Introduction to EBM Technology
In the fast-paced world of manufacturing and engineering, technological advancements are revolutionizing the way products are made. One such groundbreaking technology is Electron Beam Melting (EBM). This article delves into the world of EBM technology, exploring its principles, applications, advantages, challenges, and its impact on various industries. We will also discuss the future prospects of EBM and its role in shaping a sustainable future.
What is EBM Technology?
EBM, short for Electron Beam Melting, is a cutting-edge additive manufacturing technology that enables the creation of complex three-dimensional objects. Unlike traditional manufacturing methods, EBM utilizes an electron beam to selectively melt and fuse metal powders, layer by layer, to build a final product. This process is often referred to as powder bed fusion, making it an integral part of the additive manufacturing family.
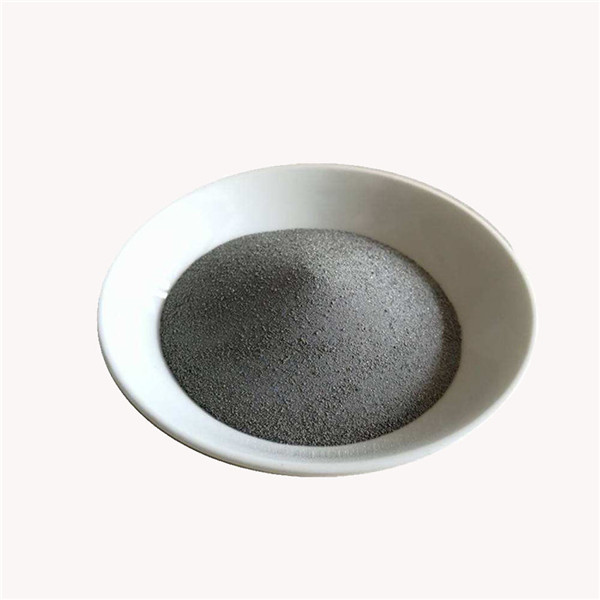
Understanding the Principles of EBM
To grasp the essence of EBM technology, it is essential to understand its fundamental principles. At its core, EBM relies on the use of high-energy electron beams that are emitted from an electron gun. These beams are precisely directed onto a thin layer of metal powder, causing the powder particles to rapidly melt and fuse together. By repeatedly scanning and adding more layers, the object gradually takes shape with exceptional accuracy.
Energy Source: Electron Gun
The electron gun serves as the primary energy source in EBM technology. It emits a focused stream of high-energy electrons, which are responsible for melting the metal powder.
Powder Bed
The metal powder used in EBM serves as the raw material for building the object. The powder bed provides a layer upon which the electron beam operates.
Selective Melting
EBM involves selective melting, where the electron beam targets specific areas on the powder bed to create the desired shape, leaving other areas untouched.
Layer-by-Layer Approach
The layer-by-layer approach is a fundamental aspect of EBM, where each successive layer is added on top of the previous one until the object is complete.
The History of EBM Technology
The roots of EBM can be traced back to the 1980s when it was first conceptualized and developed. The technology was primarily pioneered by a Swedish company called Arcam AB. Over the years, EBM has undergone significant refinements and improvements, leading to its adoption in diverse industrial applications.
Early Developments
The initial stages of EBM technology were marked by experiments with various electron beam sources and metal powders to achieve optimal results.
Arcam AB’s Contribution
Arcam AB, founded in 1997, played a pivotal role in the advancement of EBM technology. Their continuous research and development efforts contributed to making EBM a commercially viable manufacturing method.
How EBM Technology Works
To comprehend the intricacies of EBM, it’s crucial to grasp the step-by-step process of how this innovative technology works.
Digital Design
The first step in EBM involves creating a digital design of the object to be manufactured. This design serves as the blueprint for the entire manufacturing process.
Preparing the Powder Bed
The metal powder, chosen based on the material requirements, is spread evenly on the build platform, creating the first layer.
Electron Beam Melting
The electron gun emits high-energy beams, selectively melting the metal powder according to the digital design.
Adding Layers
After each layer is melted and solidified, the build platform moves down, and a new layer of metal powder is spread on top. The process is repeated until the entire object is fabricated.
