Introduction
In the realm of powder metallurgy, gas atomization is a fundamental process that plays a pivotal role in producing high-quality metal powders. The process involves converting molten metal into fine, spherical particles by subjecting it to a high-velocity stream of gas. These atomized powders find widespread applications across various industries, including aerospace, automotive, healthcare, and electronics, owing to their superior characteristics and performance.
In this article, we delve into the intricacies of the gas atomization process in powder metallurgy, its advantages, applications, challenges, and its potential future prospects.
What is gas atomization process in powder metallurgy?
Gas atomization is a powder production technique employed in powder metallurgy to fabricate metal powders with specific properties and characteristics. Unlike traditional methods, such as water atomization, the gas atomization process generates powders with a highly spherical shape and narrow particle size distribution, leading to enhanced material properties.
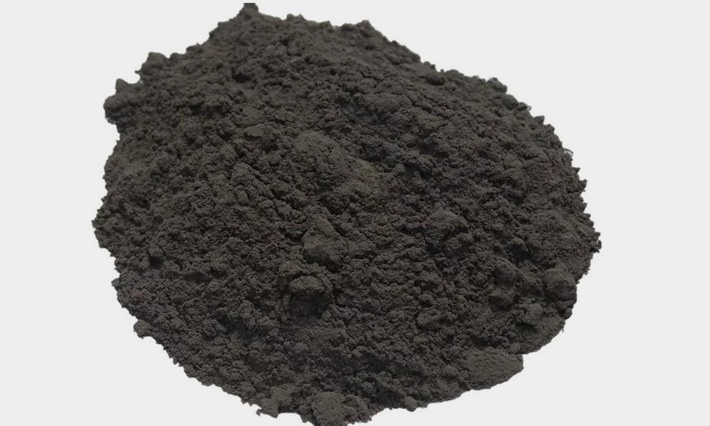
The Gas Atomization Process
Atomization Gas Selection
The choice of atomization gas is crucial to the process, as it affects the cooling rate, droplet size, and solidification behavior of the metal particles. Commonly used gases include nitrogen, argon, and helium. Each gas has distinct properties that influence the powder’s final characteristics.
Nozzle Design
The design of the atomization nozzle significantly impacts the powder’s morphology and uniformity. The nozzle must be carefully engineered to ensure efficient breakup of the molten metal stream into fine droplets.
Melting and Preparation of Alloy
The first step involves melting the metal alloy to the desired temperature. It is essential to achieve a homogenous melt to obtain consistent powder quality.
Atomization Chamber
The atomization chamber is where the magic happens. The molten metal is introduced into the chamber and exposed to the high-velocity atomization gas, leading to rapid solidification of the droplets.
Powder Collection and Classification
After atomization, the resulting powder particles are collected and separated based on their size and shape. This classification step is vital to ensure the powder meets specific requirements for various applications.
Post-Treatment
In some cases, post-treatment processes like heat treatment or surface modification are employed to further enhance the powder’s properties and tailor it for specialized applications.
Advantages of Gas Atomization
Superior Powder Characteristics
Gas atomization produces powders with excellent flowability and packing density, making them ideal for processes like powder compaction.
Enhanced Material Performance
The spherical shape of gas-atomized powders results in reduced porosity and improved mechanical properties in the final product.
Wider Alloy Range
Gas atomization enables the production of powders from a wide range of alloys, including reactive and refractory metals.
High Production Rate
The process allows for a high production rate of fine powders, making it commercially viable for various industries.
Reduced Contamination
As gas atomization occurs in a closed chamber, it reduces the risk of contamination and ensures a clean powder product.
