Tungsten cobalt powder, also known as tungsten cobalt alloys or WC-Co, refer to a composite material made by combining tungsten carbide (WC) powder with metallic cobalt binder powder. This powder metallurgy product is a popular cemented carbide material appreciated for its unique combination of hardness, toughness and thermal/wear resistance properties.
Tungsten Cobalt Powder Types
Tungsten cobalt powder is available in different compositions, sizes, shapes and grades to suit various applications and processing methods.
Type | Description |
---|---|
Composition | Typically contains 84-97% WC by weight blended with 3-16% cobalt. Ratio adjusted to optimize hardness, strength, durability and other properties. |
Particle shape | Round/spherical powder flows better for uniform die filling. Angular and crushed powders provide better compact strength. |
Particle size | Submicron nanostructured powder up to coarse particles of 100+ microns based on final part size and details. |
Grades | Multiple quality grades based on purity, particle size distribution, shape, residual carbides and other parameters. Higher grades used for more demanding applications. |
Tungsten Cobalt Processing Methods
WC-Co powder undergoes various consolidation techniques to create finished components and parts:
- Press and sinter powder metallurgy
- Metal injection molding
- Additive manufacturing like binder jetting, laser/electron beam powder bed fusion
- Thermal spray coatings
- Cold/warm compaction and roll pressing
- Cladding, brazing, welding
Suitability depends on factors like material grade, final part size, complexity, performance requirements and production volumes.
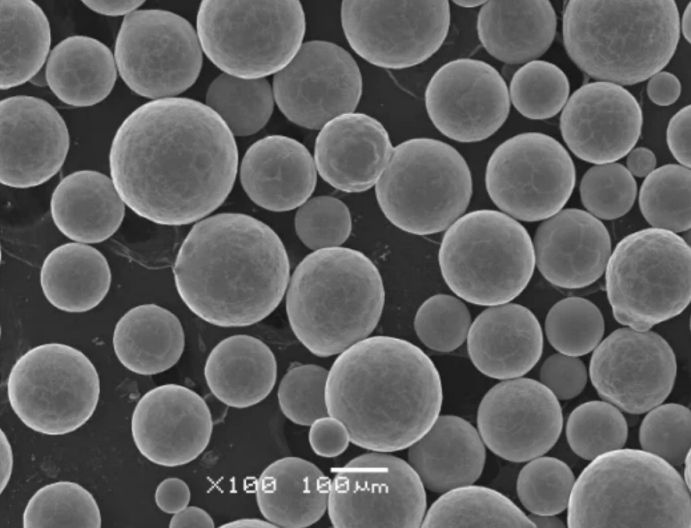
Tungsten Cobalt Composition
Tungsten cobalt powder contains two main components – tungsten carbide and cobalt. Other elements may be present based on application needs.
Constituent | Function | Weight % |
---|---|---|
Tungsten carbide (WC) | Provides extreme hardness, strength and wear resistance | 84-97% typical |
Cobalt (Co) | Ductile metallic binder that holds carbides together | 3-16% typical |
Tantalum, Titanium, Niobium carbides | Adds corrosion resistance for specific applications | Up to 5% optionally |
Vanadium carbide | Grain growth inhibitor during heat treatment | Up to 2% optionally |
Role of Cobalt
The cobalt binder phase serves critical functions in tungsten carbide hardmetals:
- Holds WC grains together in a tough, metallic matrix
- Provides fracture toughness and shock resistance to brittle WC particles
- Allows deformation and supports load sharing
- Enables heat treatment to improve strength
- Determines magnetic properties
Higher cobalt concentrations generally improve strength and ease of fabrication while reducing hardness. The WC-Co ratio directly influences physical, mechanical, electrical and magnetic characteristics.
Tungsten Cobalt Properties
Key properties of tungsten carbide cobalt hard metals include:
Property | Performance |
---|---|
Hardness | Up to 1500 HV or 90 HRA, among the hardest industrial materials |
Wear resistance | Highly resistant to abrasive and erosive wear |
Toughness | Up to 30 MPa√m crack propagation resistance |
High temperature strength | Can operate up to 1000°C for limited times |
Corrosion resistance | Fairly inert but specific grades offer better performance |
Thermal conductivity | Up to 100 W/mK for heat removal |
Electrical conductivity | Ranges from semi-conductive to near metallic based on grade |
Coefficient of thermal expansion | Similar to steel at ~5-7 x 10<sup>-6</sup> K<sup>-1</sup> |
Density | 11-15 g/cc, heavier than titanium alloys |
Magnetic properties | Determined by WC-Co ratio, critical for some segments |
The unique balance of hardness, wear performance and fracture toughness makes cemented carbides ideal to withstand extreme pressures, temps, impacts, friction and corrosive environments. Properties are fine tuned based on composition and processing parameters selected according to the specific application and service conditions.
