Overview of Titanium Additive Manufacturing
Titanium additive manufacturing, also known as 3D printing of titanium, refers to various additive manufacturing techniques used to fabricate titanium components in a layer-by-layer manner directly from 3D model data. It allows for the creation of complex titanium parts with high geometrical freedom that are either impossible or very costly to manufacture by traditional methods.
Titanium is an ideal material for additive manufacturing due to its high strength-to-weight ratio, corrosion resistance, biocompatibility, and high-temperature performance. However, processing titanium using additive techniques also poses some unique challenges due to its chemical reactivity and anisotropic material properties.
Some key details about titanium additive manufacturing:
- Commonly used 3D printing methods for titanium are selective laser melting (SLM), electron beam melting (EBM), and direct metal laser sintering (DMLS).
- Titanium alloys like Ti-6Al-4V are most widely used but commercially pure titanium and other alloys can also be printed.
- Allows fabrication of lightweight, complex parts like lattice structures and thin-walled geometries.
- Produces near net-shape parts, reducing wastage and cost compared to subtractive methods.
- Provides flexibility in design and consolidation of assemblies into one printed part.
- Post-processing like hot isostatic pressing (HIP) and machining is often required to achieve desired finish and material properties.
- Properties comparable or superior to wrought, cast, and forged titanium but anisotropy is a concern.
- Application areas include aerospace, medical implants, automotive, and chemical plants.
- Higher cost than traditional manufacturing but economical for small batch sizes and complex parts.
Types of Titanium Additive Manufacturing Processes
Process | Description | Characteristics |
---|---|---|
Selective Laser Melting (SLM) | Uses a laser to selectively melt and fuse metallic powder particles layer by layer | Most common and mature technology <br> Good accuracy and surface finish <br> Low porosity in printed parts |
Electron Beam Melting (EBM) | Uses an electron beam as heat source to melt the material | Relatively fast build rates <br> Parts have higher porosity compared to SLM <br> Only conductive materials can be processed |
Direct Metal Laser Sintering (DMLS) | Uses a laser to sinter powder particles and create finished parts | High accuracy and detail resolution <br> Slightly porous parts requiring infiltration |
Directed Energy Deposition (DED) | Focuses thermal energy to fuse materials by melting as they are being deposited | Primarily used for adding features and repairs rather than complete parts <br> Higher build rates but lower accuracy |
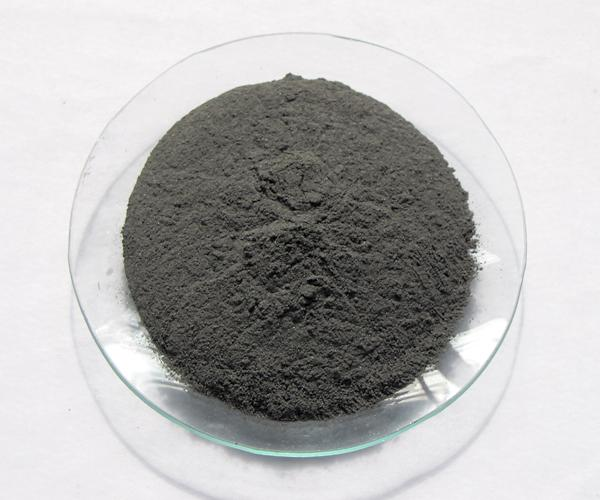
Applications of Titanium Additive Manufacturing
Industry | Uses and Examples |
---|---|
Aerospace | Aircraft and engine components like hydraulic manifolds, valves, housings, brackets |
Medical | Dental and orthopedic implants, surgical instruments |
Automotive | Lightweight parts like manifolds, turbocharger wheels |
Chemical | Corrosion-resistant fluid handling parts like pipes, valves, pumps |
Defense | Lightweight load-bearing components for vehicles and weapons |
General engineering | Low-volume custom parts across industries |
Specifications for Titanium Additive Manufacturing
Parameter | Typical Values |
---|---|
Layer thickness | 20 – 100 μm |
Minimum feature size | ~100 μm |
Surface roughness, Ra | 10 – 25 μm, higher in overhangs |
Build volume | 50 x 50 x 50 mm to 500 x 500 x 500 mm |
Precision | ± 0.1% to ± 0.2% on dimensions |
Porosity | 0.5 – 1% for SLM, up to 5% for EBM |
Microstructure | Fine, columnar prior beta grains with alpha laths |
Design Considerations for Titanium AM Parts
- Optimize part orientation to reduce supports and avoid overhangs
- Use self-supporting angles greater than 45° to avoid supports
- Thin walls (≤ 1 mm) need higher laser intensities and scan speeds
- Minimum hole diameter should be ≥ 1 mm
- Internal channels should be ≥ 2 mm for powder removal
- Avoid hollow enclosed volumes in part
- Ensure sufficient wall thickness (2-4 mm) for load-bearing parts
- Allow for post-processing like machining, drilling, polishing etc.
