Imagine a world where complex metal objects materialize from a digital blueprint, layer by layer. This isn’t science fiction; it’s the reality of 3D printing with metal powders, a revolutionary technology transforming manufacturing. But before we delve into the world of these metallic marvels, let’s rewind and explore the unsung hero of this story: the 3D printer itself.
What is a 3D Printer?
Think of a 3D printer as a high-tech sculptor, meticulously building objects from a digital model. Unlike traditional subtractive manufacturing (think carving wood), 3D printing employs an additive approach. It works like a fancy inkjet printer, but instead of ink, it deposits layers of material – plastic, resin, or in our case, metal powder – to create a three-dimensional object.
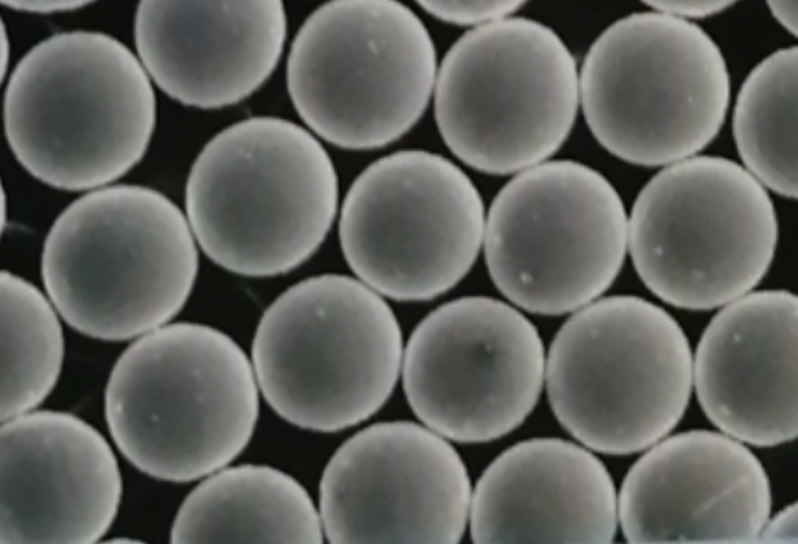
The Working Principle of 3D Printers:
Here’s a simplified breakdown of how a 3D printer brings your design to life:
- Digital Design: The journey begins with a 3D model created using computer-aided design (CAD) software. This software essentially acts as your blueprint, defining the object’s geometry and dimensions.
- Slicing the Model: Imagine slicing a loaf of bread – that’s what slicing software does to your 3D model. It digitally dissects the model into numerous thin layers, providing instructions for the printer.
- Printing Process: The 3D printer, based on the sliced model, lays down a thin layer of material (metal powder in our case) on a platform. A heat source, like a laser or electron beam, selectively melts or fuses the powder particles together, adhering them to the previous layer. This process repeats for each layer, gradually building the object from the bottom up.
- Post-Processing: Once printing is complete, the object may require additional steps like support removal (structures used during printing) and finishing touches for a professional look.
Types of 3D Printers:
Just like artists have different paintbrushes, 3D printers come in various forms, each with its own strengths and applications:
- Fused Deposition Modeling (FDM): The most common type, FDM printers typically use plastic filament. While not suitable for metal powders, FDM offers affordability and versatility for hobbyists and rapid prototyping.
- Stereolithography (SLA): SLA printers use a vat of liquid resin that solidifies layer-by-layer when exposed to a laser beam. They offer high precision and smooth finishes, ideal for creating detailed prototypes.
- Selective Laser Melting (SLM): This is where metal powders come into play! SLM printers use a high-powered laser to melt metal powder particles, creating strong and complex metal objects.
- Electron Beam Melting (EBM): Similar to SLM, EBM printers utilize an electron beam for melting. They excel at processing reactive metals like titanium, offering superior mechanical properties for demanding applications.

The Advantages of 3D Printing with Metal Powders:
Metal 3D printing unlocks a treasure trove of benefits for manufacturers:
- Design Freedom: Unleash your creativity! Unlike traditional methods limited by subtractive processes, 3D printing allows for intricate geometries, internal channels, and lightweight structures previously impossible to achieve.
- Rapid Prototyping: Gone are the days of lengthy and expensive prototyping cycles. 3D printing lets you produce functional metal prototypes quickly, accelerating your product development process.
- Reduced Waste: Traditional manufacturing often generates significant scrap metal. 3D printing uses only the necessary powder, minimizing waste and promoting sustainability.
- Lightweighting: 3D printing empowers you to create complex, hollow structures, resulting in lighter weight metal parts ideal for aerospace and automotive applications.
- Mass Customization: Imagine producing small batches of customized metal parts efficiently. 3D printing makes it possible, catering to niche markets and individual requirements.