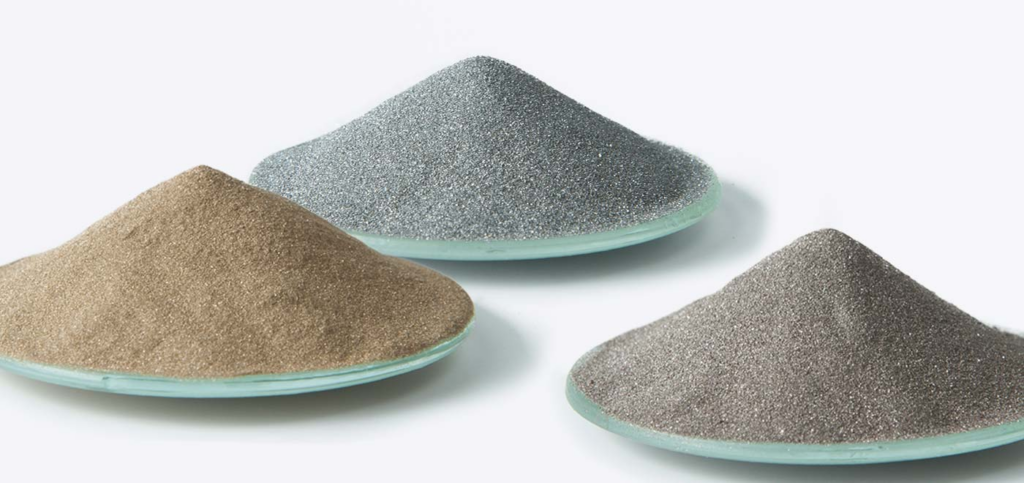
Applications of Gas Atomization Powders
Additive Manufacturing
Gas-atomized powders are extensively used in additive manufacturing processes like metal 3D printing due to their high purity and consistent characteristics.
Metal Injection Molding (MIM)
MIM relies on gas-atomized powders to produce complex-shaped metal components used in various industries.
Thermal Spray Coatings
The spherical nature of gas-atomized powders ensures uniform coating deposition in thermal spray applications.
Sintered Components
Powders produced through gas atomization are widely utilized in the production of sintered components, offering excellent mechanical properties.
Challenges in Gas Atomization Process
High Equipment Cost
Setting up a gas atomization facility can be capital-intensive, especially for smaller manufacturing units.
Oxidation of Powders
Certain metals are susceptible to oxidation during the atomization process, affecting powder quality.
Powder Agglomeration
Agglomeration of powder particles can occur during the collection process, leading to inconsistencies in particle size.
Particle Size Distribution Control
Achieving precise control over particle size distribution can be challenging and requires sophisticated equipment and process optimization.
Future of Gas Atomization in Powder Metallurgy
The gas atomization process continues to evolve, driven by ongoing research and technological advancements. As materials science and additive manufacturing techniques progress, the demand for gas-atomized powders is expected to soar, leading to further improvements in the process and its applications.
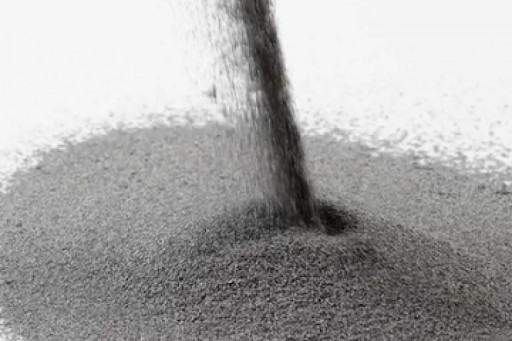
Conclusion
Gas atomization is a crucial process in powder metallurgy, enabling the production of high-quality metal powders with tailored properties. The superior characteristics of gas-atomized powders have found applications across diverse industries, from aerospace to healthcare. Despite challenges, the future holds promising developments in gas atomization techniques, solidifying its position as a vital player in the world of advanced materials and manufacturing.
FAQs
What is gas atomization in powder metallurgy? Gas atomization is a powder production technique used to create spherical metal particles with narrow size distributions, employed in powder metallurgy.
Which gases are commonly used in the gas atomization process? Commonly used gases include nitrogen, argon, and helium.
What are the advantages of gas-atomized powders? Gas-atomized powders offer superior flowability, enhanced material performance, wider alloy ranges, high production rates, and reduced contamination.
What are the applications of gas-atomized powders? Gas-atomized powders find applications in additive manufacturing, metal injection molding, thermal spray coatings, and the production of sintered components.
What are the challenges in the gas atomization process? Challenges include high equipment costs, oxidation of powders, powder agglomeration, and precise control over particle size distribution.