3D printing is also known as additive manufacturing, and additive manufacturing is a concept proposed as opposed to traditional subtractive manufacturing. We know that subtractive manufacturing is the process of cutting and sintering raw materials to produce parts, powder metallurgy, and cutting processes are all part of subtractive manufacturing. So, what does the corresponding additive manufacturing technology mean? And what technologies are used in additive manufacturing? This article will discuss what technology is used in 3D printing?
The Principle of 3D Printing
Before answering the question of what technology is used in 3D printing, it is necessary to understand the principles of 3D printing. 3D printing is a technology that uses digital model files as a basis for constructing objects by printing layer by layer using bondable materials such as powdered metal or plastic.
3D printing is usually achieved using digital technology material printers. It is often used to make models in mold-making and industrial design, and then gradually for the direct manufacture of some products, and parts have been printed using this technology.
Compared to traditional printing technologies and manufacturing processes, 3D printing has several features. Firstly, printing is done in a single pass, eliminating the need for repeated cutting and grinding, simplifying the process of product production, and shortening production
This simplifies the production process and shortens the production cycle. Secondly, the lower cost, especially in terms of batch production, is a significant cost advantage compared to traditional manufacturing. Finally, a higher degree of product sophistication.
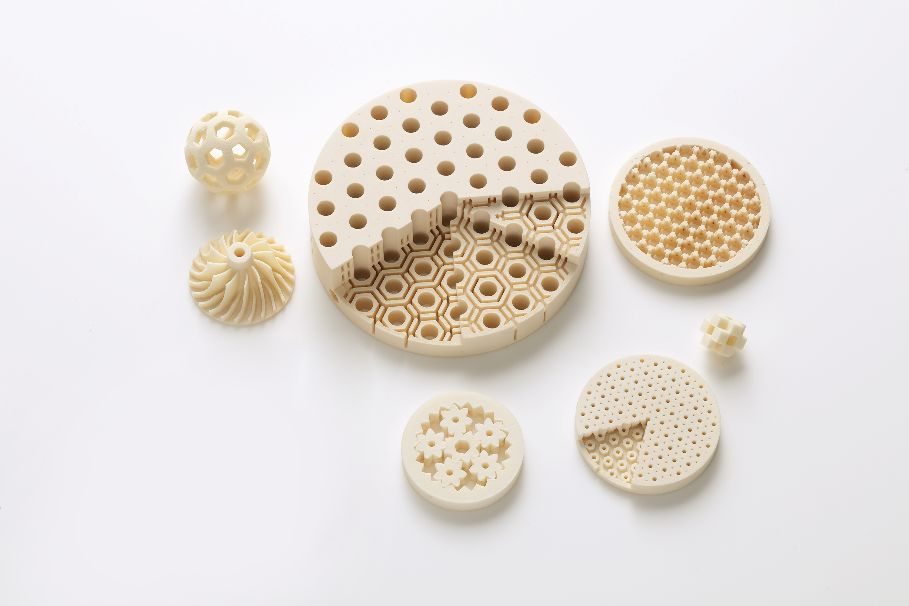
3D Printing Technologies
FDM
Fused deposition modeling, (FDM), is a method of heating and melting various hot molten filamentary materials (wax, ABS and nylon, etc.) into shape and is a type of 3D printing technology. The FDM process utilizes the hot melt, bonding properties of thermoplastic materials stacked layer by layer under PLC control. Common base materials include thermoplastic materials, eutectic system metals, edible materials, etc.
EBF
Electron beam free-forming (EBF) is a process that uses an electron beam as a heat source to construct parts using off-axis metal wires. Near-net-formed parts made by this additive manufacturing process require subsequent finishing using a reduction process.
EBF technology can directly form metals such as aluminum, nickel, titanium, or stainless steel, and it is possible to mix two materials or to embed one into the other. The technology is suitable for almost any alloyed metal material.
DMLS
Direct metal laser sintering is a process used to mass-produce molds for injection molded parts and to manufacture metal products, but it can also be used in technologies such as extrusion or blow molding and other plastic processing. DMLS is suitable for 3D printing of almost any alloy.
Electron Beam Melting (EBM) is an emerging advanced metal additive manufacturing technology in recent years. The principle is to import the 3D solid model data of the part into the EBM equipment, then lay a thin layer of fine metal powder flat in the working chamber of the EBM equipment. The high density of energy generated at the focal point by the deflection and focus of the high energy electron beam causes the metal powder layer to be scanned to produce high temperatures in tiny localized areas, resulting in the melting of the metal particles, and the continuous scanning of the electron beam will cause the tiny pools of metal to fuse and solidify, connecting to form linear and faceted metal layers.
Selective laser melting is one of the main technologies used in the additive manufacturing of metal materials. It uses a laser as the energy source and scans the metal powder bed layer by layer according to the path planning in the 3D CAD cut-out model. The scanned metal powder is melted and solidified to achieve a metallurgical bonding effect, resulting in the metal part designed by the model. Mainly suitable for 3D printing on titanium, cobalt-chromium, stainless steel, aluminum, etc.
SLS
The SLS process, also known as selective laser sintering, was developed in 1989 by C.R. Dechard at the University of Texas at Austin, U.S.A. The SLS process uses powdered material for forming. The powdered material is spread on the upper surface of the formed part and scraped flat; a high-intensity CO2 laser is used to scan the part cross-section over the freshly laid new layer; the powdered material is sintered together under the high-intensity laser light to obtain a cross-section of the part, which is bonded to the formed part below; when one layer of the cross-section has been sintered, a new layer of material powder is laid on and the next layer of the cross-section is selectively sintered.
Above we have described some of the technologies used in 3D printing. In recent years, 3D printing technology has shown strong application advantages in many fields, and many precision parts and products based on 3D printing technology have had a positive impact in promoting industrial development and innovation.
With the development of complementary technologies, more printing materials will be available in the future, and 3D printing will reduce the cost of printing equipment and enhance the human and intelligent nature of printing operations, thus providing technical support for social and economic development.
This will provide technical support for social and economic development.
Contact Turer to get a free metal 3D printing Solution!