Applications of 3D Printed Metal Parts:
Metal 3D printing is rapidly transforming various industries:
- Aerospace: Lighter, stronger components for aircraft and spacecraft are being created, pushing the boundaries of efficiency and performance.
- Automotive: Customized engine parts, lightweight chassis components, and intricate heat exchangers are paving the way for next-generation vehicles.
- Medical: Personalized implants, complex surgical tools, and even biocompatible prosthetics are being 3D printed, revolutionizing healthcare.
- Consumer Goods: From customized bike frames to intricate jewelry designs, 3D printing is making its mark on the consumer landscape.
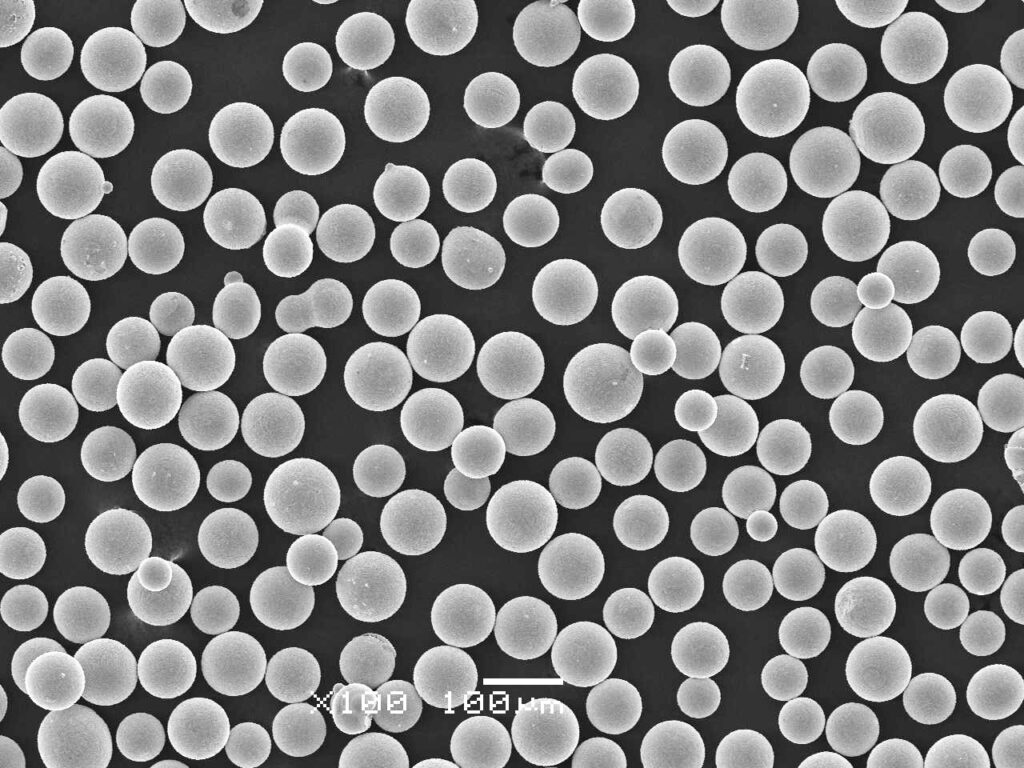
Challenges of 3D Printing with Metal Powders:
While the future of metal 3D printing is bright, there are challenges to overcome:
- Cost: Compared to traditional methods, metal 3D printing can be expensive. The printers themselves represent a significant investment, and metal powders are often priced higher than their plastic counterparts. Additionally, factors like post-processing and material handling contribute to the overall cost.
- Machine Complexity: Metal 3D printers are sophisticated machines requiring skilled operators with a deep understanding of the printing process, material properties, and machine calibration. This can pose a hurdle for smaller companies or those new to the technology.
- Surface Finish: While some metal 3D printing techniques produce near-net shapes (requiring minimal post-processing), others may yield parts with a rougher surface texture. Additional machining or finishing steps might be necessary to achieve a desired aesthetic or functional requirement.
- Material Properties: The properties of 3D printed metals can vary slightly compared to traditionally manufactured counterparts. Factors like porosity (tiny air pockets) and grain structure can influence the strength and fatigue resistance of the final product. Extensive testing and material selection are crucial for critical applications.
- Safety Considerations: Metal 3D printing processes can involve high temperatures, dust particles, and potentially hazardous materials. Implementing proper safety protocols, ventilation systems, and personal protective equipment is essential to ensure a safe working environment.
the Potential of Metal 3D Printing
Despite the challenges, the future of metal 3D printing is brimming with possibilities. Here are some exciting trends to watch:
- Advancements in Metal Powders: The development of finer and more uniform metal powders will lead to enhanced surface finishes, improved mechanical properties, and the ability to print a wider range of metals.
