Imagine a material that’s as strong as steel, yet lighter than aluminum. A metal that can withstand scorching temperatures and shrug off corrosive environments. That’s the magic of titanium-based alloy powders, and their development is revolutionizing industries from aerospace to medicine.
In this comprehensive guide, we’ll delve into the exciting world of these futuristic materials. We’ll explore the latest trends in their development, unpack their properties, and showcase the diverse applications they’re powering. Buckle up, and get ready to be amazed by the potential of titanium-based alloy powders!
Improvement of Preparation Technology for Titanium-Based Alloy Powder
The exceptional properties of titanium-based alloy powders hinge on their meticulous preparation. Traditional methods like electron beam melting (EBM) and plasma atomization (PA) have laid the groundwork. However, the quest for even better powders is driving innovation in several key areas:
- Powder morphology control: Imagine having complete control over the shape and size of each tiny powder particle. This is the dream of advanced techniques like gas atomization, which can produce spherical powders with excellent flowability and packing density. This translates to superior printing performance in additive manufacturing (AM) processes like 3D printing.
- Reduced oxygen content: Oxygen is a bit of a party crasher in the titanium world. Even small amounts can negatively impact the mechanical properties of the final product. New techniques like vacuum plasma atomization (VPA) and argon gas atomization minimize oxygen contamination, leading to stronger and more reliable components.
- Alloying element control: Just like adding spices to a dish, incorporating specific elements into the titanium base alloy can dramatically alter its properties. Advanced methods like pre-alloyed powder manufacturing allow for precise control over the addition of elements like aluminum, vanadium, or molybdenum. This enables the creation of powders with tailored properties for specific applications.
Here’s a table summarizing the key advancements in preparation technology:
Technology | Advantages | Disadvantages |
---|---|---|
Gas Atomization | Spherical powders, excellent flowability, improved packing density | Higher production costs compared to traditional methods |
Vacuum Plasma Atomization (VPA) | Reduced oxygen content, improved mechanical properties | Complex process setup |
Argon Gas Atomization | Reduced oxygen content, improved mechanical properties | Limited availability compared to VPA |
Pre-alloyed Powder Manufacturing | Precise control over alloying elements, tailored properties | Requires specialized equipment and expertise |
Food for Thought: Think of a car. Traditional titanium powders might be like building a car with generic parts, while advanced preparation techniques empower engineers to create a high-performance race car with custom-designed components.
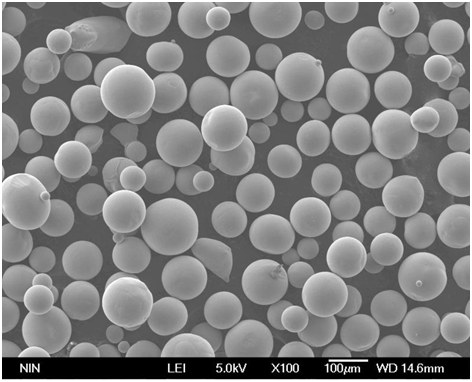
The Application of Titanium-Based Alloy Powder
The applications of titanium-based alloy powders are as diverse as they are impressive. Here are just a few examples:
- Aerospace: The relentless pursuit of lightweight, high-strength materials makes titanium alloys a perfect fit for the aerospace industry. Components like aircraft landing gear, engine parts, and airframes can be lighter and stronger thanks to 3D printing with titanium powders. This translates to improved fuel efficiency, increased payload capacity, and ultimately, a greener and more sustainable air travel experience.
- Biomedical: Imagine a bone implant that seamlessly integrates with your body. This dream becomes a reality with biocompatible titanium alloys. Surgeons can now use 3D-printed implants made from titanium powders to replace damaged bones, joints, and even entire sections of the skull. The biocompatibility and excellent osseointegration (bone bonding) properties of titanium make it a life-changing material for the medical field.
- Automotive: The race for lighter, more fuel-efficient vehicles is on, and titanium alloy powders are playing a crucial role. Components like connecting rods, suspension parts, and even some engine components can be lighter and stronger when made with these advanced powders. This translates to better fuel economy, improved handling, and potentially, a lighter environmental footprint.
