Imagine a material that’s incredibly strong yet surprisingly lightweight, corrosion-resistant yet biocompatible. That’s the magic of titanium-based alloy powders, a revolutionary material transforming industries from aerospace to medicine.
These fine, metallic powders, produced through processes like gas or plasma atomization, are like tiny building blocks, ready to be shaped into complex, high-performance components through additive manufacturing (3D printing). Let’s delve deeper into the world of titanium alloy powders, exploring their diverse applications, specific examples, and the immense potential they hold.
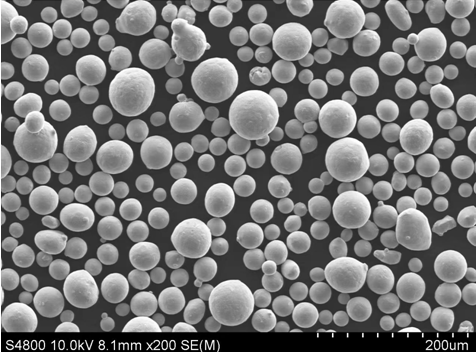
Properties and Composition of Titanium-Based Alloy Powder
Titanium alloys are renowned for their exceptional properties:
- High Strength-to-Weight Ratio: Imagine lifting a car with ease! Titanium boasts exceptional strength while remaining remarkably lightweight, making it ideal for applications demanding both.
- Superior Corrosion Resistance: Titanium stands strong against harsh environments, resisting rust and degradation, perfect for marine and chemical applications.
- Biocompatibility: The human body readily accepts titanium, making it a valuable material for medical implants and prosthetics.
- High-Temperature Performance: Titanium alloys can withstand extreme heat, a crucial feature for parts in jet engines and power plants.
These remarkable properties stem from the unique blend of elements in titanium alloys. Here’s a glimpse into some of the most common types:
Alloy | Composition (wt%) | Key Characteristics |
---|---|---|
Ti-6Al-4V (Grade 5)** | 6% Aluminum, 4% Vanadium | The workhorse of titanium alloys, offering excellent strength, ductility, and fabricability. |
Ti-6Al-4V (Grade 23)** | 6% Aluminum, 4% Vanadium (Extra Low Interstitials) | A superior version of Grade 5 with even lower oxygen and nitrogen content, enhancing ductility and weldability. |
Ti-6Al-2Sn-4Zr-2Mo (TA19)** | 6% Aluminum, 2% Tin, 4% Zirconium, 2% Molybdenum | Offers high strength, good creep resistance at elevated temperatures, and excellent fatigue strength. |
Ti-10V-2Fe-3Al (Ti-1023)** | 10% Vanadium, 2% Iron, 3% Aluminum | Known for its exceptional strength and high-temperature performance, making it ideal for aerospace applications. |
CP Titanium (Commercially Pure)** | Over 99% Titanium | Offers superior ductility and formability, making it suitable for applications requiring complex shapes. |
the Applications of Titanium-Based Alloy Powder
The versatility of titanium alloy powders is truly awe-inspiring. Here’s a spotlight on some of their most impactful applications:
The application of titanium based alloy powder in aerospace:
- Aircraft Components: From lightweight airframes to high-strength landing gear components, titanium alloys, thanks to their strength-to-weight ratio, are revolutionizing aircraft design, leading to more fuel-efficient planes.
- Jet Engine Parts: Titanium’s ability to withstand extreme temperatures makes it ideal for jet engine components like compressor blades and housings, contributing to improved engine performance and efficiency.
The application of titanium based alloy powder in energy and chemical industry:
- Desalination Plants: Titanium’s exceptional corrosion resistance is crucial for components in desalination plants that come into contact with seawater, ensuring long-lasting operation.
- Chemical Processing Equipment: Reactors and vessels used in harsh chemical environments can benefit from titanium’s resistance to corrosion, minimizing downtime and maintenance costs.