- Reduced Printing Costs: As technology matures and adoption increases, the cost of metal 3D printers and metal powders is expected to decrease, making this technology more accessible to a broader range of manufacturers.
- Hybrid Manufacturing: A growing trend involves combining 3D printing with traditional manufacturing techniques. For instance, 3D printing complex components that are then integrated into a larger assembly traditionally manufactured.
- Multi-Material Printing: The ability to print objects with different metals or a combination of metal and other materials within the same build is on the horizon, opening doors for innovative functional designs.
- Sustainability: Metal 3D printing’s inherent advantages, like reduced waste and lightweighting capabilities, contribute to a more sustainable manufacturing landscape. As concerns about environmental impact grow, this technology is poised to play a key role.
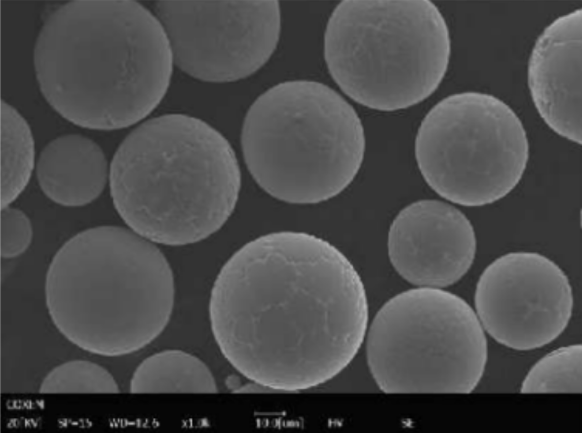
FAQ
Here’s a breakdown of some frequently asked questions regarding metal 3D printing with powders:
Question | Answer |
---|---|
What are some of the common metals used in 3D printing? | Stainless steel, titanium, aluminum, Inconel (a nickel-chromium superalloy), and precious metals like gold and silver are commonly used. |
How strong are 3D printed metal parts? | The strength of 3D printed metal parts depends on the specific metal used, the printing process, and post-processing techniques. However, they can be as strong or even stronger than traditionally manufactured counterparts. |
What are the limitations of 3D printed metal parts? | Current limitations include size restrictions (build volume of the printer) and potential challenges in achieving specific surface finishes for all applications. |
Is 3D printing with metal powders suitable for mass production? | While not yet widely used for mass production due to cost factors, metal 3D printing is ideal for creating low-volume, high-value, and complex metal parts. As technology advances, its role in mass production might expand. |
How can I learn more about metal 3D printing? | Numerous resources are available online and through industry publications. Additionally, attending industry events and conferences can provide valuable insights and networking opportunities. |
In Conclusion:
Metal 3D printing with powders represents a transformative technology with the potential to revolutionize how we design, prototype, and manufacture complex metal objects. While challenges exist, ongoing advancements in materials, processes, and affordability are paving the way for a future where metal 3D printing becomes a mainstream manufacturing tool across diverse industries. As this technology continues to evolve, one thing is certain: the possibilities for creating innovative and functional metal parts are truly limitless.
know more 3D printing processes
Additional FAQs on 3D Printers for Metal Powders
1) What’s the difference between SLM/DMLS and EBM 3D printers?
Both are powder bed fusion. SLM/DMLS uses a laser in an inert argon atmosphere; great for fine features and many alloys. EBM uses an electron beam in vacuum, with preheating that reduces residual stress; ideal for reactive metals (e.g., titanium) and thicker sections.
2) Which 3D printer should I choose for copper or highly reflective alloys?
Use systems with higher laser power, green/blue lasers, or specialized scan strategies. Some vendors offer copper-optimized LPBF or use binder jetting followed by sinter/HIP to handle pure copper and high-conductivity bronzes.
3) How do I estimate the true cost per metal printed part?
Include powder cost and reuse losses, machine hourly rate, gas/vacuum, energy, build time, supports, post-processing (HIP, heat treat, machining, surface finishing), inspection (CT/CMM), and scrap risk. Cost per part = total build cost ÷ yield of acceptable parts.
4) What tolerances and surface finishes are typical from a 3D printer using metal powders?
As-built LPBF tolerances often ±0.1–0.3 mm plus ±0.1% of length; Ra ~6–20 μm. With machining/electropolishing/shot peen, Ra <0.8 μm and tighter tolerances are routine for critical fits.
5) How does powder reuse affect print quality and safety?
Each cycle can change PSD, increase oxygen/nitrogen pickup, and add spatter/satellites, impacting flowability and porosity. Implement material passports, blend-back limits (e.g., ≤30–50% recycled), sieving, O/N/H testing, and strong housekeeping to control dust and ignition hazards.
2025 Industry Trends in Metal 3D Printers
- Multi-laser productivity: 8–12 laser LPBF systems and smarter tiling reduce build times 20–40% for Ti-6Al-4V and Inconel parts.
