Plasma Rotating Electrode Atomizing, powder making equipment, prep, powder making system
Metal powders can be prepared by a variety of methods, such as mechanical (ball milling, grinding, etc.), physical (atomisation) and chemical (reduction, electrolysis, carbonyl and displacement methods, etc.). However, to meet the requirements of SEBM technology for spherical metal powders, atomisation is the main method used for the preparation of metal powders, specifically Water atomization, WA, Gas atomization, GA, Plasma atomization, PA and Plasma rotating electrode process, PREP. process, PREP, and sometimes Hydride-dehydride, HDH, in order to reduce the cost of powder preparation.
PREP Powder- making Technology
The plasma rotating electrode atomisation method uses the plasma arc as a heat source to continuously melt the end face of a high speed rotating metal bar, under the action of centrifugal force, the melted metal droplets fly out and are rapidly solidified under the cooling effect of inert gas (argon or helium) to form a spherical metal powder. Compared to water atomisation and gas atomisation, the plasma rotary electrode atomisation method has a lower cooling rate and produces powders with high sphericity, good fluidity, low oxygen content and very few hollow and satellite powders. The prepared powder is pure as contamination of the crucible is avoided. In addition, the powder prepared by this method has a narrow particle size distribution.
Status of Application
PREP powder technology was first developed by Nuclear Metals Corporation in the USA and reported in a patent in 1963, and in 1974, the plasma torch replaced the tungsten electrode arc as the heat source and the plasma rotary electrode atomisation (PREP) method was developed.
In 1974, the plasma torch replaced the tungsten electrode arc as the heat source and the plasma rotary electrode atomisation (PREP) method was born. In 1983, the Institute of Powder Metallurgy of the Northwest Institute of Non-ferrous Metals designed and developed the first PREP equipment in China, and subsequently, a number of Chinese companies and institutions also carried out research and development on this technology. The PREP method, as a centrifugal atomisation method, has the advantages of good sphericity, high vibrancy density, good flowability, low gas content and narrow particle size distribution compared to other methods. With more than 40 years of development, the plasma rotary electrode atomisation method has been rapidly developed in terms of equipment improvement, process control and powder quality, and has become an indispensable method for the preparation of spherical metal powders.
PREP equipment usually consists of a vacuum system, a gas system, a cooling system, a power supply system, a plasma generator, a feeding device, an atomisation chamber and a collection system.
feed device, atomisation chamber and collection system. The inert gas, usually argon, helium or a mixture of argon and helium, protects and cools the powder during the atomisation process and is the key to its quality. Russian powder production facilities usually set the helium to argon ratio at 4:1.
The plasma torch usually works in two modes, the transfer arc mode and the non-transfer arc mode, the Russian equipment mostly uses the non-transfer arc mode, i.e. the arc is generated between the electrode and the nozzle. Xi’an Sailong Metals uses the transfer arc mode of operation, which allows more heat to be transferred to the bar stock, increasing the melting rate of the bar stock end face and improving production efficiency.
In recent years, Xi’an Sailong Metals has developed the first vertical industrial grade SLPA-V PREP machine in the world. This machine has a vertical electrode bar placement structure, which reduces vibration during operation, increases the working speed and ensures stable production of high quality powder.
In addition, the SLPA-D tabletop plasma rotary electrode atomisation plant with a working speed of up to 60,000 rpm is suitable for the development and production of high quality spherical metal powders in small batches and in many varieties. The industrial-grade SLPA-H PREP machine has a new dynamic seal structure, which can provide power support for the high-speed rotation of large diameter electrode rods. The new high-torque, high speed electrode rotating drive and power supply system can be used for the development and production of Φ75 mm electrodes at 13,000 to 18,000 rpm.
The new high-torque, high speed rod rotation drive and power supply system enables the normal operation of the Φ75 mm rod at 13,000-18,000 r/min and stable power supply at high currents of 3000 A.
