3D printing, also known as additive manufacturing, has revolutionized product design and manufacturing processes. By building objects layer-by-layer from the bottom up, 3D printing enables on-demand production without dedicated tooling or molds. There are now numerous types of 3D printing technologies available, each with their own advantages and limitations. This guide provides a comprehensive overview of the major 3D printing processes in use today.
Overview of Key 3D Printing Methods
3D printing technologies can be broadly categorized into 7 types:
Table: Overview of Major 3D Printing Methods
Method | Materials | Key Characteristics | Typical Applications |
---|---|---|---|
Fused Deposition Modeling (FDM) | Thermoplastics like PLA, ABS | Low cost, good strength | Prototypes, hobbyist printing |
Stereolithography (SLA) | Photopolymers | High accuracy, smooth surface | Prototypes, manufacturing |
Selective Laser Sintering (SLS) | Thermoplastics, metals | Good mechanical properties | Functional prototypes, manufacturing |
Multi Jet Fusion (MJF) | Thermoplastics | Fast printing, good accuracy | Manufacturing, mass customization |
Electron Beam Melting (EBM) | Metals | Full dense metal parts | Manufacturing, aerospace |
Laminated Object Manufacturing (LOM) | Paper, metal, plastic sheets | Low cost, large parts | Concept models, tooling |
Directed Energy Deposition (DED) | Metal alloys | Large metal parts, repairs | Aerospace, automotive |
As seen in the table, the choice of 3D printing method depends on factors like target application, suitable materials, accuracy, speed, and cost. Each method has pros and cons that make it preferable for certain uses over others.
The rest of this guide examines each of these techniques in greater depth.
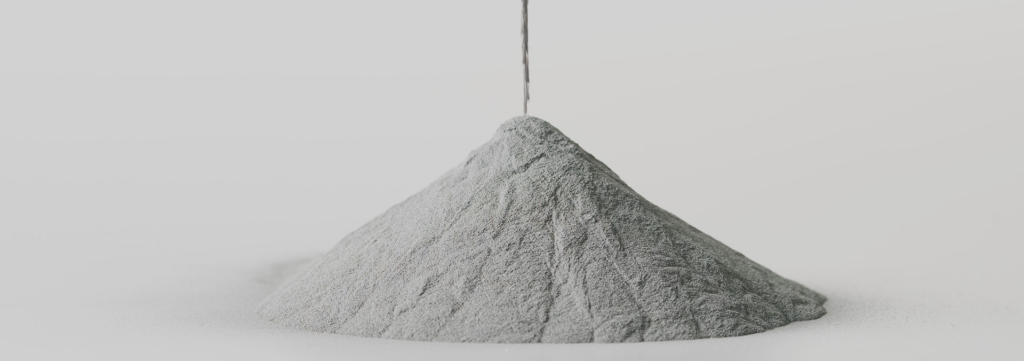
Fused Deposition Modeling (FDM)
Fused deposition modeling, or FDM, is the most common and affordable type of 3D printing used today. In FDM, an extruder heats thermoplastic filament to a semi-liquid state and deposits it layer-by-layer to build an object.
How FDM 3D Printing Works
The FDM process involves:
- Heating thermoplastic filament above its glass transition temperature to make it pliable
- Extruding the semi-molten material through a nozzle onto the build plate
- Tracing out a 2D layer, allowing it to cool and harden
- Moving the build plate down, and repeating with the next layer
FDM printers have a movable extruder head that follows a toolpath in X-Y coordinates while depositing material. The most popular materials used are ABS and PLA plastics. Dual extrusion machines can print using dissolvable supports and multiple colors.
Applications of FDM
Table: FDM 3D Printing – Uses and Capabilities
Attribute | Description |
---|---|
Cost | Low-cost 3D printing, machines under $300 |
Materials | ABS, PLA, PETG, flexible TPU, composites |
Accuracy | ±100 microns, medium resolution |
Speed | Moderate, 30-100 mm/s extrusion |
Part Size | Small to medium, max around 1 cubic foot |
Key Applications | Concept models, prototyping, hobbyist printing |
FDM is preferred for non-critical applications that benefit from inexpensive, fast, and low-wastage prototyping capability. The average accuracy and surface finish make it suitable for form and fit testing rather than functional prototypes. Parts can be drilled, sanded, painted or electroplated post-processing.
