3D printing metal powders
Metal powders are the most important raw material for 3D printing of metal parts, and powder properties are one of the most important factors affecting the quality of metal 3D printing products. Powder materials with a diameter of less than 1 mm are generally considered suitable for 3D printing, but high-quality 3D printed metal products have higher requirements for the shape, particle size and purity of the powder. The main types of 3D printing equipment are powder spreading, coaxial powder feeding and lateral powder feeding, depending on the powder replenishment method. The lateral powder feeding 3D printing final part
The shape and dimensional accuracy of the final part is low, the laser energy cannot be fully utilised and the powder utilisation rate is low. Therefore, high-quality metal 3D printing equipment is mainly The two main methods of powder replenishment are powder spreading or coaxial powder feeding.
Unlike traditional metal material manufacturing technology with its huge equipment, long process, high energy consumption, pollution and low material utilisation, metal 3D printing has the following advantages: (1) high overall material utilisation; (2) no need to open moulds, few manufacturing processes and short cycle time; (3) can manufacture parts with complex structures; (4) free design according to mechanical property requirements, without considering manufacturing processes. In recent years, metal 3D printing has developed rapidly, with GKN Aerospace supplying France’s Airbus and Safran with 2.5 m diameter Ariane 6 rocket nozzles (SWAN), processing key structural components through laser welding and laser energy deposition processes, reducing the number of nozzle components from
approximately 1,000 to approximately 100 parts, reducing costs by 40% and delivery times by 30%. Metal 3D printing is mainly used to provide rapid production of models for industrial design and the machining of complex moulds, as well as the production of small batches, complex structures, high performance and large metal components. Metal 3D printing uses metal powder as an additive material and uses rapid forming methods such as selective laser melting (SLM), electron beam selective melting (EBSM) or laser near net forming (LENS) to rapidly transform directly from a computerised digital model into a solid part. High quality 3D printed metal parts for aerospace, defence, medical, automotive and electronics applications need to have high strength, dimensional accuracy, water tightness and light weight. Quality control means for metal 3D printing processes In addition to the printing equipment, the properties of the metal powder, including powder sphericity and cleanliness, particle size distribution
sphericity and cleanliness of the powder, particle size distribution, oxygen content, flowability and loose packing density The quality of the metal powder, including powder sphericity and cleanliness, particle size distribution, oxygen content, fluidity and bulk density, also have a significant impact.
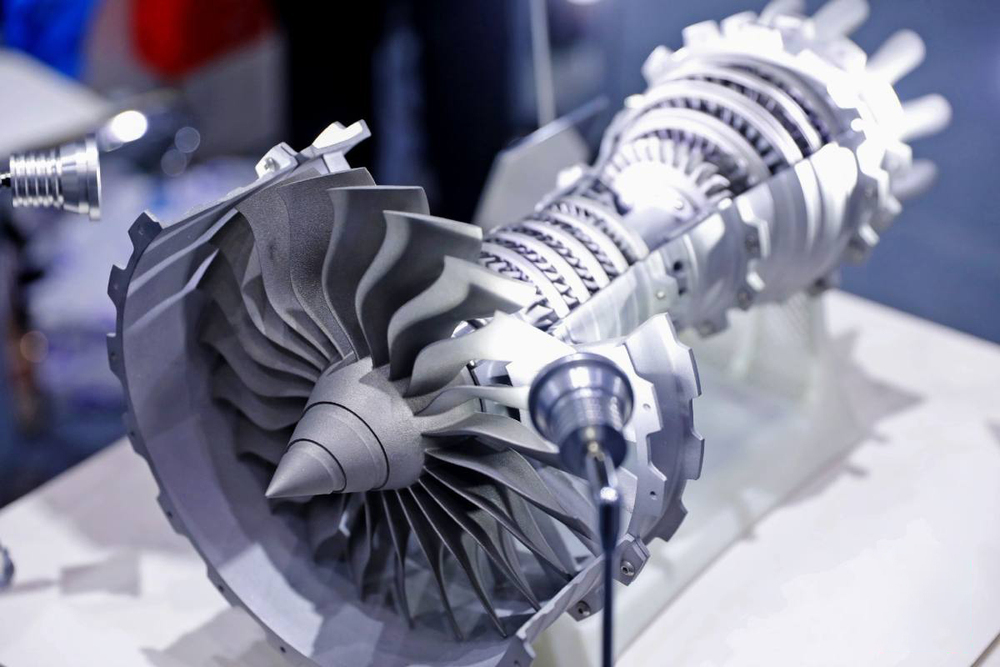
Key Performance Indicators of 3D Printing Metal Powders
(1) Purity. Ceramic inclusions can significantly reduce the performance of the final part, and these inclusions generally have a high melting point and are difficult to sinter into shape, so the powder needs to be free of ceramic inclusions. In addition, the oxygen and nitrogen content needs to be strictly controlled. The current powder preparation technology for metal 3D printing is mainly based on atomisation (including techniques such as aerosolisation and rotary electrode atomisation), where the powder has a large specific surface area and is easily oxidised. In aerospace and other special applications, the customer requirements for this indicator is more stringent, such as high temperature alloy powder oxygen content of 0.006% ~ 0.018%, titanium alloy powder oxygen content of 0.007% ~ 0.013%, stainless steel powder oxygen content of 0.010% ~ 0.025% (all mass fraction). For titanium alloy powder, nitrogen, hydrogen and titanium at high temperatures will form TiN and TiH2, reducing the plasticity and toughness of titanium alloy. Therefore, the powder preparation process should be strictly controlled for the atmosphere.
