1. Introduction
In the ever-evolving field of manufacturing, additive manufacturing, also known as 3D printing, has emerged as a groundbreaking technology. It enables the creation of complex objects layer by layer, offering unparalleled design freedom and efficiency. At the heart of this technology lies additive manufacturing powders, the key building blocks that make the magic happen.
2. What is Additive Manufacturing?
Additive manufacturing is a process of fabricating three-dimensional objects by adding material layer by layer, as opposed to traditional subtractive methods that involve cutting, drilling, or shaping a block of material. This transformative technology has found applications in various industries, including aerospace, automotive, healthcare, and consumer goods.
3. The Role of Powders in Additive Manufacturing
Additive manufacturing powders play a pivotal role in the success of the 3D printing process. These powders, composed of various materials such as metals, polymers, and ceramics, serve as the feedstock for creating intricate and precise parts. The choice of powder material significantly impacts the final product’s properties, including strength, durability, and appearance.
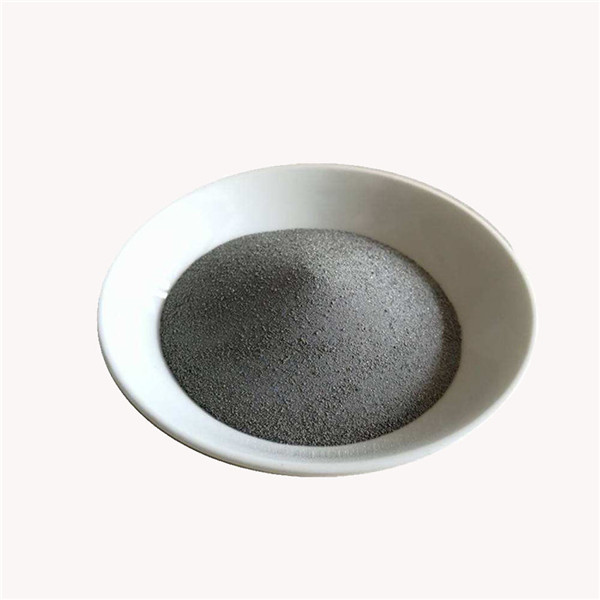
4. Types of Additive Manufacturing Powders
4.1 Metal Powders
Metal powders are widely used in additive manufacturing to produce functional and structural components. Metals such as aluminum, titanium, stainless steel, and nickel-based alloys find applications in industries requiring high-performance parts, like aerospace and medical implants.
4.2 Polymer Powders
Polymer powders are popular in additive manufacturing due to their versatility, ease of use, and cost-effectiveness. These powders consist of various thermoplastics, including ABS, PLA, and nylon, and are commonly used in industries such as consumer goods, prototyping, and healthcare.
4.3 Ceramic Powders
Ceramic powders enable the production of objects with exceptional thermal, electrical, and mechanical properties. Additive manufacturing with ceramics finds applications in industries such as electronics, aerospace, and automotive, where high-temperature stability and wear resistance are crucial. Ceramic powders like alumina, zirconia, and silicon carbide are commonly used in additive manufacturing processes.
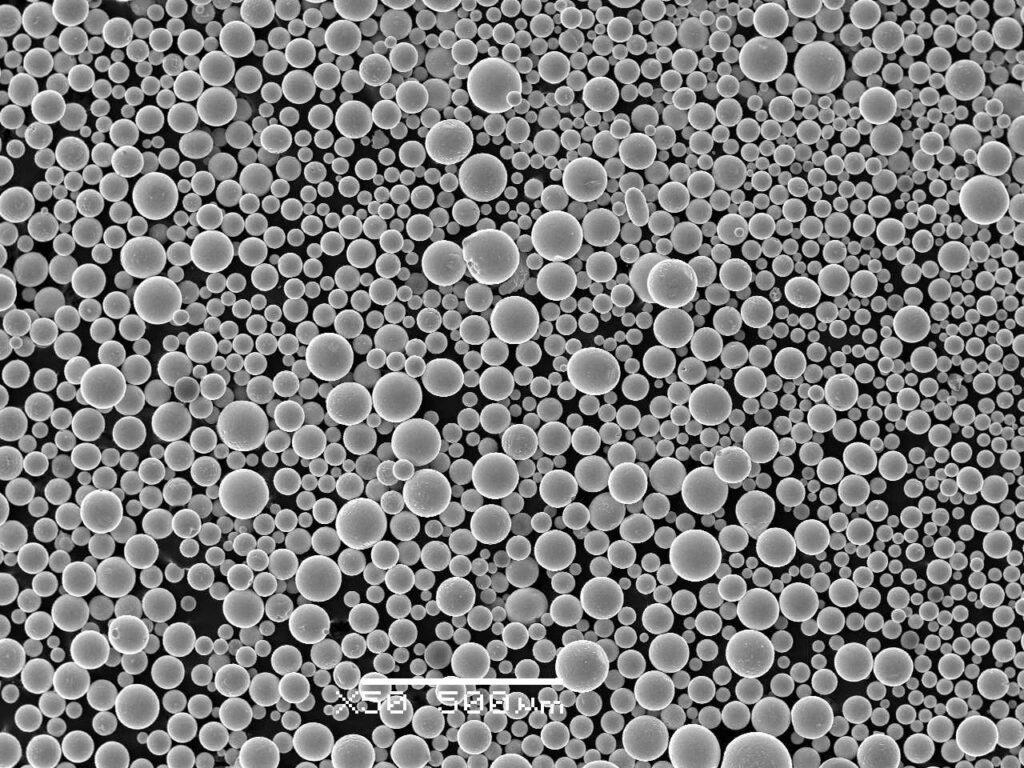
5. Powder Properties for Additive Manufacturing
To ensure successful additive manufacturing, several powder properties must be carefully considered:
5.1 Particle Size and Distribution
The particle size and distribution of the powder have a direct impact on the printed object’s resolution and surface quality. Fine powders with a narrow size distribution are preferred for achieving high levels of detail and accuracy.