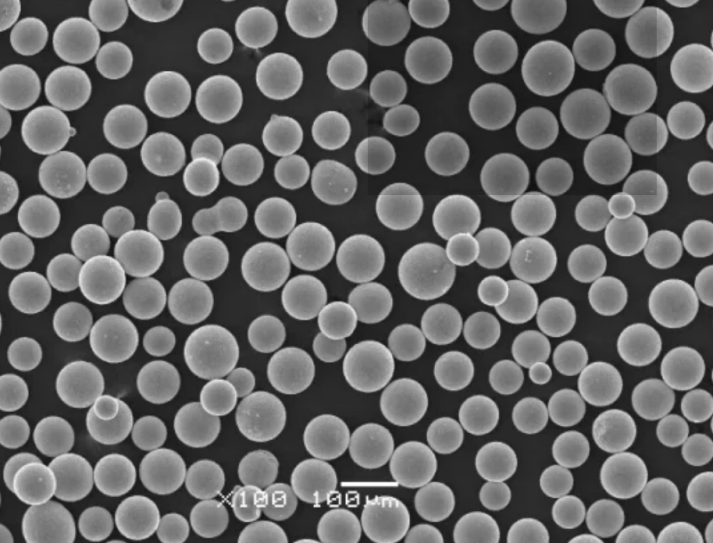
Applications of EBM in Various Industries
EBM’s capabilities have opened up new avenues in various industries. Let’s explore some of the key applications of EBM technology.
Applications of EBM in Various Industries (contd.)
Aerospace and Aviation
The aerospace and aviation industries have been early adopters of EBM technology. EBM allows for the creation of complex, lightweight, and high-strength components for aircraft and spacecraft. This has led to improved fuel efficiency, reduced emissions, and enhanced performance.
Healthcare and Medical Devices
In the medical field, EBM has revolutionized the production of customized implants and prosthetics. Its ability to create intricate and patient-specific designs ensures better compatibility and functionality, leading to improved patient outcomes.
Automotive Industry
In the automotive sector, EBM is used to manufacture lightweight and durable components, such as engine parts, gears, and brackets. This aids in increasing vehicle efficiency, reducing emissions, and enhancing overall performance.
Tooling and Prototyping
EBM is increasingly utilized in tooling and prototyping processes. It enables rapid and cost-effective production of molds, patterns, and prototypes, saving time and resources in the product development cycle.
Advantages and Benefits of EBM Technology
EBM technology offers several advantages over traditional manufacturing methods, making it an attractive choice for various industries.
Design Freedom
EBM enables the fabrication of complex geometries that would be challenging or impossible to achieve through conventional techniques. This design freedom opens up possibilities for innovation and optimization in product development.
Material Efficiency
EBM is known for its excellent material utilization, reducing waste and minimizing overall material costs. The layer-by-layer approach ensures that only the required amount of material is used to build the object.
Reduced Lead Times
The additive nature of EBM technology allows for quicker production cycles compared to subtractive methods. This reduced lead time accelerates product development and time-to-market.
Improved Performance
Components manufactured using EBM often exhibit superior mechanical properties, such as strength and fatigue resistance, leading to enhanced product performance and durability.
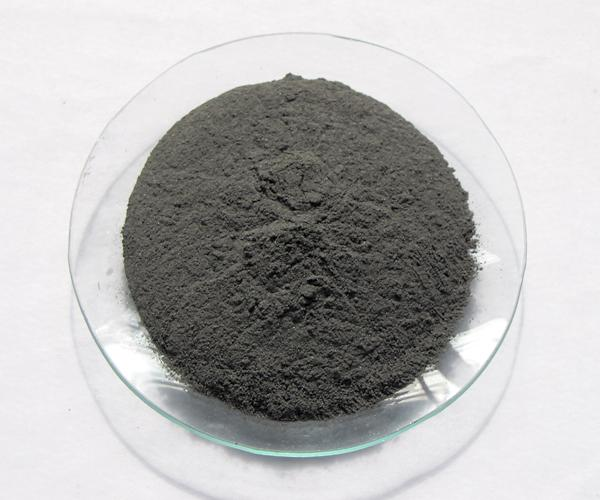
Challenges and Limitations of EBM
While EBM technology has significant potential, it also faces certain challenges and limitations that must be addressed.
Surface Finish and Post-Processing
The surface finish of EBM-produced parts may not always meet the required standards, necessitating post-processing steps, which can add time and cost to the production process.
Material Selection and Availability
The range of materials compatible with EBM is still relatively limited compared to traditional manufacturing methods. Expanding material options is essential to cater to diverse industry needs.