(2) Powder particle size distribution. As mentioned above, different 3D printing equipment and forming processes require different powder particle size distributions. At present, the commonly used powder particle size range for metal 3D printing is 15-53 μm (fine powder), 53-105 μm (coarse powder), which can be relaxed to 105-150 μm (coarse powder) in some occasions [11]. 3D printing with metal powder particle size selection is mainly based on the different energy sources of metal printers, with laser as the energy source of the printer, because of its fine focus spot, easier to melt Fine powder, suitable for use 15 ~ 53 μm powder as consumables, powder replenishment method for layer by layer laying powder; to electron beam as the energy source of laying powder type printer, focusing spot slightly coarse, more suitable for melting coarse powder, suitable for use 53 ~ 105 μm coarse powder as the main; for coaxial powder feed type printer can use the particle size of 105 ~ 150 μm powder as consumables.
(3) Powder morphology. Powder morphology and powder preparation method is closely related, generally from the metal gas or molten liquid into powder, powder particle shape tends to spherical; from the solid state into powder, powder particles are more irregular shape; and by the aqueous solution electrolysis method of preparing the powder most dendritic. Generally speaking, the higher the sphericity, the better the fluidity of the powder particles.
3D printing metal powders require a sphericity of 98% or more, which makes it easier to spread and feed the powder during printing. Aerosolisation and rotating electrode methods are the main methods for the preparation of high quality 3D printing metal powders.
- Powder fluidity and loose packing density. Powder fluidity directly affects the uniformity of powder spreading and the stability of the powder feeding process in the printing process. (4) Powder fluidity and bulk density. The fluidity is related to the powder morphology, particle size distribution and bulk density. The larger the powder particles, the larger the particle size distribution and the density of the powder. The larger the powder particles, the more regular the particle shape and the smaller the proportion of very fine powder in the particle size composition The larger the powder particles, the more regular the particle shape and the smaller the proportion of very fine powder in the particle size composition, the better the mobility. Particle The density remains the same, the relative density increases and the powder mobility increases. Particles The adsorption of water, gases etc. on the surface will reduce the fluidity of the powder. Loose packing density is a unit volume of powder when the powder specimen naturally fills the specified container. The mass of the powder. In general, the coarser the powder size, the higher the bulk density. The coarser the powder, the higher the bulk density. Loose The effect of bulk density on the density of the final metal printing product is not conclusive. There is no conclusive evidence on the effect of bulk density on the density of the final metal print product, but an increase in bulk density improves the flow of the powder.
3D printing is an emerging material manufacturing technology that has developed rapidly in recent years, as it is suitable for a wide range of materials and has a wide range of applications and high materialisation rates.
Metal powders are an important consumable for metal 3D printing, of which AA and PREP methods have been successfully applied in the aerospace industry. The AA and PREP methods have been successfully applied in the aerospace industry. However, metal powders for 3D printing need to be The powder size must be small, with a narrow particle size distribution, high sphericity, low oxygen content The use of metal powders for 3D printing is clearly a major challenge. It is clear that the PREP method is better than the traditional AA method (VIGA) for the application of metal powders in 3D printing. The PREP method is clearly more advantageous than the traditional AA method (VIGA method) for the preparation of high-quality 3D printed metal components, and is now widely used in coaxially fed 3D printing machines. The PREP method has been widely used in coaxially fed 3D printing machines. The PREP method has been widely used in coaxially fed 3D printing machines due to its ability to produce ultra-fine spherical powders (particle size up to 50 μm). (particle size up to 50 μm) and the relatively low production The use of PREP in powder spreading 3D printing equipment is relatively low due to its low yield and relatively low productivity. Therefore, there is an urgent need to optimize the process and develop a new generation of plasma rotary electrode atomised powder technology and equipment to further improve the yield of ultra-fine spherical metal The development of a new generation of plasma rotary electrode atomisation technology and equipment is therefore urgently needed to further improve the yield of ultra-fine spherical metal powders and to achieve The technology and equipment will further improve the yield of ultra-fine spherical metal powders and achieve the continuous production of high quality ultra-fine spherical metal powders such as nickel-based, cobalt-based alloys and titanium alloys in large quantities, thereby
The PREP method can be used to improve the cost performance of metal powders and adapt them to various This will improve the cost effectiveness of the PREP method and enable it to be adapted to various types of 3D printing equipment, making it more widely used in 3D printing.