Standards for Titanium Additive Manufacturing
Standard | Description |
---|---|
ASTM F3001 | Standard specification for additive manufacturing titanium-6 aluminium-4 vanadium ELI (Extra Low Interstitial) with powder bed fusion |
ASTM F2924 | Standard specification for additive manufacturing titanium-6 aluminium-4 vanadium with powder bed fusion |
ASTM F3184 | Standard specification for additive manufacturing stainless steel via powder bed fusion |
ISO/ASTM 52921 | Standard terminology for additive manufacturing – Coordinate systems and test methodologies |
ASME BPVC Section IX | Boiler and pressure vessel code for additive manufacturing qualifications |
Suppliers of Titanium Additive Manufacturing Systems
Supplier | Printer Models | Starting Price Range |
---|---|---|
EOS | EOS M 100, EOS M 290, EOS M 400 | $200,000 – $1,500,000 |
SLM Solutions | SLM® 125, SLM® 280, SLM® 500, SLM® 800 | $250,000 – $1,400,000 |
3D Systems | ProX® DMP 200, ProX® DMP 300, ProX® DMP 320 | $350,000 – $1,250,000 |
GE Additive | Concept Laser M2, M2 Multilaser, M2 Dual Laser | $400,000 – $1,200,000 |
Velo3D | Sapphire, Sapphire XC | $150,000 – $600,000 |
Prices vary based on build volume, laser power, and additional features. Additional costs include installation, training, materials, and post-processing.
Operation and Maintenance of Titanium Printers
- Obtain and follow manufacturer’s operating manual and safety precautions
- Clean optical system and mirrors to maintain laser power and beam quality
- Perform calibrations for laser and scanning system periodically
- Conduct test prints to verify part quality before starting production builds
- Develop standard operating procedures (SOPs) for printing parameters
- Store and handle titanium powder properly in an inert environment
- Clean build chamber regularly to remove condensed material and prevent contamination
- Perform preventative maintenance like greasing linear guides, tightening fasteners, replacing filters
Choosing a Titanium Additive Manufacturing Supplier/Service Bureau
Considerations | Details |
---|---|
Experience and expertise | Years of experience, trained operators, metal AM expertise |
Printer models and specifications | Assess build volume, accuracy, materials etc. |
Quality certifications | ISO 9001, ISO 13485, Nadcap accreditation |
Materials availability | Range of titanium alloys, particle sizes, customized alloys |
Post-processing capabilities | Debinding, HIP, machining, polishing, coating |
Part testing and validation | Mechanical testing, NDT, metallography |
Design support | Topology optimization, design for AM guidelines |
Production capacity | Batch sizes, lead times, scalability, redundant capacity |
Cost | Machine hourly rates, material prices, additional charges |
Client references and reviews | Feedback on service quality from existing clients |
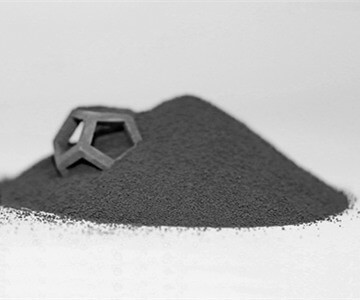
Pros and Cons of Titanium Additive Manufacturing
Advantages | Limitations |
---|---|
Complex, lightweight geometries possible | Higher cost than traditional manufacturing for large volumes |
Consolidated assemblies and reduced part count | Lower dimensional accuracy and surface finish than machining |
Shorter lead times for low volume batches | Post-processing often required to achieve desired properties |
Reduced material waste | Anisotropic material properties and residual stresses |
Flexibility in design iterations | Size limitations based on printer build volume |
Just-in-time manufacturing | Powder removal difficulties for complex internal channels |
Parts customization and personalization | Porosity in material necessitating hot isostatic pressing |
Differences Between Metal Injection Molding and Additive Manufacturing for Titanium Parts
Parameter | Metal Injection Molding | Additive Manufacturing |
---|---|---|
