With the rapid advancement of 3D printing technology, 3D printing consumables, especially 3D printing metal powder, are also developing rapidly. This includes the use of titanium powder and titanium alloy powder, titanium aluminum alloy powder, etc., which is particularly notable.
Spherical titanium alloy powder is the most widely used metal powder material in 3D printing. Therefore, this article will focus on several methods of preparing spherical titanium alloy powders and an outlook on future applications of it.
Titanium alloy has low density, high strength, good corrosion resistance, and high melting point, etc. It is one of the most commonly used metals for additive manufacturing technology, and it is widely used as structural parts in the fields of aviation, aerospace, automotive, and biotechnology.
Preparation of Titanium Alloy Powder
We also know that one of the main technologies in 3D printing, Selective Laser Melting (SLM), is suitable for the manufacture of small, precise, and complex parts. This technique needs a narrow particle size of titanium alloy powder and requires a high degree of sphericity, purity, and fluidity of the powder.
We can know that PREP equipment can produce titanium alloy powder with good sphericity, fluidity, and purity to meet the requirements of its usage after comparing several common powder preparation methods, such as Vacuum Inert Gas Atomization (VIGA), Electrode Induction Gas Atomization(EIGA), Plasma Rotating Electrode Process(PREP), Plasma Atomization(PA) and Plasma Spheroidization (PS).
The Plasma Rotating Electrode Process (PREP) is one of the most common methods for the preparation of spherical titanium alloy powders. The principle is to use a titanium alloy bar as a self-consuming electrode and to keep the electrode rotating at high speed while the plasma is used as a heat source to gradually melt the electrode.
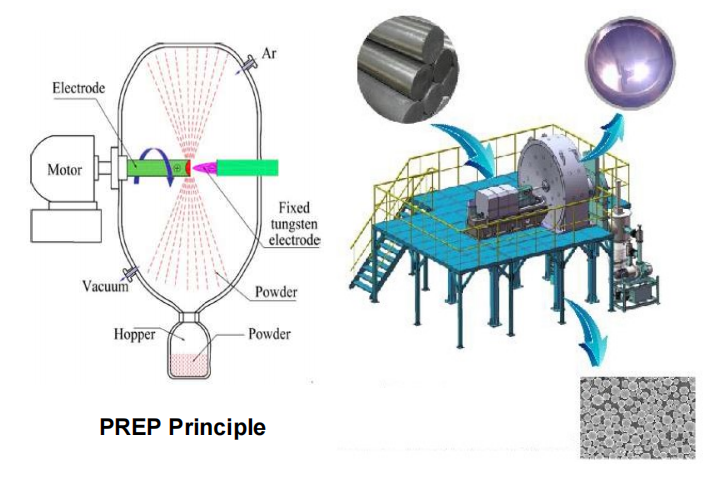
The conventional rotating electrode method (REP) uses a tungsten electrode, which can also be corroded during metal atomization and enter the powder as an impurity component.
In 1985, the Northwest Institute of Non-Ferrous Metals independently designed and developed the first PREP equipment in China.
The preparation process for the PREP they use is that the high-speed rotating electrode (raw material) is melted by the plasma arc under the protection of the high purity inert atmosphere, and the molten metal is thrown out by big centrifugal force to be atomized by the inert atmosphere and condensed into spherical powders when contacting to the internal wall of the cold chamber.
Using this technology and system, we can get high powder sphericity( over 90%), low porosity, and satellite powders. Which is totally meets the requirements of the titanium alloy powder we need.
Application of Titanium Alloy Powder
As mentioned above, titanium alloy powders are used in a wide range of applications, so we will only list some of them here for reference.
Titanium alloy is widely used in the medical field to make joint implants, prostheses, etc. Due to the high machinability of titanium alloys, individual differences can be achieved away from traditional designs, thus improving the adaptability of medical devices. Also the short processing cycle of 3D printed titanium has long-term implications for patients with diseases such as bone tumors.
The high strength, high temperature, and corrosion resistance of titanium and titanium alloys have made them a newcomer to the aerospace sector and have been rapidly adopted in recent years with the development and application of 3D printing technology. In aerospace, titanium and titanium alloys are lighter, stronger, and more ductile than ordinary materials. Its corrosion resistance also makes it increasingly competitive for marine and aircraft applications.
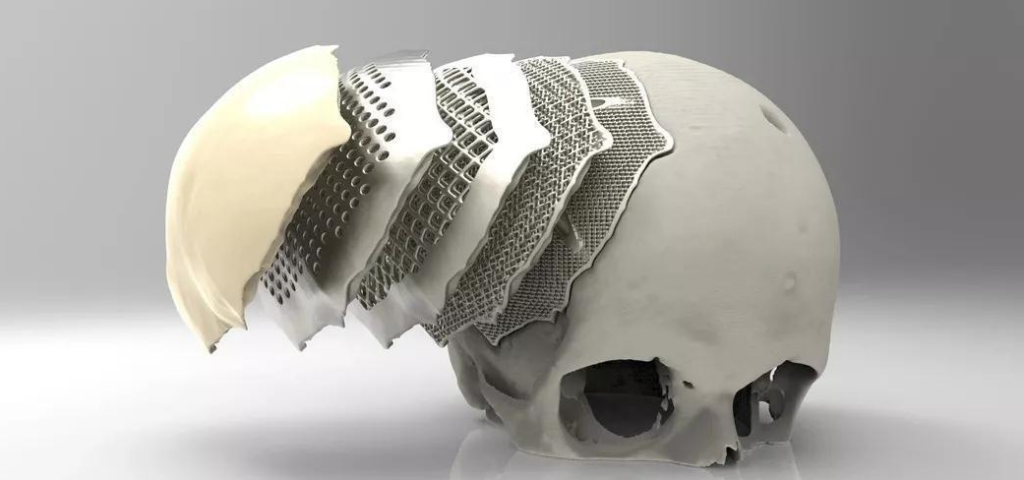
As an important consumable for 3D printing, the application and development of titanium alloys in the aerospace, automotive, and biomedical industries have also driven the development of 3D printing technology.
The Development Prospects of Titanium Alloy Powder
Defined by some as the Fourth Technological Revolution, additive manufacturing is already widely seen by the industry as one of the most cutting-edge and promising technological developments in smart manufacturing, and the development of metallic materials as printing consumables has grown rapidly in response.
According to consultancy SmarTech, the global market for additive manufacturing of metal powders is forecast to reach US$11 billion by 2024.
Titanium and titanium alloys are widely used in aerospace, automotive, biomedical, and other fields due to their excellent strength and toughness, corrosion resistance, low density, and biocompatibility, and the market demand is very promising.
The application and development of plasma technology provide technical support for the preparation of titanium alloy powder.
Although the plasma rotating electrode process is limited by factors such as electrode speed and the coarse particle size of the powder obtained, some research institutes of powder-making equipment are working to solve this problem.
With the development and promotion of plasma rotating equipment, the cost of titanium and titanium alloy powder in the field of 3D printing will be gradually reduced, and will also promote the wide application of metal powder in the field of additive manufacturing.
We have reason to believe that 3D printing will change our lives in many more areas in the future, and the preparation and development of titanium alloy powder will profoundly influence this process.