Advantages of FDM Printing
- Low machine and material costs make it accessible for small businesses
- Minimal waste compared to subtractive methods
- Ease of use with minimal training or expertise required
- Ability to pause and change filament for multi-color prints
- Functional parts with good mechanical properties and thermal resistance
Limitations of FDM Printing
- Medium accuracy of 100 microns limits precision of fine details
- Visible layer lines affect surface finish quality
- Limited number of materials compared to other processes
- Overhangs and bridges require support structures
Overall, FDM strikes a balance of affordability and capability that makes it a versatile starting point for companies exploring the benefits of additive manufacturing.
Stereolithography (SLA)
Stereolithography (SLA) was the first commercial 3D printing process, invented in the 1980s. It remains a popular choice for its high accuracy and surface quality.
How SLA Printing Works
SLA uses a vat of liquid photopolymer resin that is selectively cured layer-by-layer using an ultraviolet laser.
The main steps are:
- A build platform lowers into the liquid resin vat
- A laser beam traces the cross-section of the model, curing the resin
- The platform raises, allowing fresh resin to flow under
- The next layer is traced right above the previous one
- Once complete, the model is rinsed and cured further
The light causes polymers in the resin to crosslink, turning liquid resin into solid plastic in the desired shape. SLA builds highly detailed models with excellent surface finish.
Applications of SLA Printing
Table: SLA 3D Printing – Uses and Capabilities
Attribute | Description |
---|---|
Cost | Moderate machine cost, resin is $100-200/liter |
Materials | Standard and engineered resins, clear, flexible, castable |
Accuracy | Very high, up to 25 microns |
Speed | Fast, up to 110 mm/hour |
Part Size | Medium, max around 1 cubic foot |
Key Applications | Detailed prototypes, end-use parts, dental, jewelry |
The fine resolution makes SLA ideal for applications like concept models, visualization prototypes, dental aligners, jewelry casting, and precise end-use parts across aerospace, healthcare, and consumer products.
Advantages of SLA Printing
- Excellent surface finish and tiny details down to 25 micron resolution
- High dimensional accuracy for precision fits
- Good mechanical properties comparable to injection molding
- Supports can be easily detached after printing
Disadvantages of SLA Printing
- Photopolymer resin is more expensive than FDM filament
- Post-processing like rinse stations and UV curing chambers needed
- Resin is sensitive to light and moisture
- Limited range of materials compared to other processes
Overall, SLA offers an attractive balance of speed, detail, and strength, making it a versatile rapid prototyping process.
Selective Laser Sintering (SLS)
Selective laser sintering (SLS) uses a high power laser to fuse powdered material layer-by-layer to build a 3D object. It was developed by Carl Deckard at the University of Texas in the 1980s.
How SLS 3D Printing Works
SLS printing involves:
- A roller spreads a thin layer of powder across the build area
- A laser sinters the powder selectively, tracing the layer cross-section
- The build platform lowers, another layer of powder is spread
- The process repeats until the part is completed
- Excess powder supports overhangs while printing
- Completed parts are removed from the powder bed
A variety of thermoplastic and metal powders can be used in SLS machines. The laser melts the powder just below its boiling point, fusing particles together solidly.
Applications of SLS Printing
Table: SLS 3D Printing – Uses and Capabilities
Attribute | Description |
---|---|
Cost | High machine cost, moderate material cost |
Materials | Nylon, TPU, PEEK, aluminum, steel, alloys |
Accuracy | ±100 microns for plastics, ±50 μm for metals |
Speed | Moderate, 5-7 in3/hour |
Part Size | Medium to large, up to 15 x 13 x 18 inches |
Key Applications | Functional prototypes, end-use parts, tooling |
The key advantages of SLS include good mechanical properties, minimal supports, and multi-material printing. It is widely used for functional prototypes across automotive, aerospace, and medical sectors.