- Consumer Goods: From high-end sporting goods like golf clubs and bicycle frames to luxury watches and even designer jewelry, the applications of titanium alloy powders are expanding into the consumer realm. The combination of strength, lightness, and aesthetics makes these powders a compelling choice for manufacturers seeking to create premium products.
Here’s a table showcasing some key applications of titanium-based alloy powders:
Industry | Application Examples | Benefits |
---|---|---|
Aerospace | Aircraft landing gear, engine parts, airframes | Lighter weight, improved fuel efficiency, increased payload capacity |
Biomedical | Bone implants, joint replacements, skull implants | Biocompatible, excellent osseointegration, long-lasting performance |
Automotive | Connecting rods, suspension parts, engine components | Lighter weight, improved fuel economy, better handling |
Consumer Goods | Sporting |
Properties and Characteristics of Titanium-Based Alloy Powders
The magic of titanium-based alloy powders lies in their unique blend of properties. Here’s a closer look at what makes these powders so special:
- High Strength-to-Weight Ratio: Titanium boasts an exceptional strength-to-weight ratio, meaning it’s incredibly strong for its weight. This makes it a dream material for applications where weight reduction is paramount, like aerospace and automotive industries.
- Excellent Corrosion Resistance: Titanium naturally resists corrosion, making it ideal for harsh environments like seawater or the human body. This property is particularly valuable in biomedical applications where long-lasting implants are crucial.
- Biocompatibility: Certain titanium alloys are biocompatible, meaning they can coexist peacefully with the human body without causing adverse reactions. This characteristic makes them perfect for medical implants that integrate seamlessly with bone and tissue.
- High Melting Point: Titanium has a very high melting point, allowing it to withstand extreme temperatures. This makes it a valuable material for applications like jet engines and other high-heat environments.
- Powder Specific Properties: The preparation method and specific alloying elements significantly influence the properties of the final powder. For example, gas-atomized powders might offer superior flowability for 3D printing, while VPA powders might boast lower oxygen content for improved mechanical strength.
Here’s a table outlining the key properties and characteristics of titanium-based alloy powders:
Property | Description | Importance |
---|---|---|
High Strength-to-Weight Ratio | Strong for its weight | Enables weight reduction in critical applications |
Excellent Corrosion Resistance | Resists rust and degradation | Ideal for harsh environments and medical implants |
Biocompatibility | Compatible with the human body | Crucial for long-lasting medical implants |
High Melting Point | Withstands extreme temperatures | Valuable for high-heat applications |
Powder Specific Properties | Flowability, oxygen content, etc. | Impact performance in different applications |
Analogy Alert! Imagine titanium powder as a tiny, super-strong, and versatile building block. The way you arrange and modify these blocks determines the final product’s properties, just like using different colored Lego bricks can create spaceships or houses.
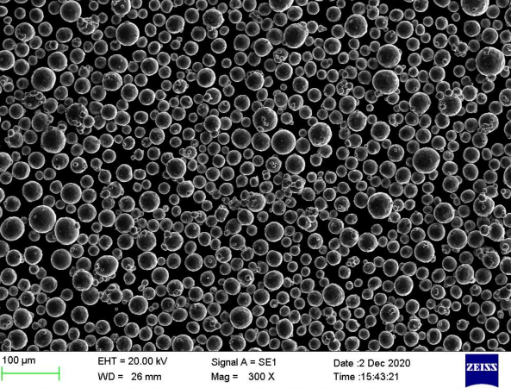
Specifications, Sizes, Grades, and Standards
When it comes to titanium-based alloy powders, there’s a world of options to choose from. Here’s a breakdown of the key specifications to consider:
- Particle Size: The size of the powder particles significantly impacts the printing process and final product properties. Powders can range in size from very fine (less than 25 microns) to coarser particles (over 100 microns). Finer powders generally offer better surface finish but can be more challenging to print due to flowability issues.
- Powder Grade: Titanium alloy powders are available in various grades, each with a specific chemical composition and mechanical properties. Common grades include Ti-6Al-4V (known for its excellent balance of strength and ductility), Ti-6Al-4V ELI (an extra-low interstitial grade with even lower oxygen content), and Gr-2 (a commercially pure titanium powder with good formability).
