está adquiriendo cada vez más importancia en la cirugía de prótesis de cadera. Todo apunta a que su adopción irá en aumento a medida que continúen los avances técnicos. Las mejoras en la repetibilidad, la calidad y los materiales permitirán que la fabricación aditiva altere por completo el diseño, el inventario y la entrega de los implantes.
En el futuro, la mayoría de los componentes de la cadera se personalizarán e imprimirán en 3D por encargo. Los hospitales instalarán habitualmente laboratorios internos de producción de implantes, incluso aprovechando sistemas de impresión móviles. La aditividad se extenderá de las caderas a otras prótesis articulares e implantes de columna. El rendimiento mejorará a medida que las impresoras 3D de metal sean más grandes y rápidas.
En general, la impresión aditiva presenta un enorme potencial para lograr prótesis de cadera de mayor rendimiento, más duraderas y más accesibles. La impresión 3D está trayendo la próxima ola de innovación para restaurar el funcionamiento natural y sin dolor de las articulaciones. El futuro parece más prometedor para los millones de personas de todo el mundo que sufren artritis y deterioro de la cadera.
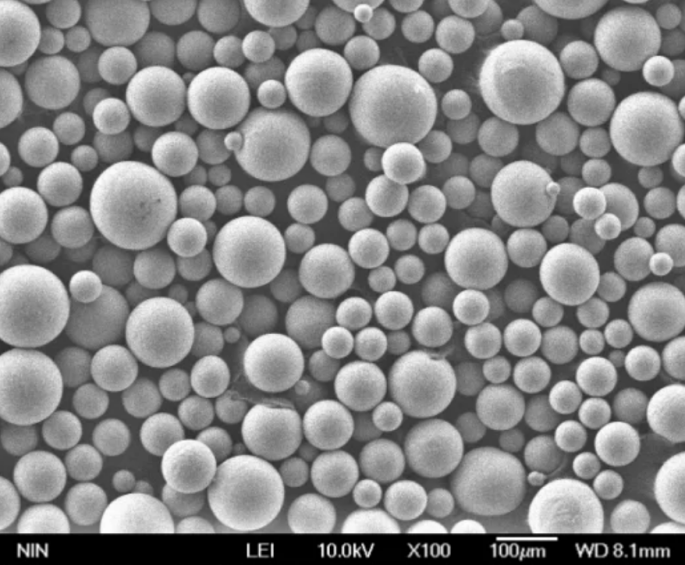
Preguntas más frecuentes
¿Cuáles son las principales ventajas de los implantes de cadera impresos en 3D?
Las principales ventajas de la fabricación aditiva para implantes de cadera son:
- Personalización para adaptarse a la anatomía del paciente y a los contornos óseos
- Capacidad para crear estructuras reticulares y topologías complejas
- Fabricación a la carta y descentralizada en hospitales
- Mejor gestión del inventario sin exceso de existencias de tamaños de implantes
- Nuevas aleaciones avanzadas y composiciones de materiales
- Iteración más rápida del diseño gracias a la creación rápida de prototipos
¿Hasta qué punto son precisos los implantes de cadera fabricados aditivamente?
La precisión dimensional de los implantes metálicos impresos de cadera es ahora comparable a la de la fabricación convencional. El procesamiento posterior, como el mecanizado CNC, mejora aún más la tolerancia y el acabado. Las resoluciones actuales de las impresoras, de 30-50 micras, permiten fabricar implantes que cumplen las normas ortopédicas.
¿Están aprobados por la FDA los implantes de cadera impresos en 3D?
Varios componentes de prótesis de cadera de fabricación aditiva han recibido la autorización 510(k) de la FDA. Ejemplos notables son las caderas Tritanium personalizadas de Zimmer Biomet, el sistema de cadera Tritanium C de Stryker y los implantes Jazz de Adler Ortho. Se esperan más aprobaciones a medida que sigan mejorando la calidad y los datos sobre aditivos.
¿Cubre el seguro las caderas personalizadas impresas en 3D?
Muchas compañías de seguros cubren las caderas adaptadas al paciente producidas mediante impresión metálica en 3D. Siguen considerándose un implante especializado, por lo que los planes con deducibles más elevados pueden conllevar más gastos de bolsillo. A medida que aumente su adopción, se espera que la cobertura se convierta en rutina, como ocurre con los componentes de cadera convencionales.
¿Se pueden fabricar caderas híbridas de metal y polímero impresas en 3D?
Sí, las principales empresas ortopédicas están desarrollando activamente procesos aditivos híbridos para fabricar implantes de cadera de metal sobre plástico. La impresión directa de metal para el vástago femoral se une al moldeo por inyección de un revestimiento de plástico impreso. De este modo se consigue la integración ósea en el lado del vástago. La fabricación híbrida pretende alterar los métodos convencionales de construcción de caderas.
¿Cuánto cuesta una prótesis de cadera impresa en 3D?
El precio actual de una prótesis total de cadera impresa en 3D es de $5000-$7500 de media en Estados Unidos. Esto es 15-20% más caro que un implante convencional. Sin embargo, ventajas como una intervención quirúrgica más rápida, menos instrumental y la eliminación de existencias innecesarias ayudan a compensar el sobreprecio. A medida que aumente su adopción, se prevé que el precio de los implantes impresos alcance la paridad con los métodos tradicionales.