5.2 Powder Flowability
Good powder flowability is essential for uniform powder spreading and layer formation during the 3D printing process. Powders with poor flowability can lead to defects, such as uneven layer thickness or incomplete filling of complex geometries.
5.3 Powder Density
Powder density affects the packing efficiency and porosity of the printed parts. Optimal powder density ensures the desired mechanical properties and dimensional accuracy of the final product.
5.4 Powder Morphology
Powder morphology, including shape and surface characteristics, influences powder flowability, packing behavior, and interparticle interactions. Spherical or irregularly shaped powders have different flow and compaction characteristics.
5.5 Chemical Composition
The chemical composition of the powder material determines the properties of the final printed part. Different alloys or polymers offer unique mechanical, thermal, and electrical characteristics, allowing for a wide range of applications.
5.6 Contamination and Purity
Contamination in powders can lead to defects and compromised material properties. It is crucial to ensure high levels of purity and minimize impurities, such as foreign particles, oxides, or moisture.
5.7 Moisture Content
Moisture content in powders can adversely affect the printing process and the quality of the printed parts. Controlling and monitoring moisture levels is vital to prevent defects like porosity and cracking.
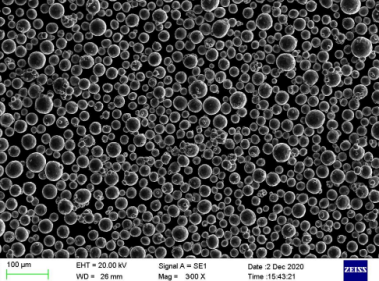
6. Powder Preparation for Additive Manufacturing
To optimize powder performance in additive manufacturing, proper powder preparation techniques are employed:
6.1 Atomization
Atomization is the primary method for producing metal powders used in additive manufacturing. It involves the conversion of molten metal into fine droplets through processes like gas or water atomization.
6.2 Gas or Water Atomization
Gas atomization involves spraying molten metal with high-pressure gas, resulting in the formation of fine powder particles. Water atomization, on the other hand, utilizes water jets to break up the molten metal stream into droplets that solidify into powder.
6.3 Powder Blending and Sieving
Powder blending ensures homogeneity and consistency of the powder composition, especially in the case of metal alloys. Sieving is performed to remove oversized or undersized particles, ensuring a desired particle size range.
7. Powder Handling and Storage
Proper handling and storage of additive manufacturing powders are critical to maintain their quality and performance:
7.1 Environmental Control
Powders should be stored in controlled environments, free from moisture, contaminants, and temperature fluctuations. Humidity and temperature can affect powder properties, such as flowability and reactivity.
7.2 Moisture Control
Moisture absorption by powders can lead to powder clumping, agglomeration, and reduced flowability. Storage conditions with low humidity levels and moisture-resistant packaging help mitigate moisture-related issues.
7.3 Contamination Prevention
Strict cleanliness measures must be implemented to prevent cross-contamination between different powder materials. Dedicated storage containers, handling equipment, and procedures should be in place to avoid mixing powders.
7.4 Segregation Prevention
Powder segregation, where particles separate based on size or density, can occur during handling or storage. Regular gentle mixing or blending of powders helps prevent segregation and ensures a consistent powder composition for reliable printing results.