- Standards: To ensure quality and consistency, titanium alloy powders adhere to various industry standards. These standards set specifications for chemical composition, particle size distribution, flowability, and other critical parameters. Common standards include ASTM International (ASTM) and Aerospace Material Specifications (AMS).
Here’s a table summarizing the specifications, sizes, grades, and standards of titanium-based alloy powders:
Specification | Description | Example |
---|---|---|
Particle Size | Diameter of individual powder particles | < 25 microns (fine) |
100+ microns (coarse) | ||
Powder Grade | Chemical composition and mechanical properties | Ti-6Al-4V |
Ti-6Al-4V ELI | ||
Gr-2 | ||
Standards | Industry-set quality and consistency guidelines | ASTM International (ASTM) |
Aerospace Material Specifications (AMS) |
Decision Time! Choosing the right powder specification depends on the specific application. For instance, a high-performance jet engine component might require a finer powder with a specific grade like Ti-6Al-4V ELI, while a non-critical consumer good could utilize a coarser, commercially pure titanium powder (Gr-2).
Suppliers and Pricing of Titanium-Based Alloy Powders
The market for titanium-based alloy powders is experiencing significant growth, with several leading suppliers offering a diverse range of products. Here are some key players to consider:
- AM powders (continued): In addition to Ti-6Al-4V and Ti-6Al-4V ELI, they also offer specialty powders like titanium alloys with added elements for specific properties (e.g., higher temperature resistance).
- APEX Additive Manufacturing: This supplier focuses on high-performance metal powders for additive manufacturing. They offer titanium powders produced using various techniques like gas atomization and electron beam melting (EBM). Their product line includes titanium alloys tailored for aerospace, medical, and automotive applications.
- Höganäs AB: A global leader in metal powder manufacturing, Höganäs offers a comprehensive selection of titanium powders. Their portfolio includes gas-atomized and water-atomized powders, catering to diverse applications from 3D printing to metal injection molding (MIM).
- LPW Technology: This company specializes in metal powders specifically designed for laser powder bed fusion (LPBF) additive manufacturing. Their titanium powder offerings include LPBF-optimized grades with excellent flowability and packing density for superior printing performance.
Pricing: The pricing of titanium-based alloy powders can vary depending on several factors, including:
- Powder grade: High-performance grades like Ti-6Al-4V ELI typically command a premium compared to commercially pure grades (Gr-2).
- Particle size: Finer powders generally cost more due to the increased processing complexity.
- Quantity: Bulk purchases often come with discounted pricing compared to smaller orders.
- Supplier: Different suppliers may have varying pricing structures based on their production costs and market positioning.
Here’s a table providing a general overview of suppliers and pricing for titanium-based alloy powders (note that specific prices may vary depending on the factors mentioned above):
Supplier | Product Focus | Example Powders |
---|---|---|
AM powders | Wide variety of gas-atomized powders | Ti-6Al-4V, Ti-6Al-4V ELI, specialty titanium alloys |
APEX Additive Manufacturing | High-performance powders for AM | Gas-atomized and EBM titanium alloys |
Höganäs AB | Comprehensive selection of titanium powders | Gas-atomized and water-atomized powders |
LPW Technology | LPBF-optimized powders | Powders specifically designed for laser powder bed fusion |
Remember: It’s crucial to contact potential suppliers directly for the most up-to-date pricing information and to discuss your specific application requirements.
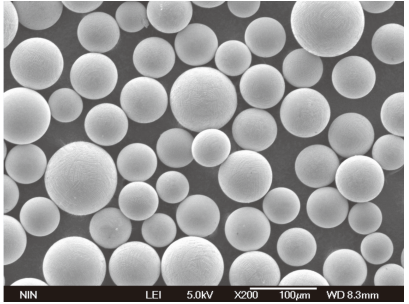
Advantages and Limitations of Titanium-Based Alloy Powders
While titanium-based alloy powders hold immense potential, it’s essential to consider both their advantages and limitations:
Advantages:
- Lightweight and Strong: The exceptional strength-to-weight ratio of titanium makes it ideal for applications demanding weight reduction without compromising performance.