Advantages of SLS Printing
- Excellent strength and thermal properties with Nylon 12 powder
- No need for dedicated support structures
- Large parts printable in a single build
- Variety of materials from plastics to composites
- Porous metal structures possible
Disadvantages of SLS Printing
- Powder-based process is messy and requires handling systems
- Lower resolution around 100 microns
- Porous and grainy surface finish requiring smoothing
- Limited number of metal alloys available currently
- High equipment cost, especially for metal powders
Overall, SLS can produce highly functional prototypes and end-use parts unmatched by most other 3D printing processes. Continued advances in materials will further widen its capabilities.
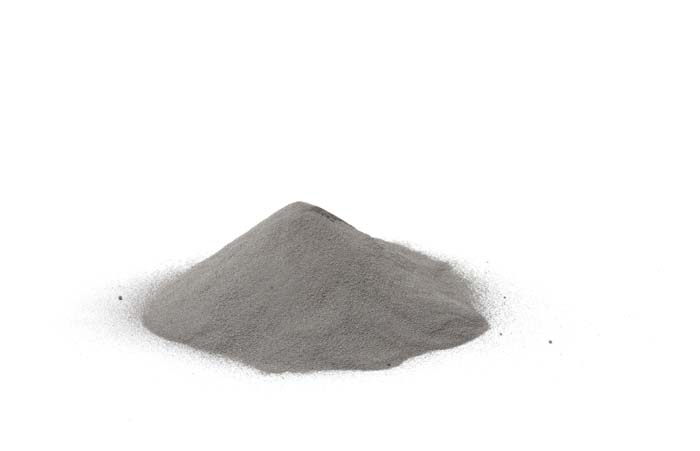
Multi Jet Fusion (MJF)
Developed by HP, Multi Jet Fusion is an industrial 3D printing process known for its fast build speeds. It uses an inkjet printhead and infrared lasers to fuse together polymer powder layer-by-layer.
How Multi Jet Fusion Works
The MJF printing process involves:
- A layer of powder spread across the build platform
- Inkjet printheads selectively deposit fusing and detailing agents
- Infrared lamps melt and fuse powder where fusing agent is applied
- Fresh layer of powder spread across, process repeats
- Unfused powder supports overhangs during printing
- Completed parts are removed from the powder bed
MJF produces excellent quality parts in full color, up to 10 times faster than SLS. The layered approach also enables functional gradients and flexible properties.
Applications of MJF Printing
Table: Multi Jet Fusion Capabilities
Attribute | Description |
---|---|
Cost | High machine cost, moderate material cost |
Materials | Nylon 12, PBT, TPU plastics |
Accuracy | Up to 80 microns |
Speed | Very fast, 5-15 cm/hour |
Part Size | Medium to large, 380 x 284 x 380 mm build volume |
Key Applications | End-use parts, mass customization, tooling |
The key strengths of MJF are its speed, quality, and functionality. It is ideal for short-run production across automotive, industrial, medical, and consumer goods.
Advantages of MJF 3D Printing
- Extremely fast build speeds via layer-wise approach
- Excellent mechanical properties and feature detail
- Full color prints possible in CMYK with voxel control
- Functional gradients and durometers customizable
- High reusability of unfused powder
Limitations of MJF
- Relatively new process, printer costs over $200k
- Limited material availability beyond Nylon 12 currently
- Requires handling un-sintered powder
- Lower accuracy compared to SLA or PolyJet (~80 microns)
- Smaller build volumes than SLS systems
As the technology matures, MJF promises to be a production-ready additive manufacturing solution combining speed, quality, and functionality.
Electron Beam Melting (EBM)
Electron beam melting (EBM) uses a powerful electron beam in a vacuum to melt and fuse metallic powders into fully dense parts layer-by-layer. It was developed in Sweden by Arcam AB in the 1990s.
How EBM 3D Printing Works
The EBM printing process works as follows:
- Metal powder is spread evenly across a build platform in a vacuum
- An electron beam selectively melts powder to trace each layer
- Lower temperatures pre-heat powder just below melting point
- The build plate lowers and powder spreader applies new layer
- Once complete, parts are left to cool before removing from machine
Any conductive metal can be 3D printed using EBM, but titanium alloys and cobalt chrome are most common. The high power ensures excellent material properties.