Tungsten Cobalt Applications
Thanks to their exceptional hardness and wear properties combined with strength and thermal resistance, tungsten carbide cobalt materials enjoy extremely broad industrial usage across the following segments:
Industry | Common Applications |
---|---|
Mining | Drilling tools and bits, rock drilling inserts and teeth, screening media |
Oil & gas | Downhole tools, wireline tools, frac balls, sleeves, well perforating |
Construction | Road milling and planning tools, trenching tools, circular saws |
Metalworking | Turning inserts, cold forming dies, rotary burrs, slitters, roller scales |
Woodworking | Cutting tools, circular saws, chippers, planer and jointer knives |
Automotive | Fuel injection nozzle holder, valves and seats |
Aerospace | Wire drawing dies, extrusion dies, swaging tools |
Electronics | Semiconductor wafer dicing blades |
Medical & dental | Surgical blades and drill bits |
Food processing | Meat chopper plates, extrusion dies |
The unique properties of tungsten carbide cobalt enables it to outperform conventional tool steels, stainless steels and other competing materials under extreme service conditions.
Tungsten Cobalt Powder Specifications
Tungsten carbide cobalt powder for press and sinter meets various international specifications:
Standard | Description |
---|---|
ISO 2768 | Geometrical tolerances for cemented carbide powders |
ISO 4499 | Methods for measurement of grain size of cemented carbide |
ASTM B771 | Standard for copper-tungsten carbide powder for injection molding |
JIS R 1601 | Classification of cemented carbide powders |
Key powder metrics along with typical values as per ISO 2768:
Parameter | Typical Range |
---|---|
Particle size | 0.2 to 120 microns |
Particle shape | Round, angular or crushed |
Apparent density | 3-8 g/cc |
Tap density | 4-12 g/cc |
Specific surface area | 0.1 to 20 m<sup>2</sup>/g |
Solid solution content | Up to 5% optionally |
Residual carbon | 0.1% max |
Residual oxygen | 0.6% max |
Manufacturers provide detailed TDS and COA specifying chemical composition, physical characteristics and inspection criteria for each powder grade tailored for target applications. Custom blends are offered for unique needs.
Tungsten Carbide vs. Cobalt Hardmetals
Key differences when comparing standard tungsten carbide grades versus cobalt-rich hardmetal powders:
Parameter | Tungsten Carbide | Cobalt Hardmetal |
---|---|---|
Composition | 94-97% WC with 3-6% Co | 84-90% WC with 10-16% Co |
Hardness | Up to 92 HRA (>1500 HV) | Up to 62 HRA (~700 HV) |
Toughness | Higher risk of brittle fracture | Up to 30 MPa√m crack propagation resistance |
Strength | 2,000 to 3,000 MPa transverse rupture strength | 4,500 to 5,500 MPa transverse rupture strength |
Wear resistance | Extreme abrasion and erosion resistance | Lower but still excellent wear performance |
Corrosion resistance | Prone to oxidation and chemical attack if unprotected by binder | Better corrosion protection from thicker cobalt layer |
Magnetic response | Slightly magnetic from trace cobalt binder | Ferromagnetic due to higher cobalt content |
Tradeoffs
Increasing cobalt content improves toughness and corrosion resistance while reducing hardness and wear performance. Choose grade based on most critical property needed – extreme hardness vs. strength and durability.
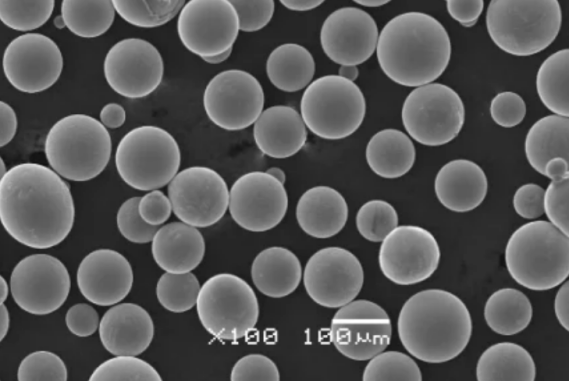
Tungsten Carbide vs. Tungsten Carbide Cobalt
It is important to distinguish between tungsten carbide powder (pure WC without cobalt binder) and tungsten carbide cobalt (composite WC+Co powder).
Metric | Tungsten Carbide | Tungsten Carbide Cobalt |
---|---|---|
Constituents | Pure tungsten carbide without cobalt | Intimate WC+Co powder mixture |
Hardness | Extremely high hardness, very brittle | Reduction in hardness offset by cobalt toughening |
Applications | Limited usage in pure WC form without binder | Most commercial uses require cobalt as binder |
Processing | Challenging to sinter pure WC powder | Easier consolidation with cobalt to strengthen product |
Price | Less expensive as just a single component | Higher cost due to cobalt content |
Availability | Less commonly used | Very widely available |
Thus tungsten carbide cobalt powders are more versatile and applicable to the majority of hardmetal part production use cases.