Machine Size and Cost
EBM machines, especially for large-scale production, can be costly to acquire and maintain. Smaller manufacturers may find it challenging to invest in EBM technology.
Process Optimization
Optimizing the EBM process to achieve consistent results across different materials and applications requires ongoing research and development.
The Future of EBM Technology
The future of EBM technology holds great promise, with ongoing research and innovation poised to overcome current limitations and unlock new possibilities.
Material Advancements
Research into new materials and alloys compatible with EBM is expected to expand the application range of this technology across industries.
Integration with Industry 4.0
As part of the Industry 4.0 revolution, EBM technology is likely to integrate with smart manufacturing systems, enabling more automated and interconnected production processes.
Multi-Material Printing
Advancements in EBM technology may lead to the ability to print objects using multiple materials in a single build, further enhancing design flexibility and performance.
Increased Accessibility
As EBM technology matures and becomes more prevalent, the costs associated with machines and materials are likely to decrease, making it more accessible to a broader range of manufacturers.
EBM Technology in Healthcare and Medicine
The medical field is witnessing significant transformations due to EBM technology. Let’s explore its impact in healthcare and medicine.
EBM Technology in Healthcare and Medicine (contd.)
Customized Implants and Prosthetics
One of the most significant contributions of EBM technology to healthcare is the production of customized implants and prosthetics. EBM allows for the creation of patient-specific designs, ensuring a perfect fit and reducing the risk of complications after implantation.
Dental Applications
EBM has found applications in the dental industry, where it is used to fabricate dental crowns, bridges, and orthodontic devices. The precise nature of EBM ensures that dental prosthetics match the patient’s unique dental anatomy accurately.
Medical Instrumentation
EBM technology enables the production of specialized medical instruments, such as surgical tools and guides. These instruments can be designed to be lightweight, ergonomic, and tailored to specific medical procedures.
Tissue Engineering
Researchers are exploring the use of EBM to print living tissues and scaffolds for tissue engineering applications. This breakthrough could revolutionize regenerative medicine and organ transplantation.
EBM in Aerospace and Automotive Industries
Lightweight Components for Aerospace
Aerospace engineers leverage EBM to fabricate lightweight and complex components for aircraft and spacecraft. This not only reduces the overall weight of the vehicles but also contributes to fuel efficiency and improved performance.
Engine Components for Automotive
In the automotive industry, EBM is utilized to manufacture critical engine components with intricate internal structures, leading to better engine performance and reduced fuel consumption.
Spare Parts Production
EBM has the potential to revolutionize spare parts production for both aerospace and automotive industries. By printing spare parts on-demand, manufacturers can significantly reduce inventory costs and ensure rapid maintenance and repairs.
EBM and Sustainability
Resource Efficiency
EBM’s material efficiency translates into reduced material waste, making it an environmentally friendly manufacturing process compared to traditional methods.
Energy Savings
The additive nature of EBM consumes less energy than traditional subtractive manufacturing techniques, contributing to overall energy savings.
Sustainable Design
EBM enables the creation of sustainable designs with optimized geometries, leading to lighter products that require less energy to operate.
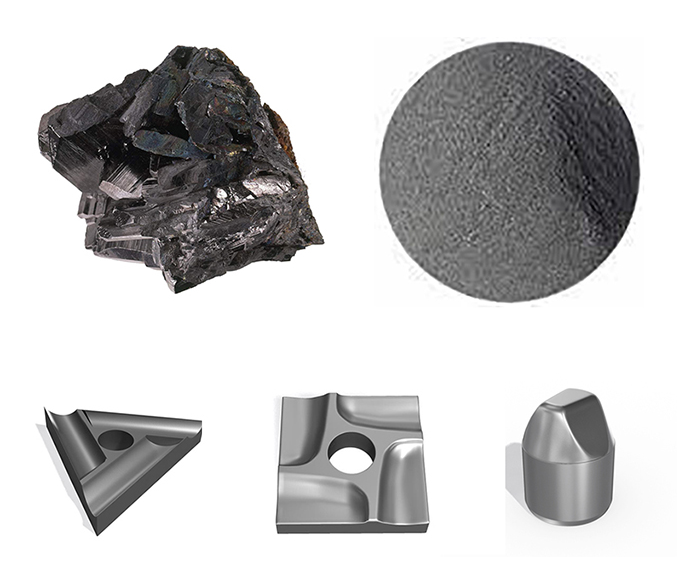
EBM vs. Traditional Manufacturing Methods
Additive vs. Subtractive Manufacturing
Comparing EBM to traditional subtractive manufacturing methods, we explore the key differences and advantages offered by the additive approach.