Applications of EBM Printing
Table: Electron Beam Melting – Uses and Capabilities
Attribute | Description |
---|---|
Cost | Very high machine cost, moderate material cost |
Materials | Titanium alloys, stainless steel, nickel, cobalt chrome |
Accuracy | ±100 microns or better |
Speed | Moderate, approx. 40-50 cm3/hr |
Part Size | Medium to large, upto 275 x 275 x 380 mm |
Key Applications | Orthopedic implants, aerospace parts, automotive |
EBM creates fully dense end-use metal parts for applications requiring high strength, heat resistance, and biocompatibility. The aerospace industry was an early adopter.
Advantages of EBM 3D Printing
- Fully melted metals with excellent material properties
- Good accuracy and surface finish
- Low internal stresses reduce warping
- High beam power results in good build speed
- Unused powder can be reused, minimizing material costs
Disadvantages of EBM Printing
- Very high equipment cost, limiting adoption
- Limited to conductive materials, mostly metals
- Post-processing like supports removal required
- Moderate build speeds slower than other methods
- Vacuum systems add engineering complexity
Overall, EBM can produce complex geometries in high performance metals unmatched by conventional manufacturing. It will continue growing across aerospace, medical, and automotive applications.
Laminated Object Manufacturing (LOM)
Laminated object manufacturing, or LOM, uses sheets of material joined together with heat or adhesive to build a 3D object. It was introduced in 1985 by Helisys Inc, which was later acquired by Cubic Technologies.
How LOM 3D Printing Works
The LOM process works as follows:
- Sheets of material are bonded together to form a block
- A heated roller laminates each new sheet onto the stack
- A laser or knife cuts the outline of each layer into the sheet
- Excess material remains in place to support overhangs
- Once printing completes, the part is separated from the extra material
Paper, plastic, composites, and metals can be used as the laminating material. LOM is relatively low cost and can produce large layered objects.
Applications of LOM Printing
Table: Laminated Object Manufacturing – Attributes
Attribute | Description |
---|---|
Cost | Low machine cost, low material cost |
Materials | Paper, plastic, composites, sheet metals |
Accuracy | Medium, around 200 microns |
Speed | Slow, depends on layer bonding |
Part Size | Large, up to 16 ft x unlimited length |
Key Applications | Concept models, form studies, tooling |
The key advantage of LOM is the ability to rapidly produce large layered objects at low costs. It is a great way to evaluate esthetic prototypes and full-scale models not feasible with other methods.
Advantages of LOM Printing
- Low machine and material costs make LOM accessible
- Build volume is theoretically unlimited
- Minimal material waste or post-processing
- Does not require support structures
- Easy integration of wood, paper, composites
Disadvantages of LOM
- Low accuracy around 200 microns
- Visible layer lines affect surface finish
- Tedious final separation of printed part
- Limited materials and material properties
- Bonding layers can be time-consuming
While the quality is not suitable for functional parts, LOM remains a compelling technology for full-scale esthetic models at consumer-friendly prices.
Directed Energy Deposition (DED)
Directed energy deposition (DED) uses a focused heat source like a laser, electron beam, or plasma arc to melt and deposit material simultaneously. It is an additive manufacturing process capable of fabricating large metal parts.
How DED 3D Printing Works
DED uses the following general process:
- A nozzle deposits metal powder at a precise location
- An energy source like a laser melts the powder to form a metallurgical bond
- The part is built up layer-by-layer by depositing and melting material
- DED systems are usually mounted on multi-axis arms for complete coverage
- Manipulators rotate and position the part as it builds up
- Minimal support structures are required during printing
DED can print features onto existing components like machine tools or engine blocks. This enables rapid repair, enhancement, and modification of metal parts.
Applications of DED Printing
Table: Directed Energy Deposition – Applications
Attribute | Description |
---|---|
Cost | High equipment cost, high material cost |
Materials | Stainless steel, titanium, Inconel, cobalt alloys |
Accuracy | ±100 microns |
Speed | High deposition rate of 0.1-0.5 kg/hour |
Part Size | Very large, unlimited as device moves |
Key Applications | Metal coating, repair, tooling, aerospace, defense |
The key advantage of DED is its ability to fabricate large metal components in virtually unlimited sizes and modify existing assets.