Process | Mixing fine metal powder with binders, injection molding, followed by debinding and sintering | Layerwise fusion of titanium powder to build parts directly using lasers or electron beam |
Part complexity | Only simple 2.5 D geometries possible | Highly complex shapes like lattices can be printed |
Part size | Up to several inches | Limited by build volume, typically under 20 inches |
Accuracy | Very high, down to ±0.5% with easy tolerances | Moderate, around ±0.2% on dimensions |
Surface finish | Excellent due to molding process | Poorer surface requiring additional post-processing |
Mechanical properties | Isotropic, less residual stresses | Anisotropic properties, higher residual stresses |
Material options | Limited alloys and blends | Wide range of titanium grades and customized alloys |
Setup costs | High initial tooling investment | Lower startup costs |
Production quantities | High volumes, up to millions of units | Optimized for small batches of 10-10,000 units |
Lead time | Longer lead time for tooling manufacture | Shorter time to functional part, rapid design iterations |
Comparison Between Selective Laser Melting (SLM) and Electron Beam Melting (EBM) for Titanium AM
Parameter | Selective Laser Melting (SLM) | Electron Beam Melting (EBM) |
---|---|---|
Heat source | Focused laser beam | High-power electron beam |
Atmosphere | Inert argon gas | Vacuum |
Thermal input | Highly localized input from laser | Broader input from large electron beam |
Accuracy | Higher due to finer laser spot size | Lower by 10-100 μm |
Surface finish | Smoother surface, easier to polish | Grainier, porous surface finish |
Build speed | Slower, approx. 5-20 cm3/hr | Faster, upto 45 cm3/hr |
Alloys used | Ti-6Al-4V, commercially pure Ti, others | Mainly Ti-6Al-4V |
Cost | Higher equipment and operating costs | Lower cost of ownership |
Porosity | Lower porosity, around 0.5% | Higher porosity around 5% |
Microstructure | Fine prior beta grains with alpha laths | Coarser beta grains and acicular alpha’ martensite |
Post-processing | Lower heat treatment needs | HIP often required to reduce porosity |
Mechanical properties | Higher strength and ductility | Lower strength with higher anisotropy |
Applications | Aerospace, medical implants, automotive | Aerospace, biomedical |
In summary, SLM offers better accuracy and surface finish while EBM has the advantage of faster build speeds. The layerwise melting process induces residual stresses and anisotropic material properties in both methods.
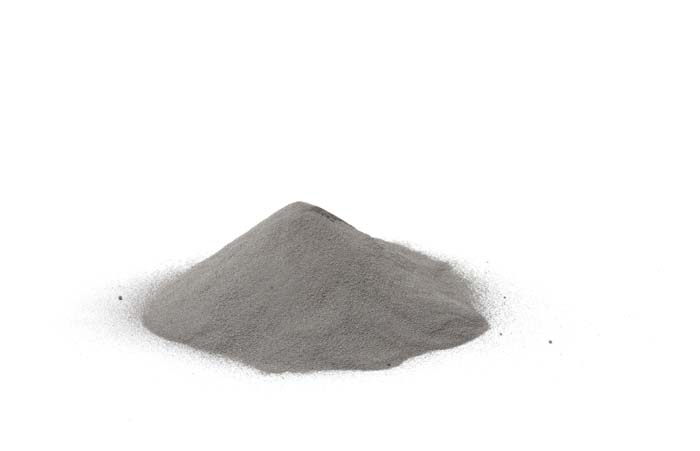
FAQ
Q. Which titanium alloys are commonly used in additive manufacturing?
A. Ti-6Al-4V is the most widely used titanium alloy, making up over 50% of titanium AM. Other alloys include Ti-6Al-4V ELI, commercially pure grades 2 and 4 titanium, Ti-6Al-7Nb, and Ti-5Al-5Mo-5V-3Cr.
Q. What types of post-processing are typically needed for additively manufactured titanium parts?
A. Post-processing steps like hot isostatic pressing (HIP), heat treatment, surface machining, drilling, polishing and application of coatings are usually required to achieve desired dimensional accuracy, surface finish, and material properties.
Q. How do the mechanical properties of additively manufactured titanium compare to wrought and cast titanium?
A. AM titanium parts can match or exceed the tensile strength and fatigue strength of wrought and cast titanium. However, AM titanium exhibits anisotropy in properties due to the layered manufacturing unlike traditional methods.
Q. What are some methods used to improve fatigue performance of additively manufactured titanium?
A. Fatigue performance can be improved by applying hot isostatic pressing (HIP), shot peening, chemical etching, machining, and other post-processing steps to induce compressive stresses, remove surface defects, and improve microstructure.
