Overview of Additive Manufacturing Powder
Additive manufacturing, also known as 3D printing, utilizes various materials in powder form to construct parts and products layer by layer. The type of powder selected depends on the specific additive manufacturing process being used, as well as the desired characteristics of the finished part.
Some of the key types of additive manufacturing powders include:
- Metal Powders – Used in powder bed fusion and directed energy deposition processes. Common materials include titanium, aluminum, steel, nickel alloys, and cobalt-chrome.
- Polymer Powders – Used in powder bed fusion and material jetting processes. Common materials include nylon, ABS, polycarbonate, polystyrene, and thermoplastic polyurethane.
- Ceramic Powders – Used in binder jetting and material extrusion processes. Common materials include silica, alumina, zirconia, and porcelain.
- Sand and Casting Powders – Used in binder jetting processes to create molds and cores for metal castings. Usually silica-based.
- Biocompatible and Bioactive Powders – Used in medical applications. Common materials include titanium, hydroxyapatite, and tricalcium phosphate.
The characteristics of additive manufacturing powders can significantly influence the properties, quality, accuracy, and performance of printed parts. Key powder properties include:
Additive Manufacturing Powder Composition
Additive manufacturing utilizes metallic, polymeric, ceramic, sand, and other powder materials with specific compositions tailored to various printing processes.
Metal Powders
Type | Common Compositions |
---|---|
Titanium alloys | Ti-6Al-4V, Ti-6Al-7Nb, Ti-Al-Fe, Ti-Al-Mn, Ti-Al-Sn |
Aluminum alloys | AlSi10Mg, AlSi12, Scalmalloy |
Steel alloys | 17-4PH, 316L, 304L, 4140 |
Nickel alloys | Inconel 625, 718; Hastelloy X |
Cobalt-chrome | CoCrMo |
Polymer Powders
Type | Common Compositions |
---|---|
Nylon | Nylon 11, Nylon 12 |
ABS | Acrylonitrile butadiene styrene |
Polycarbonate | Bisphenol A polycarbonate |
Polystyrene | PS, High impact PS |
Thermoplastic Polyurethane | TPU |
Ceramic Powders
Type | Common Compositions |
---|---|
Silica | Fused quartz, cristobalite |
Alumina | Al2O3 |
Zirconia | ZrO2, YSZ (yttria stabilized) |
Porcelain | Mix of glass, clay and feldspar |
Sand and Casting Powders
Type | Compositions |
---|---|
Silica sand | Mostly SiO2, with traces of metal oxides and nonmetal oxides |
Zircon sand | Zirconium silicate |
Olivine sand | Magnesium iron silicate |
Chromite sand | Iron chromium oxide |
Bioactive and Biocompatible Powders
Type | Common Compositions |
---|---|
Titanium and alloys | Pure titanium, Ti-6Al-4V |
Hydroxyapatite | Ca10(PO4)6(OH)2 |
Tricalcium phosphate | Ca3(PO4)2 |
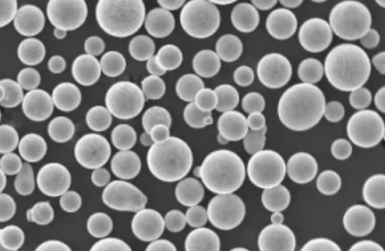
Additive Manufacturing Powder Properties
The key properties of additive manufacturing powders that influence part quality and process performance include:
Property | Description | Significance |
---|---|---|
Particle size distribution | Range and distribution of powder particle dimensions | Affects powder flowability, packing density, layer uniformity, resolution |
Morphology and shape | Aspect ratio and shape factors of powder particles | Impacts spreading, packing density, powder flow |
Density | Mass to volume ratio of the bulk powder | Determines weight and dimensional accuracy of parts |
Flowability | Ability of powder to flow freely under applied stress | Vital for uniform spreading and recoating of powder layers |
Moisture content | Percentage water content in the powder | High moisture causes powder agglomerations and printing defects |
Chemical composition | Elemental composition and phases present | Defines mechanical properties, microstructure, and performance of finished parts |
Additive Manufacturing Powder Applications
Additive manufacturing powders are used to print functional components across major industries:
Industry | Applications | Materials Used |
---|---|---|
Aerospace | Turbine blades, aircraft components, rocket engines | Titanium alloys, nickel alloys, aluminum alloys, cobalt chrome |
Automotive | Prototyping, production of parts like gears, brackets | Aluminum alloys, nylon, ABS |
Medical | Dental copings, implants, surgical instruments | Titanium alloys, cobalt chrome, stainless steel |
Consumer | Jewelry, decorative objects, lighting fixtures | Precious metals like gold, silver; polymers |
Additive Manufacturing Powder Specifications
Powder materials used in specific additive manufacturing process conform to certain size, composition, property thresholds:
Process | Particle Size | Alloy Grade | Standards |
---|---|---|---|
Powder bed fusion | 15-45 microns | Ti-6Al-4V ELI per ASTM F3001 | ASTM F3049, ASTM F2924, ASTM F2971 |
Binder jetting | 20-60 microns | 420 or 316 stainless steel | ASTM F3301, MPIF 35 |
Material jetting | 5-25 microns | 60-65 Shore D polyurethane | – |
Directed energy deposition | 45-150 microns | Inconel 718, 316L stainless steel | ASTM F3055, ASTM F3302 |
Additive Manufacturing Powder Suppliers
There is a robust network of suppliers offering a wide array of metal, polymer, ceramic and composite additive manufacturing powders:
