Introduction
In recent years, additive manufacturing, also known as 3D printing, has revolutionized various industries with its ability to create complex and customized components. One critical aspect of this technology is the powders used as raw materials. Among these, 316L powder stands out as a versatile and high-performance material, enabling the production of robust and functional parts. In this article, we will explore the world of 316L powder, its properties, applications, production process, and more.
What is 316L Powder?
316L powder is a fine, granulated form of stainless steel, primarily composed of chromium, nickel, and molybdenum, along with small amounts of other elements. The “L” in its name indicates that it has low carbon content, making it resistant to sensitization – a process that causes intergranular corrosion in some environments. The unique combination of elements provides 316L powder with remarkable properties, making it a preferred choice for various applications.
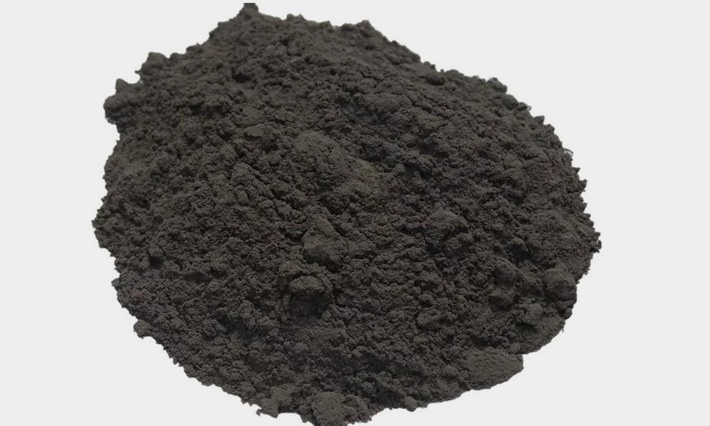
Properties of 316L Powder
Corrosion Resistance
One of the most outstanding attributes of 316L powder is its exceptional corrosion resistance. The high chromium content forms a protective oxide layer on the surface, preventing rust and corrosion in aggressive environments. This property makes it ideal for applications in marine, chemical, and food processing industries.
High Temperature Strength
316L powder exhibits significant strength and stability at elevated temperatures. This property is particularly crucial in industries where components may experience varying degrees of heat stress, such as aerospace and automotive applications.
Weldability
Weldability is a critical factor in manufacturing processes, and 316L powder excels in this regard. It can be easily welded without the risk of intergranular corrosion, making it suitable for joining various components.
Biocompatibility
The biocompatibility of 316L powder makes it highly suitable for medical applications. It is commonly used in the production of surgical implants, medical devices, and orthopedic instruments, as it does not cause adverse reactions when in contact with body tissues.
Applications of 316L Powder
Aerospace Industry
The aerospace industry demands materials that can withstand extreme conditions while maintaining structural integrity. 316L powder’s high temperature strength and corrosion resistance make it a preferred choice for aerospace components.
Medical Devices
In the medical field, 316L powder finds extensive use in producing implants and medical instruments. Its biocompatibility and corrosion resistance make it safe and reliable for use in the human body.
Additive Manufacturing
As a critical component in the additive manufacturing process, 316L powder is used to create intricate and custom-designed parts for various industries.
Chemical Processing
The chemical processing industry relies on materials that can resist corrosion and maintain purity. 316L powder’s exceptional chemical resistance makes it an ideal choice for this sector.
Advantages of Using 316L Powder
Design Flexibility
Additive manufacturing allows for unparalleled design flexibility, and 316L powder complements this by enabling the creation of complex geometries that traditional manufacturing processes cannot achieve.
Cost-Effectiveness
Although the initial cost of 316L powder may be higher, additive manufacturing reduces material wastage and overall production costs, making it a cost-effective option for specific applications.
Reduced Waste
Traditional manufacturing methods often generate significant material waste. In contrast, additive manufacturing using 316L powder produces minimal scrap, contributing to a more sustainable and environmentally friendly approach.
Customization
316L powder enables the production of highly customized components, catering to the specific needs of industries and consumers alike.