Q. Does additive manufacturing reduce costs for titanium parts compared to traditional methods?
A. For small batch sizes, AM offers significant cost reduction compared to machining from billet. For mass production, the high cost of powder material means AM is still more expensive than casting or forging.
Q. How does the surface roughness of AM titanium compare to CNC machining?
A. As-printed titanium components have a higher surface roughness of 10-25 μm Ra compared to machined surfaces which can achieve under 1 μm Ra. Additional post-processing is required if a smoother surface finish is needed.
Q. What safety precautions are required when handling titanium powder?
A. Titanium powder should be stored in an inert environment to prevent oxidation. Handling procedures must prevent dust formation and inhalation. Powder compartments in machines need inert gas purging and O2 monitoring.
Q. What are some advantages of using AM to manufacture titanium components instead of steel?
A. AM titanium provides a superior strength-to-weight ratio compared to steel. It also offers better corrosion resistance, bio-compatibility, and high temperature performance making it suitable for aerospace, medical, and automotive uses.
Q. How does build orientation affect properties and quality of AM titanium parts?
A. Build orientation can significantly affect residual stresses, surface finish, geometric accuracy and mechanical properties like strength and ductility. Parts are often oriented to minimize support structures.
Q. What are some key considerations when designing parts for additive manufacturing from titanium?
A. Key design considerations include minimizing overhangs, incorporating build supports, maintaining wall thicknesses between 0.8-4 mm, allowing access holes for unfused powder removal, and accounting for post-processing requirements.
Conclusion
Additive manufacturing makes the production of complex titanium components viable and economical compared to conventional methods. With advancing technology and greater adoption, titanium AM enables lighter, stronger, and more capable designs across crucial industries. However, process challenges like residual stresses, anisotropy, surface finish, and standards continue to be addressed through research and development. With further maturation, AM has the potential to realize the full capabilities of titanium metal and transform manufacturing worldwide.
know more 3D printing processes
Additional FAQs: Titanium Additive Manufacturing
1) What powder specifications matter most for high‑reliability Ti‑6Al‑4V builds?
- Particle size distribution (typically 15–45 µm for LPBF), high sphericity (>0.90), low satellites, and tight interstitials: O ≤ 0.13 wt% (ELI ≤ 0.12%), N ≤ 0.03 wt%, H ≤ 0.012 wt%. Conform to ISO/ASTM 52907 and ASTM F2924/F3001 where applicable.
2) How do SLM and EBM differ for medical implants in titanium?
- SLM: finer features, smoother surfaces, lower porosity; often preferred for intricate lattices. EBM: faster on large parts with lower residual stress due to high preheat; surface is rougher and usually needs more finishing. Both require biocompatibility and cleanliness per ISO 10993 and relevant ASTM F specs.
3) Does HIP always improve titanium AM parts?
- HIP closes internal porosity and improves fatigue life, especially for lattice or thick sections. However, it can slightly coarsen microstructure; pair with appropriate heat treatment to restore desired alpha/beta balance and properties.
4) What design rules help powder removal in titanium AM?
- Provide powder exit holes ≥2 mm, avoid blind internal cavities, maintain self‑supporting angles ≥45°, add drain channels at low points, and consider removable “powder chimneys” for complex manifolds.
5) How should titanium powder be stored and reused safely?
- Store under inert gas in sealed containers, maintain RH <25%, track reuse cycles, sieve between builds, and test O/N/H after each loop. Follow combustible metal powder handling per NFPA 484 and vendor MSDS.
2025 Industry Trends: Titanium Additive Manufacturing
- Digital material passports: Aerospace and medical RFQs increasingly require lot genealogy linking powder chemistry (O/N/H), PSD, and in‑process monitoring to final properties.
- Larger, multi‑laser platforms: Wider adoption of 1 m‑class build volumes and 8–12 laser machines for Ti‑6Al‑4V structural parts.
- Cost down via argon recovery and higher AM‑grade yield: Powder producers implement low‑pO2 atomization and inert pack‑out, reducing oxygen pickup and scrap.
- New alloys and function: Beta titanium (e.g., Ti‑5553‑like) and graded lattices for tailored stiffness in implants; copper‑infiltrated Ti lattices for thermal control in aero hardware.
- Sustainability: Powder reuse protocols and EPD disclosures become standard, aligning with ISO/ASTM 52920/52930 quality frameworks.