- Excellent Corrosion Resistance: Titanium’s natural resistance to corrosion allows components to function flawlessly in harsh environments, expanding their applicability.
- Biocompatible Options: Specific titanium alloys offer biocompatibility, making them invaluable for medical implants that integrate seamlessly with the human body.
- Design Freedom: Additive manufacturing with titanium powders unlocks new possibilities for complex geometries and lightweight designs previously impossible with traditional manufacturing techniques.
- Reduced Waste: Compared to subtractive manufacturing methods, 3D printing with titanium powder minimizes material waste, promoting a more sustainable approach.
Limitations:
- Cost: Titanium powder production is a complex process, and the powders themselves can be expensive compared to some conventional materials.
- Process Challenges: Additive manufacturing with titanium powders requires specialized equipment and expertise, adding complexity to the production process.
- Surface Roughness: While improving, 3D-printed components using titanium powders might still exhibit a slightly rougher surface finish compared to traditionally machined parts.
- Limited Availability: Although the market is growing, certain high-performance or specialty titanium alloy powders might have limited availability compared to more common grades.
Making the Call: The decision to use titanium-based alloy powders hinges on a careful evaluation of both the advantages and limitations. For applications where weight reduction, corrosion resistance, or biocompatibility are paramount, the benefits may outweigh the higher cost and potential processing challenges.
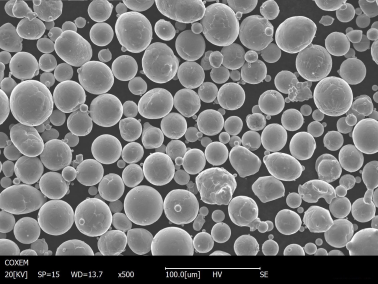
FAQ
Q: What are some of the common applications of titanium-based alloy powders?
A: Titanium alloy powders find use in various industries, including aerospace (aircraft components), biomedical (implants), automotive (lightweight parts), and even consumer goods (high-end sporting equipment).
Q: Are titanium-based alloy powders safe for use in medical implants?
A: Specific titanium alloys are biocompatible, meaning they are well-tolerated by the human body. This makes them ideal for medical implants like bone replacements, joint repairs, and even skull implants. However, it’s crucial to consult with a healthcare professional for personalized advice regarding the suitability of titanium implants for your specific needs.
Q: How strong are titanium-based alloy powders compared to other materials used in 3D printing?
A: Titanium alloys offer exceptional strength-to-weight ratios, making them significantly stronger than many commonly used 3D printing materials like plastics or even some aluminum alloys. However, the specific strength can vary depending on the chosen titanium alloy and its processing. When compared to high-strength steel powders used in 3D printing, titanium alloys might not be quite as strong in absolute terms, but their lighter weight often makes them the preferred choice for applications where weight reduction is critical.
Q: What are the environmental benefits of using titanium-based alloy powders?
A: Additive manufacturing with titanium powders can contribute to a more sustainable approach in several ways. Firstly, compared to traditional subtractive manufacturing techniques that remove material to create a final product, 3D printing with powders minimizes material waste. Secondly, the lightweight nature of titanium components made with these powders can lead to reduced fuel consumption in applications like aerospace and automotive, contributing to a lower environmental footprint.
Q: What’s the future outlook for titanium-based alloy powders?
A: The future of titanium-based alloy powders is bright. As advancements in preparation technology continue, we can expect even better powders with improved flowability, lower oxygen content, and potentially even the ability to create new alloys with tailored properties. Additionally, the development of more affordable and user-friendly additive manufacturing equipment will likely lead to a wider adoption of these powders across various industries. With ongoing research and development, titanium-based alloy powders have the potential to revolutionize how we design, manufacture, and utilize components in numerous fields.
In Conclusion
The world of titanium-based alloy powders is brimming with potential. From their exceptional properties to their ever-expanding applications, these futuristic materials are poised to transform various industries. As technology progresses and costs decrease, we can expect to see even more innovative and groundbreaking applications emerge. The future of manufacturing is undoubtedly lighter, stronger, and more versatile, thanks in no small part to the remarkable potential of titanium-based alloy powders.