The application of titanium based alloy powder in medical devices:
- Joint Replacements: Knee and hip replacements made from titanium alloys are biocompatible, long-lasting, and can significantly improve patients’ quality of life.
- Dental Implants: Offering excellent biocompatibility and osseointegration (fusion with bone), titanium dental implants provide a strong and natural-looking solution for missing teeth.
The application of titanium based alloy powder in metallurgy:
- Additive Manufacturing of Complex Parts: The intricate geometries achievable with 3D printing unlock possibilities for creating lightweight, high-performance parts for various industries, from aerospace to automotive.
- Rapid Prototyping: The ability to quickly create prototypes using titanium alloy powders allows engineers to iterate on designs faster, accelerating the development process.
The application of titanium based alloy powder in civilian use:
- High-Performance Sporting Goods: From golf clubs to bicycles, titanium alloy components can reduce weight, improve strength, and enhance performance for athletes.
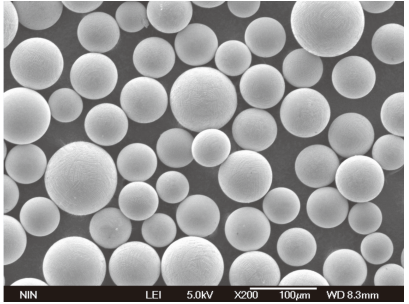
Specific Titanium-Based Alloy Powder
The world of titanium alloy powders boasts a diverse range of options, each catering to specific needs. Here are ten noteworthy examples:
- AM3D Ti-6Al-4V (Grade 23): This extra-low interstitial version of the workhorse Ti-6Al-4V shines with its enhanced ductility and weldability. Perfect for applications demanding intricate geometries and reliable welding, it’s a favorite in the aerospace and medical device industries.
- LPW Ti-6Al-4V (Grade 23): Optimized for laser powder bed fusion (LPBF) additive manufacturing, this variant of Grade 23 titanium alloy powder boasts excellent flowability and packing density, ensuring high-quality printed parts. Its focus on printability makes it ideal for creating complex, near-net-shape components.
- EOS Titanium Ti64 (Grade 23): Developed specifically for the EOS additive manufacturing platform, this powder offers exceptional control over mechanical properties and microstructure in the final printed part. This tailored approach caters to applications where precise performance is paramount.
- ATI Ti-6Al-4V ELI (Extra Low Interstitials): Meeting stringent medical device standards, this ELI (Extra Low Interstitials) grade prioritizes biocompatibility and purity. It’s the go-to choice for implants and prosthetics requiring excellent tissue acceptance and long-term functionality within the body.
- Alpha Titanium AT3 (CP Titanium): For applications demanding superior formability and ductility, commercially pure (CP) titanium powders like AT3 take center stage. Their ease of shaping allows for the creation of complex components like medical device housings and intricate aerospace parts.
- Arcam Ti6Al4V: Optimized for the Arcam Electron Beam Melting (EBM) additive manufacturing process, this powder ensures exceptional surface quality and fatigue strength in the final parts. This makes it ideal for high-stress applications in the aerospace and automotive industries.
- SLM Solutions Ti-6Al-4V (Grade 23): Tailored for the SLM Solutions selective laser melting platform, this powder offers excellent printability and control over microstructure. This targeted approach allows for the creation of high-performance parts with predictable mechanical properties.
- Renishaw Ti 6Al-4V (Grade 23): Formulated specifically for Renishaw’s additive manufacturing systems, this powder prioritizes consistent flowability and high packing density. This focus on printability ensures reliable printing and the creation of high-quality components.
- Carpenter (Ti Powder): Reaching a global audience, Carpenter offers its titanium powder range, including CP Titanium and Ti-6Al-4V options. This caters to the growing demand for these versatile powders across various industries worldwide.