Company | Powder Materials | Cost Range |
---|---|---|
LPW Technology | Titanium alloys, aluminum alloys, stainless steel, nickel alloys | $100-$500 per kg |
Sandvik Osprey | Stainless steel alloys, nickel alloys, cobalt alloys | $50-$250 per kg |
Advanced Powders & Coatings | Nylon-based polymers, PEEK, PEKK | $80-$600 per kg |
The ExOne Company | Stainless steel, tool steel, tungsten carbide, Inconel 625 | $75-$1000 per kg |
Höganäs | Stainless steel, iron-based alloys | $30-$150 per kg |
Kennametal | Tungsten carbide-cobalt, 17-4PH stainless | $100-$1200 per kg |
3DCeram | Alumina ceramic, zirconia ceramic, silica | $100-$250 per kg |
Comparison Between Additive Manufacturing Powders
There are considerable differences between various powder options regarding production processes, cost, part properties and quality:
Parameter | Polymer Powder | Metal Powder | Ceramic Powder |
---|---|---|---|
Build rate | Medium | Slow | Fast |
Resolution | Medium | High | Medium to low |
Part strength | Low to medium | Very high | Medium to high |
Part accuracy | Medium | Medium to high | Low to medium |
Surface finish | Medium | High | Low to medium |
Thermal properties | Low melting point, low conductivity | High melting point, high conductivity | High melting point, low conductivity |
Cost per part | Low to medium | High | Medium |
Post-processing | Minimal | Extensive | Medium |
Advantages of Using Powder Bed Additive Manufacturing
Some of the major advantages of using powder bed technology for manufacturing parts include:
- Ability to create complex, lightweight geometries not possible with casting or machining
- Minimal raw material waste since unused powder is recycled
- Does not require dedicated tooling or molds, allowing rapid prototyping
- Parts show high strength, durability, heat and corrosion resistance matching wrought materials
- Porosity and microstructure can be easily controlled
- Multiple materials and alloys, even graded compositions are printable
- Just-in-time production with minimal lead times is enabled
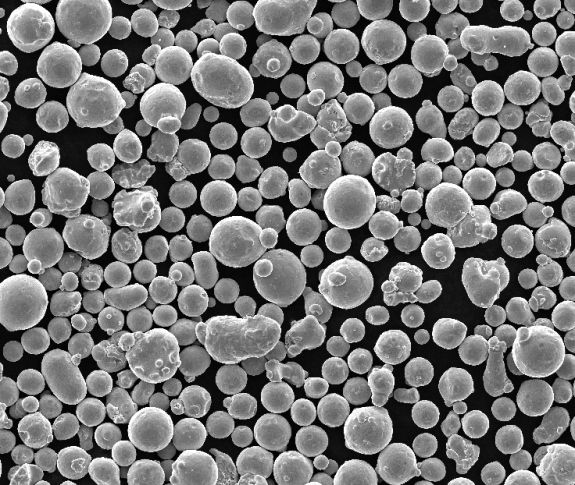
Limitations of Powder Bed Additive Manufacturing
Some drawbacks associated with powder bed additive manufacturing that need to be considered:
- High equipment and operational costs compared to other processes
- Additional post-processing like Hot Isostatic Pressing is often essential
- Powder handling procedures and equipment require special attention
- Printing of certain flexible polymers and rubber-like materials poses challenges
- Not ideal for very high volume and mass production scenarios
- Size constraints posed by build chamber dimensions may require redesigning large parts
FAQ
Q: What is the most commonly used metal powder for additive manufacturing?
A: Titanium alloys like Ti-6Al-4V are one of the most popular metal powders, due to their high strength to weight ratio and biocompatibility. Aluminum alloys, stainless steels, cobalt chrome, and nickel superalloys are also very commonly used.
Q: How fine are the powders used in AM processes?
A: The typical size range is 10-100 microns, though some processes can use ultrafine 1-10 micron nano powders. Finer powders below 20 microns result in better resolution and accuracy.
Q: What affects the pricing of additive manufacturing powders?
A: Raw material costs, composition, alloy type, particle characteristics like size distribution, flowability and morphology, purity levels, and purchase volume dictate prices. Complex alloys are costlier than simpler ones.
Q: Does the shape of powder particles matter for additive manufacturing?
A: Yes, spherical powders with good flowability, pack density and spreadability perform much better compared to highly irregular or angular powders during printing. The particle shape influences density, layer uniformity and surface finish.
Q: Can any off-the-shelf powders be used for AM processes?
A: Not always – most processes require custom powders with compositions, sizes and shapes tailored specifically for 3D printing applications to ensure ideal flow and fusion. Only established manufacturers with stringent quality control are recommended.
Q: How is unused metal powder reused or recycled in additive manufacturing?
A: After prints, the unsintered powder is filtered to remove large agglomerates and then blended with small quantities of fresh powder, to maintain its flowability, density and composition within tight limits. This powder recycling reduces costs and waste substantially.
Q: What causes layer delamination issues in powder bed 3D printing?
A: Insufficient bonding between layers results from improper preheating, uneven powder distribution, inadequate energy input, unfavorable thermal gradients or poor particle packing density among the common reasons. Optimizing process parameters is vital.
Q: Are additive manufacturing metal powders flammable hazards?
Many reactive elemental and alloy powders are highly flammable when finely divided. Proper ventilation, electrical grounding of equipment, specialized exhaust systems, spark detection and fire suppression are essential safety measures. Powder storage and handling also needs special precautions.