Advantages of DED Printing
- Can produce extra large metal parts measured in feet
- Highly portable, capabilities brought to asset via multi-axis arm
- Rapid turnaround measured in hours versus weeks
- Can add features onto existing metal parts
- Reduced material waste compared to machining
Disadvantages of DED Printing
- Very high equipment costs in the millions
- Slow cycle times measured in hours
- Limited accuracy and surface finish
- Requires extensive operator training
- Post-processing like machining required to finish parts
DED is better suited for adding metal material rapidly versus final part production. As the technology improves, it promises to transform field repair and modification across many industries.
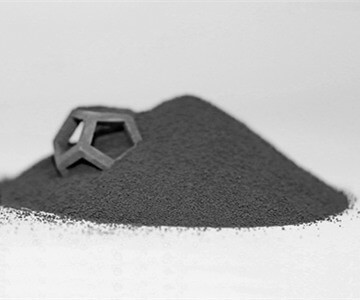
How to Choose a 3D Printing Technology
With so many 3D printing processes to choose from, how do you select the right method for an application?
Step 1: Understand Design Requirements
First, analyze the key requirements of your application:
- What are the target materials needed – plastic, metal, polymer?
- What accuracy and tolerances are expected?
- What is the desired part size and build volume?
- Does the surface finish need to be smooth or coarse?
- Does the part need specific mechanical properties? Strength, flexibility, hardness?
- What quantity is needed – a few prototypes or higher production runs?
- How fast does the project need to be completed?
Document the must-have attributes for your application. This forms the basis for choosing a 3D printing method.
Step 2: Map Requirements to Printing Technologies
Next, map your requirements to the capabilities of each 3D printing technology:
- If metals are required, look into DMLS, SLS or EBM
- For smooth surface finish, consider SLA, DMLS, PolyJet
- FDM can provide good strength and functional prototyping
- LOM allows printing large hollow parts
- SLA, SLS, Material Jetting enable multi-material parts
- Binder Jetting is optimal for high mix production
Create a table relating requirements to potential 3D printing methods to visualize the match.
Step 3: Rank by Importance and Compatibility
Prioritize your requirements from absolute essentials to nice-to-haves.
Then rank each technology on how well it matches to your priorities on a scale of 1-5.
This will provide an objective score to compare processes. The best match balances key requirements and capabilities.
Step 4: Evaluate Cost, Lead Time and Experience
Also factor in practical considerations:
- What 3D printing experience and skills do you possess in-house? Is training needed?
- What equipment cost, operation cost, and material cost makes sense for your budget?
- Can you manage the post-processing requirements of the method?
- What is your project deadline? Does the build speed match your schedule?
Weigh the qualitative and quantitative factors together to make the optimal technology choice. Leverage 3D printing services if needed to de-risk adoption.
Step 5: Validate with Prototyping
Before finalizing, build some test prototypes on the shortlisted technologies to validate compatibility.
Evaluate if the accuracy, finish, mechanical performance match expected results and iterate if needed.
Prototyping mitigates surprises and helps lock-in the best 3D printing process for an application.
Following this structured criteria ensures your 3D printing investments are targeted for maximum value and productivity gains.
The Future of 3D Printing
3D printing technology has made rapid strides since its inception over 30 years ago. The market is projected to continue growing at an average of 25% annually, surpassing $34 billion worldwide by 2024.
Several trends are fueling adoption across industries:
Advances in Materials
New 3D printable photopolymers, composites, flexible filament, and metal alloys are expanding capabilities for high-performance parts production.
Hybrid Manufacturing
Combining 3D printing with machining, robotics, and other processes in a single platform increases automation.
Mass Customization
Agile 3D printing enables custom end-products at scale versus just prototyping.
Metals Growth
Demand for metal 3D printing is increasing over 50% yearly across aerospace, dental, medical sectors.
Distributed Manufacturing
3D printing facilities located closer to point-of-use reduce logistics costs and environmental impact.
Additive manufacturing will transform design, prototyping, production, and business models across manufacturing, healthcare, consumer goods, and construction industries in the coming decade.
Key Takeaways and Summary
The major takeaways from this overview of 3D printing technologies:
- Numerous 3D printing processes exist, each with unique capabilities
- Selecting the optimal method depends on factors like target material, accuracy, part size, production quantities etc.