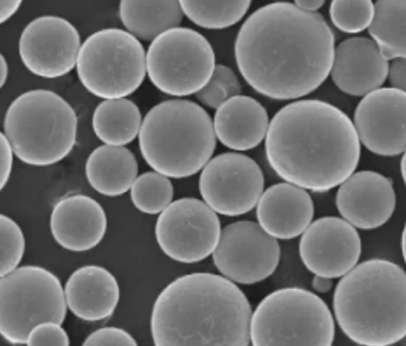
8. Quality Control in Additive Manufacturing Powders
Maintaining quality control in additive manufacturing powders is crucial for achieving consistent and reliable print outcomes:
8.1 Testing and Characterization
Thorough testing and characterization of powders help assess their suitability for additive manufacturing. Techniques such as particle size analysis, flowability testing, chemical analysis, and mechanical testing ensure compliance with desired specifications.
8.2 Certification and Standards
Certification programs and industry standards play a vital role in ensuring the quality and reliability of additive manufacturing powders. Adhering to recognized certifications and standards provides confidence in the material’s performance and compatibility.
8.3 Traceability
Establishing traceability systems helps track the origin, processing, and handling of additive manufacturing powders. This traceability ensures accountability and allows for identification and resolution of any quality issues that may arise.
9. Challenges in Additive Manufacturing Powders
Despite the significant advancements in additive manufacturing powders, several challenges remain:
9.1 Powder Reuse and Recycling
Efficient powder reuse and recycling strategies are necessary to minimize waste and reduce costs. Developing methods to recover and reprocess unused or excess powders can contribute to sustainability and cost-effectiveness.
9.2 Material Compatibility
Not all materials are suitable for additive manufacturing. Compatibility between powders and printing processes must be considered to ensure optimal results. Material development and testing are ongoing to expand the range of printable materials.
9.3 Powder Degradation
Repeated usage and exposure to environmental factors can lead to powder degradation. Factors such as oxidation, moisture absorption, and particle breakage can impact powder performance and require careful monitoring and handling.
9.4 Cost and Availability
Certain powders, especially specialized or rare materials, can be expensive and may have limited availability. Balancing the cost and availability of powders with desired material properties is a challenge that the industry continues to address.
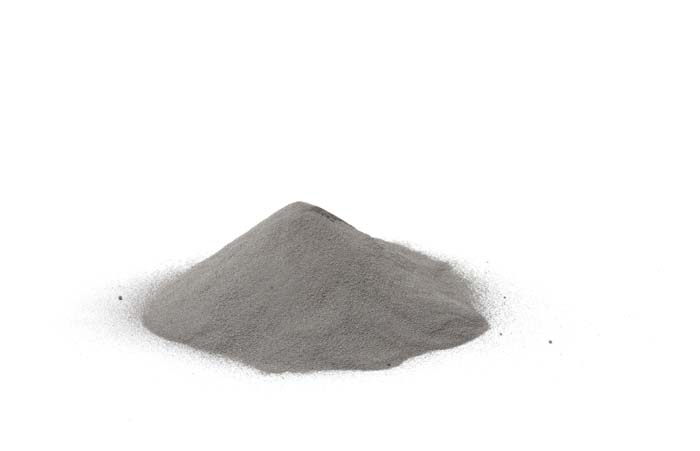
10. Future Trends in Additive Manufacturing Powders
The field of additive manufacturing powders is continually evolving, and several exciting trends are shaping its future:
- Advancements in powder atomization techniques to produce powders with tailored properties and improved quality.
- Development of new materials, including hybrid powders and composites, expanding the range of applications.
- Integration of smart materials with functionalities like sensing, self-healing, or shape-memory properties, enabling innovative designs and applications.
- Enhanced powder recycling and sustainability measures to reduce waste and promote a circular economy.
- Continued research and development in powder characterization and quality control techniques for more precise and reliable printing processes.
11. Conclusion
Additive manufacturing powders are indispensable components that drive the success of 3D printing technology. The careful selection, handling, and preparation of powders, along with quality control measures, ensure optimal print outcomes. Despite challenges, ongoing research and advancements in powder materials and processing techniques promise a future of expanded possibilities and applications in additive manufacturing.
FAQs (Frequently Asked Questions)
What are additive manufacturing powders?
Additive manufacturing powders are materials, such as metals, polymers, or ceramics, in powdered form, used as the feedstock for 3D printing processes.
How do powder properties affect additive manufacturing?
Powder properties, such as particle size, density, flowability, and chemical composition, directly impact the resolution, strength, and overall quality of the printed objects.
What are the challenges in additive manufacturing powders?
Some challenges include powder reuse and recycling, material compatibility, powder degradation, and balancing cost and availability of specialized powders.
What is the future of additive manufacturing powders?
The future trends include advancements in powder atomization, development of new materials and composites, integration of smart materials, improved powder recycling and sustainability measures, and ongoing research in powder characterization and quality control.