Grades of Tungsten Cobalt Powder
Tungsten carbide cobalt powder is commercially available in a wide range of standardized compositions and grades to meet performance needs:
Grade | Description | Applications |
---|---|---|
Micrograin | Very fine <1 micron powder for smaller, complex components | Miniature tooling, electronics |
Submicron | Just under 1 micron particles with moderate surface area | Indexable inserts, drawing dies |
Ultrafine | ~1-5 micron powder for improved properties | Cutting tools, mining picks |
Fine | Medium sized 5-10 micron particles for better flow and packing | Metal removal tools, wear parts |
Standard | General purpose 10-30 micron powder | Construction, woodworking, forming tools |
Medium/coarse | Larger >30 micron particles with higher toughness | Mining, oil and gas, large parts |
Higher grade designations denote superior quality with tighter control on critical powder metrics like particle size distribution, shape, purity levels, oxygen/carbon content and microstructure.
Premium powders improve sintered density, performance consistency and reliability in finished cemented carbide components. However, cost also increases substantially for finer, purer tungsten cobalt grades optimized for advanced applications.
Cost Analysis of Tungsten Cobalt Powder
Pricing varies based on composition, grade, order volumes and market conditions:
Powder Grade | Average Price Range |
---|---|
Standard commercial 10-30 micron | $27 to $37 per pound |
Fine grain submicron 1-5 micron | $45 to $55 per pound |
High purity ultrafine <1 micron | $90 to $110 per pound |
Special binder enriched or cobalt grades | $80 to $250+ per pound |
- Tungsten price volatility directly affects powder costs
- Higher purity medical and aerospace grades command premium pricing
- Bulk orders in thousands of pounds offer significant cost savings
With rising energy, raw material and transport costs, tungsten carbide cobalt powder prices have faced upward pressure but are expected to stabilize as markets balance supply and demand. Consider total life cycle cost analysis for decision making, as higher perfomance grades can provide superior productivity and durability translating to lower $/part costs.
FAQs
What is cemented carbide?
Cemented carbide refers to a composite material made by mixing carbide particles with a binder phase, typically cobalt. Tungsten carbide cobalt (also called tungsten cobalt, WC-Co or carbide cobalt) made using tungsten carbide powder as the carbide constituent is an extremely popular type of cemented carbide thanks to its unique properties.
What are the different tungsten carbide grades?
Tungsten carbide powder itself is available in different grades based on purity, particle size, carbon/oxygen content and other metrics. Common tungsten carbide powder designations include micrograin, submicron, fine, standard and coarse particle sizes. Additionally, cemented carbides are differentiated by composition – a higher cobalt content makes it a cobalt-rich grade with improved strength and toughness compared to standard grades optimizing hardness and wear performance. Special grades may also incorporate other carbides like tantalum, titanium or niobium carbides.
How to make tungsten carbide parts?
The preferred consolidation process to make finished tungsten carbide cobalt components involves press and sinter powder metallurgy:
- Weigh out appropriate quantities of WC and Co powders
- Ball milling to intimately mix and homogenize
- Compact into “green” parts using dies and applying pressure
- Debind and presinter parts to impart handling strength
- High temperature sintering just below cobalt melting point
- Additional heat treatments can further enhance properties
The flexibility of powder metallurgy coupled with outstanding carbide properties makes this technique extremely popular for commercial scale manufacturing.
What color is tungsten carbide?
In powder form, tungsten carbide cobalt typically exhibits a dark grey color. Final appearance varies based on composition – pure tungsten carbide without cobalt may appear light grey. Higher cobalt content imparts a more metallic color. Fully sintered tungsten carbide parts reflect differences in starting powder ratio. Overall, some shade of grey is the most representative color.
Is tungsten carbide magnetic?
Tungsten carbide itself is non-magnetic. However, magnetic response is determined by cobalt binder percentage in WC-Co alloys. Grades with 6% or less cobalt generally only exhibit weak magnetic attraction. Cobalt-rich compositions with over 10% Co become ferromagnetic. This facilitates magnetic separation techniques to recover worn and spent cemented carbide components for recycling.
Is tungsten carbide hazardous?
Like most industrial powders, certain health and safety precautions apply when handling tungsten carbide cobalt:
- Dust inhalation must be avoided
- Ensure adequate ventilation is available
- Wear PPE – masks, gloves, goggles as needed
- Prevent skin contact or ingestion
- Review SDS to manage risks appropriately
In solid form, tungsten carbide itself is relatively inert and not considered toxic. However the typical cobalt binder may cause skin or respiratory sensitization for some individuals. Overall, cemented carbides don’t pose significant health hazards if handled carefully per guidelines.
Conclusion
With its extreme hardness coupled with strength, toughness and wear performance, tungsten carbide cobalt has become the workhorse cemented carbide for metalworking, mining, construction, energy and numerous industrial applications. Customizing the WC and Co powder composition and consolidation process enables tailored property profiles. Component reliability, consistency and tool life all depend on the quality and grade of tungsten cobalt powder selected as feedstock. As pioneers continue to push performance boundaries, advances in cemented carbides will support future breakthroughs across a diverse range of cutting edge technologies.