- FDM is the most affordable and FFF the most used technology
- SLA offers excellent surface finish and fine details
- SLS enables functional prototypes with good properties
- MJF combines speed and quality for short-run production
- EBM and DED are used to 3D print large metal parts
- Hybrid manufacturing leverages 3D printing with other processes for maximum flexibility
- Advances in materials and methods will continue expanding applications
In summary, understanding the principles behind each additive manufacturing technology allows identifying the best process for a given product requirement. Prototyping key options provides further validation to minimize risk. With its versatility, productivity and waste reduction potential, 3D printing promises to be a key manufacturing technology well into the future across industries.
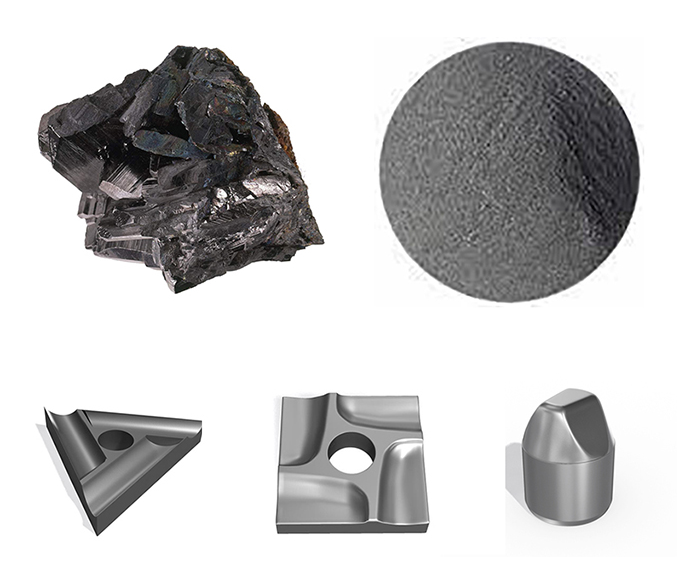
FAQ
Here are answers to some common questions about 3D printing technologies:
Q: Which 3D printing technology is the cheapest?
A: Fused deposition modeling (FDM) is the most affordable 3D printing technology. Both the equipment and material costs are lowest for FDM using common thermoplastics like PLA and ABS.
Q: Which 3D printing method has the best accuracy?
A: Stereolithography (SLA) offers the highest accuracy of all the common 3D printing technologies, ranging from 25 to 100 microns for most photopolymers. This makes it ideal for applications requiring tight tolerances.
Q: What 3D printing process allows multi-color prints?
A: Powder bed fusion methods like full color binder jetting and multi jet fusion (MJF) support multicolor prints by precisely controlling material deposition. Thermoplastic extrusion methods like FDM also enable color mixing with multiple print heads.
Q: Which metals can be 3D printed?
A: Titanium alloys, stainless steel, cobalt chrome, aluminum, nickel alloys are the most common metals that can be 3D printed using powder bed or directed energy deposition methods.
Q: What 3D printing method is best for fabrics or flexible material?
A: Fused deposition modeling using flexible TPU filament is the most straightforward way to 3D print flexible material with elastic properties similar to fabrics and rubber. SLS printing can also produce flexible parts by using powdered polyurethane material.
Q: How big can a 3D printed part be?
A: Large format 3D printers for construction can produce parts over 50 feet long. However, for most industrial systems, the maximum part size range is:
- SLS: 15 x 13 x 18 inches
- SLA: 1 cubic foot
- FDM: 12 x 12 x 12 inches
- DED: Virtually unlimited size
Q: Which 3D printing process is the fastest?
A: In terms of build speed, Multi Jet Fusion by HP can achieve speeds up to 10-100x faster than SLS and SLA processes. DED methods also have high deposition rates up to 0.5 kg/hour, but require more passes to build a full part.
Q: What 3D printing methods are used for mass production?
A: Binder jetting and material jetting are most suitable for scaled production. FDM, SLS and MJF are viable for short-run manufacturing up to 10,000’s of units. DED enables large volumes of metal parts.
Q: How accurate is metal 3D printing?
A: Powder bed fusion of metals can achieve accuracy around 50-100 microns while machining and finishing can further enhance precision. Cold spray DED has lower accuracy around 200 microns.