- French Powder Industries (FPI) TA6V: This French manufacturer offers a range of titanium alloy powders, including the popular TA6V (Ti-6Al-4V) variant. FPI caters to diverse applications with its selection of powders boasting high quality and consistent performance.
the Pros and Cons of Titanium-Based Alloy Powder
While titanium alloy powders offer a multitude of advantages, it’s important to consider their limitations:
Pros:
- Exceptional Strength-to-Weight Ratio: Components made from titanium alloy powders are incredibly strong yet remarkably lightweight, leading to significant performance improvements in various industries.
- Superior Corrosion Resistance: Titanium’s natural resistance to rust and degradation makes it ideal for applications in harsh environments, like marine and chemical settings.
- Biocompatibility: The human body readily accepts titanium, making it a valuable material for medical implants and prosthetics, promoting long-term functionality.
- High-Temperature Performance: Certain titanium alloys can withstand extreme heat, making them crucial for components in jet engines and power plants, ensuring reliable operation under demanding conditions.
- Design Freedom with Additive Manufacturing: The ability to 3D print intricate geometries with titanium alloy powders unlocks possibilities for creating complex, high-performance parts that were previously difficult or impossible to manufacture.
Cons:
- Higher Cost: Compared to traditional materials like steel or aluminum, titanium alloy powders can be more expensive. However, the weight savings and performance gains often justify the initial investment.
- Process Complexity: Additive manufacturing with titanium alloy powders requires specialized equipment and expertise, adding complexity to the production process.
- Limited Surface Finish: 3D printed components made from titanium alloy powders may require additional post-processing steps to achieve a desired surface finish.
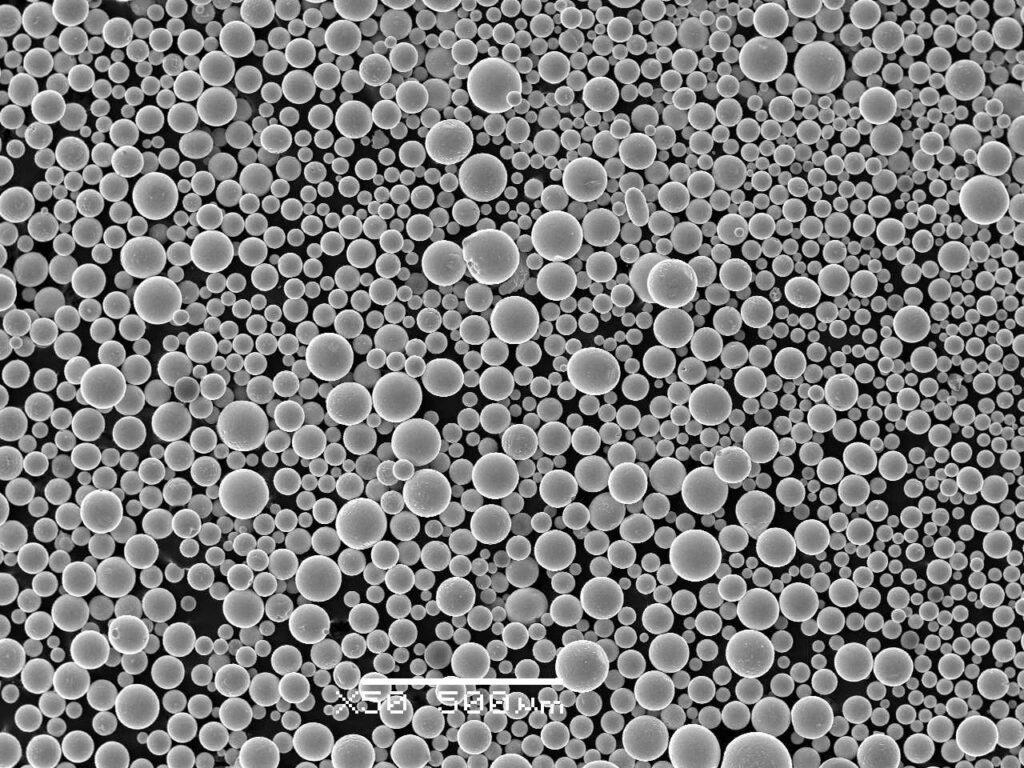
Selecting Titanium-Based Alloy Powder
Given the diverse range of titanium alloy powders available, selecting the right one for your application requires careful consideration of several factors:
- Intended Application: The specific use case will heavily influence the choice of powder. For instance, applications demanding high strength and heat resistance, like jet engine components, might favor Ti-6Al-4V ELI or Ti-10V-2Fe-3Al powders. Conversely, medical implants prioritizing biocompatibility and formability might benefit from CP titanium or ATI Ti-6Al-4V ELI options.