Complexity and Design Freedom
EBM allows for the production of highly complex geometries that would be challenging or impossible to achieve with subtractive methods.
Material Waste and Efficiency
Traditional manufacturing often generates significant material waste, while EBM minimizes waste by using only the necessary amount of material.
Cost and Time Savings
EBM can lead to cost and time savings in production, particularly for customized and low-volume manufacturing.
Innovations and Research in EBM
Material Innovation
Researchers are continually exploring new materials and alloys to expand the material options available for EBM technology.
EBM at the Nanoscale
Advancements in EBM are pushing the boundaries of resolution, allowing for nanoscale 3D printing, opening new possibilities in microelectronics and biomedicine.
In-Process Monitoring
Researchers are developing in-process monitoring techniques to ensure the quality and reliability of EBM-produced parts.
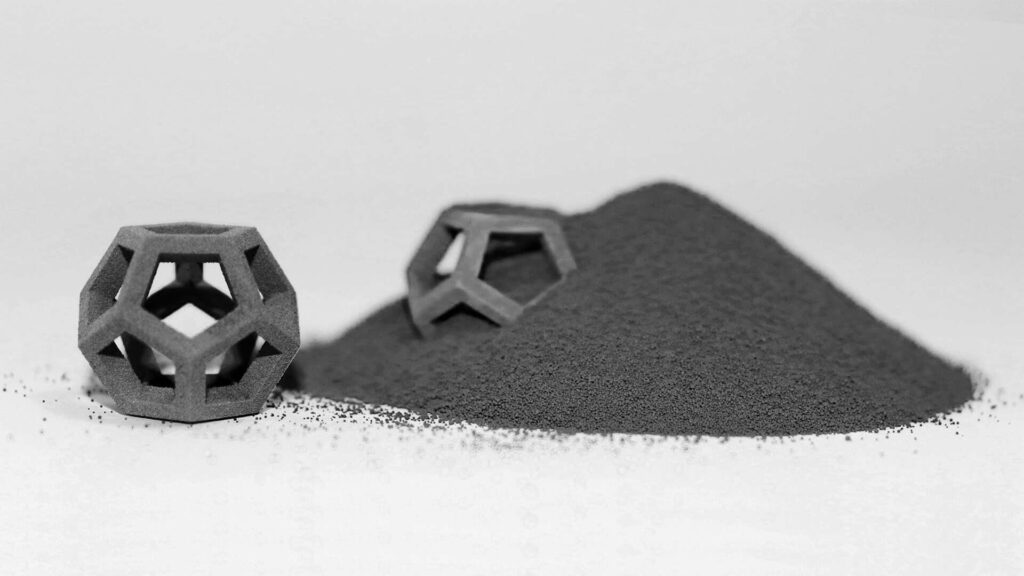
Conclusion
EBM technology has emerged as a revolutionary force in modern manufacturing. Its ability to create complex, lightweight, and customized objects has transformed industries like aerospace, healthcare, and automotive. While EBM faces challenges and limitations, ongoing research and innovations are expected to address these issues, propelling EBM towards a more sustainable and interconnected future.
FAQs
Is EBM technology limited to specific materials?EBM currently works best with certain metals, such as titanium, stainless steel, and nickel-based alloys. However, ongoing research aims to expand the range of compatible materials.
How does EBM benefit the aerospace industry?EBM allows aerospace manufacturers to create lightweight and intricate components, leading to increased fuel efficiency and improved performance of aircraft and spacecraft.
Can EBM be used for mass production?While EBM is excellent for low-volume and customized production, it is currently not as suitable for mass production due to its slower printing speed.
What is the potential impact of EBM on the medical field?EBM has the potential to revolutionize healthcare by enabling the production of patient-specific implants and prosthetics, as well as facilitating advances in tissue engineering and regenerative medicine.
How does EBM contribute to sustainability?EBM’s material efficiency, reduced energy consumption, and ability to create lightweight designs contribute to a more sustainable and eco-friendly manufacturing process compared to traditional methods.