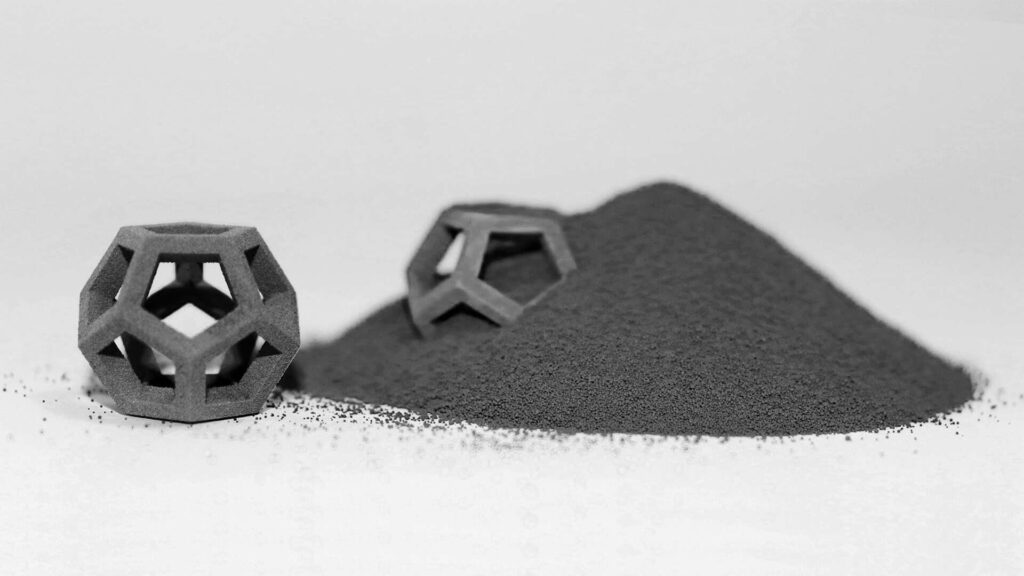
How is 316L Powder Produced?
Atomization Process
The production of 316L powder involves an atomization process, where molten metal is converted into fine droplets. These droplets solidify rapidly, forming the powder particles.
Post-Processing Steps
After atomization, the powder undergoes various post-processing steps, such as sieving, to achieve the desired particle size distribution and eliminate any irregularities.
Factors Affecting the Quality of 316L Powder
Powder Size Distribution
The particle size distribution of 316L powder plays a crucial role in determining the material’s flowability and packing characteristics during the additive manufacturing process.
Oxygen Content
Excessive oxygen content in the powder can lead to defects in the final product. Proper handling and storage are essential to maintaining low oxygen levels.
Flowability
Good flowability ensures smooth and consistent powder dispensing during the printing process, contributing to better part quality.
Sphericity
The shape of the powder particles, or sphericity, affects packing density and flow behavior, influencing the final mechanical properties of the 316L components.
Handling and Safety Precautions
Proper Storage
Storing 316L powder in a controlled environment, away from moisture and contaminants, is crucial to preserve its properties and prevent oxidation.
Handling Procedures
Operators must follow specific handling procedures to minimize the risk of particle dispersion, inhalation, or contact with skin.
Personal Protective Equipment (PPE)
Wearing appropriate personal protective equipment, such as masks and gloves, is vital to ensure the safety of workers handling 316L powder.
Future Trends and Innovations
The field of additive manufacturing continues to evolve rapidly, and ongoing research aims to enhance the properties of 316L powder further. Innovations in powder production techniques, along with advancements in 3D printing technology, promise to unlock new possibilities in various industries.
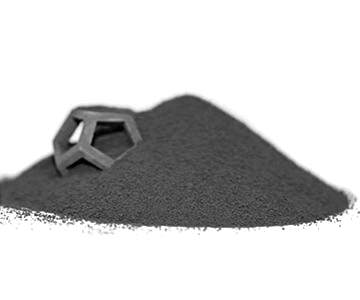
Conclusion
316L powder has emerged as a game-changer in the realm of additive manufacturing. Its exceptional properties, including corrosion resistance, high temperature strength, weldability, and biocompatibility, make it a versatile and sought-after material for a wide range of applications.
In aerospace, 316L powder is utilized to produce critical components that can withstand extreme temperatures and harsh environments. The material’s ability to maintain structural integrity under challenging conditions ensures the safety and reliability of aerospace equipment.
The medical industry benefits greatly from the biocompatibility of 316L powder. It is used in the manufacturing of surgical implants, prosthetics, and medical instruments. Its compatibility with the human body reduces the risk of adverse reactions and promotes successful medical interventions.
FAQs
- Is 316L powder the same as regular stainless steel? No, 316L powder is a granulated form of stainless steel, specifically engineered for additive manufacturing processes, such as 3D printing.
- What are the advantages of using 316L powder in aerospace applications? 316L powder’s high temperature strength and corrosion resistance make it ideal for withstanding the demanding conditions experienced in the aerospace industry.
- Is 316L powder safe for medical use? Yes, 316L powder is biocompatible and extensively used in medical devices and implants due to its non-reactive nature with body tissues.
- How does 316L powder contribute to sustainability? Additive manufacturing using 316L powder generates minimal waste, reducing the environmental impact and promoting a more sustainable manufacturing approach.
- What safety precautions should be followed when handling 316L powder? Workers should wear appropriate personal protective equipment (PPE) and follow specific handling procedures to minimize the risk of exposure to the powder. Proper storage is also crucial to maintain its properties.