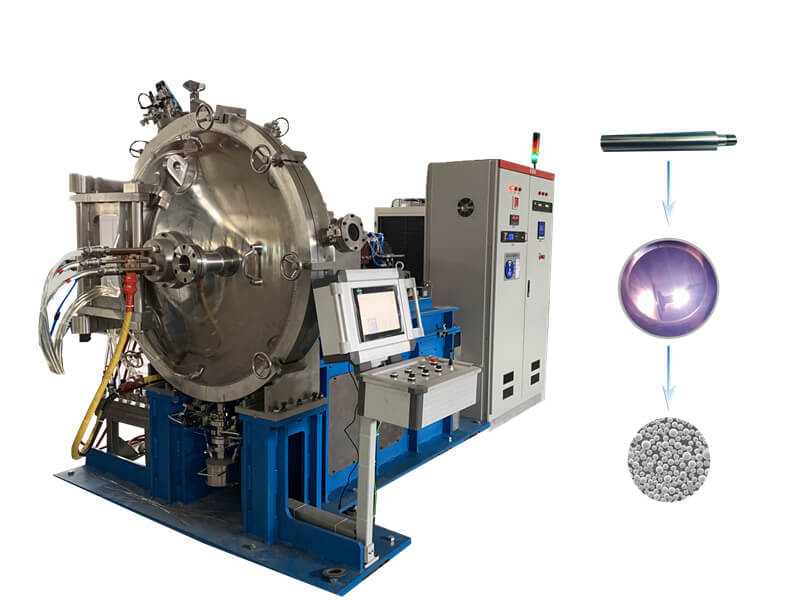
Particle Size of PREP Metal Powder
The particle size of the powder and its distribution is one of the most important concerns for subsequent applications and often affects the powder properties and ultimately the quality of the formed part, therefore the PREP process parameters should be reasonably determined so that the particle size distribution lies as much as possible within the required range.
In general, the main process parameters that influence the particle size distribution of the powder are the electrode bar material, the electrode bar rotation speed, the bar diameter, the plasma gun power, the feed rate, the distance between the plasma gun and the bar, the plasma gas flow, etc. In the PREP powder making process, droplets are thrown out when the centrifugal force is greater than the surface tension, therefore, increasing the electrode rod rotation speed or increasing the electrode rod diameter to increase the centrifugal force can make the powder particle size smaller. In addition, the melting rate at the end face of the bar should be as equal as possible to the feed rate. If the melting rate is greater than the feed rate, arc breakage will occur, if the feed rate is greater than the melting rate, poor melting will occur, forming flying edges and other problems. The distance between the plasma gun and the bar will affect the superheat of the powder and the plasma gas flow will have an effect on the cooling effect. It has been found that the average particle size of the powder is mainly related to the bar
The larger the bar speed or diameter, the finer the powder will be when the material is a certain size, while the particle size distribution is related to the bar speed, the current and the distance between the plasma gun and the end of the bar, etc. Increasing the speed, decreasing the current or the distance between the plasma gun and the end of the bar will narrow the particle size distribution curve.
When the materials are different, the average particle size and its distribution are often related to factors such as the density and surface tension of the material.
PREP Powder Making and Application
The development of PREP technology has made it possible to prepare an increasing number of new material powders. The types of powders involved are titanium alloys, 1018 steel, high nitrogen steel, Ni-Ti-Fe, Inconel 718, FGH95, Ti, TiNb, etc.
Most of the powders produced by Xi’an Sailong are titanium alloy powder, high temperature alloy powder and stainless steel powder.
So far, titanium alloy powder, cobalt-based high-temperature alloy powder, nickel-based high-temperature alloy powder, refractory metal powder (e.g. W, Mo Ta, Nb and their alloys), stainless steel powder and aluminium alloy powder and silver alloy powder, etc., and the powder has excellent performance and can be produced after The powders are widely used in aerospace, machinery and biomedical fields after being manufactured or hot isostatically pressed.