- In-situ QA: On-axis melt pool monitoring + coaxial cameras integrated with part acceptance criteria, cutting CT inspection burden for certain geometries.
- Copper-ready platforms: Blue/green lasers enable reliable pure copper printing for motor windings and heat exchangers.
- Binder jetting maturity: Sinter/HIP playbooks deliver 95–99% density in steels, Inconel, and copper, enabling larger parts at lower cost.
- Sustainability: Closed-loop powder handling, argon recirculation, and material passports with full genealogy adopted in regulated sectors.
2025 Metric (Metal 3D Printers) | Typical Range/Value | Relevance/Notes | Source |
---|---|---|---|
LPBF build rate (12‑laser Ti-64) | 40–80 cm³/h per system | Depends on layer thickness and strategy | OEM application notes |
As-built density (LPBF, post-HIP) | 99.5–99.9% | Aerospace/medical qualification | Peer-reviewed AM studies |
Binder jetted density (sinter/HIP) | 95–99% | Large, cost-sensitive parts | Vendor case data |
Copper LPBF conductivity | 70–90% IACS | With green/blue lasers and HIP | Materials datasheets |
Typical PSD for LPBF metals | D10–D90 ≈ 15–45 μm | Flow/recoat stability | ISO/ASTM 52907 |
Indicative machine uptime | 75–90% | With proactive maintenance/MES | Industry benchmarks |
Authoritative references and further reading:
- ISO/ASTM 52900 series (AM fundamentals and feedstock): https://www.astm.org and https://www.iso.org
- NIST AM Bench and data sets: https://www.nist.gov
- ASM Handbook: https://www.asminternational.org
Latest Research Cases
Case Study 1: Multi-Laser LPBF Titanium Brackets with In‑Situ Monitoring (2025)
Background: An airframe OEM needed to scale production of lattice-reinforced Ti-6Al-4V brackets while reducing inspection cost.
Solution: Deployed a 12‑laser LPBF printer with melt pool monitoring and automated anomaly tagging; HIP and targeted machining for interfaces.
Results: 28% cycle time reduction, 15% cost-per-part reduction, and a 40% reduction in CT usage after correlating in‑situ data with mechanical acceptance criteria.
Case Study 2: Binder-Jetted Copper Heat Exchanger for Power Electronics (2024)
Background: An inverter manufacturer sought complex internal channels with high conductivity at lower cost than LPBF.
Solution: Binder jetting pure copper, followed by hydrogen sintering and HIP; added Ni plating on sealing surfaces.
Results: 97–98% density, 82% IACS conductivity, 22% lower thermal resistance vs. machined copper assembly, and 35% lead-time reduction.
Expert Opinions
- Prof. John Hart, Professor of Mechanical Engineering, MIT
Key viewpoint: “The combination of in‑situ sensing and digital material passports is unlocking statistically defensible qualification pathways for production 3D printing.” - Dr. Laura Schmidt, Head of Additive Manufacturing, Fraunhofer IAPT
Key viewpoint: “Process windows for copper and nickel superalloys have widened thanks to wavelength-optimized lasers and advanced scan strategies, pushing AM into motors and turbomachinery.” - Dr. Brent Stucker, AM Industry Executive and Standards Contributor
Key viewpoint: “Hybrid workflows—AM preforms followed by forging/HIP—are delivering wrought-like properties while preserving design freedom where it matters.”
Citations for expert profiles:
- MIT: https://meche.mit.edu
- Fraunhofer IAPT: https://www.iapt.fraunhofer.de
- ASTM AM Center of Excellence: https://amcoe.org
Practical Tools and Resources
- Standards and safety
- ISO/ASTM 52907 (feedstock), 52910 (DFAM), 52931 (LB-PBF of metals): https://www.astm.org
- NFPA 484 (combustible metals safety): https://www.nfpa.org
- Design and simulation
- Ansys Additive/Mechanical; Siemens NX AM; Autodesk Netfabb: vendor sites
- nTopology for lattices and heat exchanger topology optimization: https://ntop.com
- Process control and QA
- In‑situ monitoring platforms (OEM-integrated), CT scanning best practices (ASTM E1441)
- LECO O/N/H analysis for powder reuse governance: https://www.leco.com
- Market and learning
- Wohlers Report and AM industry analyses
- NIST AM Bench, NASA MSFC AM guidelines: https://www.nasa.gov
Last updated: 2025-08-21
Changelog: Added 5 targeted FAQs, a 2025 trend table with metrics and sources, two recent 3D printer case studies, expert viewpoints with credible affiliations, and curated tools/resources.
Next review date & triggers: 2026-02-01 or earlier if ISO/ASTM standards are revised, major OEMs release new copper-capable platforms, or validated in‑situ monitoring replaces CT for additional part classes.