- Additive Manufacturing Process: Different 3D printing techniques have varying powder requirements. For instance, LPBF (laser powder bed fusion) favors powders with good flowability and packing density, while EBM (Electron Beam Melting) might prioritize powders with high thermal conductivity. Consider the specific capabilities of your chosen additive manufacturing system.
- Mechanical Properties: The desired mechanical properties of the final part, such as strength, ductility, and fatigue resistance, will guide your powder selection. Data sheets provided by manufacturers will detail the mechanical properties achievable with each powder type.
- Powder Characteristics: Factors like particle size distribution, flowability, and oxygen content can impact printability and the final part’s quality. Powders with a consistent particle size distribution and good flowability generally ensure smoother printing and better surface finishes. Lower oxygen content often translates to improved ductility and weldability.
- Cost: While titanium alloy powders offer exceptional performance, they can be more expensive than traditional materials. Consider the cost of the powder itself, alongside factors like processing complexity and potential post-processing requirements, to determine the overall cost-effectiveness for your application.
- Supplier Reputation: Choosing a reputable supplier with a proven track record of quality and consistency is crucial. Reliable suppliers offer detailed specifications, data sheets, and can provide technical support to ensure successful printing with their powders.
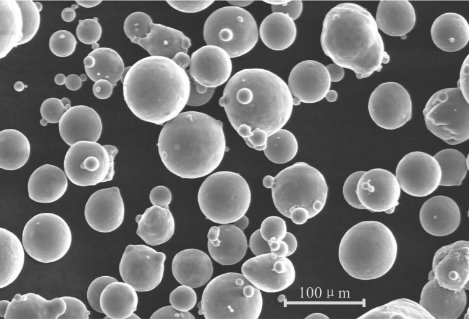
FAQ
Q: Are titanium alloy powders safe to handle?
A: While titanium itself is not considered hazardous, fine metallic powders can pose inhalation risks. Proper safety protocols, including using appropriate personal protective equipment (PPE) like respirators and working in well-ventilated environments, are essential when handling titanium alloy powders.
Q: How strong are titanium alloy powders compared to other materials?
A: Titanium alloys offer an exceptional strength-to-weight ratio. For their weight, they can be significantly stronger than steel or aluminum, making them ideal for applications demanding high strength without excessive weight.
Q: Can titanium alloy powders be recycled?
A: Yes, titanium alloy powders can be recycled back into usable feedstock for additive manufacturing. This not only reduces waste but also promotes sustainability within the production process.
Q: What are the future prospects for titanium alloy powders?
A: The future of titanium alloy powders is bright. Advancements in additive manufacturing technology, coupled with the development of new and more affordable powder options, are expected to drive wider adoption across various industries. From aerospace and medicine to consumer goods and sustainable manufacturing, titanium alloy powders hold immense potential for revolutionizing product design and performance.
In conclusion, titanium-based alloy powders represent a transformative material reshaping industries. Their unique blend of strength, weight, corrosion resistance, and biocompatibility opens doors for creating high-performance parts and components. As additive manufacturing technology continues to evolve, and the selection of available powders expands, the potential applications of titanium alloy powders are truly limitless.