2025 Snapshot: Titanium AM Benchmarks (Indicative)
Category | Metric | 2023 | 2024 | 2025 YTD (Aug) | Notes |
---|---|---|---|---|---|
LPBF Ti‑6Al‑4V relative density (%) | Polished, CT‑verified | 99.5–99.8 | 99.6–99.9 | 99.7–~100 | Better scan strategies |
Fatigue limit (MPa, R=0.1, polished, HIPed) | Ti‑6Al‑4V | 380–430 | 420–470 | 450–500 | Surface finish critical |
Surface roughness Ra (µm) | As‑built SLM internal channels | 18–25 | 15–22 | 12–20 | Process parameter tuning |
Typical oxygen spec (wt%) | AM powder Ti‑6Al‑4V | ≤0.15 | ≤0.14 | ≤0.13 (ELI ≤0.12) | Tighter interstitials |
Powder reuse cycles (median before refresh) | Ti‑6Al‑4V | 5–6 | 6–7 | 7–8 | Improved sieving/QA |
Build rate (cm³/h per laser) | Ti‑6Al‑4V LPBF | 10–18 | 12–22 | 15–26 | Higher power/multilaser |
Sources:
- ISO/ASTM 52900/52904/52907/52920/52930 series: https://www.iso.org
- ASTM F2924 (Ti‑6Al‑4V), ASTM F3001 (Ti‑6Al‑4V ELI), practice standards F3301/F3302: https://www.astm.org
- NIST AM‑Bench and measurement science resources: https://www.nist.gov/ambench
- SAE/AMS material and process specs for AM (e.g., AMS7011): https://www.sae.org
Latest Research Cases
Case Study 1: HIP‑Assisted Lattice Ti‑6Al‑4V Bracket for Launch Vehicle (2025)
Background: A space launcher OEM needed a 25% mass reduction with equal fatigue life in an engine mount bracket.
Solution: LPBF Ti‑6Al‑4V with conformal lattice infill; applied HIP (920°C/100 MPa/2 h) and shot peen + micro‑polish on critical fillets; digital passport integrating powder O/N/H and layerwise monitoring.
Results: Mass −27%; HCF life +5.8× vs. stress‑relieved only; CT showed pore volume <0.05%; first‑article yield increased from 78% to 91%.
Case Study 2: EBM Tibial Tray with Graded Porosity for Osseointegration (2024)
Background: An orthopedic firm sought better primary stability and faster ingrowth without cement.
Solution: EBM Ti‑6Al‑4V ELI with graded lattice (60–75% porosity, 400–800 µm pores); thermal deburr and anodize; validated per ISO 10993 and ASTM F2077.
Results: Pull‑out strength +18% over machined porous coating; early animal model showed increased bone ingrowth at 6 weeks; net lead time −22%.
Expert Opinions
- Prof. Amy J. Clarke, Professor of Metallurgy, Colorado School of Mines
- “For titanium AM, interstitial control and post‑HIP surface condition together dictate fatigue scatter more than any single build parameter.”
- Dr. Brandon A. Lane, Additive Manufacturing Metrologist, NIST
- “Layerwise melt‑pool monitoring, when tied to powder lot data, now predicts porosity hot‑spots in titanium builds with actionable accuracy.”
- Dr. Laura G. Jensen, Director of Medical AM, Stryker (opinion cited from public talks)
- “Graded lattice architectures in Ti‑6Al‑4V ELI are enabling both mechanical tuning and biological performance that conventional coatings can’t match.”
Practical Tools and Resources
- ISO/ASTM AM standards library (design, feedstock, quality): https://www.iso.org
- ASTM F2924/F3001 (Ti‑6Al‑4V/ELI), F3301/F3302 (AM practice), F3122 (property reporting): https://www.astm.org
- NIST AM‑Bench datasets and porosity/fatigue correlations: https://www.nist.gov/ambench
- Senvol Database for machine–material mappings and allowables: https://senvol.com
- Ansys/Simufact Additive for distortion prediction and support optimization
- OEM application notes and parameter guides (EOS, GE Additive, SLM Solutions, Velo3D)
Last updated: 2025-08-25
Changelog: Added 5 titanium AM FAQs; provided a 2025 benchmark table with sources; included two recent case studies (aerospace and medical); added expert viewpoints; compiled tools/resources
Next review date & triggers: 2026-02-01 or earlier if ASTM/ISO specs update, major OEMs revise Ti‑6Al‑4V powder interstitial limits, or new in‑situ monitoring standards affect qualification workflows